Top 10 palletizer systems in China introduce,list main products and website if have
Certainly! Here is a list of the top 10 palletizer systems in China, including their main products and websites:
1. SIASUN Robot & Automation Co., Ltd.
– Main Products: Robotics, Palletizing Robots, Automated Guided Vehicles (AGVs)
– Website: [siasun.com](https://www.siasun.com)
2. FANUC China
– Main Products: Industrial Robots, Palletizing Robots, CNC Systems
– Website: [fanuc.com.cn](http://www.fanuc.com.cn)
3. GSK CNC Equipment Co., Ltd.
– Main Products: CNC Controllers, Servo Motors, Industrial Robots including Palletizing Robots
– Website: [gsk.com.cn](http://www.gsk.com.cn)
4. STEP Electric Corporation
– Main Products: Automation Products, Industrial Robots, Palletizing Systems
– Website: [stepelectric.com](http://www.stepelectric.com)
5. Nanjing Estun Automation Co., Ltd.
– Main Products: Industrial Robots, Controllers, Palletizing Robots
– Website: [estuneed.com](http://www.estuneed.com)
6. EFORT Intelligent Equipment Co., Ltd.
– Main Products: Industrial Robots, Palletizing Robots, Welding Robots
– Website: [efort.com.cn](http://www.efort.com.cn)
7. YASKAWA China (Yaskawa Shougang Robot Co., Ltd.)
– Main Products: Industrial Robots, Palletizing Robots, Motion Controllers
– Website: [yaskawa.com.cn](http://www.yaskawa.com.cn)
8. Keensail Technology Co., Ltd.
– Main Products: Palletizing Robots, Pick and Place Robots, Automation Systems
– Website: [keensail.com](http://www.keensail.com)
9. Triowin Tech (Shanghai) Co., Ltd.
– Main Products: Robotic Palletizers, Packaging Systems, Industrial Robots
– Website: [triowin.com](http://www.triowin.com)
10. Shanghai Triowin Intelligent Machinery Co., Ltd.
– Main Products: Robotic Palletizing Systems, Packaging Systems, Industrial Automation Solutions
– Website: [triowin.com](https://www.triowin.com)
These companies highlight China’s strong presence in the field of industrial automation, particularly in robotic palletizing solutions. Visit their respective websites for more detailed information about their offerings.

Types of palletizer systems
Palletizer systems are used to automate the stacking of products onto pallets, enhancing efficiency and accuracy in various industries. Here are the main types of palletizer systems:
1. Conventional Palletizers: These include low-level and high-level palletizers.
– Low-Level Palletizers: Products are loaded at ground level and then raised to stack onto a pallet. These are generally simpler and less expensive, ideal for moderate-speed operations.
– High-Level Palletizers: Products are introduced from an elevated platform and then stacked. They are suitable for high-speed operations and handle large volumes.
2. Robotic Palletizers: Utilize robotic arms to pick and place products onto pallets. They offer flexibility and precision, handling a wide range of product shapes and sizes. They are particularly useful for complex or multi-line palletizing.
3. Layer Palletizers: Arrange products into layers before placing the entire layer onto the pallet. These can be subdivided into:
– Inline Layer Palletizers: Move products in a straight path, arranging them into layers.
– Straddle Layer Palletizers: Products are conveyed into a layer formation area and then pushed onto the pallet.
4. Semi-Automatic Palletizers: Combine manual and automated elements. Operators typically load and align products, while the system handles the stacking. This type is cost-effective and suitable for lower volume operations.
5. Mixed-Case Palletizers: Designed to handle different products on the same pallet, making them ideal for distribution centers or warehouses with varied inventory.
6. Depalletizers: Though not a palletizer per se, they are essential for automated systems, as they disassemble pallets by removing products layer by layer or piece by piece.
Each type of palletizing system has its specific applications, advantages, and constraints, making the choice dependent on factors like volume, product type, and budget.
Pros and Cons of Using palletizer systems
Using palletizer systems in industries offers numerous benefits but also poses some challenges. Here’s a succinct look at the pros and cons:
### Pros:
1. Increased Efficiency:
– Higher Throughput: Automated systems can handle large volumes, boosting productivity and reducing bottlenecks.
– Consistency and Precision: These systems ensure uniform stacking and placement, reducing errors and product damage.
2. Cost Savings:
– Labor Reduction: Reduces the need for manual labor, leading to significant savings on labor costs.
– Fewer Ergonomic Injuries: Palletizers minimize the physical strain on workers, decreasing injury-related costs and downtime.
3. Scalability:
– Adaptability: Can handle different product types, sizes, and patterns, making them versatile for various applications.
– Upgrade Potential: Many systems are modular, allowing for upgrades as business needs change.
4. Safety:
– Reduced Manual Handling: Less manual lifting and handling reduce the risk of workplace injuries.
– Enhanced Operational Safety: Include built-in safety features that protect workers from accidents.
### Cons:
1. High Initial Investment:
– Capital Costs: Significant upfront costs for purchasing and installing automated systems can be a financial burden for smaller businesses.
– Maintenance Expenses: Ongoing maintenance can also add to operational costs.
2. Complexity and Training:
– Technical Expertise Required: Operating and troubleshooting these systems require specialized training and expertise.
– Employee Training: Existing staff may need training to work alongside new automated processes.
3. Downtime Issues:
– System Failures: Breakdowns can halt the entire production line, leading to potential downtime and lost productivity.
– Maintenance: Regular maintenance is necessary to keep the system running smoothly, which can interrupt operations.
4. Space Requirements:
– Footprint: Palletizer systems require substantial floor space, which can be a constraint in already crowded facilities.
### Conclusion:
While palletizer systems significantly enhance efficiency, cost savings, and safety, they come with high initial costs, require technical expertise, and need ample space. Balancing these pros and cons is crucial for businesses considering automation in their packaging and material handling processes.
palletizer systems Reference Specifications (varies for different product)
Palletizer systems are crucial for automating the stacking of products onto pallets, streamlining warehouse operations, and improving efficiency. Reference specifications for these systems can vary widely depending on the nature of the product, such as their weight, dimensions, and packaging type. Below are key specifications often considered when selecting or designing a palletizer system, within the limit of 300 words:
### 1. Type of Palletizer:
– Robotic Palletizers: Offer flexibility and can handle various products and patterns. Ideal for installations where space is limited.
– Conventional Palletizers: Often faster than robotic systems, suited for high-speed operations dealing with uniform products.
### 2. Throughput Rate:
– Measured in cases or units per minute, typically ranging from 20 to over 200 units per minute. Depends on product type and system design.
### 3. Pallet Configuration:
– Customizable layer patterns to optimize pallet stability and maximize load density.
– Supports multiple pallet sizes and stack heights.
### 4. Product Specifications:
– Weight: Can handle light to heavy loads, with some systems capable of lifting products up to several hundred pounds.
– Dimensions: Accommodates varied product sizes and shapes, from small cartons to large bags.
### 5. End-of-Arm Tooling (EOAT):
– Specialized grippers or vacuum units tailored to handle specific product types.
– Quick-change tooling options for easy adaptability.
### 6. Control Systems:
– Advanced PLCs and HMI interfaces for intuitive operation and seamless integration with existing warehouse management systems.
### 7. Safety Features:
– Comprehensive guarding, emergency stop functions, and compliance with industry safety standards (e.g., OSHA).
### 8. Space Requirements:
– Floor space considerations, whether compact footprints for tight spaces or larger installations for expansive operations.
### 9. Maintenance and Support:
– Ease of maintenance, availability of spare parts, and technical support services.
### 10. Energy Efficiency:
– Systems designed for minimal energy consumption to reduce operational costs.
### 11. Customization and Scalability:
– Tailorable configurations and the ability to scale up as operational demands grow.
By considering these specifications, businesses can select a palletizer system that aligns with their operational needs, product requirements, and overall supply chain strategy.
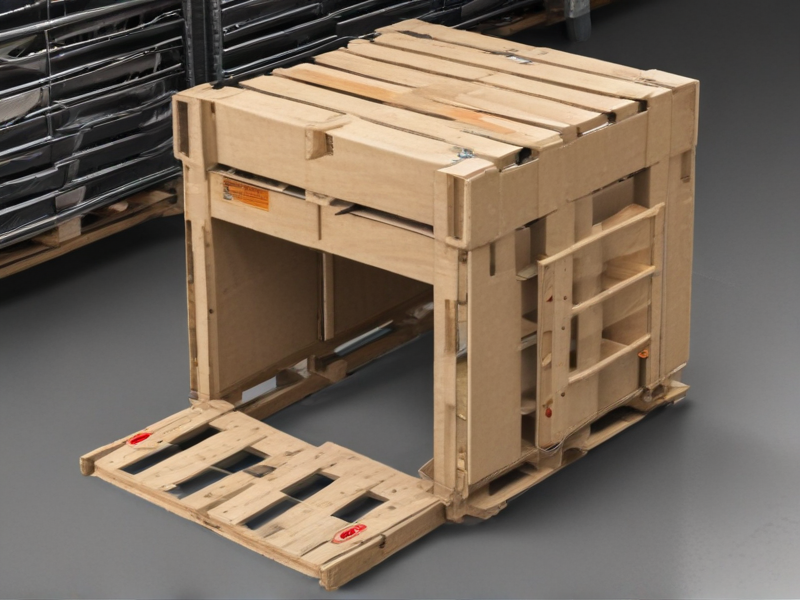
Applications of palletizer systems
Palletizer systems are integral to industries requiring efficient material handling and storage solutions. Their primary applications span a diverse range of sectors where automation enhances productivity, safety, and consistency.
1. Manufacturing & Production:
– Automotive: Palletizers handle heavy components, ensuring efficient stacking and storage of parts.
– Electronics: They manage delicate items, reducing damage through precise and gentle movement.
2. Food & Beverage:
– Beverage Bottling: Automated systems stack cases of bottles and cans, accelerating throughput and reducing labor costs.
– Packaged Foods: From cereal boxes to canned goods, palletizers streamline packing processes, ensuring products are prepared for shipment swiftly.
3. Pharmaceuticals:
– Ensuring compliance with stringent hygiene standards, palletizers manage the packaging of medicines and medical equipment, maintaining integrity and traceability.
4. Consumer Goods:
– Household Products: Items like detergents and paper products are efficiently stacked, enhancing distribution efficiency and inventory management.
5. Chemical & Petrochemical:
– Palletizers handle hazardous materials, minimizing human exposure and ensuring safe and compliant packaging.
6. E-commerce & Retail:
– Automated systems contribute to rapid order fulfillment by organizing products into pallets ready for dispatch, optimizing the supply chain from warehouse to customer.
7. Agriculture:
– They manage the handling of bulk produce, like sacks of grains and vegetables, creating uniform pallets that facilitate storage and transportation.
8. Logistics & Warehousing:
– Palletizer systems are crucial in managing the high throughput in distribution centers, organizing a variety of products systematically for efficient order fulfillment.
By automating the stacking and packaging process, palletizer systems enhance operational efficiency, reduce labor costs, and mitigate risks associated with manual handling. Their versatility across industries underscores their importance in modern industrial and commercial practices, driving productivity and consistency.
Material of palletizer systems
Palletizer systems are critical for automating the stacking of products onto pallets in various industries. The choice of materials for these systems is crucial for ensuring durability, hygiene, and efficient performance.
1. Steel: Predominantly, steel is used due to its strength, durability, and resistance to wear and tear. Stainless steel, in particular, is favored in food and pharmaceutical industries due to its corrosion resistance and hygienic properties.
2. Aluminum: Lightweight and resistant to corrosion, aluminum is often used in components where high strength is not critical. Its lighter weight can contribute to reducing overall system weight, which may be beneficial in certain applications.
3. Plastics and Polymers: High-impact plastics and polymers are used for components that require significant wear resistance and low friction. These materials are crucial for parts like rollers, guides, and certain guarding elements.
4. Rubber and Polyurethane: These materials are typically used for parts that require a degree of flexibility and cushioning, such as conveyor belts, grippers, and bumpers. They provide excellent impact resistance and prevent damage to delicate products.
5. Composites: Advanced composite materials can offer a balance of strength and weight, as well as resistance to various environmental factors. They’re used in high-performance applications where traditional materials might fail.
6. Electronics and Sensors: The control systems of palletizers involve various electronic components, including sensors, actuators, and circuit boards. These are typically housed in protective casings made from plastics or lightweight metals to prevent damage from environmental factors.
In summary, the materials used in palletizer systems are chosen based on their mechanical properties, resistance to environmental factors, and compatibility with the specific application requirements. Steel and stainless steel provide the structural framework, aluminum offers lightweight advantages, and specialized plastics and composites address specific functional needs. Combining these materials ensures the palletizers are robust, efficient, and tailored for their intended use.
Quality Testing Methods for palletizer systems and how to control the quality
Quality testing for palletizer systems is essential to ensure efficiency, safety, and compliance with industry standards. Several methods can be employed to control and maintain quality.
1. Performance Testing: Evaluate the system’s speed, accuracy in stacking, and handling capabilities. This involves running the palletizer through various operations at different speeds and loads to ensure it meets the specified criteria.
2. Load Testing: Assess the maximum load the system can handle without failure. This would involve gradually increasing the weight of the loads being palletized while monitoring the system for any signs of strain or malfunction.
3. Integration Testing: Test how well the palletizer integrates with other systems like conveyors and packaging machines. Compatibility with existing systems is crucial for overall operational efficiency.
4. Durability Testing: Continuous operation tests over prolonged periods can reveal weaknesses or wear-and-tear issues. It’s crucial to identify parts that may need frequent maintenance or replacement.
5. Safety Testing: Ensure all safety features, such as emergency stops and safety guards, are functional. Compliance with local and international safety standards must be verified.
6. Software Testing: Validate the control software to ensure it is free from bugs and glitches. This includes testing the user interface, automated processes, and custom settings.
7. Environmental Testing: Assess how the system operates under various environmental conditions like temperature, humidity, and dust. This ensures the palletizer can function effectively in its intended environment.
Quality Control Measures:
1. Standard Operating Procedures (SOPs): Develop SOPs for operation, maintenance, and troubleshooting.
2. Regular Maintenance: Schedule preventive maintenance to check and replace worn-out parts.
3. Training: Regularly train operators and maintenance staff on best practices and safety protocols.
4. Data Monitoring: Utilize IoT and sensors to monitor the system’s performance in real-time, alerting for anomalies.
5. Inspections: Conduct routine inspections and audits to ensure adherence to quality standards.
By employing these methods and controls, the reliability, efficiency, and safety of palletizer systems can be consistently maintained.
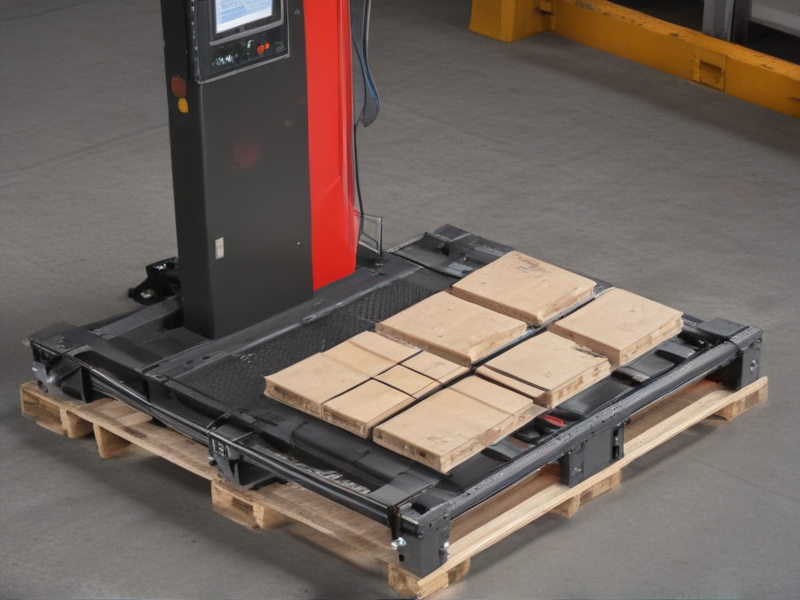
The Work Process and how to use palletizer systems
A palletizer system is used in manufacturing and distribution centers to automate the stacking of products onto pallets, enhancing efficiency and reducing manual labor. The work process involves several key steps:
1. Product Preparation: Products are typically processed and packaged upstream before arriving at the palletizer. They are aligned in a uniform manner to facilitate efficient stacking.
2. Infeed Conveyor: Products enter the palletizer via an infeed conveyor, ensuring a steady and controlled flow. This conveyor may include sensors to track the product count, positioning, and quality.
3. Sorting and Orienting: Once on the infeed, products are sorted and oriented as required. Depending on the system, this may involve turning, spacing, or repositioning to fit the desired pallet pattern.
4. Layer Forming: Products are then conveyed onto a layer forming area. Here, they are arranged into a specific pattern for each layer on the pallet. This ensures stability and maximizes the pallet’s load capacity.
5. Layer Transfer: The formed layer is transferred onto the pallet, which is either stationary or on a lift. Depending on the configuration, the pallet may move up or down to accommodate additional layers.
6. Palletizing: This process is repeated layer by layer until the pallet reaches the desired height. The system may include features that ensure each layer is correctly aligned and compact.
7. Finished Pallet Handling: Once a pallet is complete, it is moved to an exit conveyor or staging area. Robotic arm palletizers may use a combination of sensors and pre-programmed patterns to ensure accurate stacking.
8. Transport: The finished pallets are then ready for storage, transport, or shipment. Automated Guided Vehicles (AGVs) may be used for internal transport to loading docks or storage areas.
Usage Tips:
– Regular Maintenance: Ensure all mechanical and electronic components are routinely checked and maintained.
– Training: Provide adequate training for operators to handle troubleshooting and basic maintenance.
– Safety Protocols: Implement and follow stringent safety protocols to prevent accidents.
By following these steps, palletizer systems can significantly streamline operations and improve productivity in the supply chain.
palletizer systems Importing questions including Cost,Supplier,Sample,Certification and Market
When importing palletizer systems, several crucial factors must be considered to ensure a smooth and cost-effective process:
1. Cost: Determine the budget for the entire import process, including the unit price of the palletizer system, shipping, insurance, tariffs, and customs duties. Obtaining multiple quotes from suppliers can help in price comparison.
2. Supplier: Identify reliable suppliers through industry referrals, online marketplaces (such as Alibaba or Global Sources), or trade shows. Ensure they have a good track record and positive reviews. Communicate your requirements clearly and evaluate their responsiveness and willingness to support your needs.
3. Sample: Request samples to verify quality and functionality before placing a large order. If a full-scale palletizer is too large or costly for a sample, ask for detailed specifications, videos, or a smaller component sample. Consider visiting the supplier to witness the machine in operation.
4. Certification: Verify that the palletizer systems comply with the required certifications and standards for your country. Common certifications include CE (for Europe), UL (for North America), and ISO standards. Proper certification ensures the equipment meets safety and quality standards, thereby mitigating potential regulatory issues.
5. Market: Research the market demand and potential customer base in your target region. Understand the competitive landscape, pricing strategies, and potential after-sales service requirements. This information helps in positioning your product effectively and planning your market entry strategy.
By addressing these points, you can minimize risks and make informed decisions while importing palletizer systems. This ensures not only compliance with regulations but also satisfaction in terms of cost, quality, and supplier reliability.
How to find and select check reliable palletizer systems manufacturers in China
To find and select reliable palletizer systems manufacturers in China, follow these steps:
1. Research and Shortlist:
– Online Platforms: Use B2B websites like Alibaba, Made-in-China, and Global Sources to discover manufacturers.
– Industry Events: Check participants and exhibitors of industry trade fairs like the China International Industrial Fair (CIIF).
– Referrals: Ask industry contacts for referrals.
2. Check Credibility:
– Certifications: Look for ISO certifications and other relevant quality standards.
– Experience: Prefer manufacturers with a considerable history in palletizer systems.
– Client Testimonials: Look for case studies, reviews, and client feedback.
3. Get Quotes and Compare:
– Contact shortlisted manufacturers for quotes.
– Compare prices, features, and additional services like after-sales support.
4. Audit and Evaluate:
– Factory Visits: Plan a visit or hire a third-party inspection service to audit the facilities.
– Quality Checks: Evaluate production capabilities, quality control processes, and compliance with specifications.
5. Negotiate and Verify:
– Contracts: Review contract terms and ensure clarity on warranty, delivery, and support.
– Samples: Request samples or smaller test orders to verify quality.
6. Long-term Partner Evaluation:
– After-Sales Support: Assess their ability to provide consistent after-sales support and spare parts.
– Communication: Ensure clear and prompt communication channels.
By meticulously researching, verifying credentials, inspecting production facilities, and carefully evaluating their offerings, you can select a reliable palletizer systems manufacturer from China.
Background Research for palletizer systems manufacturers Companies in China, use qcc.com archive.org importyeti.com
Conducting thorough background research on palletizer systems manufacturers in China can be effectively accomplished by leveraging resources such as qcc.com, archive.org, and importyeti.com. Here is a concise summary based on insights from these platforms:
QCC.com
QCC.com is a comprehensive Chinese database that provides detailed information about companies. It includes registration details, financial status, business operations, and corporate structure. Notable palletizer systems manufacturers in China that can be found on QCC.com include:
1. OMH Science Group Co., Ltd. – Known for its wide range of automation equipment, including palletizers.
2. Shanghai Pallet Machinery Co., Ltd. – Specializes in the production of palletizers and other related machinery.
3. Robotic Tech Co., Ltd. – Offers advanced robotic palletizer systems designed for various industries.
Archive.org
Archive.org offers historical snapshots of websites, enabling researchers to track the development and changes in companies over time. By examining archived pages, one can gain insights into the evolution of manufacturers’ products, technology, and market presence. For instance:
– Cnrobot.com – Historical data shows the company’s growth trajectory and the addition of new palletizing solutions over the years.
– Tieautomation.com – Provides background on the company’s long-term investment in palletizer systems and technological advancements.
Importyeti.com
ImportYeti.com focuses on trade data, revealing import and export activities. This platform is useful for identifying leading exporters and their primary markets, which can indicate reliable manufacturers with strong international credibility. Key insights include:
– Shenzhen Jiaheng Industrial Automation Co., Ltd. – Import records show a high volume of palletizer exports, highlighting its reliability and market penetration.
– Hangzhou Youngsun Intelligent Equipment Co., Ltd. – Known for exporting palletizing systems to various global suppliers, indicating robust manufacturing capabilities.
By leveraging data from these resources, stakeholders can make informed decisions when selecting Chinese manufacturers for their palletizer system needs, ensuring they choose reputable and technologically advanced partners.

Price Cost Research for palletizer systems manufacturers Companies in China, use temu.com and 1688.com
Certainly! Here’s a concise overview of palletizer systems manufacturers in China with pricing details sourced from Temu.com and 1688.com.
### Temu.com
1. Jingsu King Plus Machinery Manufacturing Co., Ltd.
– Model: KP-PZ120
– Price: $25,000 – $35,000 per unit
– Features: Robotic arm, touch screen interface, customizable configurations.
2. Wuxi Hyber Co., Ltd.
– Model: HYP-2200
– Price: $18,000 – $25,000 per unit
– Features: High-speed operations, energy-efficient, extensive warranty.
### 1688.com
3. Shenzhen Jiawei Intelligent Equipment Co., Ltd.
– Model: JW-PZ180
– Price: Â¥120,000 – Â¥180,000 (approx. $17,000 – $26,000) per unit
– Features: Compact design, easy integration with existing systems, real-time monitoring.
4. Guangzhou Tekwell Machinery Co., Ltd.
– Model: TKW-PZ200
– Price: Â¥150,000 – Â¥200,000 (approx. $21,000 – $28,000) per unit
– Features: Advanced robotics, high payload capacity, user-friendly interface.
### Summary
– Price Range: $17,000 – $35,000 per unit.
– Key Features: Most manufacturers offer models equipped with robotic arms, high-speed operations, and user-friendly interfaces.
– High-End Options: Higher-priced units typically include advanced robotics and customization.
– Budget-Friendly Options: Models around the $18,000 to $20,000 range offer essential features with good efficiency and reliability.
For detailed specifications and purchasing, visiting Temu.com and 1688.com will provide comprehensive insights and contact details of the suppliers.
Note: Prices are subject to change and may vary based on specific configurations and additional features requested. Always directly inquire with manufacturers for the most current pricing and options.
Shipping Cost for palletizer systems import from China
Shipping costs for palletizer systems imported from China can fluctuate based on several key factors:
1. Weight and Dimensions: The size and weight of a palletizer system greatly influence shipping costs. Bulkier or heavier systems generate higher charges, relevant whether you’re transporting via air or sea.
2. Shipping Method:
– Air Freight: Fastest, ideal for urgent deliveries; more expensive, calculated on chargeable weight (whichever is greater between volumetric weight and actual weight).
– Sea Freight: Cost-effective for less urgent, bulk shipments; calculated based on container size (e.g., 20-foot, 40-foot containers) and weight.
3. Incoterms: Specific terms (EXW, FOB, CIF, DDP) clarify cost-bearing responsibilities between seller and buyer. FOB (Free On Board) may offer greater control and transparency for the buyer.
4. Destination: Shipping costs vary by destination, influenced by distance, port fees, and customs tariffs.
5. Additional Costs:
– Customs Duties and Taxes: Varies by country and product.
– Insurance: Coverage during transit.
– Handling Fees: Port handling, inland transport fees, and terminal charges.
6. Freight Forwarders: Utilize freight forwarders who offer competitive quotes and logistics management. Costs typically include shipping, customs brokerage, and delivery to your final location.
Estimated Costs:
– Air Freight: Approximately $1.50 to $5 per kg (subject to high fluctuation).
– Sea Freight:
– 20-foot container: Roughly $1000-$2000.
– 40-foot container: $2000-$3000.
Example:
For a 40-foot container full of palletizer systems weighing 15 tons:
– Sea Freight: Around $2500.
– Additional Costs: Customs duties, taxes, insurance, handling (e.g., $1000-$2000).
Conclusion: For the most accurate estimate, provide specifics (dimensions, weight, destination) to freight forwarders for tailored quotes.
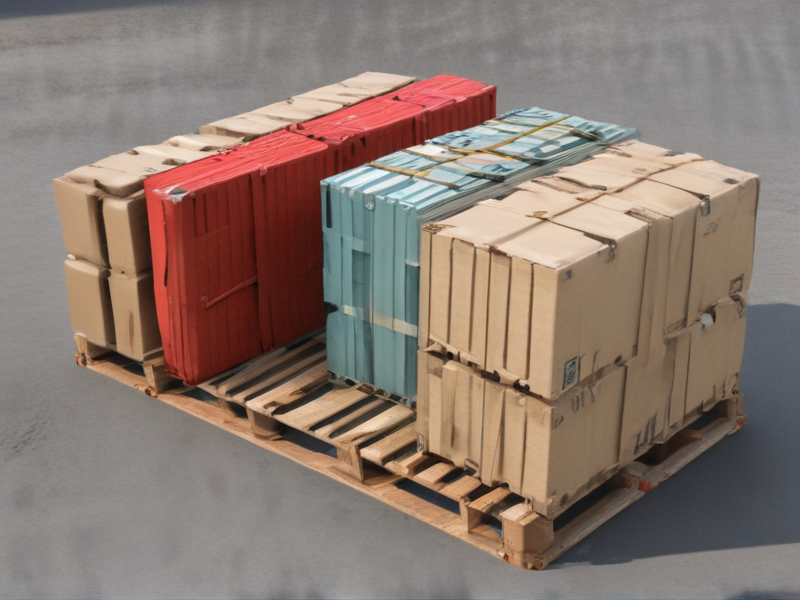
Compare China and Other palletizer systems Markets: Products Quality and Price,Visible and Hidden Costs
When comparing China’s palletizer systems market to other international markets, several factors come into play: product quality, price, and costs (both visible and hidden).
Product Quality:
Chinese palletizers often come with a lower upfront cost but can vary widely in quality. High-end manufacturers in China have significantly improved, offering robust and sophisticated systems. However, variability remains, making it essential to scrutinize supplier reputation and product reviews. In contrast, palletizers from regions like North America, Europe, and Japan are generally recognized for superior and consistent quality, reliability, and advanced technology due to stringent manufacturing standards.
Price:
The price of Chinese palletizers is typically lower, often by 20-40%, due to reduced labor costs and economies of scale. This cost advantage is appealing for budget-conscious businesses or those new to automation. However, systems from other regions, while more expensive, often justify their higher price through enhanced performance, longevity, and support services.
Visible and Hidden Costs:
Visible costs include the upfront price and shipping. Chinese palletizers’ initial costs are lower, but long-term use reveals hidden costs like maintenance, parts replacement, and downtime, which can erode the initial savings. Conversely, palletizers from well-established markets, despite a higher purchase price, may incur lower hidden costs due to better longevity, efficiency, and robust after-sales support.
In summary, China’s palletizer market offers a cost-effective entry point with a variable quality spectrum, potentially higher long-term maintenance costs, and uneven after-sales support. Other markets provide higher initial investment with dependable quality, better performance, and reduced hidden costs over time, making them suitable for organizations prioritizing reliability and long-term efficiency.
Custom Private Labeling and Branding Opportunities with Chinese palletizer systems Manufacturers
Custom private labeling and branding opportunities with Chinese palletizer systems manufacturers offer a strategic advantage for businesses looking to enhance their market presence and differentiate their products. Many Chinese manufacturers specialize in producing high-quality palletizer systems at competitive prices, making them ideal partners for custom branding initiatives.
Benefits of Custom Private Labeling:
1. Brand Recognition: Customized branding allows companies to imprint their logo, design, and unique features on the palletizer systems, fostering brand recognition and loyalty.
2. Market Differentiation: With private labeling, businesses can tailor the design and functionality to meet specific market needs, effectively differentiating from generic offerings.
3. Cost Efficiency: Chinese manufacturers often provide cost-effective solutions for customization due to lower production expenses and economies of scale.
4. Quick Turnaround: Efficient production processes and advanced technology enable faster turnaround times for custom orders, facilitating timely market entry.
Steps to Engage with Chinese Manufacturers:
1. Research and Select Manufacturers: Identify reputable Chinese manufacturers with proven expertise in palletizer systems. Conduct due diligence to ensure quality standards and reliability.
2. Define Customization Requirements: Clearly outline the branding elements, design specifications, and performance criteria you need. This includes logos, color schemes, and any unique features.
3. Request Prototypes: Collaborate with the manufacturer to develop prototypes of the customized palletizer systems. This phase is crucial for assessing quality and ensuring specifications are met.
4. Negotiate Terms: Discuss pricing, minimum order quantities, lead times, and other essential terms. Ensure that agreements are documented and clear.
5. Quality Control and Compliance: Implement rigorous quality control measures to ensure that the final product meets all regulatory standards and aligns with your brand’s quality expectations.
By partnering with Chinese palletizer systems manufacturers, businesses can leverage custom private labeling to enhance brand identity, offer unique products, and achieve competitive advantage in their markets.
Tips for Procurement and Considerations when Purchasing palletizer systems
When purchasing a palletizer system, careful consideration and strategic planning are essential to ensure optimal performance and value. Here are some key tips and considerations:
1. Assess Needs: Identify your specific requirements such as speed, load capacity, space constraints, and integration with existing systems. Determine whether a high-level, low-level, or robotic palletizer suits your needs.
2. Budget and ROI: Establish a clear budget, factoring in not just the purchase price but also installation, training, and maintenance costs. Evaluate the expected return on investment (ROI) by considering labor savings, improved efficiency, and reduced product damage.
3. Supplier Reputation: Research potential suppliers, focusing on their reputation, customer service, and post-sale support. Look for references, reviews, and case studies of similar installations.
4. Customizability and Flexibility: Ensure the system can be customized to handle different product types and pallet patterns. Flexibility in adapting to future changes in production or packaging is invaluable.
5. Technology and Compatibility: Opt for modern systems with advanced technology such as automated changeovers, diagnostics, and remote monitoring. Check compatibility with existing warehouse management systems (WMS) and manufacturing execution systems (MES).
6. Reliability and Durability: Invest in a robust system designed for long-term reliability. Consider the build quality and the reputation of the system’s components.
7. Safety Features: Ensure the system includes comprehensive safety features to protect operators and mitigate workplace hazards. Compliance with safety standards is crucial.
8. Energy Efficiency: Energy-efficient systems can reduce operational costs and support sustainability goals. Evaluate the energy consumption of different models.
9. Training and Support: Confirm that the supplier provides thorough training for operators and maintenance staff. Ongoing support and readily available spare parts are also critical.
10. Trial and Testing: If possible, test the system with your product before purchase to ensure it meets your operational requirements.
By addressing these considerations, you can select a palletizer system that enhances productivity and aligns with your operational goals.
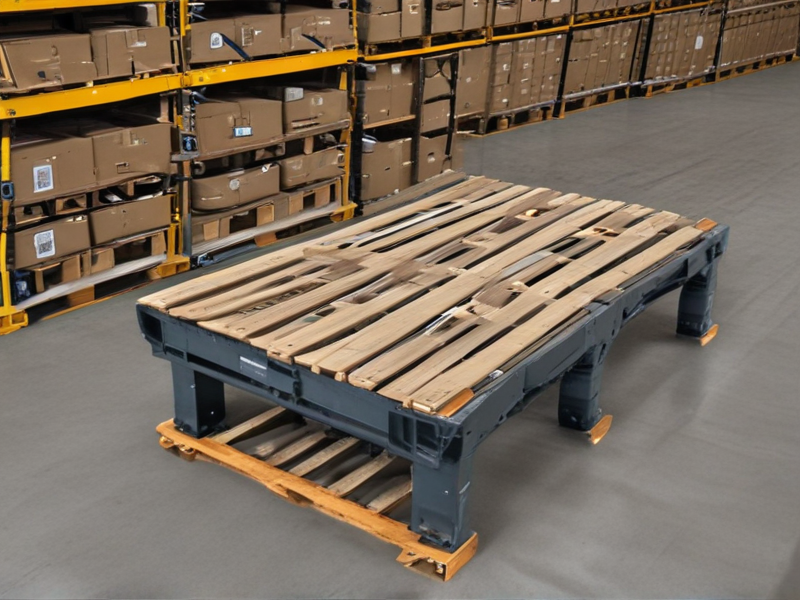
FAQs on Sourcing and Manufacturing palletizer systems in China
### Frequently Asked Questions on Sourcing and Manufacturing Palletizer Systems in China
1. Why Source Palletizer Systems from China?
– Cost-Effectiveness: Lower manufacturing and labor costs.
– Advanced Manufacturing Capabilities: Use of cutting-edge technology and equipment.
– Large Selection: Wide variety of palletizer systems catering to different needs.
2. How Do I Choose the Right Supplier?
– Research: Look for ISO-certified manufacturers.
– Reputation: Check reviews, references, and company history.
– Visit Facilities: If possible, visit manufacturing plants to ensure quality control.
3. What Should I Consider Regarding Quality?
– Certifications: Ensure compliance with international standards like CE or UL.
– Material and Components: Verify the quality of materials and components used.
– Testing and Inspection: Ask for detailed reports on product testing and quality inspections.
4. Can I Customize My Palletizer System?
– Customization Options: Many Chinese manufacturers offer customization based on your specific needs.
– Lead Time: Customization may extend the lead time, so plan accordingly.
5. What are the Average Lead Times?
– Standard Models: Typically 1-2 months.
– Custom Models: Could extend to 3-6 months, depending on complexity.
6. How Does Shipping and Logistics Work?
– Incoterms: Familiarize yourself with terms like FOB, CIF, and DDP.
– Logistics Partner: Work with a reliable logistics company to handle shipping.
– Customs: Ensure all paperwork is correctly prepared to avoid customs delays.
7. What are the Payment Terms?
– Common Terms: 30% deposit and the remaining 70% before shipment.
– Methods: Bank transfers (T/T), Letters of Credit (L/C).
8. Are There Risks Involved?
– Quality: Risk of receiving low-quality products.
– Communication Barriers: Language differences and time zone challenges.
– Scams: Always vet suppliers thoroughly to avoid fraudulent companies.
9. How Do I Mitigate Risks?
– Contracts: Detailed contracts specifying standards, penalties, and warranties.
– Third-Party Inspections: Hire independent inspectors to check product quality.
– Regular Communication: Maintain constant communication to solve issues promptly.