Top 10 end of line packaging solutions in China introduce,list main products and website if have
Certainly! Here are the top 10 end-of-line packaging solution providers in China:
1. SaintyCo
Main Products: Tablet presses, packaging machines, and blister packaging solutions.
Website: [saintyco.com](https://www.saintyco.com/)
2. SaintyTec
Main Products: Liquid filling machines, capping machines, and labeling machines.
Website: [saintytec.com](http://www.saintytec.com/)
3. Wenzhou Accurate Machinery Manufacturing Co., Ltd.
Main Products: Cartoning machines, case packers, and palletizers.
Website: [accuratepack.com](http://www.accuratepack.com/)
4. Jiangsu Tom Packaging Machinery Co., Ltd.
Main Products: Stretch wrapping machines, shrink wrappers, and strapping machines.
Website: [tom-pack.com](http://www.tom-pack.com//)
5. Zhongshan Tentop Fine Machinery Co., Ltd.
Main Products: Automatic cartoning machines, case erectors, and robotic palletizing systems.
Website: [tentop.com.cn](http://www.tentop.com.cn//)
6. Ruian Honetop Machinery Co., Ltd.
Main Products: Carton forming machines, multi-function packing machines, and overwrapping machines.
Website: [honetop.com](https://www.honetop.com/)
7. Shanghai Kesi Pack Co., Ltd.
Main Products: Customized end-of-line solutions, including conveyor systems and packaging line automation.
Website: [kesipack.com](http://www.kesipack.com/)
8. Shanghai Shenhu Packaging Machinery Equipment Co., Ltd.
Main Products: Vertical form fill seal machines, horizontal pouch packing machines, and case sealers.
Website: [shenhuma.com](https://www.shenhuma.com/)
9. Guangzhou XTime Packaging Equipment Co., Ltd.
Main Products: Filling machines, capping machines, and labeling systems.
Website: [xtpackagingmachine.com](http://www.xtpackagingmachine.com/)
10. Zhejiang Dingye Machinery Co., Ltd.
Main Products: Sealing machines, vacuum packaging machines, and strapping machines.
Website: [dingye.com.cn](http://www.dingye.com.cn/)
These companies are known for providing advanced, efficient, and reliable end-of-line packaging solutions tailored for various industries.
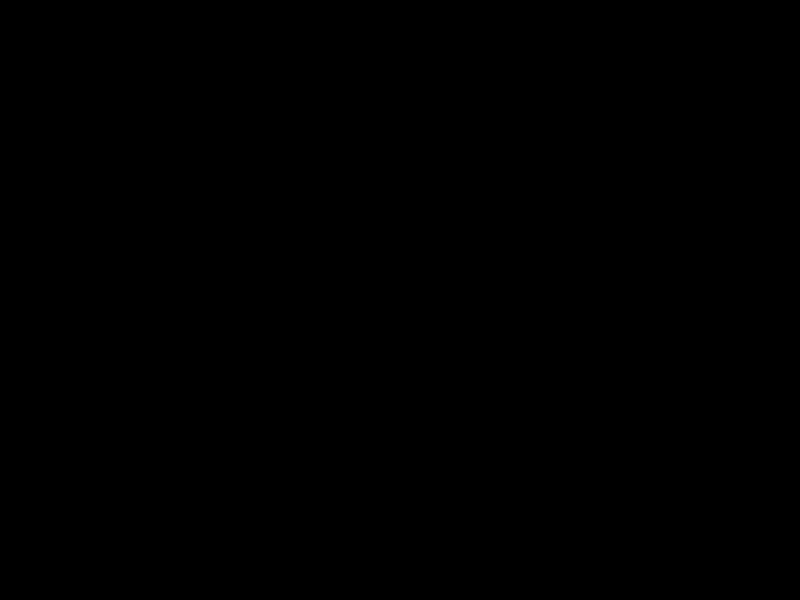
Types of end of line packaging solutions
End-of-line packaging solutions are crucial in optimizing the final stages of production, ensuring products are efficiently and securely packed for distribution. Various types of solutions cater to different packaging needs:
1. Case Erectors and Sealers: These machines automatically form corrugated boxes and seal them after they are packed with products, enhancing productivity and uniformity.
2. Palletizers: Automated palletizing systems arrange cartons, bags, or other packaging units onto pallets in a consistent pattern, reducing manual labor and increasing throughput.
3. Shrink Wrappers: These units apply heat-shrinkable plastic films over products or pallets, providing a secure and tamper-evident seal, ideal for both single items and bulk packaging.
4. Stretch Wrappers: Machines that wrap stretch film around pallets to stabilize and protect goods during transportation. Options include semi-automatic and fully automatic stretch wrappers.
5. Cartoning Machines: These automate the process of forming, loading, and closing cartons, providing a versatile solution for various product sizes and types.
6. Strapping Machines: Used for binding boxes and packages with plastic or metal straps, ensuring the goods are tightly secured, especially during transit.
7. Labeling Systems: Automated label applicators that precisely place labels on products, boxes, or pallets, improving accuracy and traceability.
8. Robotic Systems: Robots equipped with end-of-arm tools can perform various packaging tasks such as picking, placing, packing, and palletizing, offering flexibility and reducing labor costs.
9. Conveyors: These transport products and packages between different end-of-line machines, maintaining a continuous flow and improving efficiency.
10. Void Fillers and Cushioning Systems: These include machines that dispense and place materials like air pillows, foam inserts, and paper to fill empty spaces and protect products inside boxes.
By integrating these solutions, businesses can enhance packaging efficiency, ensure product protection, and reduce labor costs, ultimately leading to smoother operations and higher customer satisfaction.
Pros and Cons of Using end of line packaging solutions
### Pros of Using End-of-Line Packaging Solutions
1. Efficiency: Automating packaging processes significantly speeds up production lines, reducing bottlenecks and increasing throughput.
2. Consistency: Automated systems ensure uniform packaging, which enhances product presentation and reduces errors associated with manual packaging.
3. Cost Savings: Although the initial investment is high, automation leads to long-term savings by reducing labor costs and minimizing material waste.
4. Scalability: As demand grows, automated end-of-line packaging systems can be scaled up easily, ensuring that production keeps pace with market requirements.
5. Safety: Automation reduces human involvement in potentially hazardous tasks, thereby lowering the risk of workplace injuries.
6. Traceability: Advanced systems often come with tracking features, making it easier to trace product batches and manage inventory efficiently.
### Cons of Using End-of-Line Packaging Solutions
1. High Initial Cost: The capital expenditure for advanced packaging machinery can be substantial, which might be a barrier for smaller businesses.
2. Maintenance: These systems require regular maintenance and occasional technical support, which can add to operational costs.
3. Complex Setup: Implementing and integrating these systems into existing production lines can be complex and time-consuming.
4. Job Displacement: Increased automation can lead to reduced demand for manual labor, potentially resulting in job losses.
5. Dependency on Technology: Over-reliance on automated systems can make operations vulnerable to technical glitches and failures, which could disrupt production.
6. Training Requirements: Staff need to be trained to operate and maintain these systems, which requires time and resources.
In summary, while end-of-line packaging solutions offer significant benefits in terms of efficiency, consistency, and long-term cost savings, they also come with challenges like high initial costs, maintenance, and potential job displacement. Businesses must weigh these pros and cons to determine if such systems align with their operational goals and capabilities.
end of line packaging solutions Reference Specifications (varies for different product)
End of line packaging solutions are crucial for optimizing the final stages of production. These systems automate processes like case packing, sealing, palletizing, and labeling, ensuring efficiency and consistency. Various types of equipment, each with specific reference specifications, cater to different product needs. Below are some general specifications for key end-of-line packaging equipment:
1. Case Packing Machines
– Types: Horizontal, Vertical, Wraparound
– Speed: 10-200 cases per minute
– Product Size Range: Adjustable to handle diverse dimensions
– Material Handling: Corrugated trays, RSC cases, wraparound blanks
2. Case Sealers
– Sealing Methods: Tape, Glue, or Staples
– Speed: 10-150 cases per minute
– Case Size: Width: 0-30 inches, Height: 0-25 inches
– Adjustability: Tool-free, quick changeovers
3. Palletizers
– Types: Conventional, Robotic
– Speed: Up to 120 cases per minute
– Load Capacity: From 50 lbs to over 1000 lbs per pallet
– Pattern Flexibility: Programming capability for varied stacking patterns
4. Stretch Wrappers
– Types: Turntable, Rotary Arm, or Ring
– Wrap Speed: Up to 40-60 loads per hour
– Pre-Stretch Capability: 200%-300%
– Load Weight: Up to 5000 lbs
5. Labeling Systems
– Types: Print-and-Apply, Pre-Printed Labels
– Speed: Up to 150 labels per minute
– Label Size: Width: 1-6 inches, Length: 1-12 inches
– Print Resolution: Up to 600 dpi
These specifications vary depending on the product’s characteristics, production speed requirements, and packaging materials used. Customizable features and automation levels, such as integration with warehouse management systems and IoT capabilities, further enhance adaptability and efficiency.
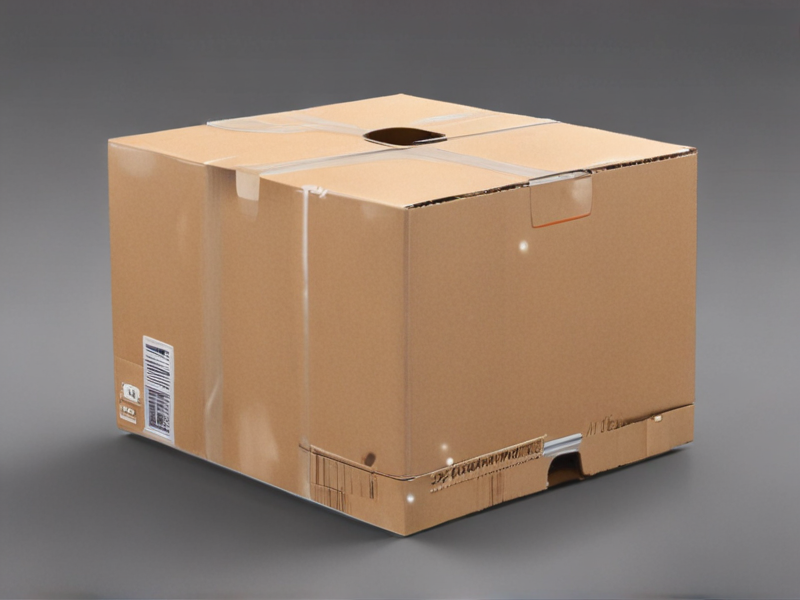
Applications of end of line packaging solutions
End-of-line (EOL) packaging solutions are integral to the efficiency, speed, and cost-effectiveness of various industries. These solutions encompass technologies and equipment that are employed during the final stages of the production process to prepare goods for distribution and sale. The applications of EOL packaging solutions are numerous, spanning several critical aspects of production and logistics:
1. Product Wrapping: Ensures products are securely wrapped to prevent damage during transit. This includes shrink-wrapping, stretch-wrapping, and banding.
2. Cartoning and Case Packing: Involves automated machinery that arranges products into cartons or cases. This is essential for industries like food and beverage, pharmaceuticals, and consumer goods to maintain product integrity and streamline handling.
3. Palletizing: Automated palletizers stack products onto pallets for storage or shipment. This is crucial for managing large volumes efficiently and is widely used in manufacturing and warehousing environments.
4. Labeling and Coding: EOL solutions often integrate labeling and coding technologies to apply necessary product information, including barcodes, QR codes, expiry dates, and batch numbers. This ensures regulatory compliance and enhances traceability.
5. Inspection and Quality Control: Advanced EOL systems can include inspection units that verify product quality and packaging integrity. This minimizes the risk of defects reaching the consumer, which is vital for maintaining brand reputation, especially in pharmaceutical and food sectors.
6. Serialization: Particularly important for pharmaceuticals, serialization involves assigning unique identifiers to each product to prevent counterfeiting and ensure traceability throughout the supply chain.
7. Customization and Flexibility: Modern EOL packaging solutions are designed for flexibility to accommodate various product sizes, shapes, and packaging types. This is essential for industries that face frequent changes in packaging requirements.
8. Environmental Impact: EOL solutions can incorporate sustainable packaging practices, such as using recyclable materials or minimizing excess packaging, contributing to environmental conservation efforts.
Overall, EOL packaging solutions play a pivotal role in enhancing operational efficiency, product protection, compliance, and sustainability across diverse industries.
Material of end of line packaging solutions
End-of-line packaging solutions involve the final steps in the packaging process where products are sealed, boxed, and prepared for shipment. Key materials used in these solutions include:
1. Corrugated Fiberboard:
– Widely used for shipping boxes, corrugated fiberboard combines strength, lightweight properties, and cost-effectiveness. It offers excellent protection for various products during transit.
2. Plastic Films:
– Stretch films and shrink wraps are essential for securing products on pallets. Stretch film is typically made from linear low-density polyethylene (LLDPE), providing elasticity and tensile strength. Shrink film, usually polyolefin or polyvinyl chloride (PVC), conforms tightly around products when heat is applied, offering stability and protection.
3. Adhesives:
– Tapes and hot melt adhesives are crucial for sealing boxes. Pressure-sensitive tapes often use polypropylene or polyester backings. Hot melt adhesives, based on thermoplastic polymers, provide quick bonding and durability.
4. Foam and Cushioning Materials:
– Polyethylene (PE) and polyurethane (PU) foams are common cushioning materials that protect sensitive items from shocks and vibrations. These materials can be tailored to fit specific product shapes, ensuring maximum protection.
5. Strapping Materials:
– Polypropylene (PP) and polyester (PET) straps are used to secure boxes and pallets. PP is cost-effective for lighter loads, while PET offers higher strength and is suitable for heavier, more demanding applications.
6. Biodegradable and Recyclable Options:
– With increasing emphasis on sustainability, biodegradable plastics and recyclable paper-based materials are gaining traction. These alternatives help in reducing the environmental impact of packaging waste.
In conclusion, end-of-line packaging solutions utilize a variety of materials tailored to provide protection, stability, and efficiency during the shipping process. Emphasis on sustainability is driving innovation in this sector, with new materials emerging to meet eco-friendly standards.
Quality Testing Methods for end of line packaging solutions and how to control the quality
Ensuring the quality of end-of-line packaging solutions is critical for maintaining product integrity and customer satisfaction. Here are key quality testing methods and control measures:
1. Visual Inspection: Regular visual checks for defects such as misalignment, tears, or incorrect labeling can catch obvious issues early. Automated vision systems enhance accuracy and consistency.
2. Weight Checks: Automated scales ensure packages meet specified weight requirements. Discrepancies can indicate missing or excess components, prompting further investigation.
3. Seal Integrity Testing: Seals are crucial for protecting contents. Techniques like dye penetration and vacuum decay tests can confirm seal strength and consistency.
4. Drop Test: Simulating shipping conditions through controlled drops helps assess the packaging’s ability to protect its contents during transit.
5. Compression Strength Test: This measures how much weight a package can withstand in stacked storage, ensuring it doesn’t get crushed under pressure.
6. Vibration Test: Simulating transport vibrations in a lab environment identifies potential weaknesses in packaging that could be exacerbated during shipping.
7. Barcode Verification: Ensuring barcodes are correctly printed and scannable prevents issues in inventory management and retail operations.
8. Temperature and Humidity Testing: Exposure to extreme conditions can test material resilience, ensuring that packaging can withstand various environments.
Quality Control Measures:
– Standard Operating Procedures (SOPs): Detailed procedures for each step in the packaging process ensure every worker follows the same quality standards.
– Random Sampling: Regular sampling of products for detailed quality checks can identify trends before they become serious issues.
– Employee Training: Well-trained employees are more likely to spot and correct issues early.
– Feedback Loops: Collecting and analyzing feedback from customers and end-users can highlight recurring problems and areas for improvement.
Implementing these testing methods and control measures creates a robust quality assurance system, safeguarding both product and brand reputation.
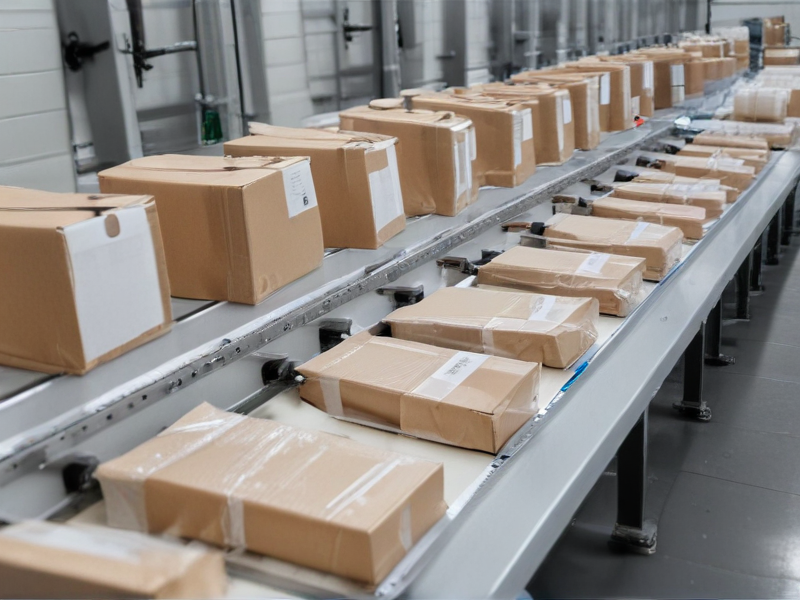
The Work Process and how to use end of line packaging solutions
End-of-line packaging solutions are critical in manufacturing and distribution processes, ensuring efficiency, product safety, and streamlined logistics. The work process for integrating and using these solutions involves several key steps:
1. Assessment and Planning:
– Analyze Requirements: Understand product types, packaging needs, and throughput rates.
– Define Objectives: Set goals such as reducing manual labor, improving packaging speed, and enhancing product protection.
– Choose Equipment: Select appropriate machinery like case packers, palletizers, shrink-wrap machines, or labeling units based on requirements.
2. Design and Layout:
– Workflow Layout: Design the physical layout of the packaging area for smooth movement of goods with minimal bottlenecks.
– Integrate Systems: Ensure that packaging equipment integrates seamlessly with upstream production and downstream logistics.
3. Installation and Configuration:
– Setup Equipment: Install and configure machinery according to the manufacturer’s guidelines.
– Connect Controls: Integrate control systems for automation; this often involves PLCs (Programmable Logic Controllers).
– Safety Checks: Implement safety protocols and emergency stops to ensure worker safety.
4. Training and Testing:
– Staff Training: Train operators on using the machinery, troubleshooting common issues, and maintenance routines.
– Trial Runs: Conduct initial test runs to verify that systems work correctly and meet performance targets.
5. Operation and Monitoring:
– Regular Operation: Use machines for packaging tasks, ensuring that operations align with production schedules.
– Quality Checks: Regularly inspect the quality of packaging, ensuring it meets standards.
– Monitor Performance: Track machine performance and throughput to identify any inefficiencies or maintenance needs.
6. Maintenance and Improvement:
– Routine Maintenance: Follow a scheduled maintenance plan to reduce downtime and extend equipment life.
– Continuous Improvement: Collect data to identify areas for improvement and adjust processes or equipment as necessary.
By meticulously following these steps, businesses can effectively implement end-of-line packaging solutions, enhancing overall operational efficiency, product integrity, and customer satisfaction.
end of line packaging solutions Importing questions including Cost,Supplier,Sample,Certification and Market
When considering importing end-of-line packaging solutions, it’s essential to evaluate several key factors:
1. Cost: Determine both upfront costs (including machinery, shipping, taxes, and duties) and operational costs (energy consumption, maintenance, and labor). Request comprehensive quotations to compare prices and understand the cost-benefit ratio.
2. Supplier: Research potential suppliers thoroughly. Evaluate their reputation, reliability, and customer service. It’s advisable to check reviews, request case studies, and look for any red flags regarding delivery times or product quality.
3. Sample: Before making a large investment, ask for samples or a demonstration of the equipment. This allows you to assess the quality and suitability of the packaging solutions for your specific needs. Some suppliers might offer virtual demos or trial periods.
4. Certification: Verify if the equipment complies with local regulatory standards and certifications (e.g., CE, UL, ISO). Ensuring compliance is critical to avoid legal issues and to guarantee safety and performance standards.
5. Market: Analyze the market demand for the type of packaging solution you are importing. Understand your industry’s needs, potential clients, and competitors. Identifying a niche or unique selling proposition (USP) can also help in effectively positioning your product.
Conducting a thorough analysis of these facets will help in making a well-informed decision, ensuring that the imported packaging solutions meet your business’s needs and support its growth effectively.
How to find and select check reliable end of line packaging solutions manufacturers in China
Finding and selecting reliable end-of-line packaging solutions manufacturers in China involves careful research and due diligence. Here’s a streamlined approach to help you:
1. Online Research:
– Use platforms like Alibaba, Made-in-China, and Global Sources to find manufacturers.
– Filter your search to focus on those with high ratings, good reviews, and industry certifications (ISO 9001, CE, etc.).
2. Evaluate Credibility:
– Check for certifications and compliance with international standards.
– Review the company’s years in business and their production capacity.
– Look for customer reviews and case studies showcasing successful projects.
3. Request Quotations:
– Contact multiple manufacturers to get quotations.
– Assess the responsiveness and professionalism of their sales team.
– Compare pricing, but also consider quality and service.
4. Assess Quality:
– Request product samples if possible.
– Ask for details about quality control processes.
– Consider commissioning a third-party inspection service to verify product quality.
5. Visit Facilities:
– If feasible, visit the manufacturer’s facility to see their operations firsthand.
– Evaluate the production process, equipment, and workforce.
6. Check References:
– Request references from existing clients.
– Contact references to get direct feedback on the manufacturer’s reliability and product quality.
7. Review Contracts:
– Ensure contracts clearly outline terms, pricing, delivery schedules, and quality expectations.
– Clarify any warranties or service agreements.
By following these steps, you can effectively identify and collaborate with a reliable end-of-line packaging solutions manufacturer in China. Proper vetting ensures you receive quality products and dependable service.
Background Research for end of line packaging solutions manufacturers Companies in China, use qcc.com archive.org importyeti.com
End-of-line packaging solutions are critical for ensuring that products are securely packaged and ready for distribution. China has emerged as a key player in manufacturing these solutions, catering to both domestic and international markets. Below is an overview of notable companies in China, gathered using qcc.com, archive.org, and importyeti.com.
1. Hefei Saimo Technology Co., Ltd.
Hefei Saimo Technology offers a range of packaging solutions including palletizers, stretch wrapping machines, and case packers. Their products are known for their automation capabilities, offering high efficiency and precision. Research from qcc.com shows they have a significant market presence and have been expanding their product lines to cater to diverse industrial needs.
2. Shanghai Kuko Packing Machinery Co., Ltd.
Specializing in shrink wrapping machines and case sealers, Shanghai Kuko is a well-established name in the packaging machinery sector. Archive.org reveals a history of innovation and adaptation to modern packaging requirements, with a focus on customizable solutions to meet different client demands.
3. Gurki Packaging Machine Co., Ltd.
Based in Shenzhen, Gurki Packaging Machine provides comprehensive packaging solutions including E-commerce logistics packaging machines and automatic carton erectors. Importyeti.com highlights their robust export network, indicating a strong international presence particularly in North America and Europe.
4. Youngsun Intelligent Equipment Co., Ltd.
This company offers highly automated packaging solutions such as strapping machines, carton sealers, and stretch wrappers. They have a broad spectrum of applications ranging from food and beverages to electronics. Import records suggest strong partnerships with global companies, reflecting reliability and advanced technological capabilities.
5. Jochamp Machinery Co., Ltd.
Known for case packing and palletizing systems, Jochamp Machinery emphasizes capacity for customization and integration into existing manufacturing lines. Their machinery is well-regarded for durability and efficiency, according to qcc.com data, making them a preferred choice for large-scale industrial applications.
These companies represent the forefront of end-of-line packaging solutions in China, each contributing unique strengths to the market. By leveraging advanced technologies and maintaining robust export partnerships, they continue to excel in the competitive landscape of packaging machinery.

Price Cost Research for end of line packaging solutions manufacturers Companies in China, use temu.com and 1688.com
Conducting a price cost research for end-of-line packaging solutions from Chinese manufacturers can be effectively achieved using platforms like Temu.com and 1688.com. Here’s a brief overview based on recent data for 2023:
### Temu.com
Temu.com is a popular platform offering a wide range of industrial products. Searching for end-of-line packaging solutions, you’ll find various manufacturers offering equipment such as carton sealing machines, palletizers, and stretch wrapping machines.
– Carton Sealing Machines: Prices generally range from $500 to $2,000 depending on the machine’s features and automation level.
– Palletizers: These can vary significantly, from $6,000 for basic models to upwards of $50,000 for fully automated systems.
– Stretch Wrapping Machines: Prices are usually between $1,500 and $7,000, again depending on the automation and capacity.
### 1688.com
1688.com, a subsidiary of Alibaba, caters predominantly to the Chinese domestic market but is accessible globally. It offers extensive listings of end-of-line packaging machines.
– Carton Sealing Machines: Prices often range from Â¥2,000 to Â¥10,000 (approx. $300 to $1,500).
– Palletizers: These are listed between Â¥30,000 and Â¥300,000 (approx. $5,000 to $45,000), with variations depending on automation and technology.
– Stretch Wrapping Machines: Expect prices between Â¥10,000 and Â¥50,000 (approx. $1,500 to $7,500).
### Key Insights
– Bulk Discounts: Both platforms offer substantial discounts for bulk purchases.
– Customization: Many manufacturers offer customization options, impacting the final price.
– Shipping Costs: Note that shipping costs can add significantly to the total expenditure, especially for large machinery.
This analysis provides a snapshot of current market prices for end-of-line packaging solutions from Chinese manufacturers. For the most accurate and updated pricing, direct contact with suppliers via these platforms is recommended.
Shipping Cost for end of line packaging solutions import from China
When importing end-of-line packaging solutions from China, several factors influence the shipping costs. Here’s a concise breakdown of the essential considerations:
### 1. Shipping Methods:
– Sea Freight: The most cost-effective for large, heavy consignments. It typically takes 20-40 days.
– Air Freight: Faster (5-10 days) but more expensive, suitable for urgent and lighter shipments.
### 2. Costs Components:
– Freight Charges: Costs vary based on weight, volume, and the shipping method.
– Sea Freight: Charged by Full Container Load (FCL) or Less than Container Load (LCL).
– Air Freight: Charged by weight or volume (whichever is greater).
– Packaging Costs: Secure and protective packaging may add to the cost.
– Insurance: Protects against loss or damage during transit (~1-3% of the declared value).
– Customs Duties and Taxes: Import duties, VAT/GST based on the destination country’s regulations.
– Handling Fees: Port handling, delivery, and customs clearance fees.
### 3. Examples:
– Sea Freight FCL Cost: A 20-feet container might cost between $1,000 to $4,000 depending on the route and carrier.
– Air Freight Cost: Roughly $3-$8 per kg for standard services.
### 4. Calculating Overall Costs:
– Volume and Weight: Dimensional weight (LxWxH/5000) for air freight; use containers for sea freight.
– Service Providers: Compare quotes from freight forwarders or online platforms like Freightos.
### 5. Additional Tips:
– Consolidate Shipments: To optimize costs, especially for smaller volumes.
– Plan Ahead: Early booking can get better rates, particularly for sea freight.
It’s essential to work with a reliable freight forwarder to navigate these variables effectively and get accurate estimates for your specific needs.
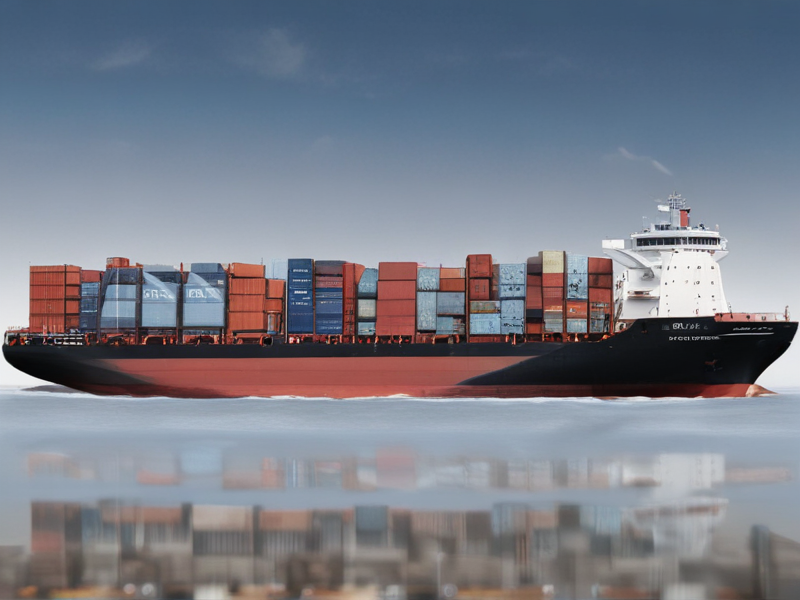
Compare China and Other end of line packaging solutions Markets: Products Quality and Price,Visible and Hidden Costs
China’s end-of-line packaging solutions are often lauded for their cost-effectiveness, making them highly competitive in global markets. Chinese manufacturers frequently offer lower initial prices due to cheaper labor costs and economies of scale. This makes their products appealing for companies prioritizing budget constraints.
However, lower price tags can sometimes come with trade-offs in product quality. While many Chinese manufacturers produce high-quality packaging technology, there are notable disparities in quality and durability. Quality control can be inconsistent, requiring buyers to conduct thorough due diligence.
In contrast, end-of-line packaging solutions from Western markets, such as the U.S. or Germany, typically boast superior build quality and advanced technological integration. These products often come with higher reliability, longer lifespan, and better after-sales support. Nonetheless, such advantages come at a higher initial cost, which can be prohibitive for some companies.
Visible costs involve the upfront price of machinery, installation, and initial training. China generally wins on this front with significantly lower prices. However, hidden costs must also be considered. These include maintenance, repair, downtime due to lower durability, and potentially longer lead times for replacement parts from distant suppliers. Hidden costs can also emerge from inefficiencies and additional training required when using less sophisticated machinery.
In summary, China’s end-of-line packaging solutions offer a cost-effective entry point, suitable for budget-conscious buyers, but may involve compromise on quality and potential hidden costs. Western alternatives, while more expensive initially, often provide better quality, reliability, and lower hidden costs, appealing to those seeking long-term value and robustness.
Custom Private Labeling and Branding Opportunities with Chinese end of line packaging solutions Manufacturers
Custom private labeling and branding with Chinese end-of-line packaging solutions manufacturers offer distinct advantages for businesses looking to enhance their market presence and product appeal. These manufacturers provide a comprehensive range of services tailored to meet diverse packaging needs, including customized designs, labeling, and branding solutions.
Advantages:
1. Cost Efficiency: China is renowned for its manufacturing capabilities at competitive prices. This allows businesses to achieve high-quality packaging without inflating costs, thus enhancing profit margins.
2. Advanced Technology: Chinese manufacturers are equipped with state-of-the-art machinery and technology, ensuring precision, innovation, and high output.
3. Customization: From custom shapes, sizes, and designs to specific branding needs like logo placement and unique color schemes, these manufacturers offer extensive customization options.
4. Scalability: Whether you need small batches or large-scale production, Chinese manufacturers can efficiently scale operations to meet your demands, ensuring timely delivery.
5. Quality Assurance: Adherence to international quality standards ensures that products meet rigorous safety and durability criteria, essential for maintaining brand reputation.
Process:
1. Initial Consultation: Discuss your brand requirements, product specifications, and desired outcomes with the manufacturer.
2. Design & Prototyping: Collaborate with design teams to create prototypes that align with your brand vision. Utilize 3D modeling and sample productions to fine-tune the design.
3. Production: Once designs are finalized, the manufacturer proceeds with mass production, employing advanced techniques like automated assembly and quality control checks.
4. Branding: Integration of your branding elements, including custom labels, logos, and packaging designs, to create a cohesive brand experience.
5. Delivery & Support: Comprehensive logistics support ensures efficient shipping. After-sales service and ongoing support are also typically available.
Partnering with Chinese end-of-line packaging solutions manufacturers for custom private labeling and branding not only streamlines the packaging process but also reinforces your brand’s market position with innovative, quality solutions tailored to your specifications.
Tips for Procurement and Considerations when Purchasing end of line packaging solutions
When procuring end-of-line packaging solutions, several key considerations ensure optimal performance, cost-effectiveness, and long-term satisfaction:
1. Define Requirements: Clearly outline your packaging needs—types of products, packaging materials, production volume, speed, and automation level. This ensures the solution aligns with your operational goals.
2. Budget Planning: Establish a realistic budget, considering not only the initial cost but also long-term expenses like maintenance, energy consumption, and potential upgrades.
3. Vendor Research: Evaluate multiple suppliers. Look for those with strong reputations, industry experience, and robust after-sales support. Assess testimonials, case studies, and references.
4. Technology and Compatibility: Choose systems compatible with your existing equipment and software. Consider future scalability and technological advancements to accommodate business growth.
5. Quality and Reliability: Prioritize high-quality machinery known for reliability and durability. Assess warranty terms and the availability of service parts.
6. Compliance and Standards: Ensure the equipment meets industry standards and regulatory requirements pertinent to your products and market.
7. Customization and Flexibility: Opt for solutions offering customization to handle different packaging types and sizes effortlessly. Flexible systems can adapt to changes in product lines and packaging trends.
8. Training and Support: Confirm that the supplier provides comprehensive training for your staff and robust ongoing technical support to minimize downtime.
9. Maintenance and Upkeep: Factor in maintenance ease and the cost of consumables. Preventive maintenance plans can enhance uptime and longevity.
10. Environmental Considerations: Evaluate the system’s environmental impact, including energy efficiency and waste reduction capabilities. Sustainable solutions align with modern corporate responsibility initiatives.
11. ROI Analysis: Conduct a thorough return on investment analysis to justify the purchase. Include productivity gains, labor savings, and potential quality improvements.
By considering these aspects, you can select an end-of-line packaging solution that enhances operational efficiency, minimizes costs, and supports your long-term business goals.
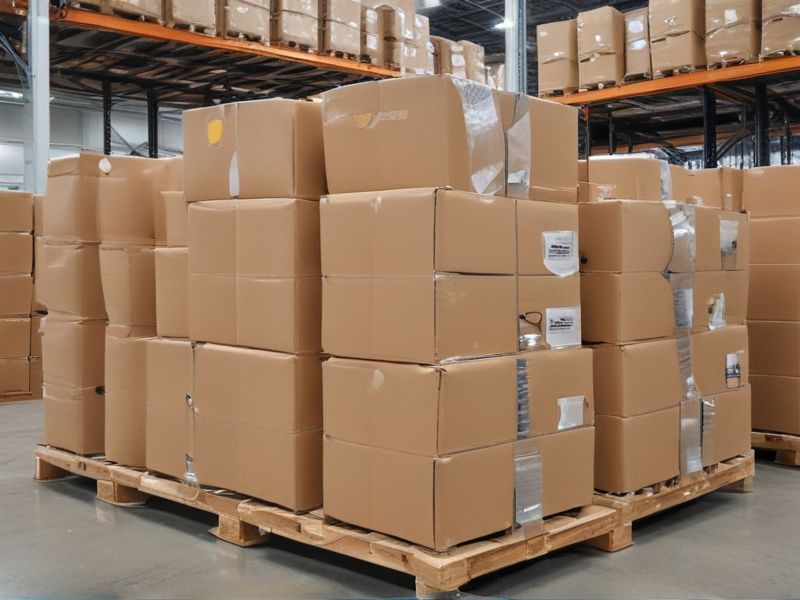
FAQs on Sourcing and Manufacturing end of line packaging solutions in China
### FAQs on Sourcing and Manufacturing End-of-Line Packaging Solutions in China
1. What are end-of-line packaging solutions?
End-of-line packaging solutions refer to machinery and systems used in the final stages of production to prepare products for shipment. This includes case packers, palletizers, shrink-wrap machines, and conveyor systems.
2. Why source end-of-line packaging solutions from China?
China is a global manufacturing hub offering cost advantages, a wide range of suppliers, rapid production capabilities, and advancements in automation technologies. Companies can benefit from competitive pricing and innovative packaging solutions.
3. How do I identify reliable suppliers in China?
Use reputable sourcing platforms like Alibaba, Global Sources, and Made-in-China. Conduct thorough background checks, request samples, and verify certifications such as ISO and CE standards. Visiting trade shows and factory audits are also beneficial.
4. What are the key considerations when selecting a Chinese manufacturer?
Evaluate the manufacturer’s experience, production capacity, quality control processes, lead times, and after-sales support. Clear communication and established contracts outlining specifications and deadlines are crucial.
5. Are there any language or cultural barriers?
Language can be a barrier, but many international-facing companies have English-speaking staff. Understanding cultural nuances and building relationships can aid negotiations and project management.
6. How do I ensure quality control?
Implement rigorous quality assurance processes including third-party inspections, factory audits, and pre-shipment inspections. Collaboration with a local agent or quality control company can help maintain standards.
7. What are the shipping logistics involved?
Choose between air freight for speed or sea freight for cost-efficiency. Ensure compliance with international shipping regulations. Partnering with a reliable freight forwarder can simplify customs clearance and logistics management.
8. What are the typical lead times?
Lead times vary depending on the complexity of machinery and order size. Typically, it ranges from 30 to 90 days, including production and shipping. Plan accordingly to accommodate potential delays.
9. Are technical support and training available?
Many Chinese manufacturers offer remote or on-site technical support and training. Ensure these services are part of the agreement to facilitate smooth installation and operation of equipment.
10. How do I manage intellectual property (IP) concerns?
Protect IP by using Non-Disclosure Agreements (NDAs) and working with reputable manufacturers. Registering patents and trademarks in China can also provide legal recourse in case of infringement.
Finding the right partner for end-of-line packaging solutions in China requires due diligence but can lead to significant cost savings and operational efficiencies.