Top 10 robotic packaging systems in China introduce,list main products and website if have
Sure, here is a brief overview of the top 10 robotic packaging systems in China, their main products, and websites if available.
1. **SIASUN Robot & Automation Co., Ltd.**
– **Main Products:** Industrial robots, packaging robots, automated guided vehicles.
– **Website:** [siasun.com](http://www.siasun.com)
2. **GSK CNC Equipment Co., Ltd.**
– **Main Products:** Robotic palletizers, pick-and-place robots, industrial robots.
– **Website:** [www.gsk.com.cn](http://www.gsk.com.cn)
3. **STEP Electric Corporation**
– **Main Products:** Robotic arms, industrial robots for packaging, robotic controllers.
– **Website:** [www.stepelectric.com](http://www.stepelectric.com)
4. **Tianjin EasyRobot Technology Co., Ltd.**
– **Main Products:** Collaborative packaging robots, automation systems.
– **Website:** [www.easyrobot.com.cn](http://www.easyrobot.com.cn)
5. **EFORT Intelligent Equipment Co., Ltd.**
– **Main Products:** Automated robotic systems for packaging, industrial robots.
– **Website:** [www.efort.com.cn](http://www.efort.com.cn)
6. **Aubo Robotics**
– **Main Products:** Collaborative robots for packaging, industrial automation solutions.
– **Website:** [www.aubo-robotics.cn](http://www.aubo-robotics.cn)
7. **Googol Technology (HK) Ltd.**
– **Main Products:** Motion controllers, industrial robotic arms for packaging.
– **Website:** [www.googoltech.com](http://www.googoltech.com)
8. **HRG Robotics (HIT Robot Group)**
– **Main Products:** Packaging robots, conveyor automation systems, robotic integration.
– **Website:** [www.hitrobotgroup.com](http://www.hitrobotgroup.com)
9. **ESTUN Automation Technology Co., Ltd.**
– **Main Products:** Robotic arms, packaging automation solutions.
– **Website:** [www.estuneurope.com](http://www.estuneurope.com)
10. **Techman Robot**
– **Main Products:** Collaborative robots (cobots) for packaging, vision systems, integration solutions.
– **Website:** [www.tm-robot.com](http://www.tm-robot.com)
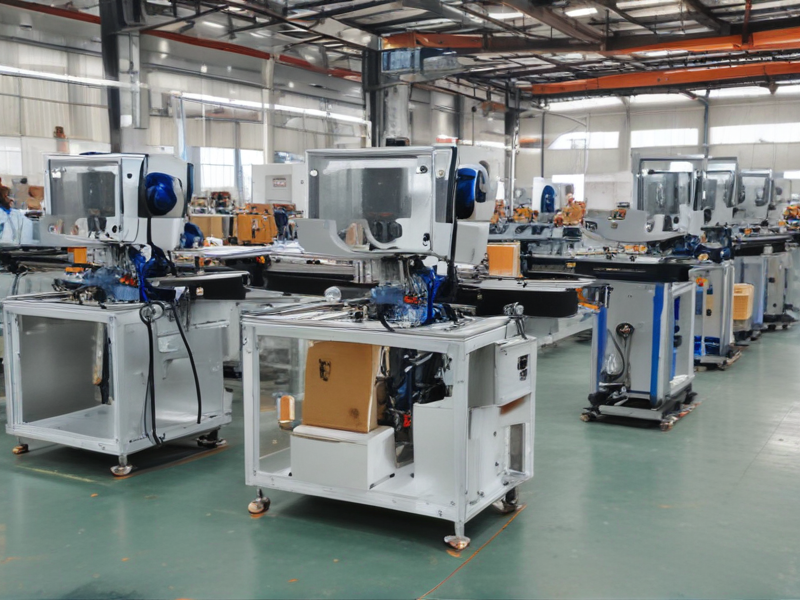
Types of robotic packaging systems
Robotic packaging systems are integral to modern manufacturing and logistics, optimizing efficiency, speed, and accuracy. Here are some common types:
1. **Pick-and-Place Robots**: These robots are designed to pick items from a source location and place them into packaging containers. They are highly versatile and are often used in food, pharmaceutical, and electronics industries.
2. **Case Packers**: These systems automate the process of packing products into cases or cartons. They can be further classified into top-load, side-load, and bottom-load case packers, depending on the method of loading products into the cases.
3. **Carton Erectors**: Carton erectors automatically form flat-packed cartons into open boxes, ready for product placement. This type of robot is essential in streamlining the first step of packaging.
4. **Palletizers and Depalletizers**: Palletizing robots stack products onto pallets for shipment, whereas depalletizing robots unload goods from pallets. These robots are vital in heavy-load operations, enhancing warehouse efficiency.
5. **Wrapping and Sealing Robots**: These machines apply wrapping materials like shrink wrap around products or seal packages for safety and integrity. They are widely used in food, beverage, and consumer goods industries.
6. **Labeling Robots**: Automated labeling systems apply labels to products or packages with precision. They can handle a variety of label types and placements, ensuring consistency and compliance with branding and regulatory standards.
7. **Collaborative Robots (Cobots)**: Cobots work alongside human operators, assisting in various packaging tasks such as assembly, weighing, and quality control. They are designed to be safe and easy to program, making them ideal for complex or changing applications.
8. **Form, Fill, and Seal (FFS) Machines**: These systems perform three tasks in one motion: forming the packaging material into a container, filling it with product, and sealing it for delivery. They are common in industries requiring high throughput.
Employing these robotic systems in packaging processes enhances speed, accuracy, and productivity, meeting the demands of modern high-speed manufacturing and distribution environments.
Pros and Cons of Using robotic packaging systems
**Pros:**
1. **Increased Efficiency:** Robotic packaging systems can significantly speed up packaging processes, reducing time and labor costs.
2. **Consistency and Precision:** Robots provide uniformity in packaging, ensuring that each package meets the same quality standards.
3. **Reduced Labor Costs:** Automation decreases the need for manual labor, reducing payroll expenses and minimizing the risk of human error.
4. **24/7 Operation:** Unlike humans, robots can work continuously without breaks, increasing overall productivity.
5. **Improved Safety:** Robots can handle dangerous or repetitive tasks, reducing the likelihood of workplace injuries.
6. **Adaptability:** Modern robotic systems can be easily reprogrammed for different tasks, making them versatile for various packaging needs.
7. **Inventory Management:** Automated systems can integrate with inventory management software, improving supply chain efficiency.
**Cons:**
1. **High Initial Investment:** The cost of purchasing and installing robotic systems can be significant, posing a barrier for small businesses.
2. **Maintenance Costs:** Regular maintenance and potential repairs of robotic systems can add to operational expenses.
3. **Job Displacement:** Automation can lead to job losses for workers who previously performed these tasks.
4. **Complexity:** Implementing and managing robotic systems requires technical expertise, which may necessitate additional training or hiring specialized personnel.
5. **Downtime Risks:** Mechanical failures or software glitches can cause unexpected downtime, disrupting production schedules.
6. **Limited Flexibility:** While adaptable, robots may still struggle with highly specialized or delicate tasks that require a human touch.
7. **Initial Learning Curve:** Adapting to an automated system may take time, impacting short-term productivity as employees learn to work alongside the technology.
In summary, while robotic packaging systems offer substantial benefits in efficiency, precision, and safety, they also come with significant costs, complexity, and potential impacts on the workforce. Businesses should weigh these factors carefully to determine if automation aligns with their operational goals and capabilities.
robotic packaging systems Reference Specifications (varies for different product)
Robotic packaging systems are automated solutions designed to handle various packaging tasks such as filling, sealing, labeling, and palletizing. These systems enhance productivity, consistency, and efficiency in manufacturing and distribution environments. Reference specifications for robotic packaging systems can vary depending on the product type, packaging material, and other operational requirements. Here are some general aspects:
1. **Payload Capacity**: The weight the robot can handle, typically ranging from a few grams for delicate items to several kilograms for bulk products.
2. **Speed and Throughput**: Measured in cycles per minute (CPM), it defines how fast the system can package items. High-speed systems may exceed 200 CPM for lightweight products.
3. **Precision and Accuracy**: Crucial for tasks like labeling and sealing. Tolerances can be as tight as ±0.1 mm, ensuring the exact placement of labels or seals.
4. **Footprint and Size**: The system’s dimensions, which need to fit within the available floor space in the facility. Compact designs are often preferred to save space.
5. **Flexibility and Modular Design**: Ability to adjust to different product sizes and shapes without extensive reconfiguration. Modular systems allow for easy upgrades and expansions.
6. **End-of-Arm Tooling (EOAT)**: Customizable tools that interact directly with the products, such as grippers, suction cups, or specialized handling tools tailored to the specific items being packaged.
7. **Integration Capability**: Compatibility with existing equipment and software systems, including conveyors, scanners, vision systems, and enterprise resource planning (ERP) systems.
8. **Environmental Conditions**: Suitability for specific conditions such as extreme temperatures, humidity, or cleanliness requirements (e.g., food-grade or pharmaceutical-grade environments).
9. **Control System and Interface**: User-friendly interfaces and robust control systems for easy operation, monitoring, and troubleshooting. Advanced systems may include touchscreens, programmable logic controllers (PLCs), and remote access capabilities.
10. **Safety Features**: Compliance with safety standards, including emergency stop buttons, safety barriers, and sensors to prevent accidents.
The choice of a robotic packaging system should be based on a thorough analysis of the product specifications, production volumes, and operational goals to ensure optimal performance and return on investment.
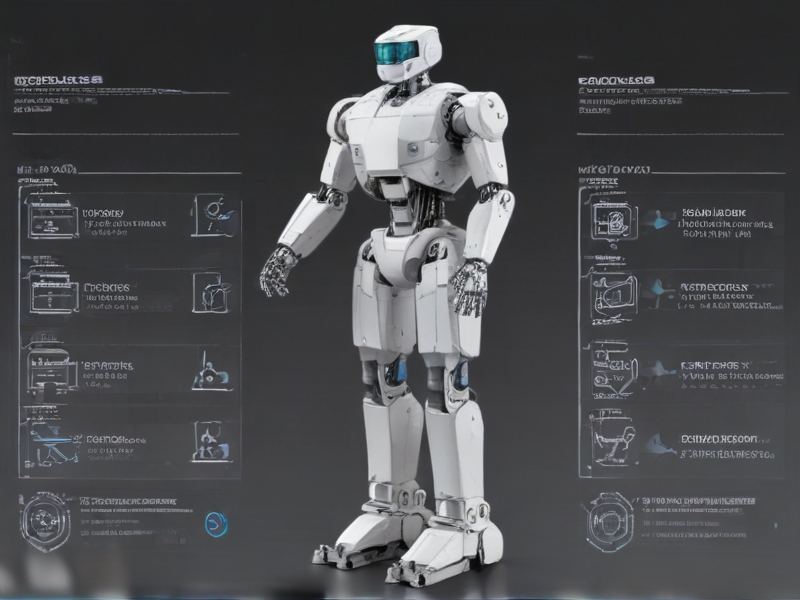
Applications of robotic packaging systems
Robotic packaging systems have revolutionized various industries by enhancing efficiency, accuracy, and flexibility in the packaging process. Here are some key applications across different sectors:
1. **Food and Beverage**: Robotic systems improve hygiene and speed in packaging perishable goods. They handle tasks like sorting, picking, placing, and sealing with precision, reducing contamination risks and enhancing shelf life.
2. **Pharmaceuticals**: In this sector, robots ensure the accurate and sterile packaging of medicines. They handle small, delicate components, perform complex tasks like blister packing, and ensure traceability with labeling and serialization.
3. **E-commerce and Retail**: Robots streamline order fulfillment processes, from picking and packing items to sorting and palletizing packages. This results in faster shipping times and improved accuracy, crucial for customer satisfaction.
4. **Automotive**: Robotic packaging systems manage the packaging of spare parts and components efficiently, ensuring that parts are correctly sorted and securely packed to prevent damage during transportation.
5. **Consumer Electronics**: In this industry, robots handle delicate and expensive items, ensuring they are packaged securely. This includes anti-static packaging for sensitive electronics and precise insertion of components into custom-fit packaging.
6. **Health and Beauty**: For cosmetics and personal care products, robotic systems maintain high standards of hygiene and precision. They can handle diverse packaging styles, from bottles to pouches, ensuring consistency and quality.
7. **Agriculture**: Robots package fresh produce, maintaining speed and precision while reducing food waste. They can adapt to varying shapes and sizes of fruits and vegetables, ensuring optimal packing.
8. **Chemical**: In hazardous environments, robots safely package chemicals, reducing human exposure to dangerous substances. They ensure precise filling and sealing, critical for safety and compliance.
Robotic packaging systems thus provide versatility, scalability, and improved safety, making them invaluable across diverse industries. Their ability to adapt to different packaging needs helps businesses optimize their operations, reduce costs, and maintain high standards of quality and compliance.
Material of robotic packaging systems
Robotic packaging systems integrate various materials to optimize performance, durability, and hygiene standards in industrial packaging settings. The materials commonly used in these systems are:
1. **Stainless Steel**: Predominantly used for its strength, resilience, and resistance to corrosion and staining. In food and pharmaceutical industries, stainless steel is essential due to its hygienic properties, easy cleaning, and conformity to sanitary standards. Grades like 304 and 316 are commonly favored.
2. **Aluminum**: Valued for its lightweight, corrosion resistance, and cost-effectiveness, aluminum is often used in non-load-bearing components and frames. Its ease of machining and forming also makes it suitable for various custom parts.
3. **Carbon Steel**: Known for its strength and rigidity, carbon steel is used in constructing heavy load-bearing parts and structural components. It is often treated or coated to enhance corrosion resistance and durability.
4. **Plastics**: Various engineering plastics are used for parts requiring flexibility, chemical resistance, or electrical insulation. Examples include:
– **Polyethylene (PE)**: Known for its toughness and resistance to impact and moisture.
– **Polypropylene (PP)**: Valued for its chemical resistance and fatigue endurance.
– **Acrylonitrile Butadiene Styrene (ABS)**: Chosen for its strength and rigidity.
– **Polyoxymethylene (POM)**: Used in high-precision parts due to its low friction and dimensional stability.
5. **Composites**: Fiber-reinforced materials like carbon fiber and fiberglass offer a blend of strength, lightweight, and thermal stability, used in specialized components where traditional metals would be too heavy.
6. **Rubbers and Elastomers**: These materials are utilized for flexible seals, grips, and cushions due to their excellent elasticity and damping properties. Common types include silicone, nitrile, and polyurethane.
7. **Specialty Coatings**: Anti-wear, anti-corrosion, and lubricative coatings are applied to various surfaces to prolong the lifespan of components and enhance their performance under harsh conditions.
The selection of materials is crucial in robotic packaging systems to ensure reliability, efficiency, and compliance with industry-specific standards.
Quality Testing Methods for robotic packaging systems and how to control the quality
Effective quality testing methods and quality control for robotic packaging systems ensure reliability, efficiency, and safety. Here are some key approaches:
### Testing Methods:
1. **Functional Testing:** Verifies that the system performs its intended functions, such as picking, placing, and sealing items correctly. This involves running the system under normal operating conditions to check for errors.
2. **Performance Testing:** Assesses the system’s speed, accuracy, and repeatability. Metrics such as cycle time, throughput, and error rates are evaluated to ensure the system meets performance standards.
3. **Durability Testing:** Involves running the robotic system continuously for extended periods to identify potential wear and failure points, ensuring long-term reliability.
4. **Integration Testing:** Ensures seamless interaction between the robotic system and other components of the packaging line. This includes testing communication protocols, synchronization, and data integration.
5. **Environmental Testing:** Assesses the system’s performance under various environmental conditions, such as temperature, humidity, and dust, to ensure robustness and durability.
### Quality Control:
1. **Automated Inspection Systems:** Utilize cameras and sensors to continuously monitor the packaging process, detecting defects or anomalies in real-time. This allows for immediate correction and minimizes waste.
2. **Regular Calibration:** Keep robotic components calibrated according to manufacturer specifications to maintain accuracy and precision.
3. **Predictive Maintenance:** Implement machine learning algorithms to predict potential failures based on historical data, enabling preemptive maintenance actions.
4. **Standard Operating Procedures (SOPs):** Develop and adhere to SOPs for setup, operation, and maintenance. Regular audits ensure compliance and identify areas for improvement.
5. **Training Programs:** Continuously train operators and technicians on the latest best practices, safety protocols, and troubleshooting techniques to maintain high-quality standards.
By combining robust testing methods with proactive quality control measures, robotic packaging systems can achieve optimal performance and reliability.
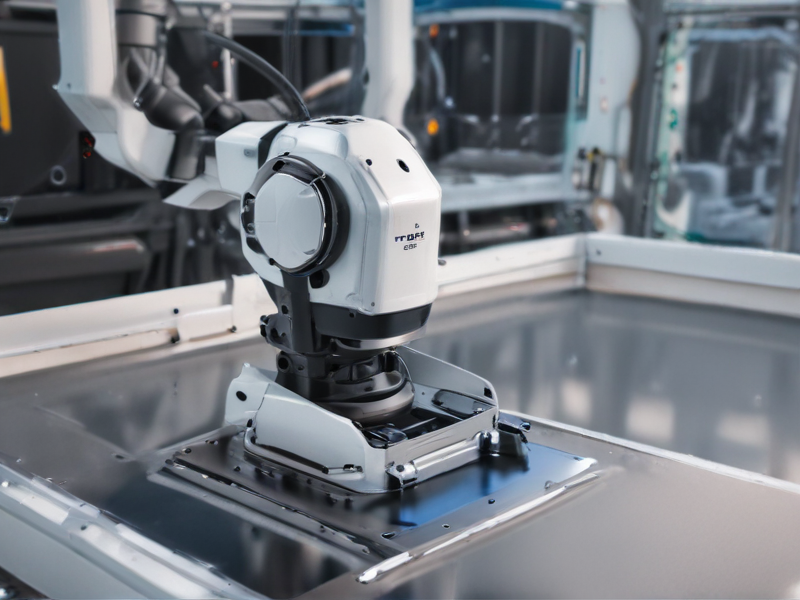
The Work Process and how to use robotic packaging systems
Robotic packaging systems revolutionize packaging processes, enhancing speed, accuracy, and efficiency. Here’s a streamlined work process for effectively utilizing these systems:
### Workflow Steps:
1. **Assessment & Planning**:
– Analyze product dimensions, shapes, and packaging requirements.
– Choose suitable robotic systems (e.g., pick-and-place, palletizing, wrapping robots).
– Design the packaging line layout to streamline operations.
2. **Integration & Setup**:
– Install robotic arms, conveyors, and necessary sensors.
– Integrate robots with existing systems via software and control units.
– Program robots with task specifications and workflows (can include machine learning algorithms for adaptive performance).
3. **Feeding & Detection**:
– Supply products through conveyors or feeders.
– Use vision systems or sensors for defect detection and orientation.
4. **Pick and Place**:
– Robotic arms equipped with grippers or vacuum systems pick products.
– Place products into packaging using pre-programmed patterns to maximize efficiency.
5. **Packaging Application**:
– Robots insert products into boxes, bags, or other packaging formats.
– Apply labels, seals, and barcodes automatically.
6. **Quality Control & Adjustment**:
– Conduct continuous monitoring using cameras and sensors.
– Make real-time adjustments to address any inconsistencies or defects.
7. **Palletizing & Wrapping**:
– Arrange packaged goods onto pallets.
– Utilize robotic stretch wrappers to securely wrap pallets for shipping.
### Key Benefits:
– **Increased Efficiency**: Operate 24/7 without fatigue.
– **Consistency**: Maintain high-quality standards consistently.
– **Flexibility**: Adapt quickly to different packaging needs.
– **Safety**: Minimize human error and reduce workplace injuries.
### Best Practices:
– Regular maintenance to prevent downtime.
– Training staff on robotic system operations and troubleshooting.
– Implementing data analytics for performance optimization.
Adopting robotic packaging systems transforms efficiency and reliability, optimizing the overall production workflow.
robotic packaging systems Importing questions including Cost,Supplier,Sample,Certification and Market
When considering the importation of robotic packaging systems, several key questions must be addressed to make an informed decision:
1. **Cost**:
– What is the total cost, including purchase price, shipping, import duties, and taxes?
– Are there volume discounts or financing options available?
– What are the long-term costs related to maintenance, software updates, and spare parts?
2. **Supplier**:
– Who are the reputable suppliers or manufacturers?
– What is the supplier’s track record in terms of quality and reliability?
– Can the supplier provide after-sales support and service locally?
– Are there any reputable third-party reviews or case studies available?
3. **Sample**:
– Can the supplier provide a sample unit for testing before committing to a full purchase?
– What is the cost of obtaining a sample, and are there any return policies?
– Is there an option for a pilot program to assess the system’s performance in a real-world environment?
4. **Certification**:
– What certifications and standards does the robotic packaging system adhere to (e.g., CE, UL, ISO)?
– Are there specific certifications required for use in your country or industry?
– Can the supplier provide all necessary documentation to support these certifications?
5. **Market**:
– What is the current market demand and competition for robotic packaging systems in your target region?
– Are there trends indicating an increase in automation and demand for such systems?
– How does the system fit into the existing market landscape, and what is its value proposition compared to competitors?
Addressing these questions comprehensively will help you make a well-informed decision, ensuring that the robotic packaging system you import is cost-effective, reliable, and compliant with all necessary standards.
How to find and select check reliable robotic packaging systems manufacturers in China
Finding and selecting reliable robotic packaging systems manufacturers in China involves several strategic steps:
1. **Research and Shortlisting**:
– **Directories**: Utilize online directories like Alibaba, Made-in-China, and Global Sources to identify potential manufacturers.
– **Industry Forums**: Join industry-specific forums and social media groups to gather recommendations.
2. **Evaluate Credibility**:
– **Certifications**: Check for industry-specific certifications, such as ISO 9001, CE, and other relevant quality management standards.
– **Experience**: Look for manufacturers with extensive experience in the robotic packaging sector.
– **Reputation**: Read reviews and testimonials from previous clients.
3. **Company Background Check**:
– **Company Website**: Thoroughly examine the manufacturer’s website for detailed information about their products, services, and company history.
– **Third-Party Audits**: Utilize third-party auditing services to verify the company’s legitimacy and operational standards.
4. **Technical Capability**:
– **Product Range**: Evaluate the range of products and technologies offered to ensure they meet your specific requirements.
– **Innovation**: Check for R&D capabilities indicating the company’s ability to innovate and adapt to new technologies.
5. **Quality Assurance**:
– **Inspection Reports**: Request detailed quality inspection reports of products.
– **Factory Visits**: If possible, visit the factory to assess the production processes and quality control measures firsthand.
6. **Customer Support and After-sales Service**:
– **Support Infrastructure**: Ensure robust customer support and after-sales service, including training, maintenance, and spare parts availability.
– **Contracts and Agreements**: Negotiate clear terms for warranties and service agreements.
7. **Samples and Prototyping**:
– **Trial Orders**: Place small trial orders to test the quality and reliability of their robotic packaging systems before committing to larger orders.
By following these steps, you can identify and select reliable robotic packaging systems manufacturers in China.
Background Research for robotic packaging systems manufacturers Companies in China, use qcc.com archive.org importyeti.com
Conducting background research on Chinese manufacturers of robotic packaging systems can be efficiently done through various specialized tools and platforms. Below is a summary incorporating findings from qcc.com, archive.org, and importyeti.com.
**qcc.com**:
Qcc.com is a comprehensive database that offers detailed information about Chinese enterprises. Researching on this platform, key players in the robotic packaging systems market include:
1. **Siasun Robot & Automation Co., Ltd.**: One of the leading robotic automation firms in China, specializing in a wide range of applications including packaging.
2. **GSK CNC Equipment Co., Ltd.**: Known for its expertise in industrial robots, this company has ventured into packaging solutions leveraging advanced robotics.
3. **Efort Intelligent Equipment Co., Ltd.**: Focuses on intelligent manufacturing and offers solutions for automated packaging.
These companies exhibit strong capabilities in manufacturing and innovation, supported by extensive R&D and sales networks.
**archive.org**:
By using the Wayback Machine on archive.org, historical data and web pages of the companies can be accessed to understand their evolution, product offerings, and market positioning over time. For instance, archived pages of Siasun and GSK CNC reveal their progressive advancements in robotics technology and their growing portfolio in the packaging sector.
**importyeti.com**:
ImportYeti provides insights into trade activities by identifying suppliers and shipment data. Relevant data about robotic packaging systems can be attained by analyzing:
– **Siasun’s international shipments**, indicating robust export activity and partnerships.
– **GSK CNC’s import records**, reflecting their supply chain and procurement practices for components and raw materials, aiding in packaging equipment manufacture.
The combination of insights from these resources paints a comprehensive picture of Chinese manufacturers in the robotic packaging systems market. This holistic view underscores their technological prowess, market strategies, and international trade dynamics, showcasing their significant role in global supply chains.
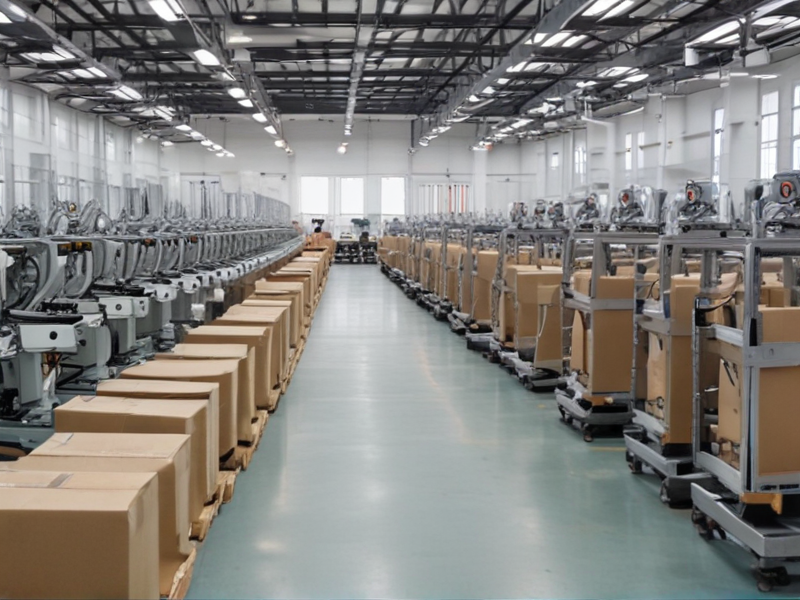
Price Cost Research for robotic packaging systems manufacturers Companies in China, use temu.com and 1688.com
Conducting price cost research for robotic packaging systems manufacturers in China involves leveraging both Temu.com and 1688.com, two leading e-commerce platforms widely used for sourcing industrial components and machinery. Here’s a concise analysis within a 300-word limit.
### Temu.com Analysis
Temu.com features a range of suppliers offering robotic packaging systems. On Temu, prices for robotic packaging systems vary widely depending on the complexity, functionality, and brand prestige.
– **Entry-Level Systems**: Basic robotic arms equipped for simple packaging tasks are listed starting around $8,000 to $10,000.
– **Mid-Range Systems**: More sophisticated systems that offer features like automated sorting, advanced robotics integration, and user-friendly software interfaces range between $15,000 to $30,000.
– **High-End Systems**: Fully integrated solutions designed for high-speed, high-volume operations, often with custom configurations, can start from $50,000 and go upwards depending on the customization and scalability options.
### 1688.com Analysis
1688.com, a platform operated by Alibaba Group, offers extensive listings from a variety of manufacturers specializing in robotic packaging systems.
– **Entry-Level Systems**: Similar to Temu, basic automated systems suitable for small-scale operations are priced from RMB 50,000 to RMB 70,000 (approximately $7,000 to $10,000).
– **Mid-Range Systems**: These systems, incorporating additional features like vision systems and enhanced robotics, range between RMB 100,000 to RMB 200,000 ($14,000 to $28,000).
– **High-End Systems**: Premium models tailored for extensive automated operations and designed for large manufacturing lines can cost upwards of RMB 300,000 ($42,000) and scale higher based on specific industrial requirements.
### Conclusion
Both Temu.com and 1688.com offer competitive options for sourcing robotic packaging systems in China. Entry-level systems are comparably priced around $7,000 to $10,000. Mid-range options float between $14,000 to $30,000, while high-end, fully integrated systems escalate beyond $50,000. For detailed specifications and tailored quotations, direct inquiries with manufacturers via these platforms are advisable.
Shipping Cost for robotic packaging systems import from China
Shipping costs for importing robotic packaging systems from China can vary widely based on several factors, including the size and weight of the equipment, shipping method, distance, and additional services. Below is a concise breakdown of potential costs and considerations:
1. **Shipping Methods:**
– **Air Freight:** Faster but more expensive. Costs range from $5 to $10 per kilogram.
– **Sea Freight:** More economical, especially for large and heavy shipments. Costs range from $1,000 to $4,000 per 20-foot container, depending on the route.
– **Express Shipping:** For urgent needs, companies like DHL, FedEx, or UPS can be used but can be very costly, potentially $20 to $30 per kilogram.
2. **Destination-Specific Costs:**
– **Port Fees and Duties:** Upon arrival, destination ports may charge handling, customs, and import duties, adding 5% to 10% to overall costs.
– **Inland Transportation:** Costs for transporting from the port to your final destination; typically $100 to $500 depending on distance.
3. **Insurance:**
– Essential to cover potential damages or losses. Cost is generally 1% to 2% of the equipment’s value.
4. **Packaging:**
– Secure packaging is crucial for robotic systems; ensure the seller uses robust materials that can add around $100 to $500.
5. **Freight Forwarders:**
– A professional can manage logistics, potentially charging 5% to 10% of the total shipping cost.
6. **Potential Additional Costs:**
– Expedited handling, warehousing, or special handling can increase expenses.
In summary, while sea freight for large shipments is the most cost-effective, weighing between $1,000 to $4,000 per container, air freight could range from $5 to $10 per kilogram for faster delivery. Always confirm with freight forwarders for precise, up-to-date quotes.
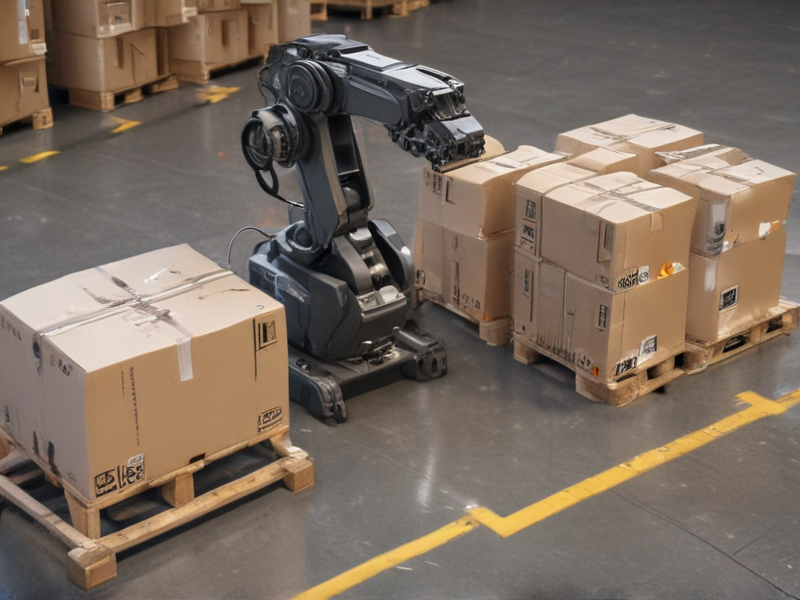
Compare China and Other robotic packaging systems Markets: Products Quality and Price,Visible and Hidden Costs
China has emerged as a significant player in the global robotic packaging market, offering a competitive mix of quality and price. However, there are notable differences when compared to other markets, such as Europe, Japan, and the USA.
**Product Quality and Price:**
Chinese robotic packaging systems typically offer lower prices, attributed to reduced labor costs and economies of scale. In terms of quality, China has made substantial improvements, with top-tier manufacturers producing robotics that can compete with Western counterparts. Nevertheless, concerns about consistency and durability can still arise, particularly with lower-tier Chinese manufacturers. Conversely, robotic packaging systems from Europe, Japan, and the USA are often perceived as more reliable and advanced, albeit at higher price points, reflecting superior technology, stringent manufacturing standards, and rigorous quality control.
**Visible and Hidden Costs:**
Visible costs, such as initial purchase prices, are usually lower for Chinese systems. However, hidden costs need careful consideration. These can include longer lead times, higher shipping fees, and additional import taxes. Chinese systems may also incur higher long-term maintenance and operational costs due to potential reliability issues and the need for more frequent repairs. Parts availability and after-sales service can further impact total cost of ownership.
In contrast, Western brands generally offer better after-sales service, easier access to replacement parts, and support that can reduce downtime. While the upfront cost is higher, the reliability and lower maintenance demands might balance overall expenditure over the system’s life.
In summary, while Chinese robotic packaging systems provide cost-effective solutions with improving quality, they come with potential hidden costs that require thorough evaluation. Systems from Europe, Japan, and the USA offer higher reliability and support at a premium price, potentially offering better value for long-term investments.
Custom Private Labeling and Branding Opportunities with Chinese robotic packaging systems Manufacturers
Partnering with Chinese robotic packaging systems manufacturers for custom private labeling and branding presents a remarkable opportunity for companies looking to scale and differentiate their product offerings. These partnerships enable businesses to leverage advanced Chinese technology, often characterized by innovations, competitive pricing, and robust manufacturing capabilities.
China boasts a plethora of manufacturers skilled in producing high-quality robotic packaging systems tailored for various industries, including food, pharmaceuticals, and consumer goods. By collaborating with these manufacturers, companies can access state-of-the-art equipment designed for efficiency, precision, and versatility. Most Chinese manufacturers are open to customization requests, allowing integration of specific branding elements such as logos, color schemes, and unique design features into the packaging machines.
One key advantage of custom private labeling is the ability to create a distinctive market presence. Branded robotic packaging systems not only enhance brand visibility but also build credibility and trust with clients. Additionally, manufacturers often offer extensive after-sales support and training, which can be customized under the company’s branding, further reinforcing customer loyalty and satisfaction.
Moreover, the cost-effectiveness of manufacturing in China cannot be overstated. Chinese manufacturers benefit from economies of scale and lower production costs, enabling businesses to obtain high-tech equipment without exorbitant investments. This financial flexibility allows companies to invest in other areas of growth, such as marketing and R&D.
Strategic partnerships with Chinese manufacturers can also facilitate faster production cycles and quicker time-to-market, vital in industries with high velocity and competition. Moreover, the ability to respond swiftly to market demands with rebranded and customized solutions ensures companies stay ahead of trends.
In conclusion, leveraging custom private labeling and branding opportunities with Chinese robotic packaging systems manufacturers can significantly enhance market positioning, operational efficiency, and overall business growth. This strategic alignment offers a pathway to innovative, cost-effective, and brand-specific packaging solutions.
Tips for Procurement and Considerations when Purchasing robotic packaging systems
When purchasing robotic packaging systems, it’s essential to thoroughly evaluate your requirements and the capabilities of the equipment. Here are some key tips and considerations to guide the procurement process:
1. **Assessment of Needs:** Understand your specific packaging requirements such as product types, packaging materials, throughput rates, and space constraints.
2. **Technology Compatibility:** Ensure the robotic system can integrate seamlessly with your existing machinery and software. Compatibility with Industry 4.0 technologies can enhance efficiency.
3. **Scalability:** Choose a system that can grow with your business. Modular designs allow for future upgrades and expansions without significant additional investment.
4. **Reliability and Maintenance:** Look for proven reliability and low maintenance needs. Investigate the availability of local service support and spare parts to minimize downtime.
5. **Total Cost of Ownership (TCO):** Consider the initial purchase price, but also factor in installation, training, maintenance, and operational costs over the lifespan of the system.
6. **Flexibility:** Opt for systems that can handle multiple product types and packaging formats to accommodate varying demands and production runs.
7. **Ease of Use:** Prioritize systems with intuitive user interfaces and straightforward programming to reduce the learning curve and training time for operators.
8. **Safety:** Ensure the robotic packaging system complies with industry safety standards and includes features such as safety enclosures and emergency stop mechanisms.
9. **Energy Efficiency:** Consider the energy consumption of the robotic system to keep operational costs in check and support sustainability goals.
10. **Vendor Reputation:** Research potential suppliers, check references, and read reviews. A reputable supplier with a solid track record in delivering quality robotic systems is crucial.
By addressing these considerations, you can make a well-informed decision that enhances your packaging operations and aligns with your long-term business objectives.
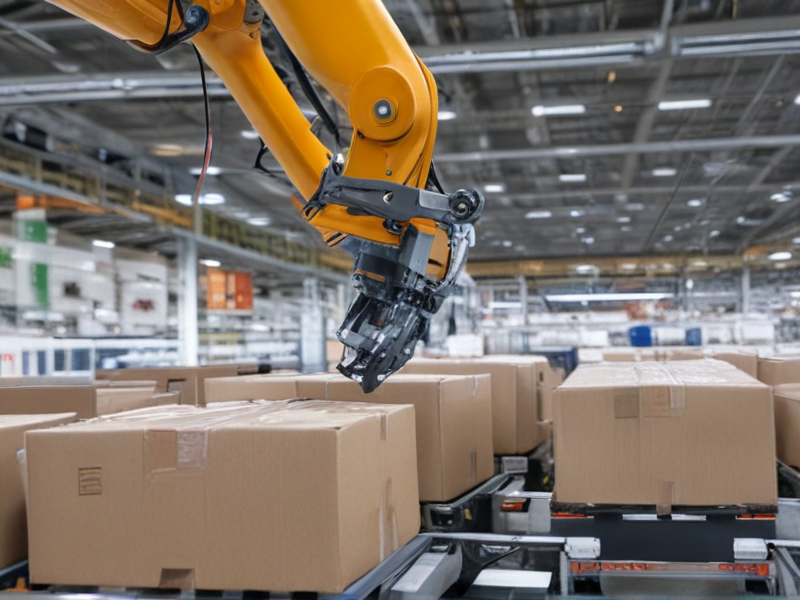
FAQs on Sourcing and Manufacturing robotic packaging systems in China
### FAQs on Sourcing and Manufacturing Robotic Packaging Systems in China
#### 1. **Why source robotic packaging systems from China?**
China is a global leader in manufacturing, offering advanced technology, skilled labor, and competitive pricing, making it a prime destination for sourcing robotic packaging systems.
#### 2. **What should I look for in a supplier?**
Look for ISO certifications, a proven track record, good customer feedback, and the ability to provide after-sales service and support. Visiting the factory to verify capabilities is also advisable.
#### 3. **How do I ensure product quality?**
Engage third-party inspection services, conduct factory audits, and request samples or trial runs. It’s crucial to establish clear quality parameters upfront.
#### 4. **What are the key legal considerations?**
Familiarize yourself with Chinese business laws, intellectual property rights (IPR), and the details of your contractual agreement, including payment terms, delivery schedules, and warranty policies.
#### 5. **How long does the manufacturing process take?**
Lead times vary based on complexity and customization but typically range from 8-16 weeks. It’s vital to confirm timelines upfront to align with your project schedule.
#### 6. **Can I customize my order?**
Yes, most suppliers offer customization according to your specific requirements. Ensure your specifications are clear and detailed in the contract.
#### 7. **What about shipping and logistics?**
Choose between air and sea freight depending on urgency and budget. Partnering with a reliable freight forwarder can simplify customs clearance and logistics.
#### 8. **What are the payment terms?**
Common terms include T/T (Telegraphic Transfer), L/C (Letter of Credit), and occasionally escrow services for added security. Ensure the payment structure aligns with production milestones.
#### 9. **How do I handle post-purchase support?**
Establish after-sales service agreements, including maintenance, spare parts availability, and technical support. Verify the supplier’s warranty policies and service capabilities.
#### 10. **What challenges should I anticipate?**
Be prepared for potential language barriers, cultural differences, and fluctuations in lead times. Effective communication and a reliable local intermediary can mitigate these risks.