Top 10 packaging automation in China introduce,list main products and website if have
Sure! Here’s a concise overview of the top 10 packaging automation companies in China:
1. **Sino-Pack (China Packaging Machinery Co., Ltd.)**
– **Main Products:** Filling machines, sealing machines, labeling machines
– **Website:** [sino-pack.com](http://www.sino-pack.com)
2. **Lepok Automation**
– **Main Products:** High-speed filling and capping machines, labeling systems, automatic cartoners
– **Website:** [lepok.com.cn](http://www.lepok.com.cn)
3. **Triowin**
– **Main Products:** Bottling lines, labeling machines, packaging robots, palletizers
– **Website:** [triowin.com](https://www.triowin.com)
4. **Jimei**
– **Main Products:** Beverage production lines, dairy processing equipment, filling machines
– **Website:** [jimeimachinery.com](http://www.jimeimachinery.com)
5. **HengYuan Machinery Equipment Co., Ltd.**
– **Main Products:** Filling machines, capping machines, labeling machines, and packaging lines
– **Website:** [filling-packing-machine.com](http://www.filling-packing-machine.com)
6. **Newamstar**
– **Main Products:** Beverage filling machines, packaging systems, PET bottle producing lines
– **Website:** [newamstar.com](http://www.newamstar.com)
7. **Sunpack**
– **Main Products:** Carton sealing machines, shrink packaging machines, pallet wrap machines
– **Website:** [sunpack.com.cn](http://www.sunpack.com.cn)
8. **KYNHOR Packaging Machinery**
– **Main Products:** Bottling machines, pouch packaging machines, and labeling equipment
– **Website:** [kynhor.com](http://www.kynhor.com)
9. **Ruian Onfocus Machinery**
– **Main Products:** Automatic cartoning machines, blister packaging machines, and pillow packaging machines
– **Website:** [onfocusmachinery.com](http://www.onfocusmachinery.com)
10. **Zhangjiagang King Machine Co., Ltd.**
– **Main Products:** Water treatment machines, beverage filling machines, labeling, and packing machines
– **Website:** [king-machine.com](http://www.king-machine.com)
These companies represent a diverse range of packaging automation solutions, from beverage processing to comprehensive production lines, reflecting China’s robust capabilities in industrial automation.

Types of packaging automation
Packaging automation encompasses various technologies designed to streamline the packaging process, improve efficiency, and reduce human error. Here are some common types of packaging automation:
1. **Form, Fill, and Seal Machines (FFS):**
– **Vertical Form-Fill-Seal (VFFS):** Ideal for loose, granular products like snacks and grains.
– **Horizontal Form-Fill-Seal (HFFS):** Suited for items like frozen foods, cosmetics, and pharmaceuticals.
2. **Case Erectors and Sealers:**
– **Case Erectors:** Automatically assemble flat-packed boxes.
– **Case Sealers:** Apply tape or glue to seal filled boxes, used in warehousing and distribution.
3. **Palletizing Systems:**
– **Robotic Palletizers:** Use robots to stack products efficiently on pallets, reducing labor costs.
– **Conventional Palletizers:** Employ traditional mechanical systems for stacking.
4. **Conveyors and Sorting Systems:**
– **Belt Conveyors:** Move items along a production line.
– **Automated Sorting Systems:** Categorize products based on predefined criteria, crucial for logistics and distribution.
5. **Labeling and Printing Machines:**
– Automates the application of labels and printing of barcodes, essential for product tracking and compliance.
6. **Wrapping and Shrink Wrapping Machines:**
– **Stretch Wrappers:** Apply stretch film to palletized loads for stability during transport.
– **Shrink Wrappers:** Encase products in shrink film, which is then heated to form a tight seal.
7. **Automated Guided Vehicles (AGVs):**
– Transport materials around a facility, replacing manual labor and improving productivity.
8. **Inspection Systems:**
– **Visual Inspection:** Uses cameras and sensors to check packaging quality.
– **X-ray and Metal Detection:** Ensures product safety and regulatory compliance.
These systems, ranging from simple machines to complex integrations, cater to various industries and product types, significantly boosting operational efficiency and consistency.
Pros and Cons of Using packaging automation
**Pros of Using Packaging Automation:**
1. **Increased Efficiency:** Automation significantly reduces packaging time and minimizes human error, leading to faster and more consistent production cycles.
2. **Cost Savings:** While the initial investment is substantial, automated systems reduce labor costs and waste, leading to long-term savings.
3. **Quality Control:** Automated packaging ensures uniformity and precision, improving product quality and customer satisfaction.
4. **Scalability:** Companies can easily scale up operations to meet high demand without proportional increases in labor costs or working hours.
5. **Safety:** Automation reduces the risk of workplace injuries associated with repetitive or strenuous packaging tasks, enhancing worker safety.
**Cons of Using Packaging Automation:**
1. **High Initial Investment:** Purchasing and setting up automated packaging systems require a significant upfront financial commitment, which can be a barrier for small businesses.
2. **Maintenance and Downtime:** Automated machinery requires regular maintenance and can be susceptible to breakdowns, leading to potential downtime and repair costs.
3. **Skill Requirements:** Operating and maintaining automated systems demand specialized skills, potentially necessitating additional training or hiring.
4. **Job Displacement:** Automation can lead to reduced need for manual labor, potentially resulting in job losses and affecting employee morale.
5. **Flexibility Limitations:** Automated systems can be less flexible compared to human workers when dealing with custom or small-batch packaging needs, requiring adjustments or additional programming.
In summary, while packaging automation offers substantial benefits in terms of efficiency, cost savings, and quality control, businesses must weigh these advantages against the high initial costs, maintenance requirements, and potential impacts on labor flexibility and employment.
packaging automation Reference Specifications (varies for different product)
Packaging automation is essential for enhancing efficiency, consistency, and reliability in the packaging industry. Reference specifications for various products in packaging automation vary depending on the product requirements and industry standards. Here are some key elements commonly considered:
1. **Product Characteristics:**
– **Type (solid, liquid, semi-solid)**
– **Size and Shape**
– **Weight and Volume**
– **Fragility and Sensitivity**
2. **Packaging Material:**
– **Type (plastic, glass, metal, paper)**
– **Thickness and Durability**
– **Compatibility with Content**
3. **Machine Specifications:**
– **Speed (units per minute/hour)**
– **Accuracy and Precision**
– **Multi-functionality (filling, sealing, labeling)**
– **Ease of Changeover**
4. **Environment:**
– **Ambient Temperatures**
– **Humidity Levels**
– **Cleanroom Compliance (for pharmaceuticals/food)**
5. **Safety and Compliance:**
– **Regulatory Compliance (FDA, ISO, etc.)**
– **Machine Safety Features (guards, emergency stops)**
– **Error Detection Systems**
6. **Integration and Scalability:**
– **Compatibility with Existing Systems**
– **Modular Design for Scalability**
– **IoT and Smart Integration**
7. **Quality Control:**
– **Inspection Systems (vision, weight checks)**
– **Reject Mechanisms**
– **Traceability**
### Example Application:
**Food Industry:**
1. **Characteristics**:
– **Type**: Solid (snack packs)
– **Shape**: Irregular
– **Weight**: 50 – 200 grams
2. **Material**:
– **Type**: Food-grade plastic film
– **Durability**: Puncture-resistant, moisture barrier
3. **Machine**:
– **Speed**: 80 packs/minute
– **Functions**: Filling, vacuum sealing, date coding
4. **Environment**:
– **Temperature Range**: 10-25°C
– **Cleanliness**: Food industry hygiene standards
5. **Safety**:
– **Compliance**: HACCP, FDA
– **Safety systems**: Light curtains, interlocks
6. **Integration**:
– **IoT**: Real-time monitoring, predictive maintenance
– **Modularity**: Upgradeable filling capacity
7. **Quality**:
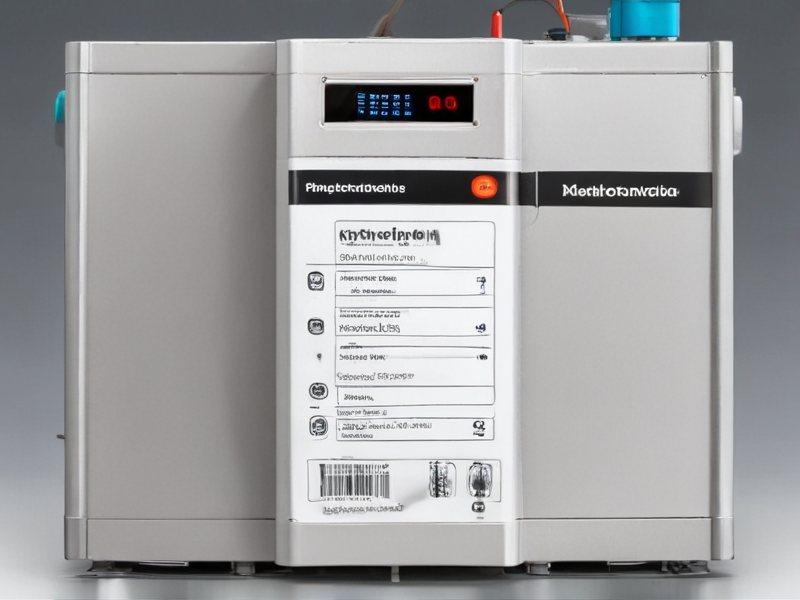
Applications of packaging automation
Packaging automation is revolutionizing various industries by enhancing efficiency, reducing costs, and improving product quality. Key applications include:
1. **Food and Beverage**: Automated systems ensure consistent portioning, sealing, and labeling, enhancing hygiene and reducing waste. For example, robotic arms can handle delicate bakery items without damaging them, and sensors can check for proper sealing to prevent contamination.
2. **Pharmaceuticals**: Precision is crucial in drug packaging. Automation provides accurate dosing, tamper-evidence features, and detailed labeling to comply with regulatory requirements. Automated serialization systems help track products, mitigating the risk of counterfeiting.
3. **Consumer Goods**: From cosmetics to electronics, automated packaging lines streamline the packing process, ensuring products are wrapped attractively and securely. Automated systems can quickly adapt to different package sizes and styles, facilitating rapid product changeovers.
4. **E-commerce and Retail**: Automation in warehousing ensures fast, accurate order fulfillment. Machines can pick, sort, and pack items efficiently, reducing labor costs and human error. Automated packaging systems can dynamically create custom-sized boxes, reducing shipping volume and materials.
5. **Automotive**: Automated packaging of components ensures precise handling and protection of high-value parts. Systems can manage heavy or awkward items, reducing injury risk and ensuring products arrive ready for assembly.
6. **Agriculture**: Automated systems can package produce rapidly while sorting by size and ripeness. This increases throughput and meets varying market requirements. Advanced systems also handle pre-packaged salads, ensuring freshness and hygiene.
7. **Medical Devices**: Automation ensures sterile packaging of medical devices, maintaining compliance with stringent health standards. Precise handling and packing reduce contamination risks and enhance reliability.
By integrating robotics, advanced sensors, and AI, packaging automation enhances speed, accuracy, and flexibility across these diverse sectors, ultimately contributing to supply chain optimization and customer satisfaction.
Material of packaging automation
Packaging automation leverages advanced machinery and control systems to streamline the process of packaging products. Selecting the right materials is critical for optimizing functionality, sustainability, and cost-effectiveness. Below are some commonly used materials and their characteristics:
1. **Plastics**: Versatile and widely used, plastics such as polyethylene (PE), polypropylene (PP), and polyvinyl chloride (PVC) are popular in packaging due to their durability, flexibility, and lightweight properties. They can be molded into various shapes and provide excellent barrier protection against moisture and contaminants. However, environmental concerns are prompting shifts toward recyclable and biodegradable options.
2. **Metals**: Aluminum and steel are frequently used in packaging automation for their strength and resistance to corrosion. Aluminum is lightweight and often used for beverage cans and foil packaging. Steel’s robustness makes it ideal for industrial packaging and containers. Both materials are recyclable, adding a sustainability edge.
3. **Paper and Cardboard**: These materials are eco-friendly and widely recyclable. They are commonly used for boxes, cartons, and wrapping. Advances in coatings and treatments can enhance their durability and moisture resistance. Sustainable sourcing from managed forests and the use of recycled fibers are increasingly popular.
4. **Glass**: Offering excellent barrier properties, glass is used in packaging beverages, pharmaceuticals, and food products. It is inert, ensuring no chemical reactions with the contents. Glass is recyclable but heavier and more fragile compared to other materials.
5. **Biodegradable Materials**: Growing environmental awareness is driving the use of biodegradable materials like polylactic acid (PLA) derived from renewable resources like corn starch. These materials decompose naturally and reduce waste.
Automation enhances the efficiency, accuracy, and speed of packaging, ensuring consistent quality and reducing labor costs. Integration with IoT and AI technologies offers real-time monitoring and analytics, further optimizing operations. In conclusion, selecting suitable materials is essential for balancing performance, sustainability, and cost in packaging automation.
Quality Testing Methods for packaging automation and how to control the quality
Quality testing methods for packaging automation are crucial to ensure the reliability, safety, and efficiency of packaging processes. Here’s an overview of key quality testing methods and control strategies:
### Key Quality Testing Methods
1. **Visual Inspection Systems:**
– **Automated Vision Systems:** Use high-resolution cameras and software to detect defects such as incorrect labels, misaligned packages, and damaged products.
– **Machine Learning Algorithms:** Train systems to recognize patterns and deviations to improve accuracy over time.
2. **Functional Testing:**
– **Seal Integrity Testing:** Measures the strength and leak resistance of package seals using techniques like vacuum decay and bubble emission.
– **Drop and Vibration Tests:** Assess the durability of packaging during transit by simulating conditions like drops, shocks, and vibrations.
3. **Material Testing:**
– **Tensile and Compression Tests:** Evaluate the strength and flexibility of packaging materials to ensure they meet specified thresholds.
– **Barrier Property Tests:** Check for permeability to gases and moisture, especially important for food and pharmaceuticals.
4. **Automation Performance Testing:**
– **Speed and Throughput Tests:** Ensure the automated system meets the required packaging speed without compromising quality.
– **Error Rate Analysis:** Measure the incidence of errors and identify trends to optimize the system.
### Quality Control Strategies
1. **Statistical Process Control (SPC):**
– Utilizes statistical methods to monitor and control the packaging process, identifying and addressing variations before they lead to defects.
2. **Closed-Loop Systems:**
– Implement feedback mechanisms that use real-time data to adjust settings and parameters automatically, maintaining consistent quality.
3. **Preventative Maintenance:**
– Regular inspections and servicing of automation equipment to minimize downtime and prevent unexpected failures.
4. **Training and Calibration:**
– Continuous training for staff handling automated systems and regular calibration of machinery to adhere to standards and regulations.
5. **Standard Operating Procedures (SOPs):**
– Documented protocols for every stage of the packaging process, ensuring consistency and compliance with industry standards.
By employing these methods and strategies, organizations can ensure high-quality outcomes in their packaging automation processes.

The Work Process and how to use packaging automation
Packaging automation streamlines the packaging process, enhancing efficiency, consistency, and scalability. Here’s a concise guide on how it works and how to deploy it effectively.
### Work Process:
1. **Assessment**: Begin by evaluating current packaging processes to identify pain points and areas for improvement.
2. **Planning**: Develop a strategy outlining the types of automation equipment needed, such as automated case erectors, robotic cartoners, or palletizers.
3. **Equipment Selection**: Choose machinery that fits your product type, volume, and packaging requirements. Common options include:
– **Filling machines**: For liquids, powders, or granular materials.
– **Sealing machines**: For bagging or lidding.
– **Wrapping machines**: For stretch-wrapping pallets.
– **Labeling machines**: For precise and consistent label application.
4. **Integration**: Implement the machinery into your production line, ensuring minimal disruption. Integrate software systems for tracking and monitoring.
5. **Training**: Educate staff on new equipment operations and safety protocols.
6. **Testing**: Conduct rigorous testing to ensure operational effectiveness and address any issues before full-scale deployment.
7. **Optimization**: Continuously monitor and refine the system. Use data analytics for predictive maintenance and efficiency improvements.
### Benefits:
– **Efficiency**: Reduces manual labor, speeds up production.
– **Consistency**: Ensures uniform quality and packaging standards.
– **Scalability**: Easily adjusts to increased production demands.
– **Cost Savings**: Minimizes waste and lowers labor costs over time.
### Implementation Steps:
1. **Define Objectives**: Set clear goals for what you aim to achieve with automation, such as reducing labor costs or increasing throughput.
2. **Budgeting**: Allocate funds considering initial investment and long-term savings.
3. **Select Supplier**: Partner with reputable automation suppliers.
4. **Pilot Run**: Start small before scaling up to mitigate risks.
5. **Full Rollout**: Once optimized, deploy across all applicable production lines.
By following these steps, companies can efficiently incorporate packaging automation into their operations, resulting in significant improvements in productivity and cost-efficiency.
packaging automation Importing questions including Cost,Supplier,Sample,Certification and Market
When automating your packaging process, importing relevant information is key. Here are key areas to focus on:
1. **Cost**:
– **Initial Investment**: Understand the upfront costs for machinery, software, installation, and initial setup.
– **Operational Expenses**: Consider ongoing costs such as maintenance, workforce training, and energy consumption.
– **ROI**: Calculate the expected return on investment. Automation typically offers savings through reduced labor costs and increased efficiency.
2. **Supplier**:
– **Credibility**: Research the supplier’s reputation, customer reviews, and industry standing.
– **Support**: Ensure the supplier offers robust after-sales support, including maintenance, troubleshooting, and spare parts availability.
– **Customization**: Check if the supplier can customize machinery to fit your specific packaging needs.
3. **Sample**:
– **Test Runs**: Request sample products or trial runs to evaluate the machinery’s performance and the quality of packaging it provides.
– **Validation**: Conduct thorough testing to ensure the machinery meets your operational requirements and packaging standards.
4. **Certification**:
– **Compliance**: Ensure the machinery complies with industry standards and local regulations (e.g., CE marking in Europe, UL certification in the USA).
– **Documentation**: Obtain relevant certifications or compliance documents to avoid legal complications and ensure quality assurance.
– **Safety**: Verify that the automated systems meet safety standards to protect operators and avoid workplace injuries.
5. **Market**:
– **Demand Analysis**: Assess market demand to determine if the increased production capacity is justified.
– **Competitor Benchmarking**: Analyze competitors’ use of automation to stay competitive.
– **Scalability**: Choose automation solutions that can scale with market growth and product diversification.
By focusing on these aspects, you can make informed decisions when implementing packaging automation in your operations, ensuring efficiency, cost-effectiveness, and regulatory compliance.
How to find and select check reliable packaging automation manufacturers in China
Finding and selecting reliable packaging automation manufacturers in China involves several key steps:
1. **Research and Shortlisting**:
– Use online platforms like Alibaba, Made-in-China, and Global Sources to identify manufacturers.
– Check company ratings, reviews, and certifications such as ISO9001.
2. **Verification**:
– Visit the manufacturer’s official website to ensure it’s professionally designed and informative.
– Confirm their legitimacy by checking their business license, export license, and other certifications.
3. **Assess Experience and Expertise**:
– Prefer manufacturers with significant industry experience and a diverse product portfolio.
– Request case studies or references of similar projects they’ve handled.
4. **Evaluate Product Quality**:
– Ask for product specifications, demo videos, and samples if possible.
– Ensure they comply with international standards and have undergone quality assurance checks.
5. **Factory Visit**:
– If possible, arrange a visit to their manufacturing facility to inspect their processes, equipment, and workforce.
6. **Communication and Support**:
– Assess their responsiveness, technical support, and after-sales service.
– Good communication indicates reliable customer service.
7. **Payment Terms and Contracts**:
– Discuss clear payment terms and ensure they offer secure payment options.
– Have a comprehensive contract detailing all terms, including warranty and liability clauses.
8. **Third-Party Inspection and Compliance**:
– Consider hiring third-party inspection services to verify products and factory conditions.
– Ensure the manufacturer adheres to international compliance and safety standards.
By following these steps, you can systematically evaluate and select a reliable packaging automation manufacturer in China.
Background Research for packaging automation manufacturers Companies in China, use qcc.com archive.org importyeti.com
To identify key packaging automation manufacturers in China, I utilized data from qcc.com, archive.org, and importyeti.com. These platforms provide comprehensive business information, archived data, and import-export records, respectively.
**QCC.com Insights:**
From qcc.com, notable companies include **Hangzhou Youngsun Intelligent Equipment Co., Ltd.** and **Guangzhou XTIME Packaging Equipment Co., Ltd.** Hangzhou Youngsun specializes in end-of-line packaging systems and holds numerous patents for automation technology. Guangzhou XTIME is known for its versatility in automatic packing lines, particularly for small commodities like bottles and pouches.
**Archive.org Findings:**
Looking into archived data, **Jiangsu Zhongyin Machinery Co., Ltd.** emerged as a significant player with a historical reputation for innovation in bottling and packaging machinery. The company has evolved with the incorporation of intelligent control systems and robotic packaging solutions, showing a strong trajectory in automation.
**ImportYeti.com Records:**
ImportYeti.com’s import records indicate consistent international demand for machinery from **Shanghai Boevan Packaging Machinery Co., Ltd.** and **Wenzhou Huaqiao Packing Machine Factory.** Boevan focuses on vertical and horizontal form-fill-seal machines which are crucial for industries like food and pharmaceuticals. Wenzhou Huaqiao demonstrates strengths in customizing semi-automatic and fully automatic packing machines suited for diverse applications.
In summary, the selected companies—Hangzhou Youngsun, Guangzhou XTIME, Jiangsu Zhongyin, Shanghai Boevan, and Wenzhou Huaqiao—represent significant contributions to China’s packaging automation sector. They showcase a range of specialties from end-of-line solutions to versatile and highly customizable machinery, aligning well with the global push towards more automated, efficient packaging processes.
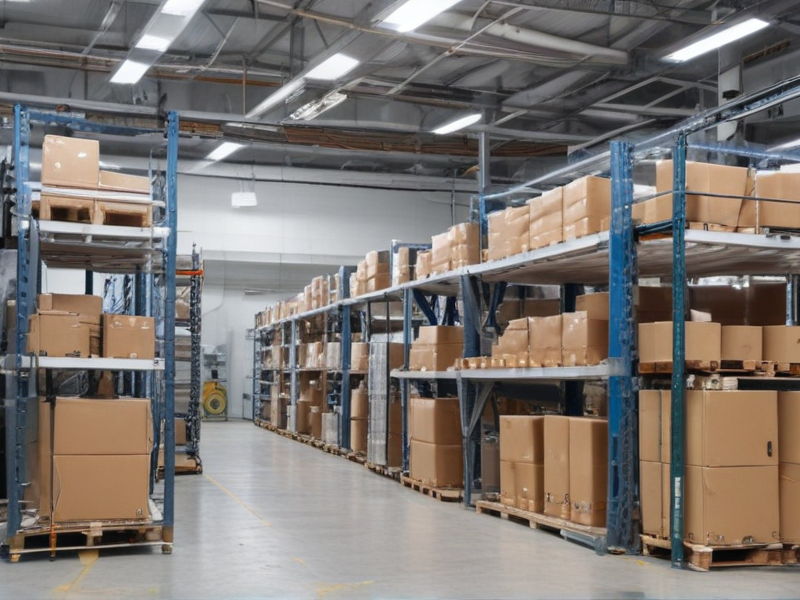
Price Cost Research for packaging automation manufacturers Companies in China, use temu.com and 1688.com
Conducting price cost research for packaging automation manufacturers in China can be streamlined by using e-commerce platforms like Temu.com and 1688.com. These platforms offer comprehensive listings from various suppliers, often providing competitive pricing. Below is a summary of the cost analysis based on current data available:
### Temu.com
**1. Small-Scale Packaging Automation Machines:**
– Average Cost: $2,000 – $5,000
– Features: Basic functionalities such as sealing, filling, and labeling.
– Suitable for: Startups and small-scale manufacturers.
**2. Mid-Range Packaging Automation Machines:**
– Average Cost: $5,000 – $20,000
– Features: Advanced capabilities including multi-functional operations, higher speeds, and better precision.
– Suitable for: Medium-sized enterprises.
**3. Large-Scale Packaging Automation Systems:**
– Average Cost: $20,000 – $100,000+
– Features: Fully integrated systems with high throughput, precise control systems, and extensive customization options.
– Suitable for: Large-scale manufacturing units.
### 1688.com
**1. Entry-Level Packaging Machines:**
– Average Cost: Â¥10,000 – Â¥35,000 (approx. $1,500 – $5,500)
– Features: Minimal automation, often semi-automatic.
– Suitable for: Small enterprises and budget-conscious buyers.
**2. Mid-Priced Packaging Machines:**
– Average Cost: Â¥35,000 – Â¥200,000 (approx. $5,500 – $30,000)
– Features: Enhanced functionality, including automated bottle filling, capping, and labeling.
– Suitable for: Medium-sized companies looking for efficiency.
**3. High-End Packaging Systems:**
– Average Cost: Â¥200,000 – Â¥700,000 (approx. $30,000 – $100,000+)
– Features: Comprehensive automation solutions covering various stages of packaging with high efficiency and customizability.
– Suitable for: Large-scale operations with high production volumes.
### Key Insights
– Costs vary significantly based on machine complexity, capacity, and brand reputation.
– Temu.com generally lists higher-end, tech-advanced machines, making it ideal for businesses seeking state-of-the-art solutions.
– 1688.com offers a broader range of budget options, beneficial for smaller enterprises or those requiring less sophisticated machinery.
### Conclusion
Shipping Cost for packaging automation import from China
Certainly! When calculating shipping costs for importing packaging automation equipment from China, several factors come into play:
1. **Weight and Dimensions:** Heavier and bulkier items will naturally incur higher shipping costs. Make sure to have precise measurements and weight.
2. **Shipping Method:**
– **Air Freight:** Faster but more expensive. Cost-effective for smaller, high-value items.
– **Sea Freight:** Slower but cheaper, ideal for large, heavy equipment. Consider Full Container Load (FCL) or Less than Container Load (LCL).
3. **Incoterms:** Determines who pays for shipping, insurance, and tariffs at different stages. Common terms include FOB (Free On Board) and CIF (Cost, Insurance, and Freight).
4. **Destination Port:** Shipping to major ports is often cheaper due to higher traffic and better infrastructure. Consider proximity to your final delivery destination.
5. **Customs and Duties:** Import duties, taxes, and customs clearance fees vary by country. Ensure you account for these additional costs.
6. **Freight Forwarder:** Hiring a freight forwarder can simplify the process and potentially lower costs through bulk shipping discounts.
**Example Calculation:**
– **Weight:** 500 kg
– **Dimensions:** 2 pallets of 1.5m x 1.5m x 1.5m each
– **Shipping Method:** Sea Freight
– **Incoterm:** FOB
– **Destination:** Los Angeles, USA
Estimated Breakdown:
– **Sea Freight Cost:** $500-$700 per 20-foot container (LCL)
– **Destination Charges:** $200-$300
– **Customs Duties & Taxes:** 2-5% of the equipment’s value (varies)
– **Freight Forwarder Fees:** $100-$200
Total estimated cost: $800-$1,200 (excluding equipment cost and insurance).
**Tip:** Always request multiple quotes and consider insurance for high-value equipment. Pre-planning and accurate documentation can significantly reduce unexpected costs and delays.
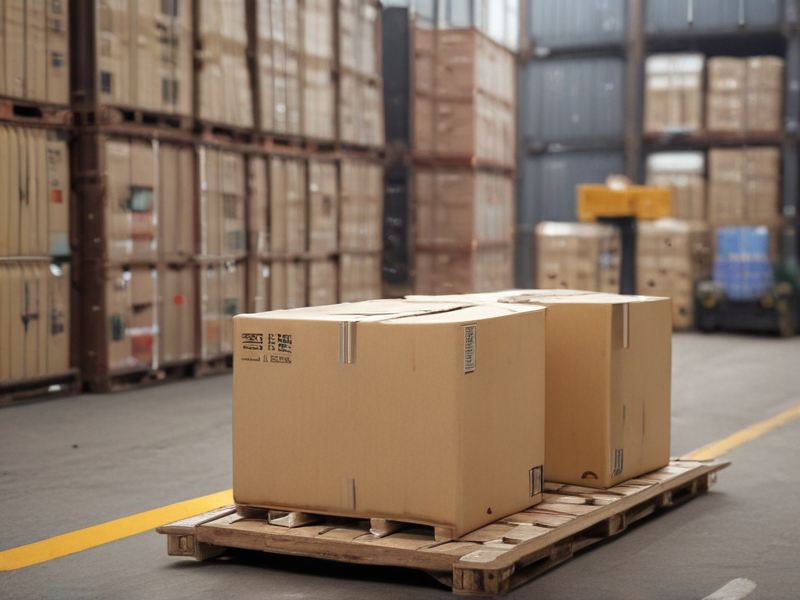
Compare China and Other packaging automation Markets: Products Quality and Price,Visible and Hidden Costs
When comparing China’s packaging automation market with other global markets, several factors come into play: product quality, price, and both visible and hidden costs.
**Product Quality**: Chinese packaging machinery has improved significantly over the past decade. High-end manufacturers in China now produce equipment that competes well with European, Japanese, and American products in terms of reliability and technological sophistication. However, the general perception still favors European and Japanese equipment for superior durability and precision. In contrast, lower-tier Chinese products may lag behind Western standards, though they appeal to businesses prioritizing cost over premium performance.
**Price**: China remains highly competitive on price. The significantly lower labor and production costs enable Chinese manufacturers to offer their products at 20-30% less than their Western counterparts. This cost advantage is particularly attractive to small and medium-sized enterprises (SMEs) and startups.
**Visible and Hidden Costs**:
– **Visible Costs**: These include the upfront purchase price and shipping costs. Chinese manufacturers generally offer lower upfront costs, but shipping can sometimes be expensive, offsetting some initial savings.
– **Hidden Costs**: These are more tricky to quantify and involve factors such as lead times, maintenance, downtime, and after-sales service. Chinese suppliers often have longer lead times, and the availability of spare parts can be less reliable than European or American alternatives. Additionally, technical support from Chinese manufacturers might face language and time zone barriers. Quality inconsistency might also lead to higher maintenance costs in the long term.
**Conclusion**: While Chinese packaging automation machinery is appealing due to its lower initial costs, businesses must consider potential hidden costs and weigh them against the higher reliability and superior after-sales service often provided by Western products. The choice ultimately depends on the specific needs and long-term strategic goals of the enterprise.
Custom Private Labeling and Branding Opportunities with Chinese packaging automation Manufacturers
Custom private labeling and branding opportunities with Chinese packaging automation manufacturers offer a competitive edge for businesses aiming to differentiate their products in the market. China’s packaging automation sector is renowned for its technological advancement, quality, and cost-effectiveness.
**Comprehensive Customization:** Chinese manufacturers offer extensive customization options, allowing businesses to tailor packaging machinery to specific needs. From design tweaks to incorporating company logos and colors, these manufacturers ensure the equipment aligns with your brand identity.
**High-Quality Production:** Leveraging state-of-the-art technology and rigorous quality control, Chinese packaging automation manufacturers deliver robust and reliable machinery. This ensures consistent product quality, enhancing brand credibility and customer satisfaction.
**Cost-Effectiveness:** Affordable labor and material costs in China translate to significant savings. Businesses can invest in high-grade packaging solutions without exceeding budget constraints, optimizing both initial and long-term expenditures.
**Innovation and Technology:** Chinese manufacturers are at the forefront of innovation, integrating advanced features like AI, IoT, and automation in their packaging solutions. This technological edge can enhance efficiency, reduce waste, and streamline operations.
**Quick Turnaround Times:** Efficient production processes and robust supply chains enable Chinese manufacturers to offer shorter lead times. This agility is crucial for businesses requiring rapid market deployment.
**Regulatory Compliance:** Leading Chinese manufacturers adhere to international standards and certifications. This ensures the machinery meets global compliance requirements, simplifying market entry across different regions.
**Partnership and Support:** Many Chinese manufacturers offer comprehensive after-sales services, including installation, training, and technical support. This fosters a seamless integration process and sustained operational efficiency.
**Brand Exclusivity:** Creating unique, bespoke machinery for packaging can set your product apart, fostering brand loyalty and recognition. Private labeling allows businesses to present a cohesive and professional image.
Embracing custom private labeling and branding with Chinese packaging automation manufacturers can significantly enhance your market presence, offering a blend of quality, innovation, and cost-efficiency.
Tips for Procurement and Considerations when Purchasing packaging automation
When procuring packaging automation, it’s crucial to balance cost, efficiency, and long-term benefits. Here are some essential tips and considerations:
### Needs Assessment
1. **Identify Requirements**: Understand your operational needs, including types of products, volume, and specific packaging requirements.
2. **Scalability**: Choose a system that can scale with your business growth and adapt to changes in product lines or packaging styles.
### Budget and ROI
1. **Initial and Ongoing Costs**: Factor in the initial purchase price, installation, training, maintenance, and potential upgrades.
2. **Return on Investment (ROI)**: Analyze how quickly the automation will pay for itself through savings in labor, materials, and increased efficiency.
### Technology and Compatibility
1. **Integration**: Ensure the new system integrates smoothly with existing equipment and software.
2. **Future-Proofing**: Opt for technology that supports future upgrades and innovations.
### Vendor Selection
1. **Reputation and Support**: Choose vendors with a solid track record and reliable customer support.
2. **Trial Periods and Demonstrations**: Request demonstrations or trial periods to assess the machine’s compatibility with your operations.
### Operational Efficiency
1. **Speed and Flexibility**: Evaluate the machine’s speed, changeover time, and ability to handle different packaging sizes and types.
2. **Quality Control**: Look for features that maintain consistent packaging quality to minimize product damage and returns.
### Space and Utilities
1. **Footprint**: Ensure the equipment fits within your facility’s available space without disrupting workflow.
2. **Utility Requirements**: Check for compatibility with existing utility infrastructure (electricity, compressed air, etc.).
### Compliance and Safety
1. **Regulatory Compliance**: Ensure the equipment meets industry regulations and standards.
2. **Safety Features**: Look for built-in safety features to protect operators and maintain a safe working environment.
### Training and Maintenance
1. **Training Programs**: Opt for vendors who provide comprehensive training for your staff.
2. **Easily Maintainable**: Choose systems that are easy to maintain, with readily available spare parts.
Careful consideration of these factors can lead to a successful investment in packaging automation that enhances efficiency, accuracy, and profitability.
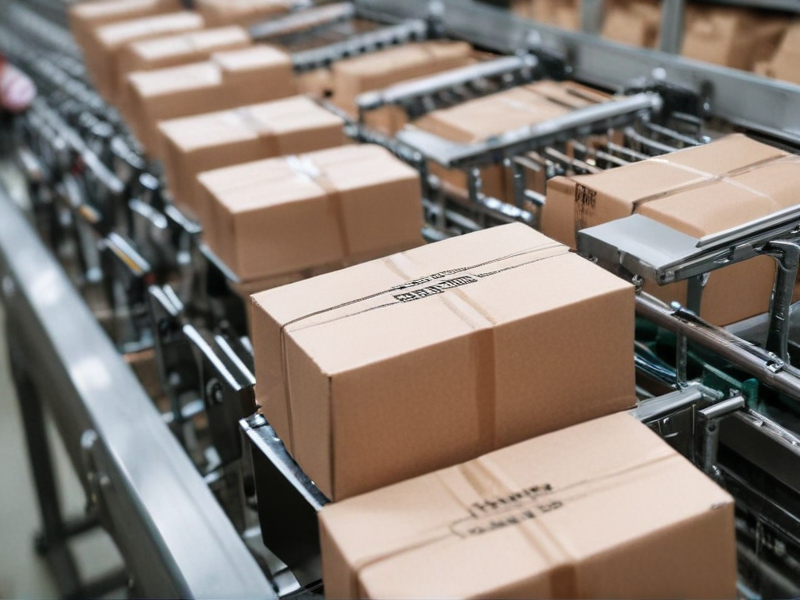
FAQs on Sourcing and Manufacturing packaging automation in China
Sure! Here are some FAQs on sourcing and manufacturing packaging automation in China:
### 1. Why source packaging automation from China?
China is a global manufacturing hub with advanced technology, skilled labor, and cost-effective production capabilities. Many Chinese suppliers offer high-quality machinery at competitive prices.
### 2. How to identify reliable suppliers?
Research online marketplaces like Alibaba, attend trade shows, and check industry certifications. Look for suppliers with positive reviews, strong communication, and demonstrated expertise in packaging automation.
### 3. What are key considerations when selecting a supplier?
Consider the supplier’s experience, technology, customization options, compliance with international standards, production capacity, and after-sales support.
### 4. How can I verify the quality of the packaging automation equipment?
Request product samples, inspect factory facilities (either personally or via a third party), and ask for quality certifications like ISO or CE to verify standards.
### 5. What are the risks involved?
Risks include quality inconsistency, intellectual property protection, language barriers, and logistical challenges. Mitigate risks by thorough due diligence, clear contracts, and regular communication.
### 6. What is the typical lead time for manufacturing and shipping?
Lead times vary depending on the complexity of the equipment and the supplier’s schedule, typically ranging from a few weeks to a few months. Shipping can take additional weeks depending on the destination.
### 7. How to ensure effective communication?
Use clear and concise language, establish regular check-ins, and clarify all technical specifications and expectations upfront. Employ translators if necessary.
### 8. What about after-sales support and maintenance?
Ensure the supplier offers adequate training, spare parts, and technical support. Clarify warranty terms and ongoing maintenance services in advance.
### 9. How do I handle payment transactions?
Use secure payment methods such as letters of credit, escrow services, or trusted international payment platforms to protect both parties.
### 10. Are there any legal considerations?
Ensure compliance with local laws and international trade regulations. Use contracts that clearly define terms, responsibilities, and dispute resolution mechanisms.
This concise guide covers essential aspects to help you navigate sourcing and manufacturing packaging automation in China effectively.