Top 10 automated packaging in China introduce,list main products and website if have
Sure! Below is a brief introduction to some of the top automated packaging companies in China, along with their main products and websites:
1. **Sino-Pack**
– **Main Products**: Complete automated packaging solutions for industries including food, beverages, pharmaceuticals, and consumer goods.
– **Website**: [sinopackpackaging.com](http://www.sinopackpackaging.com/)
2. **Tech-Long**
– **Main Products**: Intelligent packaging lines, including bottle blow molding, filling, labeling, packaging, and palletizing.
– **Website**: [tech-long.com](http://www.tech-long.com/)
3. **Buhler Group**
– **Main Products**: Grain and food automated processing and packaging equipment.
– **Website**: [buhlergroup.com](https://www.buhlergroup.com/)
4. **Newamstar**
– **Main Products**: Liquid packaging production lines, including PET bottle blowing, filling, and packaging.
– **Website**: [newamstar.com](http://www.newamstar.com/)
5. **Sinyoung**
– **Main Products**: Packaging and automation solutions for the pharmaceutical and food industries.
– **Website**: [sinyoung.com](http://www.sinyoung.com/)
6. **Triowin**
– **Main Products**: Food processing and packaging machinery, including fruit and vegetable processing lines.
– **Website**: [triowin.com](http://www.triowin.com/)
7. **JNWB Packaging (Jinan Wanban Packaging Automation)**
– **Main Products**: Packaging machinery and automation solutions, focusing on bagging and wrapping technologies.
– **Website**: [jnwbpack.com](http://www.jnwbpack.com/)
8. **Goldpack**
– **Main Products**: Automated packaging machines for liquid, powder, granule, and other materials.
– **Website**: [goldpack.com.cn](http://www.goldpack.com.cn/)
9. **Teconn Prosperity Group**
– **Main Products**: Diverse packaging machines including stretch wrapping, carton sealing, and palletizing.
– **Website**: [teconn.com.cn](http://www.teconn.com.cn/)
10. **Shanghai Grepack**
– **Main Products**: Filling machines, capping machines, labeling machines, and integrated packaging solutions.
– **Website**: [grepack.com](http://www.grepack.com/)
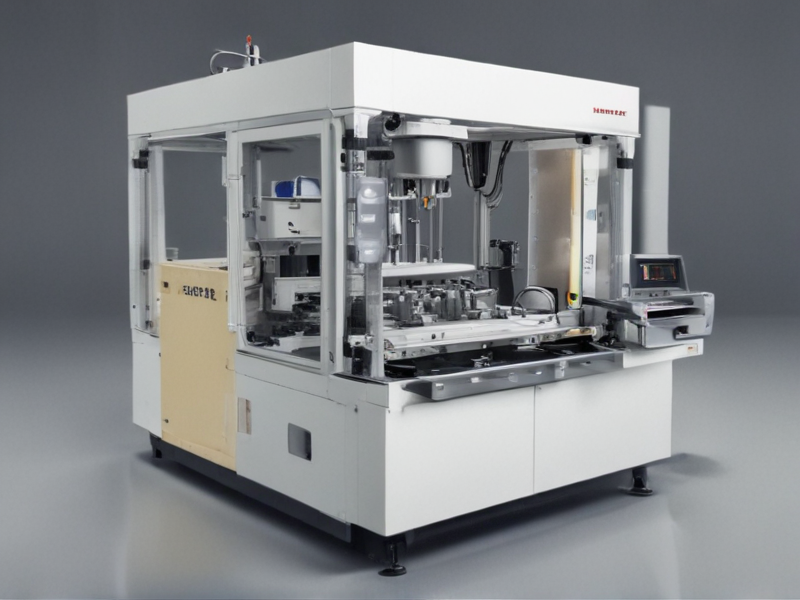
Types of automated packaging
Automated packaging systems streamline the packing process, enhancing efficiency and reducing labor costs. Here are the main types of automated packaging:
1. **Filling Machines**:
– Used to fill bottles, cans, or containers with liquids, powders, or solids.
– Variants include liquid fillers, powder fillers, and granular product fillers.
2. **Capping Machines**:
– Apply and secure caps or lids onto containers.
– Types include screw cappers, press-on cappers, and rotary cappers.
3. **Labeling Machines**:
– Attach labels to packages or products.
– Common types are pressure-sensitive labelers, sleeve labelers, and hot-melt glue labelers.
4. **Form, Fill, Seal (FFS) Machines**:
– Construct packages from a roll of materials, fill them with product, and seal them.
– Utilized for products like snacks, powders, liquids, and more.
5. **Cartoning Machines**:
– Form cartons from flat blanks and fill them with products.
– Can be horizontal or vertical based on product type and packaging requirements.
6. **Wrapping Machines**:
– Enclose products in protective packaging such as shrink wrap or stretch film.
– Popular for bundling multiple items together or securing them on pallets.
7. **Palletizing Systems**:
– Automatically stack products onto pallets in a defined pattern.
– Can be robotic or conventional, depending on complexity and speed requirements.
8. **Case Packing Machines**:
– Pack individual products into cases or boxes.
– Variants include wrap-around case packers, drop packers, and pick-and-place packers.
9. **Blister and Skin Packaging Machines**:
– Create blister packs or skin packs for individual product packaging.
– Common in the pharmaceutical and small consumer goods sectors.
10. **Inspection and Quality Control Systems**:
– Detect defects, verify weights, and ensure correct labeling.
– Technologies include vision systems, metal detectors, and checkweighers.
Automated packaging systems offer versatility and can be tailored to different industries, enhancing productivity and consistency.
Pros and Cons of Using automated packaging
Automated packaging systems have become increasingly popular in manufacturing and logistics due to their numerous advantages, but they also come with some drawbacks. Below, I outline the key pros and cons of using automated packaging.
### Pros
1. **Efficiency and Speed**: Automated systems significantly increase the speed of packaging processes, enabling higher throughput and consistent output.
2. **Cost Savings**: While the initial investment can be high, the reduction in labor costs and increased productivity often result in long-term cost savings.
3. **Consistency and Quality**: Automated packaging ensures uniformity and reduces human error, leading to more consistent and higher-quality packaging.
4. **Enhanced Safety**: By reducing the need for manual labor in potentially hazardous environments, automated systems can improve workplace safety.
5. **Scalability**: Automated systems can easily be scaled up or adapted to handle different types of products with minimal manual intervention.
### Cons
1. **High Initial Investment**: The cost of purchasing and installing automated packaging equipment can be prohibitive for small and medium-sized enterprises.
2. **Maintenance and Downtime**: Automated systems require regular maintenance and can experience downtime, which could disrupt operations if not managed properly.
3. **Job Displacement**: Automation can lead to reduced demand for manual labor, which might result in job losses and require retraining of the affected workforce.
4. **Complexity and Training**: Operating and maintaining automated systems often require specialized skills, necessitating additional training for existing personnel.
5. **Rigidity**: While scalable, automated systems can sometimes be less flexible when it comes to handling custom or small-batch packaging needs compared to manual processes.
### Conclusion
Automated packaging systems offer significant advantages in terms of efficiency, cost savings, and quality control, making them highly attractive for large-scale operations. However, the high initial investment, maintenance requirements, and job displacement issues pose considerable challenges. Companies must carefully weigh these factors to determine whether automation aligns with their operational goals and capabilities.
automated packaging Reference Specifications (varies for different product)
Automated packaging systems are pivotal in enhancing efficiency, accuracy, and productivity in various industries. The reference specifications for automated packaging can vary widely based on the type of product being packaged. Below are the general considerations and specifications that are commonly adapted to specific products:
1. **Product Types**:
– **Fragile Items**: Requires gentle handling, padding, and precise placement to prevent damage.
– **Perishable Goods**: Needs temperature control, fast processing, and possibly vacuum sealing.
– **Bulk Goods**: Involves heavy-duty machines, robust materials, and scalable operations.
– **Pharmaceuticals**: Must comply with stringent regulations, incorporate precise dosing, and secure packaging for contamination prevention.
2. **Packaging Materials**:
– Materials vary from cardboard, plastic, glass, metal, to bioplastics, each selected based on product needs and sustainability goals.
3. **Machines & Technology**:
– **Cartoning Machines**: For box packaging.
– **Wrapping Machines**: For stretch, shrink, and film wrapping.
– **Filling Machines**: For liquid, powder, or granular products.
– **Labeling Machines**: For barcode, QR code, and information labeling.
– **Sealing Machines**: For heat sealing, induction sealing, etc.
– Integration with **Robotic Arms** for precise and fast movements.
4. **Machinery Specifications**:
– **Speed**: Varied depending on production volume (e.g., 30 to 200 units per minute).
– **Accuracy**: Essential for correct fill levels, placement, and sealing.
– **Modularity**: Ability to adapt and upgrade components as needed.
– **Footprint**: Space constraints and layout design considerations.
– **User Interface**: Intuitive control panels, often with touch screens.
– **Maintenance**: Ease of cleaning, routine checks, and minimal downtime.
5. **Compliance and Safety**:
– Adherence to industry standards (e.g., FDA for food and pharmaceuticals).
– Safety features such as emergency stops, sensors, and guarding.
6. **Software Integration**:
– Use of MES (Manufacturing Execution Systems), SCADA (Supervisory Control and Data Acquisition), and ERP (Enterprise Resource Planning) systems for real-time monitoring, data collection, and process optimization.
In summary, automated packaging specifications must be customized to meet the diverse requirements of different products while focusing on efficiency, accuracy, and compliance with industry standards.
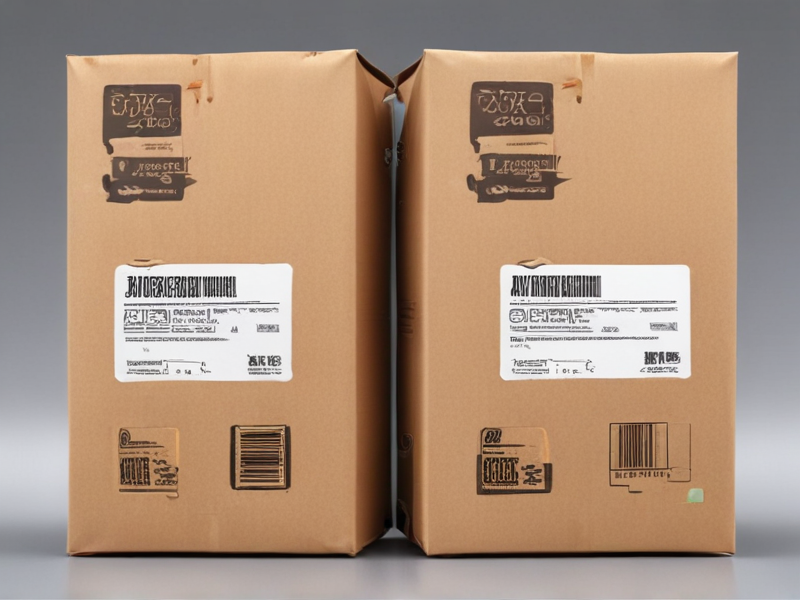
Applications of automated packaging
Automated packaging technology has revolutionized numerous industries by enhancing efficiency, accuracy, and cost-effectiveness. Here are some key applications:
1. **Food and Beverage Industry**: Automated systems handle tasks like filling, sealing, labeling, and palletizing. This not only speeds up the process but also ensures hygiene and consistency, crucial for products like sauces, beverages, and snack foods.
2. **Pharmaceuticals**: In the pharmaceutical industry, precision is paramount. Automation ensures accurate dosing, secure sealing, and tamper-evident packaging which is vital for maintaining drug efficacy and safety standards.
3. **Consumer Goods**: From electronics to household items, automation in packaging allows for customized packaging solutions, reducing material waste and enhancing the visual appeal, which is important in a competitive retail environment.
4. **E-commerce and Logistics**: Automated packaging systems improve order fulfillment speed and accuracy. Technologies like automated box sizing and robotic sorters streamline the packaging process, significantly reducing shipping errors and handling time.
5. **Automotive Industry**: Components are often packaged in specialized containers to prevent damage during transit. Automation helps in efficiently managing these processes, ensuring components reach assembly lines or dealerships intact.
6. **Cosmetics and Personal Care**: This sector benefits from automation through precise filling and attractive packaging, crucial for customer satisfaction. Automated systems can handle delicate and variable-sized items, ensuring high-quality presentation.
7. **Agriculture**: Automated packaging in agriculture helps in bagging grains, seeds, and produce swiftly and consistently, minimizing human error and enhancing storage life with vacuum sealing technologies.
8. **Medical Devices**: Ensuring sterility and integrity of medical devices is critical. Automated packaging systems provide hermetic sealing and sterile barrier systems, often incorporating validation processes to meet regulatory standards.
Each of these applications leverages the speed, precision, and efficiency of automated packaging to meet industry-specific demands, ultimately contributing to overall productivity and quality improvement.
Material of automated packaging
Automated packaging systems, designed to optimize efficiency and precision in packing processes, rely on various materials depending on the specific application and requirements. Key materials include:
1. **Plastics**: Polyethylene (PE), polypropylene (PP), and polyvinyl chloride (PVC) are commonly used due to their flexibility, durability, and cost-effectiveness. These materials are ideal for creating bags, wraps, and containers.
2. **Metals**: Stainless steel and aluminum are prevalent in automated packaging machinery for their strength, corrosion resistance, and longevity. These metals are integral to the construction of machine frames, conveyors, and other structural components.
3. **Paper and Cardboard**: For eco-friendly packaging solutions, paper and cardboard are favored. These materials are biodegradable and recyclable, making them suitable for boxes, cartons, and wrapping.
4. **Biodegradable Plastics**: Polylactic acid (PLA) and other biodegradable polymers are gaining traction as sustainable alternatives to traditional plastics. These materials decompose more quickly, reducing environmental impact.
5. **Foams**: Polyurethane and polyethylene foams are utilized for cushioning and protecting products within packaging. These foams can be molded or cut to fit various shapes and sizes.
6. **Composite Materials**: A combination of materials like paper-plastic laminates provides enhanced properties such as moisture resistance and strength, ideal for complex packaging needs.
Each material offers distinct advantages and is selected based on factors such as product type, protection level required, sustainability goals, and cost constraints. Automated packaging systems are designed to seamlessly integrate these materials, ensuring efficient and reliable packaging processes for a wide range of industries.
Quality Testing Methods for automated packaging and how to control the quality
Ensuring quality in automated packaging involves a suite of testing methods and control strategies to maintain high standards and prevent defects. Here are key methods and controls:
1. **Visual Inspection Systems**: High-resolution cameras and machine learning algorithms detect visual defects like misprints, misalignment, and package damage. Automated systems flag defects in real-time, ensuring only compliant products proceed.
2. **Weight Verification**: Checkweighers ascertain each package meets specified weight standards. This is vital for compliance and consumer trust, especially in food and pharmaceutical industries.
3. **Seal Integrity Testing**: Ensures hermetic seals or other closure systems are intact, preventing contamination and ensuring freshness. Methods include vacuum decay tests and pressure differential testing.
4. **Barcode Verification**: Optical scanners verify the accuracy of barcodes, ensuring proper tracking and inventory management. This reduces errors in the supply chain and enhances traceability.
5. **Functionality Testing**: For packages with functional elements (e.g., reclosable zippers), automated systems check that these features operate correctly.
Quality Control Strategies:
1. **Statistical Process Control (SPC)**: Uses statistical methods to monitor and control the production process. It helps identify variations that can indicate defects, enabling proactive adjustments.
2. **Automated Data Logging & Analysis**: Systems log data from inspections and tests. Advanced analytics detect trends, facilitating early intervention in the process.
3. **Fail-Safe Mechanisms**: Incorporate redundancy and fail-safes to halt production when anomalies are detected, ensuring defective batches don’t proceed.
4. **Regular Calibration and Maintenance**: Keep all machinery and testing equipment calibrated and well-maintained. Regular audits and maintenance schedules prevent equipment drift and ensure accuracy.
5. **Employee Training**: Though the process is automated, training staff to understand and oversee automated systems is crucial. Skilled personnel can quickly address issues and maintain smooth operations.
Collectively, these methods and controls create a robust framework to ensure consistent, high-quality packaging in automated environments.
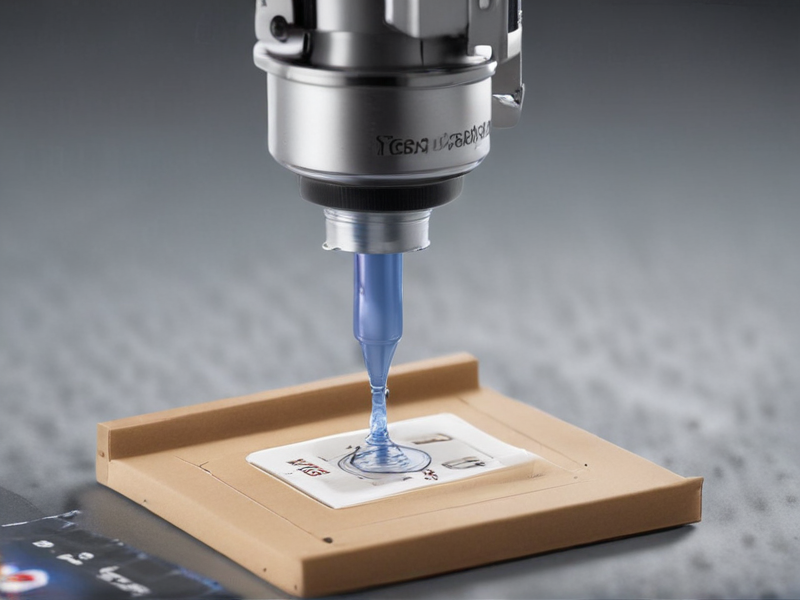
The Work Process and how to use automated packaging
Streamlining the work process with automated packaging solutions enhances efficiency, reduces labor costs, and ensures consistent quality. Here’s how to effectively implement and utilize automated packaging:
1. **Assessment and Planning:**
– **Evaluate Needs:** Examine the type and volume of products to determine suitable packaging machinery.
– **Budgeting:** Establish a budget considering both initial costs and long-term savings.
2. **Selecting Equipment:**
– **Types of Machines:** Choose from options like automatic bagging machines, case packers, palletizers, wrapping machines, and labeling systems.
– **Customization:** Opt for machines that can be customized to handle specific packaging materials and sizes.
3. **Integration:**
– **Seamless Workflow:** Integrate the packaging machinery into the existing production line to minimize bottlenecks.
– **Software Compatibility:** Ensure the machinery is compatible with your operational software for efficient tracking and control.
4. **Operator Training:**
– **Hands-On Training:** Train operators on machine settings, troubleshooting, and routine maintenance.
– **Safety Protocols:** Emphasize safety guidelines to prevent accidents and ensure workplace safety.
5. **Process Automation:**
– **Efficiency:** Utilize sensors and automated controls to streamline the packaging process, reducing manual intervention.
– **Quality Control:** Implement automated systems for inspection to ensure packaging consistency and quality.
6. **Maintenance and Support:**
– **Regular Maintenance:** Schedule regular checks and maintenance to prolong machinery lifespan.
– **Technical Support:** Ensure access to professional support for troubleshooting and repairs.
7. **Data Utilization:**
– **Analytics:** Use machine data to monitor performance, identify inefficiencies, and make informed decisions.
– **Continuous Improvement:** Regularly evaluate and upgrade systems to adapt to new packaging needs and technologies.
By opting for automated packaging solutions, businesses can significantly boost productivity, maintain consistent quality, and optimize resource allocation, ultimately leading to better operational efficiency and cost savings.
automated packaging Importing questions including Cost,Supplier,Sample,Certification and Market
Importing automated packaging systems involves several critical considerations to ensure cost-effectiveness and compliance with regulations. Below are key points you should address:
**Cost:**
– **Initial Investment:** Assess the cost of the machinery, including shipping and installation.
– **Operating Costs:** Account for maintenance, energy consumption, and potential downtime.
– **Total Cost of Ownership (TCO):** Consider long-term costs over the machine’s lifespan.
**Supplier:**
– **Reputation:** Research supplier reliability, customer reviews, and industry standing.
– **Support:** Evaluate the level of technical support and after-sales service offered.
– **Compliance:** Ensure the supplier adheres to international trading laws and standards.
**Sample:**
– **Testing:** Request sample machinery or trial periods to evaluate performance.
– **Customization:** Ensure the supplier can tailor the system to meet your specific needs.
– **Evaluation:** Conduct tests in real operational settings to assess efficiency and compatibility.
**Certification:**
– **Quality Standards:** Verify certifications like ISO 9001, CE marking, or other relevant industry certifications.
– **Regulatory Compliance:** Ensure the equipment complies with local and international safety and environmental regulations.
– **Documentation:** Obtain all necessary documentation for customs, installation, and operation.
**Market:**
– **Demand Analysis:** Evaluate current and future demand for the types of packaging automation you intend to implement.
– **Competition:** Analyze competitors to understand market position and potential profitability.
– **Adaptability:** Ensure the machinery can adapt to future market trends and diverse packaging requirements.
By addressing these critical areas, you can make informed decisions that enhance operational efficiency and market competitiveness.
How to find and select check reliable automated packaging manufacturers in China
Finding and selecting reliable automated packaging manufacturers in China requires a methodical approach. Here’s a concise guide using less than 300 words:
1. **Research**:
– **Online Directories**: Use platforms like Alibaba, Made-in-China, and Global Sources to get a list of manufacturers.
– **Industry Forums and Networks**: Join packaging industry forums and LinkedIn groups to get recommendations.
2. **Assess Credibility**:
– **Company Profile**: Check the manufacturer’s history, scale, and product range on their website and online directories.
– **Certifications**: Look for ISO certification and other industry-related credentials.
– **Customer Reviews**: Read reviews and ratings on both the manufacturer’s site and third-party portals.
3. **Direct Communication**:
– **Initial Contact**: Email or call the manufacturers to gauge their responsiveness and professionalism.
– **Inquire About Experience**: Ask about their experience with automated packaging systems and specific industries they serve.
4. **Quality Assurance**:
– **Request Samples**: Get samples or case studies of their past projects to evaluate their quality and reliability.
– **Factory Audits**: Conduct virtual or physical audits if possible to inspect their facilities and processes.
5. **Competitive Analysis**:
– **Quotes and Proposals**: Obtain detailed quotes and compare them, considering not just cost but also the value offered.
– **Lead Times**: Compare production and shipping timelines to ensure they align with your needs.
6. **References and Testimonials**:
– **Ask for References**: Request contact information of past clients and conduct brief interviews to understand their experiences.
7. **Agreements and Support**:
– **Contracts**: Ensure clear terms on quality, delivery schedules, and after-sales support.
– **After-Sales Service**: Verify the availability of technical support and spare parts post-purchase.
By following these steps, you can identify and select a reliable automated packaging manufacturer in China.
Background Research for automated packaging manufacturers Companies in China, use qcc.com archive.org importyeti.com
Sure, here’s a concise overview of some notable automated packaging manufacturers in China utilizing information from qcc.com, archive.org, and importyeti.com:
1. **Hangzhou Youngsun Intelligent Equipment Co., Ltd.**
– **Overview**: Established in 1983, Youngsun specializes in manufacturing automated packaging systems such as strapping machines, wrapping machines, and vacuum packing machines.
– **Reputation**: Recognized for its technological advancements and extensive product range.
– **Key Clients**: Frequently listed in import data, indicating strong international demand.
2. **Guangzhou PackBest Air Packaging Co., Ltd.**
– **Overview**: Known for producing air cushion machines and packaging solutions specializing in void fill, cushioning, and wrapping.
– **Technology**: Focuses on eco-friendly packaging automation, integrating latest technologies to improve efficiency and reduce waste.
– **Export Data**: ImportYeti shows consistent export activity to North America and Europe.
3. **Jenton Group (Shantou Jiesheng Robot Technology Co., Ltd.)**
– **Overview**: Founded in 2012, specializes in robotic packaging solutions including automated sealing and labeling systems.
– **Innovation**: Emphasizes R&D to introduce advanced robotic technologies tailored to packaging needs.
– **Archival Information**: Archive.org indicates steady growth and adaptation to market trends.
4. **Kunshan Bojin Trading Co., Ltd.**
– **Overview**: Focuses on small-to-medium scale automated packaging machines such as tape dispensers and label applicators.
– **Diversity**: Offers a wide range of customizable solutions for various industries.
– **Market Presence**: ImportYeti data highlight significant exports primarily to Asian and African markets.
5. **Zhejiang Dingye Machinery Co., Ltd.**
– **Overview**: Established in 1986, Dingye manufactures diverse packaging machinery including sealing, strapping, and vacuum packaging machines.
– **Market Reach**: Strong domestic presence with growing international market footprint.
– **Customer Base**: Regularly featured in import databases, signaling robust export operations.
Each of these companies leverages advanced technology to streamline packaging processes, offering scalable solutions to meet the diverse needs of their global clientele. Archival research and import data reinforce their credible market positions and continuous innovation trends.
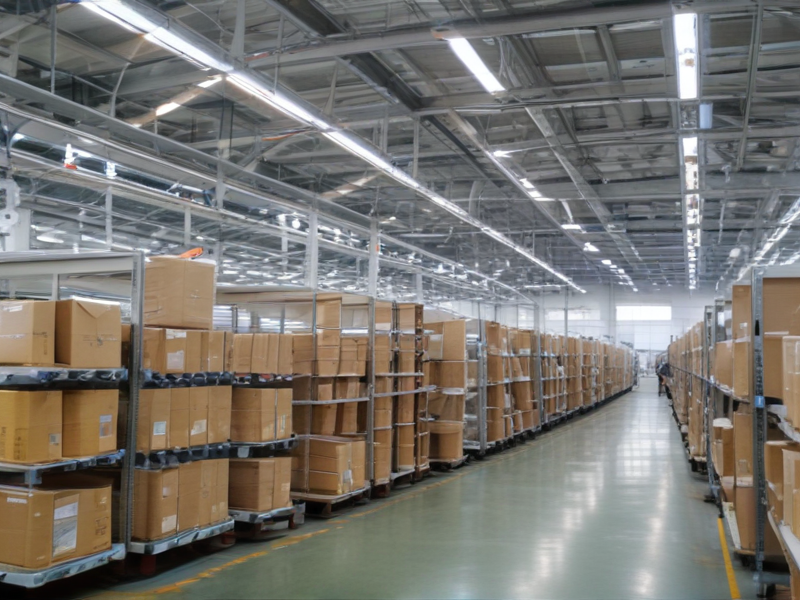
Price Cost Research for automated packaging manufacturers Companies in China, use temu.com and 1688.com
Conducting price cost research for automated packaging manufacturers in China can provide insights into potential suppliers and cost structures. Using platforms like Temu.com and 1688.com, two prominent Chinese B2B marketplaces, can be highly effective.
### Temu.com
Temu.com often serves international buyers seeking suppliers for various industrial needs. Automated packaging systems are complex, and their costs can vary widely based on specifications. As of my research, basic automated packaging machines for small-scale operations start around USD 5,000. Mid-range systems with more advanced features such as multi-functionality, higher speed, and better precision can range from USD 15,000 to USD 30,000. High-end, fully automated packaging systems, suitable for large industrial operations, can exceed USD 50,000.
### 1688.com
1688.com caters more to the Chinese domestic market but is also useful for international buyers. Prices here can sometimes be lower due to direct access to manufacturers. Entry-level automated packaging machines on 1688.com can start as low as CNY 30,000 (approximately USD 4,700). Mid-range systems are generally priced between CNY 80,000 to CNY 200,000 (approximately USD 12,500 to USD 31,300). Advanced, fully automated systems can cost upwards of CNY 300,000 (around USD 47,000).
### Considerations
1. **Customization**: Prices often vary based on customization needs.
2. **Volume Discounts**: Larger orders can often secure better pricing.
3. **Shipping and Import Fees**: These can add significantly to the cost.
### Conclusion
Both Temu.com and 1688.com offer valuable insights into the price ranges and suppliers of automated packaging machinery in China. For potential buyers, it is essential to evaluate machinery specifications, customization capabilities, and total costs, including shipping and tariffs, to make informed purchasing decisions.
Shipping Cost for automated packaging import from China
Shipping costs for automated packaging equipment imported from China can vary widely based on several factors:
1. **Shipping Method**:
– **Sea Freight**: This is generally the most cost-effective for bulky items like automated packaging machines. Shipping a 20-foot container costs between $1,000 to $3,000 depending on the route and market conditions. A 40-foot container might range from $2,500 to $4,500.
– **Air Freight**: Much faster but markedly more expensive. Rates can be anywhere from $5 to $15 per kilogram, making it suitable for urgent, small shipments.
2. **Weight and Dimensions**: Heavier and larger items incur higher costs. Measure and weigh your equipment accurately for precise quotes.
3. **Customs and Duties**: Import duties and taxes apply, often calculated as a percentage of the shipment’s value, including shipping costs. Check with local customs for specific rates.
4. **Port Charges and Handling Fees**: Expect additional costs at both the origin and destination ports, including terminal handling charges, documentation fees, and inland transportation if needed.
5. **Shipping Insurance**: Recommended for high-value machinery. Costs typically range from 0.5% to 2% of the shipment’s value.
6. **Shipping Company/Agent**: Rates differ by company. Obtaining multiple quotes is advisable.
**Cost Example**:
– A mid-sized automated packaging machine can cost approximately $2,000 to ship by sea in a 20-foot container.
– Adding insurance and handling fees might raise total costs to around $2,400 to $3,000.
– By air, the same machine might cost significantly more, potentially $10,000 or higher, depending on the machine’s weight and air freight rates.
**Recommendation**:
Sea freight is generally preferred for cost-efficiency unless time constraints necessitate air shipping. Always confirm the reliability of the shipping provider and ensure comprehensive coverage for transit risks.
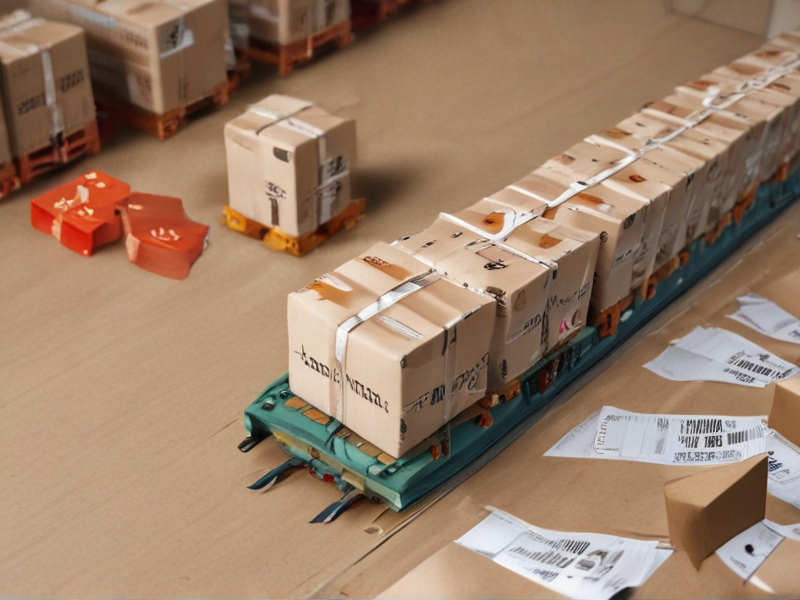
Compare China and Other automated packaging Markets: Products Quality and Price,Visible and Hidden Costs
When comparing China to other automated packaging markets, several factors come into play: product quality and price, visible and hidden costs.
**Product Quality and Price:**
Chinese automated packaging machinery is generally known for its affordability. Manufacturers can offer lower prices due to economies of scale, lower labor costs, and government subsidies. However, the quality of Chinese products can vary significantly. High-end manufacturers in China do produce competitive and reliable machines, but lower-tier providers may offer substandard products.
In contrast, automated packaging machines from markets like Germany, Japan, and the United States are often associated with superior quality and advanced technology. These markets invest heavily in research and development, reflected in the high precision, durability, and efficiency of their products. However, the upfront cost can be much higher than Chinese alternatives.
**Visible and Hidden Costs:**
The visible costs of automated packaging machinery encompass purchase price, shipping, and installation. Chinese machines often come with lower upfront costs, providing an attractive option for businesses on a tight budget. However, hidden costs can offset these savings.
Hidden costs include maintenance, spare parts availability, technical support, and machine downtime. Chinese manufacturers may not always offer robust after-sales support and local service centers, leading to longer downtimes and higher maintenance expenses. Conversely, manufacturers from Europe, Japan, and the U.S. typically provide comprehensive after-sales service, easy access to spare parts, and a reliable warranty, ensuring minimal disruption.
**Conclusion:**
Choosing between Chinese and other automated packaging markets requires balancing initial investment and long-term operational costs. Chinese machines are cost-effective for initial setup but involve risks of variable quality and higher long-term maintenance costs. Higher-priced machines from established global markets promise superior quality, reliability, and lower hidden costs, making them a preferable option for businesses prioritizing long-term efficiency and durability.
Custom Private Labeling and Branding Opportunities with Chinese automated packaging Manufacturers
Custom private labeling and branding with Chinese automated packaging manufacturers present lucrative opportunities for businesses aiming to enhance their product identity and market appeal. Leveraging China’s advanced manufacturing capabilities and cost efficiencies, businesses can achieve premium packaging solutions that align with their brand ethos and market strategies.
### Advantages:
**Cost-Effectiveness:** Chinese manufacturers offer competitive pricing thanks to lower labor and material costs, making high-quality packaging accessible even for small businesses.
**Technological Proficiency:** Equipped with cutting-edge automated machinery, Chinese manufacturers can produce intricate and innovative packaging designs with high precision and consistency.
**Scalability:** The high production capacity of Chinese manufacturers ensures they can handle both small and large scale orders, allowing flexibility as business needs evolve.
**Customization:** These manufacturers provide extensive customization options, from material selection to design elements such as logos, colors, and textures, enabling brands to create distinctive packaging that stands out in the market.
**Speed to Market:** Efficient production processes and robust logistics infrastructure in China mean quicker turnaround times, essential for staying competitive in fast-moving markets.
### Key Considerations:
**Quality Assurance:** Partnering with manufacturers known for stringent quality control measures is crucial. Certifications like ISO 9001 and regular audits can help ensure consistent quality.
**Communication:** Clear and consistent communication is vital. Language barriers should be addressed, potentially via bilingual managers or third-party quality assurance services.
**Supplier Reliability:** Conduct thorough due diligence to verify the track record and reliability of potential manufacturers. This includes assessing their financial stability, capacity, and references from previous clients.
**Intellectual Property (IP) Protection:** Enforce strong IP agreements to safeguard your brand assets. This can include non-disclosure agreements (NDAs) and contracts that specify IP rights clearly.
By strategically partnering with Chinese automated packaging manufacturers, businesses can enhance their branding efforts, reduce costs, and improve market responsiveness, ultimately driving growth and customer loyalty.
Tips for Procurement and Considerations when Purchasing automated packaging
When purchasing automated packaging systems, consider the following tips to ensure you make an informed decision:
1. **Assess Your Needs**: Identify the specific requirements of your production line, including volume, packaging types, and sizes. Customize solutions according to your operational demands.
2. **Budgeting**: Determine your budgetary constraints, considering both upfront costs and long-term savings through efficiency and reduced labor costs.
3. **Technology Compatibility**: Ensure the new system is compatible with existing equipment and software. Integration challenges can lead to increased downtime and additional expenses.
4. **Supplier Reputation**: Research suppliers’ track records for reliability and after-sales support. Read reviews, ask for references, and consider their market presence and expertise.
5. **Scalability**: Choose systems that can grow with your business. Modular designs or easily upgradable systems provide flexibility as production needs evolve.
6. **Maintenance and Support**: Evaluate the availability of technical support and spare parts. A supplier with a robust support network can minimize downtime and maintenance costs.
7. **Energy Efficiency**: Opt for energy-efficient models to reduce operational costs and support sustainability goals. Analyze the total cost of ownership, including energy consumption.
8. **User Training**: Ensure that comprehensive training programs are available for staff to maximize the new system’s benefits. Well-trained operators enhance productivity and mitigate risks.
9. **Regulatory Compliance**: Verify that the equipment adheres to industry standards and regulations, ensuring it meets safety and quality requirements.
10. **ROI Analysis**: Conduct a return on investment analysis to justify the expenditure. Calculate potential savings from reduced labor, increased throughput, and minimized waste.
By considering these factors, you can make a well-rounded decision that aligns with your financial goals and enhances operational efficiency.
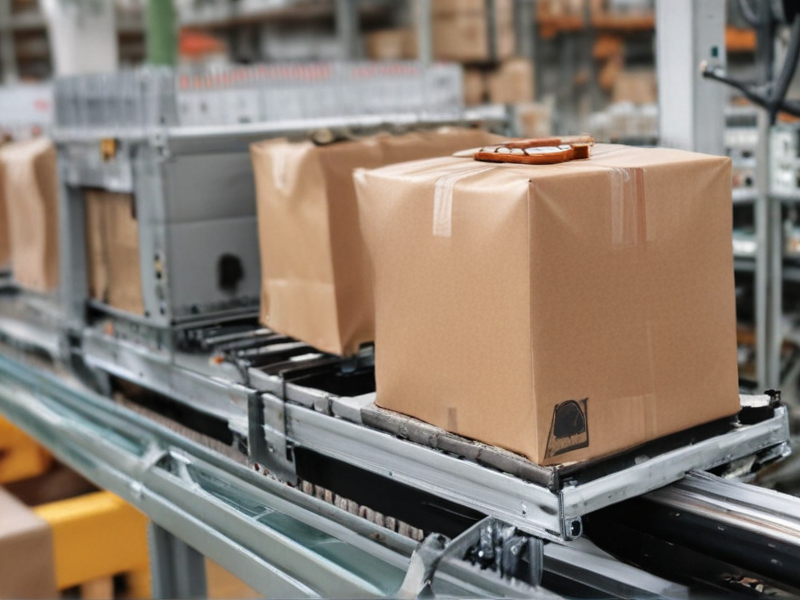
FAQs on Sourcing and Manufacturing automated packaging in China
**FAQs on Sourcing and Manufacturing Automated Packaging in China**
1. **Why source automated packaging from China?**
China is renowned for its cost-effective manufacturing, diverse supplier base, and ability to scale production quickly. This is coupled with advancements in automation technologies, making it an attractive destination for automated packaging solutions.
2. **How to find reliable suppliers?**
Use platforms like Alibaba, Global Sources, and Made-in-China. Industry trade shows, referrals, and third-party sourcing agents can also help identify reputable suppliers. Always cross-check references and verify credentials.
3. **What should I consider in supplier evaluation?**
Assess their manufacturing capabilities, quality control processes, lead times, certifications (like ISO), and past client reviews. Factory audits and sample inspections are also crucial.
4. **What are common pitfalls in China sourcing?**
Quality inconsistencies, communication barriers, and intellectual property risks. Mitigate these by establishing clear specifications, contracts, and using IP protection measures (e.g., patents, trademarks).
5. **How does the cost compare?**
While labor costs may be lower, consider shipping, tariffs, and potential quality control expenses. Total Cost of Ownership (TCO) should be evaluated, not just unit price.
6. **What are the logistics involved?**
Decide on shipping terms (e.g., FOB, CIF), and work with experienced freight forwarders. China’s robust logistics infrastructure facilitates efficient global distribution.
7. **Can I get customized solutions?**
Many manufacturers offer customization for design, size, materials, and technology integration. Ensure detailed communication and prototypes to align with your requirements.
8. **How do I ensure quality control?**
Implement stringent quality control measures such as third-party inspections, in-process checks, and pre-shipment audits. Detailed contracts specifying quality standards are vital.
9. **What are the trends in automated packaging from China?**
Integration of AI, IoT for smarter packaging solutions, use of sustainable materials, and development of high-speed automation technologies.
10. **Is there support for after-sales service?**
Many suppliers offer after-sales support, including spare parts and technical assistance. Ensure this is outlined in your agreement.
By addressing these key points, you can navigate the complexities of sourcing and manufacturing automated packaging in China effectively.