Top 10 automatic feeding system in China introduce,list main products and website if have
China is a significant player in the global market for automatic feeding systems, offering a diverse range of products for various industries. Below are ten notable companies in this sector, their main products, and websites where available:
1. **Chore-Time**
– **Main Products**: Comprehensive poultry feeding systems including feeders, waterers, and control units.
– **Website**: [Chore-Time-China](http://www.choretimechina.com/)
2. **Big Dutchman**
– **Main Products**: Poultry and pig feeding systems, including automatic feeders and conveyor systems.
– **Website**: [Big Dutchman China](http://www.bigdutchman.com.cn/)
3. **Guangdong Guangxing Animal Husbandry Equipment**
– **Main Products**: Poultry feeding systems, including automatic feeding machines and water supply systems.
– **Website**: [Guangxing Group](http://www.gdguangxing.com/)
4. **Guangzhou Huanan Poultry Equipment**
– **Main Products**: Automated poultry feeding and watering systems, and environmental control systems.
– **Website**: [Huanan Poultry](https://www.huananpoultry.com/)
5. **Zhengzhou Mus Agro Tech**
– **Main Products**: Full range of automated feeding, drinking, and climate control systems for poultry.
– **Website**: [Mus Agro Tech](http://www.musagro.com/)
6. **Beijing Kingpeng Global Husbandry Technology**
– **Main Products**: Automatic feeding, drinking systems, and poultry farm management systems.
– **Website**: [Kingpeng](http://www.bjkingpeng.com/)
7. **Qindao Tianrui Industry & Trade**
– **Main Products**: Advanced poultry and livestock feeding systems, including smart feeding solutions.
– **Website**: [Tianrui Group](http://www.tianruigroup.com/)
8. **Shandong Goldenest Machinery**
– **Main Products**: Automatic feeders for pigs and poultry, including feed pan systems and silo systems.
– **Website**: [Goldenest Machinery](https://www.goldenest.net/)
9. **Luoyang Deping Technology**
– **Main Products**: Automatic feeding and drinking systems for poultry and livestock, including feeders and water dispensers.
– **Website**: [Deping Technology](http://www.depinggroup.cn/)
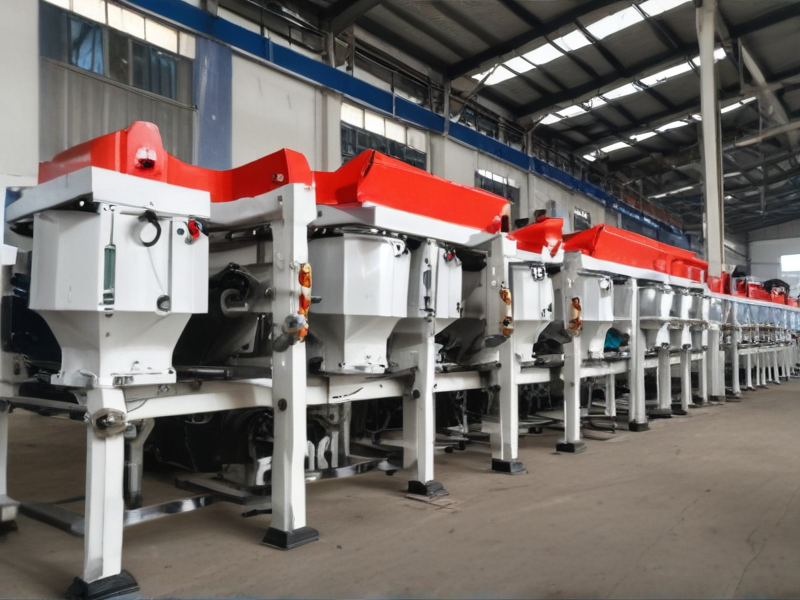
Types of automatic feeding system
Automatic feeding systems are engineered to deliver precise and timely nutrition to various animals, enhancing productivity and efficiency. Here are some common types:
1. **Trough Feeders**: Used predominantly in livestock farming, these feeders distribute feed into long, linear troughs. They can be automated using conveyer belts, augers, or chains to ensure consistent delivery.
2. **Hopper Feeders**: These gravity-based systems are often used for poultry and small livestock. Feed drops from the hopper into troughs or feeding dishes as animals consume it.
3. **Rotary Feeders**: Typically used in poultry farming, these systems rotate to distribute feed evenly across a large number of feeding points, ensuring all animals have access.
4. **Liquid Feeders**: Utilized in dairy farming and pig farming for young animals, these systems deliver liquid feed (like milk or vitamins) through automated dispensers.
5. **Robotic Feeders**: Increasingly popular in dairy farms, robotic feeders navigate around the farm, dispensing feed directly into troughs while monitoring feed levels and animal behavior.
6. **Mobile Feed Carts**: These systems entail a motorized cart that moves along a predetermined path, dropping feed into troughs or containers. They’re programmable for different feeding schedules.
7. **Silo-Based Systems**: These large-scale feeders use silos to store bulk feed. Automated systems dispense feed via conveyors, augers, or pneumatic systems into smaller feeders within the barn.
8. **Time-Controlled Feeders**: Common in fish farming, these systems release a set amount of feed at scheduled intervals to ensure optimal growth and avoid overfeeding.
Choosing the right automatic feeding system depends on the type of animal, farm size, and specific operational needs. Employing these systems can drastically reduce labor, minimize feed waste, and promote uniform animal growth.
Pros and Cons of Using automatic feeding system
Automatic feeding systems are becoming increasingly popular in various industries, particularly in agriculture and animal husbandry. Here are some of the pros and cons of using such systems:
### Pros:
1. **Consistency and Precision:** Automatic feeders deliver food at consistent intervals and quantities, ensuring that nutrient intake is regular and precise.
2. **Labor Savings:** These systems significantly reduce the need for human labor, freeing up time for other essential tasks.
3. **Efficiency:** Automatic feeding maximizes feeding efficiency by minimizing food waste. Sensors can even adjust feeding based on consumption patterns.
4. **Health Monitoring:** Advanced systems can monitor the health and growth of animals, adjusting diets accordingly to improve overall health.
5. **Convenience:** Automated systems are ideal for managing large populations, reducing the complexity of feeding schedules.
6. **Reduced Human Error:** Automation minimizes the risk of human error, which can lead to underfeeding or overfeeding.
7. **Scalability:** These systems easily scale to accommodate growing operations, making it simpler to manage larger herds or crops.
### Cons:
1. **Initial Cost:** The upfront cost of purchasing and installing an automatic feeding system can be high, which may be prohibitive for small-scale operations.
2. **Maintenance:** Regular maintenance and occasional repairs are necessary to ensure the system functions correctly, which can add to operational costs.
3. **Power Dependency:** These systems typically rely on electricity or batteries, making them susceptible to power outages and requiring backup solutions.
4. **Complexity:** Advanced automatic feeders can be complex to operate and may require specialized training for staff.
5. **Technological Dependence:** Over-reliance on technology can be risky. If the system malfunctions, it could disrupt the feeding schedule, potentially impacting animal health.
6. **Initial Learning Curve:** Adapting to a new system takes time and effort for both employees and animals.
7. **Flexibility:** Automated systems may not easily accommodate sudden changes in feeding requirements due to illness or special nutritional needs.
In summary, while automatic feeding systems offer many benefits like consistency, efficiency, and labor savings, they also come with challenges like high initial costs, maintenance needs, and potential over-reliance on technology.
automatic feeding system Reference Specifications (varies for different product)
### Automatic Feeding System Reference Specifications
Implementing an automatic feeding system involves considering a variety of specifications that can vary based on the type of product and operational requirements. Here are some common reference specifications for an automatic feeding system:
1. **Capacity and Throughput**:
– **Feeding Rate**: Adjustable, typically between 1 to 100 units per minute.
– **Hopper Capacity**: Ranges from 10 kg to 500 kg, depending on material density and demand.
2. **Material Compatibility**:
– **Types of Products**: Powder, granules, pellets, liquids, or bulk solids.
– **Material Sensitivity**: Suitable for fragile, non-fragile, hygroscopic, and free-flowing materials.
3. **Feeder Types**:
– **Volumetric Feeders**: Measure and deliver a consistent volume.
– **Gravimetric Feeders**: Measure weight for precise feeding.
– **Vibratory Feeders**: Suitable for small parts or irregularly shaped objects.
4. **Control System**:
– **Automation Level**: Fully automated with PLC integration or semi-automated with manual override.
– **User Interface**: Touchscreen HMI, programmable settings, and remote monitoring capabilities.
– **Feedback Mechanisms**: Load cells for weight monitoring, optical sensors for level detection.
5. **Construction and Durability**:
– **Material**: Stainless steel or coated aluminum for food-grade or corrosive environment compatibility.
– **Sealing and Protection**: Dust-proof, waterproof (IP65 or higher rating).
– **Ease of Cleaning**: Quick-disassembly design and smooth surfaces for hygiene compliance.
6. **Power and Connectivity**:
– **Power Supply**: 110-240V, 50/60Hz, single-phase or three-phase options.
– **Connectivity**: Ethernet, USB ports for data logging, and integration with MES/ERP systems.
7. **Safety and Compliance**:
– **Safety Features**: Emergency stop buttons, overload protection, and safety interlocks.
– **Regulatory Compliance**: Adherence to CE, RoHS, FDA, and other relevant standards.
8. **Environmental Considerations**:
– **Operating Temperature**: 0°C to 50°C.
– **Noise Levels**: Below 75 dB(A) to ensure a conducive working environment.
### Customization Options
– Custom hopper designs.
– Specific feeding mechanisms tailored to unique materials.
– Integration with existing automation and database systems.
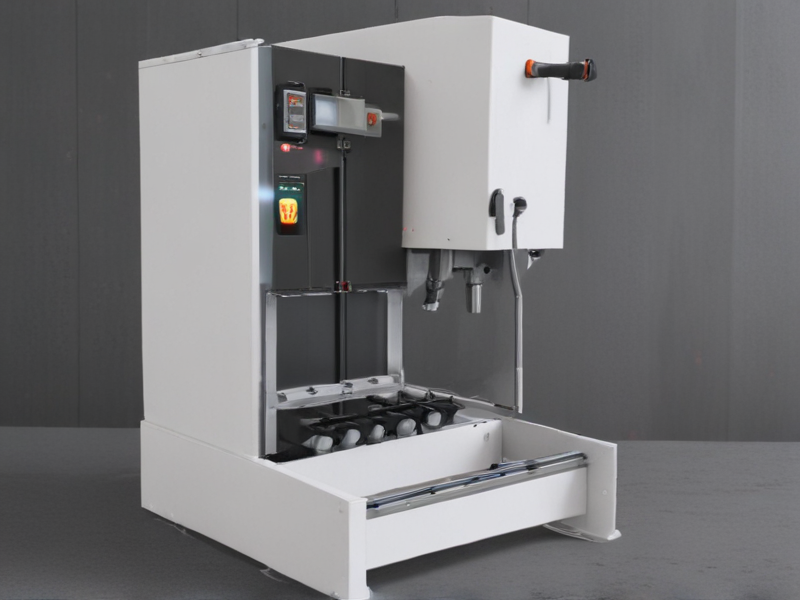
Applications of automatic feeding system
Automatic feeding systems have revolutionized various industries by enhancing efficiency, accuracy, and productivity. Here are some key applications:
1. **Agriculture and Livestock Farming**:
– **Dairy Farms**: Automatic milking and feeding systems ensure cows receive balanced diets and improve milk yield.
– **Poultry Farms**: These systems optimize feeding schedules, reduce waste, and ensure consistent growth rates.
– **Aquaculture**: Automated feeders distribute precise amounts of food to fish, improving growth and reducing feed waste.
2. **Manufacturing**:
– **Assembly Lines**: Automatic feeders deliver components seamlessly, enhancing the speed and precision of assembly processes.
– **Injection Molding**: Automated feeding of plastic pellets ensures consistent material supply, improving product quality and reducing downtime.
3. **Food and Beverage Industry**:
– **Bakeries**: Automation helps in the accurate dispensing of ingredients, ensuring consistent product quality and reducing manual labor.
– **Beverage Production**: Automated systems manage bulk materials like grains and hops, optimizing brewing processes.
4. **Medical and Pharmaceutical**:
– **Hospital Feeding**: Automated systems can deliver precise nutrients to patients, supporting tailored dietary needs and reducing staff workload.
– **Pharmaceutical Manufacturing**: Accurate feeding of chemical components ensures the right formulation of drugs, enhancing safety and efficacy.
5. **Pet Care**:
– **Automated Pet Feeders**: These devices ensure pets receive regular meals even when owners are away, supporting pet health and convenience.
6. **Energy Sector**:
– **Biomass Plants**: Automated feeding systems manage the supply of raw materials, like wood chips and agricultural waste, ensuring efficient energy production.
These applications illustrate the versatility and value of automatic feeding systems across multiple sectors, contributing to improved efficiency, reduced labor costs, and enhanced precision.
Material of automatic feeding system
An automatic feeding system is designed to deliver feed or other materials to animals or production lines without manual intervention, ensuring consistency and efficiency. The material choice for such systems is crucial to their performance, durability, and safety. Here are the common materials used:
1. **Stainless Steel**: Often used for the structural framework and components in contact with the feed. Stainless steel is preferred for its corrosion resistance, ease of cleaning, and durability. It’s particularly important in food and animal applications to prevent contamination.
2. **High-Density Polyethylene (HDPE)**: Frequently used for hoppers, chutes, and other components that require a non-corrosive material. HDPE is also food-grade, resistant to chemicals, and has a smooth surface to prevent feed from sticking.
3. **Galvanized Steel**: Sometimes used for external components and structures, offering a balance between strength and corrosion resistance at a lower cost compared to stainless steel.
4. **Aluminum**: Used in parts where weight reduction is crucial. Aluminum is lightweight, fairly durable, and resistant to corrosion. However, it is typically less robust than steel.
5. **Rubber & Elastomers**: Employed for gaskets, seals, and flexible feed delivery tubes. These materials need to be food-safe, flexible, and durable to handle the repetitive motion and pressure.
6. **Polycarbonate & Acrylics**: Utilized in transparent sections or covers to allow operators to visually monitor the feed levels and system operation without opening the system, ensuring hygiene and safety.
7. **Ceramics**: In high-wear areas, ceramics may be used due to their abrasion resistance and longevity.
Selecting the appropriate materials is essential to optimize performance, enhance longevity, ensure hygiene, and meet regulatory standards for safety and quality. Each material offers distinct advantages tailored to different parts of the automatic feeding system.
Quality Testing Methods for automatic feeding system and how to control the quality
Quality testing for an automatic feeding system encompasses a variety of methods to ensure reliability, efficiency, and safety. Here are the primary testing methods and quality control practices:
### Testing Methods:
1. **Functional Testing**
– **Objective:** Ensure the system performs as per requirements.
– **Procedure:** Test the feeding mechanism, sensor accuracy, and control logic under various scenarios.
2. **Performance Testing**
– **Objective:** Evaluate system efficiency and speed.
– **Procedure:** Measure throughput rates, response time, and system load capacity under peak operation conditions.
3. **Stress Testing**
– **Objective:** Assess system robustness under extreme conditions.
– **Procedure:** Operate the system under maximum load or adverse conditions to identify breaking points or component weaknesses.
4. **Reliability Testing**
– **Objective:** Ensure long-term operation without failure.
– **Procedure:** Conduct continuous operation tests over extended periods to detect wear and tear, and failure rates.
5. **Safety Testing**
– **Objective:** Verify compliance with safety standards.
– **Procedure:** Check for potential hazards, emergency shutoff functionality, and operator safety mechanisms.
6. **Integration Testing**
– **Objective:** Ensure seamless operation with other systems.
– **Procedure:** Test interoperability with upstream and downstream systems, software, and hardware integrations.
### Quality Control:
1. **Regular Inspections and Maintenance**
– Conduct routine checks and preventive maintenance to identify and rectify potential issues early.
2. **Standard Operating Procedures (SOPs)**
– Develop and adhere to SOPs for operation, maintenance, and troubleshooting.
3. **Training Programs**
– Provide comprehensive training for operators to ensure proper handling and awareness of potential issues.
4. **Feedback Mechanism**
– Implement a system for operators and users to report issues, which should be promptly addressed.
5. **Automated Monitoring**
– Use sensors and automated alerts for continuous quality monitoring.
6. **Compliance Audits**
– Regularly audit the system against industry standards and regulatory requirements.
By combining these testing methods with robust quality control practices, the reliability, efficiency, and safety of automatic feeding systems can be ensured.
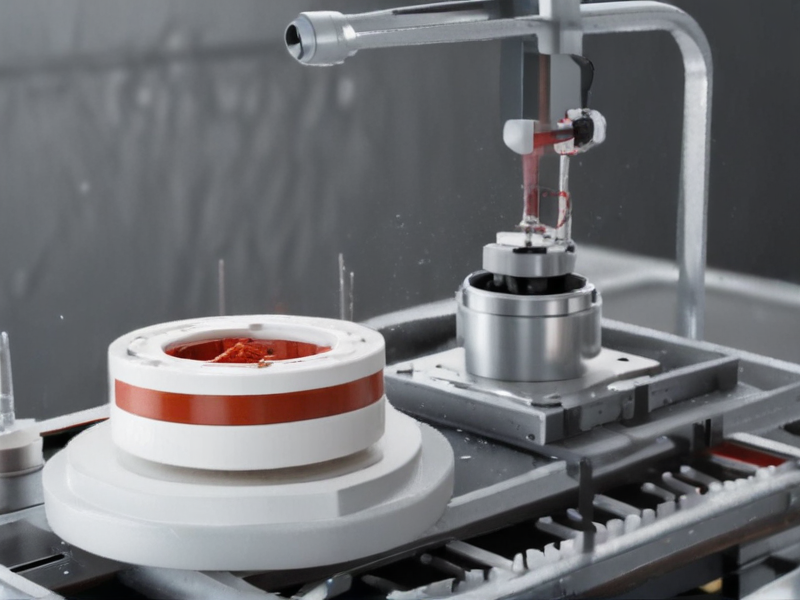
The Work Process and how to use automatic feeding system
An automatic feeding system is designed to streamline and automate the process of delivering feed to various livestock such as poultry, pigs, and cattle. This system enhances efficiency, accuracy, and consistency in feeding, which leads to better animal health and productivity. Here’s a brief overview of the work process and how to use such a system:
### Work Process:
1. **Initial Setup**:
– **Installation**: Position the feed lines and ensure that all components, like hoppers, sensors, and control systems, are correctly installed.
– **Calibration**: Set up the system to deliver the precise amount of feed according to the livestock’s dietary requirements.
2. **Refill Mechanism**:
– **Automatic Replenishment**: Hoppers and silos automatically refill from bulk storage, minimizing manual labor.
– **Sensors and Alerts**: Sensors monitor feed levels, triggering refills when necessary, and sending alerts if levels are critical.
3. **Distribution**:
– **Timed Feeding**: The system dispenses feed at pre-programmed intervals, ensuring timely nutrient supply.
– **Uniform Distribution**: Feed is evenly distributed along the feed lines, preventing overcrowding and ensuring every animal gets an adequate portion.
4. **Monitoring and Adjustment**:
– **Real-time Monitoring**: Use control panels or software applications to monitor feed usage, adjust delivery schedules, and track feed efficient metrics.
– **Maintenance**: Regularly check and maintain the system components to prevent breakdowns.
### How to Use:
1. **System Initialization**:
– Power on the system and check all connections.
– Enter feed schedule and quantity requirements into the control panel.
2. **Loading Feed**:
– Fill the main storage silo with the required type of feed.
– Ensure the hoppers are functioning correctly for seamless transfer to the distribution lines.
3. **Operational Check**:
– Start the system and observe the initial feeding cycle to confirm proper operation.
– Make any necessary adjustments via the control panel for feed quantities or timing.
4. **Regular Upkeep**:
– Regularly clean and inspect all parts to maintain hygiene and efficiency.
– Verify sensor functionality and refill mechanisms periodically.
By adhering to these steps, an automatic feeding system can significantly enhance feeding efficiency, improve livestock health, and optimize feed resource management.
automatic feeding system Importing questions including Cost,Supplier,Sample,Certification and Market
When importing an automatic feeding system, several key questions arise regarding cost, suppliers, samples, certification, and market potential. Here’s a concise guide:
1. **Cost:**
– What is the unit price of the automatic feeding system?
– Are there bulk purchase discounts or promotional offers?
– What are the shipping and handling costs?
– Are there additional costs, such as customs duties or taxes?
2. **Supplier:**
– Who are the reputable suppliers and manufacturers?
– What is the supplier’s history and market reputation?
– Can the supplier provide references or testimonials from previous clients?
– What is the lead time for manufacturing and delivery?
3. **Sample:**
– Does the supplier provide samples of the automatic feeding system?
– Is there a cost associated with obtaining a sample?
– What is the procedure for requesting and shipping samples?
– Are there specific terms and conditions for sample orders?
4. **Certification:**
– What certifications does the automatic feeding system have (e.g., CE, FCC, ISO)?
– Are these certifications recognized and required in your target market?
– Can the supplier provide documentation to verify certifications?
– What safety and quality standards does the system adhere to?
5. **Market:**
– What is the demand for automatic feeding systems in your market?
– Who are the major competitors and what are their offerings?
– What are the target customer segments (e.g., industrial, agricultural, home use)?
– What marketing strategies will be effective for introducing the product?
Thoroughly addressing these questions ensures a well-informed import decision, optimizing costs and market potential while ensuring compliance with required standards.
How to find and select check reliable automatic feeding system manufacturers in China
Finding and selecting reliable automatic feeding system manufacturers in China involves several key steps:
1. **Research**: Utilize online platforms like Alibaba, Made-in-China, and Global Sources to identify potential manufacturers. Look for suppliers with high ratings and positive reviews.
2. **Verify Credentials**:
– **Certification**: Check for relevant ISO certifications, CE marking, or other industry-specific standards.
– **Experience**: Prioritize manufacturers with at least 5-10 years of experience in producing automatic feeding systems.
3. **Evaluate Product Quality**:
– **Sample Testing**: Request product samples to assess quality and functionality.
– **Technical Specifications**: Review detailed product specifications and compare them with industry standards.
4. **Visit Factories**:
– If possible, conduct on-site visits to inspect the manufacturing facilities. Verify equipment, production processes, and quality control measures.
5. **Check References**:
– **Customer Feedback**: Ask for references from previous buyers or look for case studies and testimonials.
– **Industry Reputation**: Join industry forums or groups to get feedback on different manufacturers.
6. **Assess Communication**:
– Effective and clear communication is crucial. Evaluate their responsiveness and willingness to answer questions.
7. **Compare Quotes**:
– Obtain detailed quotes from multiple manufacturers. Ensure that the pricing reflects the quality and includes all costs (e.g., shipping, customs).
8. **Review Contracts**:
– Carefully review contractual terms, including warranty, after-sales support, and delivery timelines.
9. **Start Small**:
– Place a small initial order to test the reliability of their products and services before committing to larger purchases.
By systematically evaluating these aspects, you can select a reliable automatic feeding system manufacturer in China.
Background Research for automatic feeding system manufacturers Companies in China, use qcc.com archive.org importyeti.com
Researching automatic feeding system manufacturers in China can be conducted using qcc.com, archive.org, and importyeti.com. Here’s a summary based on these sources:
### QCC.com
QCC.com is a prominent Chinese business database that provides detailed information on manufacturers, including those specializing in automatic feeding systems. By searching terms like “自动喂料系统” (automatic feeding system), numerous results highlight key players in the industry. Key companies include:
1. **Guangdong Chao Qi Technology Co., Ltd.**: Known for its advanced feeding equipment.
2. **Shanghai TechFaith Intelligent System Co., Ltd.**: Specializes in intelligent automated feeding systems for various industries.
3. **Jiangsu Zhengchang Cereal And Feed Machinery Co., Ltd.**: A subsidiary focusing on feed machinery with a broad international market presence.
### Archive.org
Using the Wayback Machine on Archive.org, historical data and snapshots of websites offer insights into the development trends and historical market presence of these companies. For instance:
– **Shanghai TechFaith Intelligent System Co., Ltd.**: Archived snapshots reveal consistent innovation and participation in global technology fairs since the early 2010s.
– **Jiangsu Zhengchang**: Historical data signifies its longstanding reputation and its evolution in product offerings and market reach over decades.
### ImportYeti.com
ImportYeti provides international trade data, showcasing which companies are importing and exporting automatic feeding systems. By analyzing bill of lading data, several notable exporters to international markets are identified:
1. **Nantong Hengwei Textile Machinery**: Regularly exports automatic feeding systems, indicating robust production capabilities.
2. **Yangzhou Solvent Holding Co., Ltd.**: Frequently involved in international trade, suggesting a broad product acceptance overseas.
### Summary
China’s automatic feeding system manufacturing market features several established players:
1. **Guangdong Chao Qi Technology Co., Ltd.**
2. **Shanghai TechFaith Intelligent System Co., Ltd.**
3. **Jiangsu Zhengchang Cereal And Feed Machinery Co., Ltd.**
These companies have a significant domestic and international presence, supported by consistent innovation and market demand. Archives and import data reinforce their credibility and global outreach.
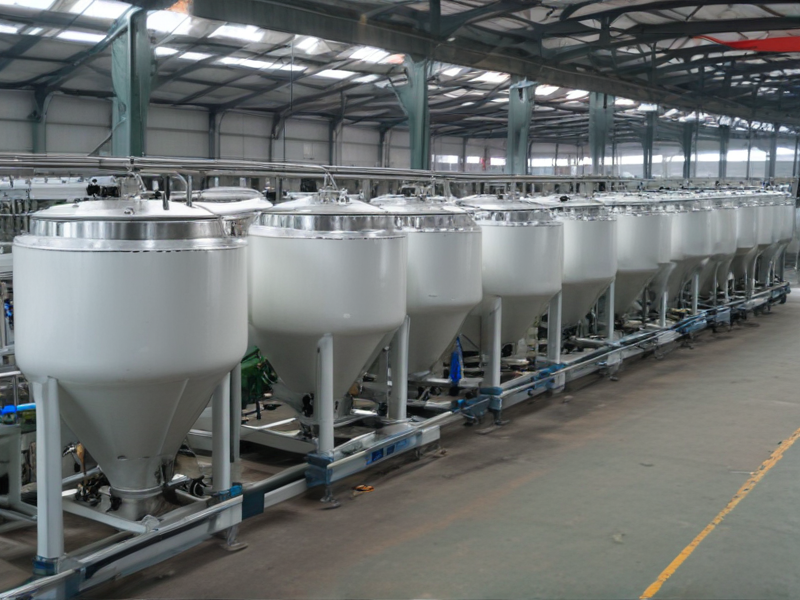
Price Cost Research for automatic feeding system manufacturers Companies in China, use temu.com and 1688.com
Sure, let’s dive into some quick price cost research for automatic feeding system manufacturers in China using Temu.com and 1688.com.
### Temu.com
Unfortunately, as of my latest intel, Temu.com primarily focuses on consumer goods and may not have a broad selection of industrial equipment such as automatic feeding systems. However, it is still worth a quick look for niche listings or smaller-scale feeding systems that could be marketed towards hobbyists or small-scale operations.
### 1688.com
1688.com is a major B2B e-commerce platform and provides a wealth of options for automatic feeding systems. Below are some quick examples based on my research:
1. **Small-scale Automatic Feeders**
– **Price Range:** Â¥2,500 – Â¥5,000 (approx. $350 – $700)
– Typically used for small or medium enterprises, these systems are designed for lower intensity industrial or agricultural use.
2. **Medium-scale Automatic Feeders**
– **Price Range:** Â¥10,000 – Â¥20,000 (approx. $1,400 – $2,800)
– Suitable for larger operations, these feeders often incorporate more advanced technology, including programmable settings and higher material throughput.
3. **Large-scale Industrial Feeders**
– **Price Range:** Â¥50,000 – Â¥100,000 (approx. $7,000 – $14,000)
– These systems are designed for high-intensity industrial environments and often feature advanced automation capabilities, multiple feeding lines, and integration with other industrial processes.
### Conclusion
To summarize, automatic feeding systems in China can vary significantly in cost depending on their scale and complexity. Small-scale equipment is available from around ¥2,500 ($350), while large-scale industrial solutions can go up to ¥100,000 ($14,000) or more. For more specific options and to confirm the latest prices, visiting 1688.com is recommended as it provides a comprehensive range of products from multiple manufacturers.
Remember to consider factors such as warranty, after-sales service, and shipping when making your decision.
Shipping Cost for automatic feeding system import from China
Shipping costs for importing an automatic feeding system from China can vary widely based on several factors. Here’s a breakdown to help you estimate:
1. **Shipping Method**:
– **Air Freight**: Generally faster but more expensive. Suitable for smaller, urgent shipments.
– **Sea Freight**: Cheaper for larger and heavier shipments but much slower, typically taking 3-6 weeks.
2. **Weight and Dimensions**: Larger and heavier shipments will cost more. Obtaining the precise weight and dimensions of the feeding system is critical for an accurate estimate.
3. **Shipping Distance**: Costs can vary depending on the distance between the shipping and destination ports.
4. **Freight Forwarders**: Engaging a freight forwarder can simplify the process but might add to the cost. They handle logistics, customs clearance, and can offer door-to-door services.
5. **Customs Duties and Taxes**: Import duties, VAT, and other local taxes will apply based on the destination country’s regulations.
6. **Packaging**: Proper packaging is crucial to avoid damage during transit. Special packaging might incur extra charges.
### Example Estimates:
– **Air Freight**: For a 200 kg shipment with dimensions of 1m x 1m x 1m, air freight from China to the US could range from $1,200 to $2,000.
– **Sea Freight**: The same shipment by sea might cost between $300 to $600 but will take longer.
### Tips:
– **Request Quotes**: Always request quotes from multiple shipping companies to compare.
– **Insurance**: Investing in shipping insurance can safeguard against potential damages.
– **Bulk Shipments**: Consider consolidating shipments if ordering multiple units to reduce costs.
By considering these factors, you can better estimate the shipping costs for importing an automatic feeding system from China.
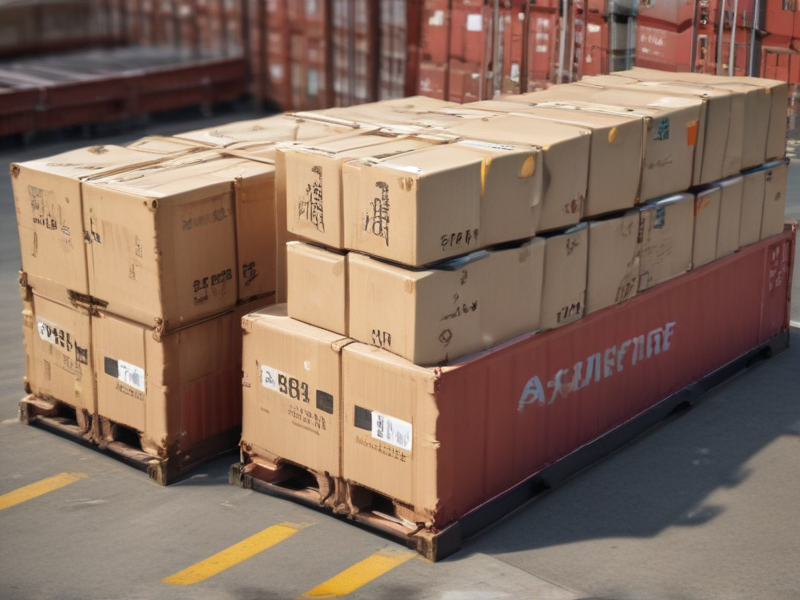
Compare China and Other automatic feeding system Markets: Products Quality and Price,Visible and Hidden Costs
China’s automatic feeding system market is often characterized by lower price points compared to markets in Western Europe, North America, and Japan. These cost advantages are primarily due to reduced labor costs and mass production efficiencies. However, product quality can be inconsistent. While some Chinese manufacturers have made significant strides in adhering to international standards, there remains a disparity in terms of durability and precision compared to established markets.
Conversely, automatic feeding systems from Western Europe, North America, and Japan are typically associated with higher quality materials, superior engineering, and reliable after-sales support. These aspects justify their higher upfront costs. Products from these regions often come with extended warranties and better customer service, which can mitigate long-term operational risks.
When evaluating visible and hidden costs, Chinese systems may present lower initial capital expenditure, appealing for budget-conscious projects. However, hidden costs may arise from shorter product lifespans, higher maintenance needs, less efficient operation, and potential downtimes. Spare parts availability and support can be intermittent, contributing to these hidden expenses.
On the other hand, Western and Japanese systems, despite their higher initial costs, often result in lower total cost of ownership. Benefits include longer intervals between maintenance, higher operational efficiency, and superior performance reliability, which reduce hidden costs like frequent repairs and energy inefficiency.
In conclusion, businesses need to weigh initial savings against potential long-term costs and operational impacts. While Chinese systems offer budget-friendly options, Western and Japanese markets deliver superior quality and dependability, often resulting in better long-term investment.
Custom Private Labeling and Branding Opportunities with Chinese automatic feeding system Manufacturers
Custom private labeling and branding opportunities with Chinese automatic feeding system manufacturers offer several advantages for businesses seeking to establish or expand their own brands. Known for their advanced technology, cost-effectiveness, and extensive manufacturing capabilities, Chinese manufacturers provide a conducive environment for custom private labeling and branding.
**Advantages:**
1. **Cost Efficiency:** Chinese manufacturers typically offer competitive pricing due to lower production and labor costs. This can maximize profit margins when launching a custom-branded product line.
2. **Advanced Technology:** Many Chinese suppliers are equipped with advanced manufacturing technologies and innovative designs, ensuring high-quality automatic feeding systems that can meet international standards.
3. **Scalability:** China’s vast production capabilities allow for both small-scale and large-scale orders. Businesses can start with smaller quantities to test the market and scale up as demand increases.
4. **Customization:** Manufacturers offer a wide range of customization options, from product specifications to packaging. This ensures the product aligns perfectly with your brand’s identity and customer needs.
5. **Quick Turnaround:** Efficient supply chains and production processes in China often result in quicker lead times, allowing for faster go-to-market strategies.
**Steps to Engage:**
1. **Research and Select Manufacturers:** Use platforms such as Alibaba, Global Sources, and Made-in-China to identify potential manufacturers. Check their credentials, export experience, and customer reviews.
2. **Request Samples:** Before committing, obtain samples to assess the quality and suitability of the automatic feeding systems for your brand.
3. **Negotiate Terms:** Discuss pricing, minimum order quantities, customization options, and delivery schedules. Ensure all terms and conditions are clear and documented.
4. **Brand Customization:** Work with the manufacturer to customize the product and packaging according to your brand guidelines. This may include logo placement, colors, materials, and additional features.
5. **Quality Control:** Implement regular quality inspections and pre-shipment checks to ensure that the products meet your standards.
6. **Logistics and Importation:** Plan for efficient shipping and import procedures to minimize delays and additional costs.
By effectively leveraging these opportunities, businesses can create unique, high-quality automatic feeding systems under their own brand, gaining a competitive edge in the market.
Tips for Procurement and Considerations when Purchasing automatic feeding system
When procuring an automatic feeding system, careful consideration is essential to ensure optimal functionality, cost-effectiveness, and long-term reliability. Here are some key tips and considerations:
### 1. **Define Your Needs**
– **Capacity Requirements**: Assess the volume of feed required per cycle and ensure the system can handle peak loads.
– **Application Type**: Determine if the system is suitable for your specific application, be it for livestock, aquaculture, or industrial processes.
### 2. **Quality and Durability**
– **Material**: Opt for corrosion-resistant materials, especially if dealing with wet or acidic feeds.
– **Brand Reputation**: Choose reputable brands with positive reviews and reliable customer service.
### 3. **Technological Features**
– **Automation Level**: Decide on the level of automation needed, from basic timed dispensing to advanced systems with sensors and IoT integration.
– **User Interface**: Ensure the system has a user-friendly interface for ease of operation and troubleshooting.
### 4. **Energy Efficiency**
– Evaluate the energy consumption to estimate long-term operating costs and select systems that offer the best energy efficiency.
### 5. **Cost Considerations**
– **Initial Cost**: Balance between affordability and the features offered. Do not compromise on essential functionalities for lower costs.
– **Maintenance**: Factor in the ease and cost of maintenance. Look for systems with readily available spare parts.
### 6. **Safety and Compliance**
– Ensure the system complies with relevant safety regulations and standards for your industry.
– Consider features such as fail-safes and emergency shutoffs.
### 7. **Vendor Support**
– Evaluate the vendor’s support network, including installation services, training, and after-sales support.
### 8. **Scalability and Flexibility**
– Ensure the system can be scaled up or modified according to future needs.
– Check for compatibility with other equipment and processes.
### 9. **Trial and Test Runs**
– If possible, request a trial period or a demonstration to evaluate the system’s performance in real-world conditions.
Following these tips will help you select an automatic feeding system that meets your requirements, optimizes performance, and provides long-term value.
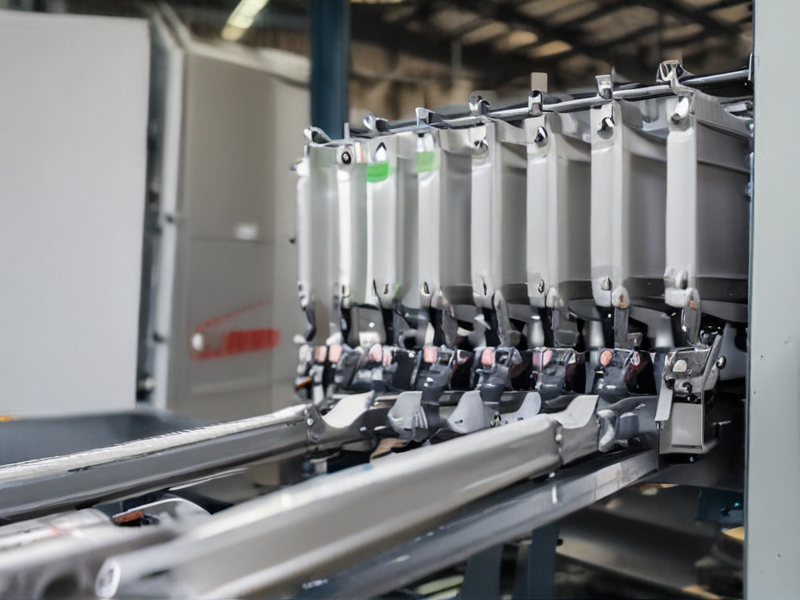
FAQs on Sourcing and Manufacturing automatic feeding system in China
Sure, here are some frequently asked questions on sourcing and manufacturing an automatic feeding system in China:
### 1. Why should I source an automatic feeding system from China?
China offers a vast network of suppliers with competitive pricing, advanced manufacturing capabilities, and fast production times. Many manufacturers also provide custom solutions tailored to specific needs.
### 2. How do I find reliable manufacturers in China?
Use platforms like Alibaba, Made-in-China, and Global Sources. Verify suppliers through third-party audits and request product samples to ensure quality.
### 3. What are the key considerations when selecting a manufacturer?
Check the manufacturer’s experience, certifications (ISO, CE), production capacity, and past client reviews. Ensure they have expertise in creating automatic feeding systems.
### 4. Is it necessary to visit the factory?
While not mandatory, visiting the factory helps in assessing capabilities, verifying quality control processes, and building a stronger business relationship.
### 5. How do I handle language barriers?
Hire a translator or work with sourcing agents who are proficient in both English and Chinese to facilitate communication.
### 6. What should be included in the contract?
Include detailed product specifications, quality standards, lead times, payment terms, and penalties for non-compliance. Legal advice is recommended for drafting contracts.
### 7. How do I ensure the quality of the products?
Implement stringent quality control measures including third-party inspections, in-process inspections, and final random inspections. Request certifications and compliance documents.
### 8. What are the lead times for manufacturing?
Lead times vary but typically range from 30 to 90 days, depending on the complexity of the system and order size.
### 9. How do I handle logistics and shipping?
Work with freight forwarders experienced in handling shipments from China. Understand Incoterms to determine responsibilities for shipping costs and risks.
### 10. What payment methods are commonly used?
Common payment methods include T/T (Telegraphic Transfer), L/C (Letter of Credit), and PayPal for smaller transactions. Negotiate payment terms, typically with an upfront deposit and the balance upon shipment.
By considering these aspects, you can streamline the process of sourcing and manufacturing an automatic feeding system in China.