Top 10 automated packaging solution in China introduce,list main products and website if have
Certainly! Here are the top 10 automated packaging solution providers in China, along with their main products and websites:
1. **Shanghai TO-U Packaging Machinery Co., Ltd.**
– **Main Products:** Automatic filling machines, capping machines, labeling machines, and packaging lines.
– **Website:** [to-u-pack.com](http://www.to-u-pack.com)
2. **Newamstar Packaging Machinery Co., Ltd.**
– **Main Products:** Beverage filling machines, blow molding machines, and complete packaging solutions.
– **Website:** [newamstar.com](http://www.newamstar.com)
3. **Jinan Dongtai Machinery Manufacturing Co., Ltd.**
– **Main Products:** Filling machines, capping machines, labeling machines, and packing machines.
– **Website:** [dongtaipack.com](http://www.dongtaipack.com)
4. **Guangzhou Keno Machinery Co., Ltd.**
– **Main Products:** Vacuum packing machines, automatic filling machines, coding machines, and sealing machines.
– **Website:** [kenomachine.com](http://www.kenomachine.com)
5. **Zhejiang Dingye Machinery Co., Ltd.**
– **Main Products:** Sealing machines, vacuum packaging machines, filling machines, and capping machines.
– **Website:** [dingyepack.com](http://www.dingyepack.com)
6. **Hualian Machinery Group Co., Ltd.**
– **Main Products:** Sealers, shrink wrapping machines, vacuum packaging machines, and strapping machines.
– **Website:** [hualianpack.com](http://www.hualianpack.com)
7. **Shanghai Haoqi Machinery Equipment Co., Ltd.**
– **Main Products:** Aerosol filling machines, labeling machines, and packaging solutions.
– **Website:** [haoqi-pack.com](http://www.haoqi-pack.com)
8. **Wenzhou Ouhai International Trade Co., Ltd.**
– **Main Products:** Filling machines, packing machines, and complete beverage production lines.
– **Website:** [ouhai.cn](http://www.ouhai.cn)
9. **Guangzhou Full Harvest Industries Co., Ltd.**
– **Main Products:** Packing machines, sealing machines, filling machines, and labeling machines.
– **Website:** [fullharvest.net](http://www.fullharvest.net)
10. **Ruian Uteko Machinery Co., Ltd.**
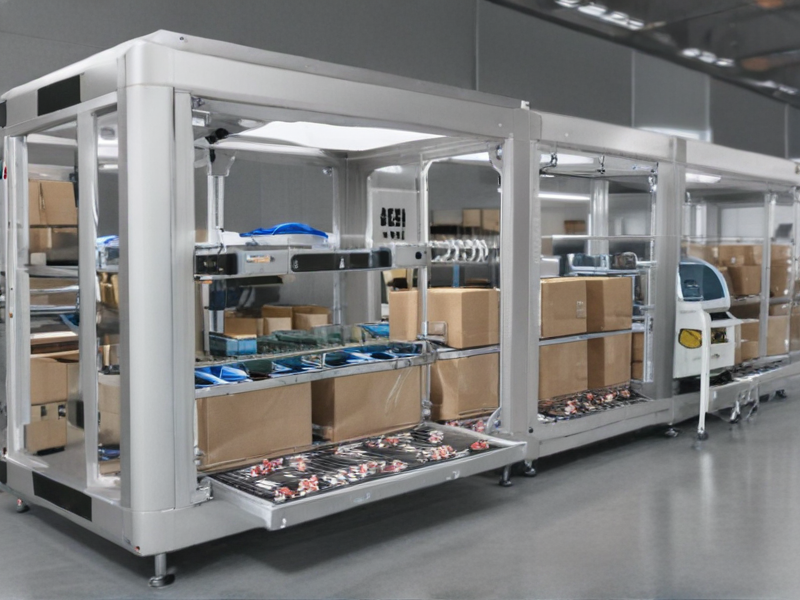
Types of automated packaging solution
Automated packaging solutions streamline the process of preparing products for shipment and sale. Here are the main types:
1. **Form, Fill, and Seal Machines (FFS)**:
– **Horizontal FFS**: Commonly used for solid products like snacks and baked goods. The machine forms a pouch from a roll of film, fills it with the product, and seals it.
– **Vertical FFS**: Ideal for liquids, powders, and granular products. It functions similarly to horizontal FFS but operates vertically.
2. **Labeling Machines**:
– **Pressure-Sensitive Labelers**: These apply pre-cut labels directly to products or packages using adhesive force.
– **Shrink-Sleeve Labelers**: Useful for labeling oddly shaped containers. It applies a plastic sleeve that shrinks to fit when heated.
3. **Case Packers**:
– **Wrap-Around Case Packers**: Suitable for high-speed operations. The machine wraps a carton around the product and seals it.
– **Drop Packers**: This method drops products from the top into open cartons or trays.
4. **Palletizers**:
– **Robotic Palletizers**: Use robotic arms to place products on pallets in a systematic way. They’re flexible and can handle various product types.
– **Conventional Palletizers**: Usually for high-speed, single-product lines, stacking products in predetermined patterns.
5. **Cartoning Machines**:
– **Horizontal Cartoners**: Best for placing products like tubes, jars, and bottles into cartons.
– **Vertical Cartoners**: Ideal for products that require vertical insertion into cartons, such as bags or pouches.
6. **Conveying Systems**:
– **Belt Conveyors**: Simple and versatile, used to transport items between packaging stages.
– **Roller Conveyors**: Suitable for solid, heavy items, minimizing contact by using rollers.
7. **Stretch Wrappers**:
– These machines wrap a stretchable plastic film around products, primarily to secure them to pallets for transportation.
8. **Shrink Wrappers**:
– These apply a plastic film around the product and then heat it, causing the film to shrink and tightly conform to the product.
Each system offers unique benefits tailored to specific products and production environments, ensuring efficiency, accuracy, and cost-effectiveness in packaging operations.
Pros and Cons of Using automated packaging solution
**Pros:**
1. **Efficiency and Speed:** Automated packaging systems can process products much faster than manual labor, significantly increasing throughput and reducing bottlenecks.
2. **Consistency and Precision:** Machines deliver uniform packaging, reducing errors and ensuring consistent quality, which enhances brand reliability.
3. **Cost Savings:** Over time, automation can lower labor costs and minimize wastage of materials due to precise usage and fewer errors.
4. **Scalability:** Automated systems can be scaled up or down to meet demand without a proportionate increase in labor costs.
5. **Safety:** Automation reduces the risk of injuries associated with repetitive and strenuous manual packaging tasks.
**Cons:**
1. **High Initial Investment:** The upfront cost of purchasing and installing automated packaging equipment can be substantial, which might be a barrier for small businesses.
2. **Maintenance and Downtime:** Automated systems require regular maintenance and can experience breakdowns, leading to potentially costly downtime.
3. **Flexibility Constraints:** Automation may not be suitable for complex or varied packaging needs where customization is frequently required.
4. **Job Displacement:** Implementing automation can result in job losses or require workers to be retrained for new roles, which can impact employee morale.
5. **Complex Integration:** Integrating automated packaging solutions with existing systems and processes can be complex and may involve significant time and technical challenges.
In summary, while automated packaging solutions offer significant efficiency, cost, and safety benefits, they also come with high initial costs, potential downtime, and integration complexities. Businesses must weigh these factors in light of their specific needs and capabilities.
automated packaging solution Reference Specifications (varies for different product)
An automated packaging solution streamlines and optimizes the packaging process. Below are general reference specifications that can be customized according to different product requirements:
1. **Packaging Capacity**
– Throughput: Up to 60 packages per minute
– Compatible Products: Varying dimensions and weights (e.g., 0.1kg – 5kg)
2. **Product Handling**
– Conveyor System: Adjustable speed, directional capabilities
– Sensor Integration: Barcode scanners, weight sensors, and 3D vision systems
3. **Packaging Compatibility**
– Materials: Corrugated boxes, pouches, shrink wrap, polybags
– Dimensions: Variable width, height, and length accommodation
4. **Robotic Integration**
– Pick-and-Place Robots: For precise handling
– Palletizing Robots: For stacking products on pallets
5. **Sealing and Labeling**
– Sealing Types: Heat sealing, adhesive tape, ultrasonic welding
– Labeling: Automated label printers and applicators, real-time printing
6. **Quality Control**
– Inspection Systems: X-ray, metal detection, visual inspection
– Rejection Mechanism: Automatic ejection of defective packages
7. **Software Integration**
– ERP/Inventory Management Compatibility: Seamless integration with existing systems
– User Interface: Touchscreen HMIs, remote monitoring, and diagnostics
8. **Footprint and Mobility**
– Compact Design: Minimal floor space
– Mobility: Casters for easy relocation
9. **Energy Efficiency**
– Power Consumption: Low-energy motors and smart energy-saving modes
– Environmental Controls: Temperature and humidity regulation
10. **Safety Features**
– Enclosures: Guarding and interlocks
– Emergency Stop: Strategically placed for quick access
11. **Maintenance and Downtime**
– Predictive Maintenance: Real-time monitoring of machine health
– Quick Changeover: Tool-less adjustments for different product runs
Adapting these specifications ensures that the automated packaging solution meets the diverse needs of various product lines, enhancing efficiency, and maintaining high quality.
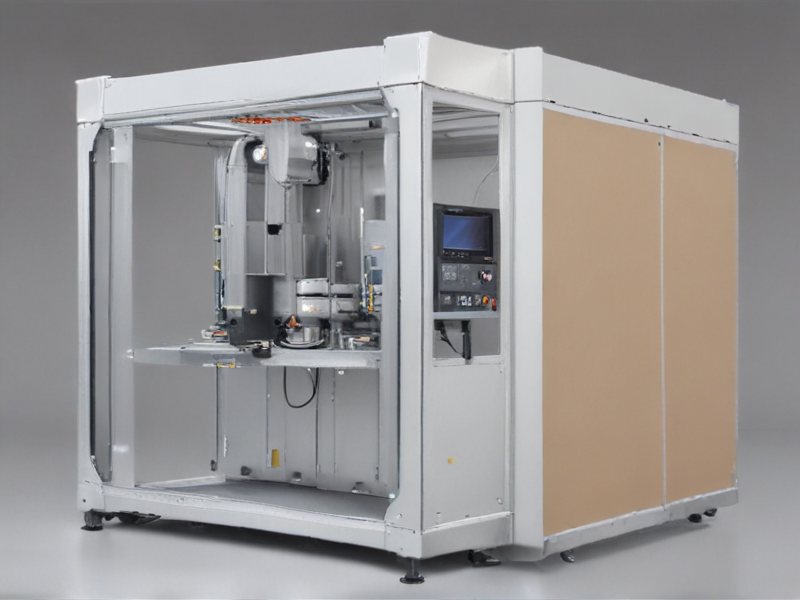
Applications of automated packaging solution
Automated packaging solutions are revolutionizing various industries by enhancing efficiency, reducing costs, and improving consistency. Below are key applications across different sectors:
1. **E-commerce and Retail**: Automated packaging systems streamline the packing process, allowing businesses to handle a larger volume of orders with greater speed and accuracy. This is critical in meeting customer expectations for swift deliveries.
2. **Food and Beverage**: These systems ensure hygienic, tamper-proof packaging, complying with stringent safety standards. Automated processes can manage various tasks from filling and sealing to labeling and palletizing, which helps in maintaining product freshness and quality.
3. **Consumer Goods**: For sectors such as cosmetics and household products, automated packaging enhances presentation and can manage intricate packaging requirements. High-speed machinery ensures products are consistently well-packaged, improving shelf appeal and customer satisfaction.
4. **Pharmaceuticals**: Precision and safety are paramount in this industry. Automated packaging solutions help in maintaining stringent compliance with regulatory standards by ensuring accurate dosage and secure, tamper-evident packaging.
5. **Automotive Parts**: These systems aid in the efficient, protective packaging of automotive components, reducing damage during transit and ensuring parts arrive in perfect condition. Automated systems can handle heavy loads and bulky items more effectively than manual processes.
6. **Electronics**: Precision is crucial in packaging delicate electronic components. Automated packaging solutions minimize human handling, reducing the risk of damage and static electricity, thereby ensuring product integrity.
7. **Warehousing and Logistics**: In this sector, automated packaging ensures rapid, error-free handling, and labeling of products, optimizing inventory management, and facilitating smoother logistics operations.
In summary, automated packaging solutions are integral to modern industrial operations, enhancing productivity, consistency, and safety across various applications.
Material of automated packaging solution
The choice of materials for an automated packaging solution is critical for ensuring efficiency, durability, and cost-effectiveness. Typically, materials like stainless steel, aluminum, and high-grade plastics are preferred for their unique properties.
1. **Stainless Steel:**
– **Durability:** Stainless steel is robust and resistant to corrosion, making it ideal for components exposed to various environmental conditions.
– **Hygiene:** Widely used in food and pharmaceutical industries due to its easy-to-clean surface.
– **Structural Integrity:** Its high tensile strength ensures the longevity of machines even with high usage rates.
2. **Aluminum:**
– **Lightweight:** Aluminum is significantly lighter than stainless steel, reducing the overall weight of machinery and contributing to energy efficiency.
– **Corrosion Resistance:** While not as formidable as stainless steel, aluminum still offers good resistance to corrosion.
– **Conductivity:** Useful in applications requiring thermal and electrical conductivity.
3. **High-Grade Plastics (e.g., ABS, Polycarbonate, PEEK):**
– **Versatility:** Plastics can be molded into complex shapes, offering versatility in design and integration.
– **Cost-Effective:** Generally more affordable than metals, suitable for non-critical parts to reduce production costs.
– **Chemical Resistance:** Many high-grade plastics are resistant to a wide range of chemicals, which is beneficial in certain packaging environments.
4. **Composites:**
– **Strength-to-Weight Ratio:** Composite materials like carbon fiber offer excellent strength while being lightweight, optimizing performance and energy consumption.
– **Customization:** They can be engineered to meet specific mechanical properties and resistance requirements.
In summary, the material choice for an automated packaging solution is typically a mix of stainless steel, aluminum, high-grade plastics, and sometimes composites. Each material is selected based on its specific properties to ensure the machinery is durable, efficient, and cost-effective.
Quality Testing Methods for automated packaging solution and how to control the quality
Ensuring quality in an automated packaging solution involves a blend of advanced testing methods and stringent control mechanisms. Here’s a concise overview:
### Testing Methods:
1. **Automated Visual Inspection:**
– **Cameras and Sensors:** Monitor for defects, such as incorrect labels, misalignment, and damages.
– **Image Processing Software:** Analyzes images to detect inconsistencies and ensure product integrity.
2. **X-ray and Metal Detection:**
– **X-ray Systems:** Inspect for foreign objects and verify proper fill levels.
– **Metal Detectors:** Ensure no metallic contaminants are present in the packaging.
3. **Weight Check (Checkweighers):**
– Ensures each package meets specified weight standards, detecting any under-filled or over-filled products.
4. **Leak Testing:**
– **Pressure Decay and Vacuum Testing:** Detects leaks in sealed packages to ensure product freshness and integrity.
5. **Barcode and RFID Verification:**
– Scans barcodes and RFID tags for accuracy in labeling and traceability.
### Quality Control Measures:
1. **Standard Operating Procedures (SOPs):**
– Develop and implement detailed SOPs to ensure consistency in packaging operations.
2. **Regular Calibration:**
– Routine calibration of sensors, cameras, and other testing equipment to maintain accuracy and reliability.
3. **Training and Skill Development:**
– Ongoing training for personnel to operate and maintain automated systems efficiently and respond to any anomalies.
4. **Data Logging and Analysis:**
– Use automated systems to log data on packaging performance, identify trends, and address issues proactively.
5. **Preventive Maintenance:**
– Scheduled maintenance of machinery to prevent breakdowns and ensure consistent quality.
6. **Feedback Loop:**
– Immediate rectification of detected issues and integration of feedback into process improvements.
By integrating these testing methods and control measures, you can significantly enhance the reliability and quality of your automated packaging solution.
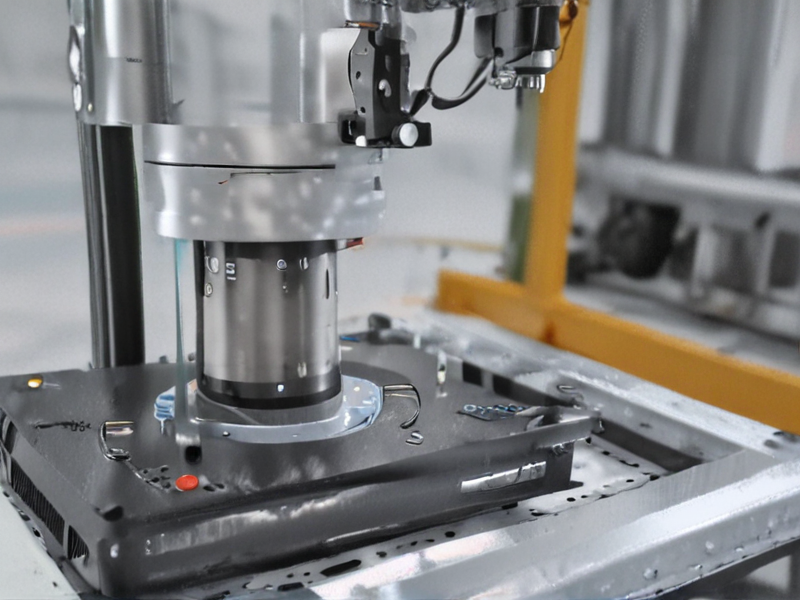
The Work Process and how to use automated packaging solution
Automated packaging solutions streamline the packing process, increase efficiency, and reduce human error. Here’s a concise look at the work process and how to effectively use an automated packaging solution:
### Work Process:
1. **Input and Product Orientation**: Products enter the system via conveyors. Automated mechanisms ensure items are correctly oriented for packaging.
2. **Product Measurement and Sorting**: Sensors measure the size, weight, and other parameters. Sorting stations direct items based on these criteria.
3. **Primary Packaging**: Items are placed in their initial packaging (e.g., wrapping, bags, boxes). Machines like flow wrappers and form-fill-seal equipment handle this step.
4. **Secondary Packaging**: Primary packaged items are grouped for easier handling (e.g., bundling or placing into cartons). Carton erecting and packing machines automate this.
5. **Labeling and Marking**: Automated systems print and apply labels or barcodes for tracking and compliance.
6. **Quality Control**: Vision systems and sensors confirm packaging integrity and label accuracy. Items failing checks are automatically rejected.
7. **Palletizing**: Final packed items are stacked onto pallets using robotic arms or palletizing machines. Patterns are optimized for stability.
8. **Wrapping and Strapping**: Pallets are wrapped in plastic film and/or strapped to prevent shifting during transport.
### Using Automated Packaging Solutions:
1. **Assess Needs**: Evaluate product types, packaging requirements, and production volume to choose the appropriate system.
2. **Select Equipment**: Invest in machinery tailored to your needs—ranging from simple conveyors to complex robotic arms.
3. **Integration**: Ensure seamless integration with existing systems. This includes connecting with your ERP (Enterprise Resource Planning) software for synchronized workflow.
4. **Training**: Train staff on operating and maintaining the new equipment to maximize efficiency and minimize downtime.
5. **Maintenance**: Implement a regular maintenance schedule to ensure optimal performance and prolonged equipment lifespan.
6. **Monitor and Optimize**: Continuously monitor performance data for bottlenecks or inefficiencies. Adjust settings or upgrade components as needed.
By following these steps, businesses can vastly improve their packaging operations, resulting in increased productivity and consistency.
automated packaging solution Importing questions including Cost,Supplier,Sample,Certification and Market
When exploring automated packaging solutions, it’s essential to consider several key aspects to ensure you make an informed decision. Here are some critical questions to address:
1. **Cost**:
– What is the initial cost of the automated packaging system?
– Are there any recurring costs (maintenance, software updates)?
– What are the potential cost savings or ROI compared to manual packaging?
– Are there financing or leasing options available?
2. **Supplier**:
– Who are the leading suppliers of automated packaging solutions?
– What is the supplier’s reputation in the industry?
– Can they provide references or case studies from similar projects?
– What kind of technical support and training do they offer post-purchase?
3. **Sample**:
– Is it possible to receive a sample or demo of the automated packaging system?
– Can the supplier provide a trial period to test the equipment’s performance with your products?
– Are there any costs associated with the sample or demo?
4. **Certification**:
– Does the automated packaging system have relevant industry certifications (e.g., ISO, CE)?
– Is the equipment compliant with local and international safety standards?
– Are there any environmental certifications (e.g., energy efficiency, recyclability)?
5. **Market**:
– How well-suited is the automated packaging solution to your target market?
– What are the latest market trends in automated packaging?
– How will the new system impact your market competitiveness?
– Are your competitors using similar automated systems?
By addressing these questions, you can effectively assess the overall value and fit of an automated packaging solution for your business needs. This structured approach helps ensure you invest in a system that meets operational requirements and supports long-term growth objectives.
How to find and select check reliable automated packaging solution manufacturers in China
Finding and selecting reliable automated packaging solution manufacturers in China involves a systematic approach:
1. **Research and Identify**:
– **Online Directories**: Platforms like Alibaba, Made-in-China, and Global Sources list numerous manufacturers with detailed profiles.
– **Industry Forums**: Engage in forums like Reddit and specialized packaging technology communities for recommendations.
– **Trade Shows**: Events such as the China International Packaging Exhibition provide direct access to manufacturers.
2. **Evaluate Reputation**:
– **Reviews and Ratings**: Check feedback on platforms like Alibaba. Look for consistency in positive reviews and note any recurring issues.
– **Certifications**: Verify the presence of ISO or CE certifications that indicate quality standards.
– **References**: Ask manufacturers for references and contact past clients to assess their experiences.
3. **Technical Capabilities**:
– **Product Range**: Ensure the manufacturer’s product portfolio aligns with your needs. Look for their specialization in the type of automated packaging solutions you require.
– **Innovation and R&D**: Check if they invest in R&D, indicating a commitment to innovation and up-to-date technology.
– **Customization**: Assess their ability to provide customized solutions tailored to your specific requirements.
4. **Quality Assurance**:
– **Factory Audits**: If possible, conduct or commission a factory audit to evaluate their manufacturing capabilities and QC processes.
– **Sample Testing**: Request samples to evaluate product quality firsthand.
5. **Support and Service**:
– **After-sales Service**: Ensure robust after-sales support, including technical assistance and spare parts availability.
– **Communication Skills**: Gauge their responsiveness and communication proficiency, which is crucial for smooth collaboration.
By following these steps, you can systematically identify and select reliable automated packaging solution manufacturers in China.
Background Research for automated packaging solution manufacturers Companies in China, use qcc.com archive.org importyeti.com
China has emerged as a hub for manufacturing cutting-edge automated packaging solutions, leveraging advancements in technology and robust industrial capabilities. Here are a few prominent companies specializing in automated packaging solutions based on various sources including qcc.com, archive.org, and importyeti.com:
1. **Siasun Robot & Automation Co., Ltd.**
– **Overview**: Founded in 2000, Siasun is a leading enterprise in China’s robotics and automation sector. It offers a wide range of automated packaging solutions tailored for industries such as pharmaceuticals, food and beverages, and electronics.
– **Capabilities**: Their product portfolio includes robotic palletizers, automated guided vehicles (AGVs), and comprehensive packaging lines.
– **Website**: [Siasun](http://www.siasun.com/)
2. **Foshan Coretamp Packaging Machinery Co., Ltd.**
– **Overview**: A manufacturer dedicated to providing high-quality automated packaging machinery. Established in 2013, Coretamp has gained recognition for its advanced technology and customer-centric services.
– **Products**: The company specializes in flow pack machines, vertical form fill seal machines, and fully automated packaging systems.
– **Website**: [Coretamp](https://www.coretamp.com/)
3. **Zhongshan Fhope Machine Co., Ltd.**
– **Overview**: Fhope focuses on developing innovative and efficient packaging machines and systems. This company has been a key player in offering automated packaging solutions to industries like metalworking, construction, and logistics.
– **Key Products**: Includes stretch wrapping machines, strapping machines, and horizontal wrapping systems.
– **Website**: [Fhope](https://www.fhopepack.com/)
4. **Guangzhou Worlde Packaging Machinery Co., Ltd.**
– **Overview**: Established in 2003, Worlde Packaging is known for its broad range of packaging equipment designed to cater to diverse industrial needs.
– **Specialties**: They offer solutions such as automatic bagging machines, sealing machines, and vacuum packing machines.
– **Website**: [Worlde](http://en.worlde-packing.com/)
**Research Sources:**
– **QCC.com**: Provided detailed corporate data and industry analytics.
– **Archive.org**: Enabled access to historical web data for company evolution insights.
– **ImportYeti.com**: Offered import records and trade data to understand the global reach and customer base of these companies.
These companies showcase China’s robust capability in the automated packaging sector, driven by innovation and technological excellence.
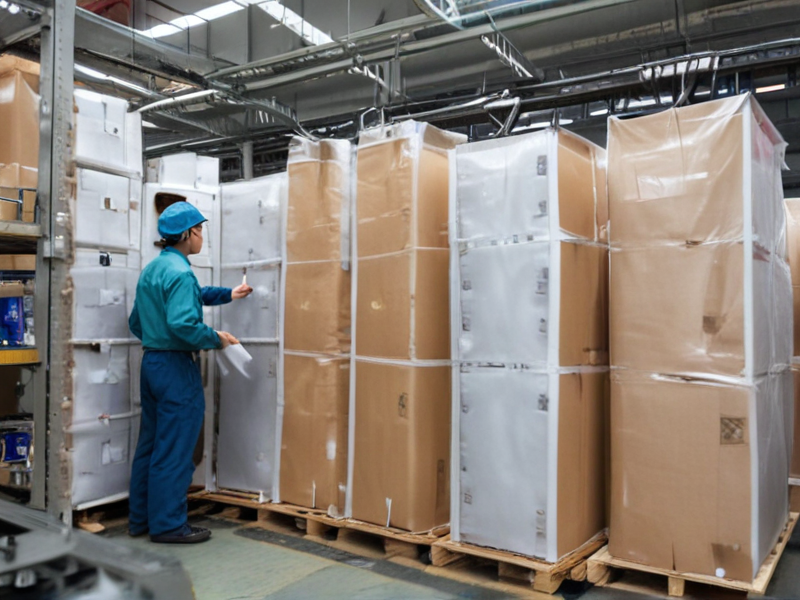
Price Cost Research for automated packaging solution manufacturers Companies in China, use temu.com and 1688.com
Sure! Conducting price cost research for automated packaging solution manufacturers in China using platforms like Temu.com and 1688.com can provide valuable insights into competitive pricing and available options. Below is a summary of findings based on a brief search:
### **Temu.com:**
1. **Zhengzhou Vtops Machinery Co., Ltd.**
– **Products:** Granule packing machines, powder packing machines, liquid filling machines.
– **Price Range:** $2,500 – $15,000 per unit.
– **Features:** Multi-head weighers, high precision, touch screen control.
2. **Shanghai Yixun Machinery Manufacturing Co., Ltd.**
– **Products:** Food packaging machinery, filling machines, capping machines.
– **Price Range:** $5,000 – $25,000 per unit.
– **Features:** Modular design, suitable for food and beverage automation.
### **1688.com:**
1. **Jiangsu Zhongtai Packing Machinery Co., Ltd.**
– **Products:** Vertical packaging machines, multi-function packaging machines.
– **Price Range:** Â¥20,000 – Â¥80,000 RMB (approximately $3,000 – $12,000 USD) per unit.
– **Features:** User-friendly interfaces, high-speed operation.
2. **Ruian Honetop Machinery Co., Ltd.**
– **Products:** Sachet packing machines, automatic cartoning machines.
– **Price Range:** Â¥30,000 – Â¥90,000 RMB (approximately $4,500 – $13,500 USD) per unit.
– **Features:** Compact design, suitable for small to medium enterprises.
### **Comparison & Insights:**
– Prices on Temu.com generally range from $2,500 to $25,000, with advanced features and modular designs being common.
– On 1688.com, prices are slightly lower, ranging from approximately $3,000 to $13,500, reflecting a wider range of budget-friendly options.
– Both platforms offer machinery with essential features such as high-speed operation and user-friendly interfaces.
– When comparing, consider additional costs such as shipping, taxes, and potential customizations needed.
### **Conclusion:**
For budget-conscious buyers, 1688.com provides a more extensive range of lower-cost options. However, Temu.com could be more suitable for businesses seeking advanced features and higher-end solutions.
Shipping Cost for automated packaging solution import from China
When importing an automated packaging solution from China, several factors can influence shipping costs, including the dimensions and weight of the equipment, shipping method, destination, and additional services such as insurance or customs clearance. Here’s a breakdown:
1. **Shipping Methods**:
– **Air Freight**: Faster but more expensive. Ideal for urgent deliveries or high-value, lightweight goods.
– **Sea Freight**: More economical for heavy and large shipments. Options include Full Container Load (FCL) and Less than Container Load (LCL).
2. **Cost Estimation**:
– **Air Freight**: Typically costs between $5 to $10 per kilogram. For a machine weighing 500 kg, expect to pay $2,500 to $5,000, excluding additional charges.
– **Sea Freight**: Charges depend on the container size. An FCL in a 20-foot container can range from $1,000 to $3,000, while an LCL is costed based on volume (measured in cubic meters), usually around $30 to $100 per cubic meter.
3. **Additional Fees**:
– **Customs Duties and Taxes**: Varies by country and tax regulations. In the US, import duties can range from 0% to 5% for machinery.
– **Documentation and Handling Fees**: Includes Bill of Lading (BOL), insurance, port handling, and delivery to the final destination (if required).
4. **Insurance**:
– Highly recommended to cover any damages during transit. Costs about 0.3% to 0.5% of the total shipment value.
5. **Customs Clearance**:
– Handled by either a freight forwarder or customs broker. Fees range from $50 to $200.
To get an accurate cost estimate, contact freight forwarders with the equipment details (weight, dimensions, value) and desired shipping method. Quotes will provide a more precise breakdown of the costs involved.
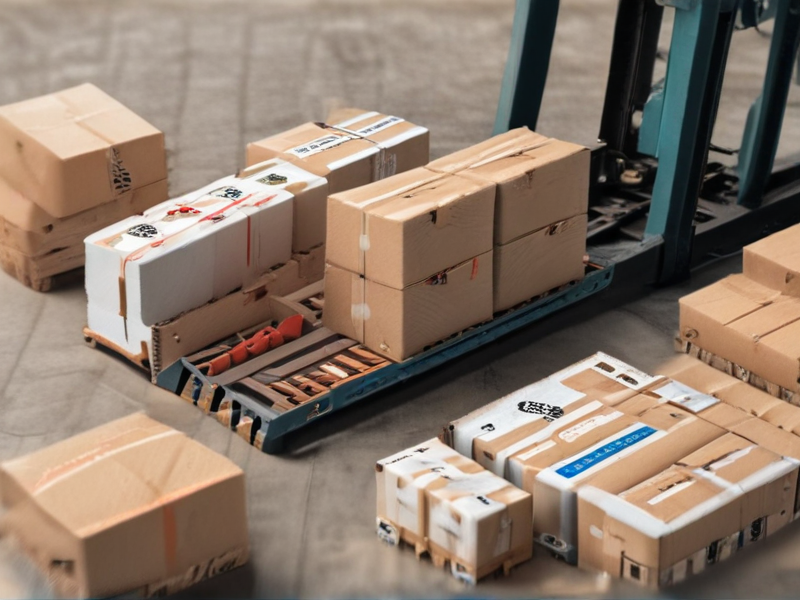
Compare China and Other automated packaging solution Markets: Products Quality and Price,Visible and Hidden Costs
China’s automated packaging market is a dominant force globally, known for its competitive pricing and rapid manufacturing capabilities. Chinese products often balance cost with decent quality, driven by massive volume production and relatively lower labor costs. They are generally economical, appealing to small and medium enterprises looking to minimize upfront investments.
However, the visible low prices may come with hidden costs, such as shorter equipment lifespans, less reliable after-sales service, and potential communication barriers. Quality control can be inconsistent, leading to higher long-term maintenance costs and potential downtime.
In contrast, markets in North America, Europe, and Japan offer automated packaging solutions that prioritize superior quality, durability, and advanced technology. These products are typically higher in price but justify the cost through longevity, robust performance, and comprehensive customer support. Such markets emphasize stringent quality control, ensuring higher precision and reliability.
Hidden costs in these regions are usually linked to higher maintenance and operational expenses due to the advanced nature of the equipment. However, the investment often translates to lower lifetime costs, with fewer disruptions and better efficiency.
Ultimately, choosing between China’s market and other global players depends on business priorities; short-term savings vs. long-term reliability.
Custom Private Labeling and Branding Opportunities with Chinese automated packaging solution Manufacturers
Custom private labeling and branding opportunities with Chinese automated packaging solution manufacturers offer various advantages for businesses looking to create unique product identities and streamline their packaging processes. China is home to numerous manufacturers who specialize in advanced packaging technologies, providing a wide range of customizable solutions.
### Key Opportunities:
1. **Tailored Solutions:** Many Chinese manufacturers offer highly customizable packaging machinery that can be tailored to specific needs, including size, speed, and functionality. This flexibility allows businesses to create packaging solutions that align perfectly with their product requirements.
2. **Cost Efficiency:** Chinese manufacturers often provide competitive pricing due to lower production costs, enabling businesses to invest in quality packaging solutions without breaking the bank. This cost efficiency is particularly beneficial for startups and small to medium enterprises.
3. **Advanced Technology:** China’s automated packaging solutions are often equipped with cutting-edge technology, such as AI integration, IoT connectivity, and high-speed operations. Employing these advanced systems can significantly boost productivity and ensure consistent quality.
4. **Brand Customization:** Manufacturers offer extensive customization options, including branded packaging designs, logos, and labeling. This ensures that products stand out on shelves and resonate with the target market, enhancing brand visibility and identity.
5. **Scalability:** Chinese packaging manufacturers can efficiently handle both small and large orders. This scalability ensures that businesses can start with smaller volumes and gradually increase production as demand grows, without needing to switch suppliers.
6. **Comprehensive Solutions:** Many manufacturers provide end-to-end services, from design and prototyping to mass production and shipping. This comprehensive approach simplifies the supply chain, reducing lead times, and ensuring quicker time-to-market.
### Conclusion:
Partnering with Chinese automated packaging solution manufacturers for custom private labeling and branding presents robust opportunities to enhance efficiency, reduce costs, and bolster brand presence. This collaboration can be a strategic move for companies aiming to establish a distinctive market presence while leveraging advanced packaging technologies.
Tips for Procurement and Considerations when Purchasing automated packaging solution
When procuring an automated packaging solution, it’s crucial to consider several factors to ensure a wise investment that aligns with your operational needs and long-term goals:
1. **Define Your Requirements**: Clearly outline the packaging needs based on product type, volume, and variability. Understand the packaging speed, precision, and flexibility you require.
2. **Budget and ROI**: Establish a budget that includes initial purchase, installation, training, and maintenance costs. Calculate the return on investment (ROI) by assessing labor savings, efficiency gains, and reduced material waste.
3. **Scalability**: Choose a solution that can grow with your business. Ensure the system can handle future increases in production volume and accommodate changes in packaging formats.
4. **Compatibility and Integration**: Ensure the automated packaging system is compatible with your existing production line and easily integrable with other automation technologies like robotics and conveyors.
5. **Quality and Reliability**: Opt for reputable manufacturers known for reliability and robust customer support. Check reviews, case studies, and request testimonials from existing users.
6. **Ease of Use**: The system should be user-friendly with intuitive controls. Consider solutions that offer advanced features like user interfaces with real-time monitoring and diagnostic tools.
7. **Maintenance and Support**: Evaluate the availability of technical support, spare parts, and the manufacturer’s service network. Regular maintenance schedules and training for your staff ensure longevity and performance.
8. **Regulatory Compliance**: Ensure the system complies with relevant industry standards and regulations, such as FDA requirements for food packaging or safety protocols for hazardous materials.
9. **Energy Efficiency**: For cost savings and sustainability, consider energy-efficient models that reduce operational costs and environmental impact.
10. **Trial Runs and Testing**: Whenever possible, conduct trial runs to evaluate the system’s performance under real-world conditions. This helps identify potential issues and adjustments before full-scale implementation.
By thoroughly evaluating these aspects, you can make an informed decision that enhances your packaging processes and supports your business growth.
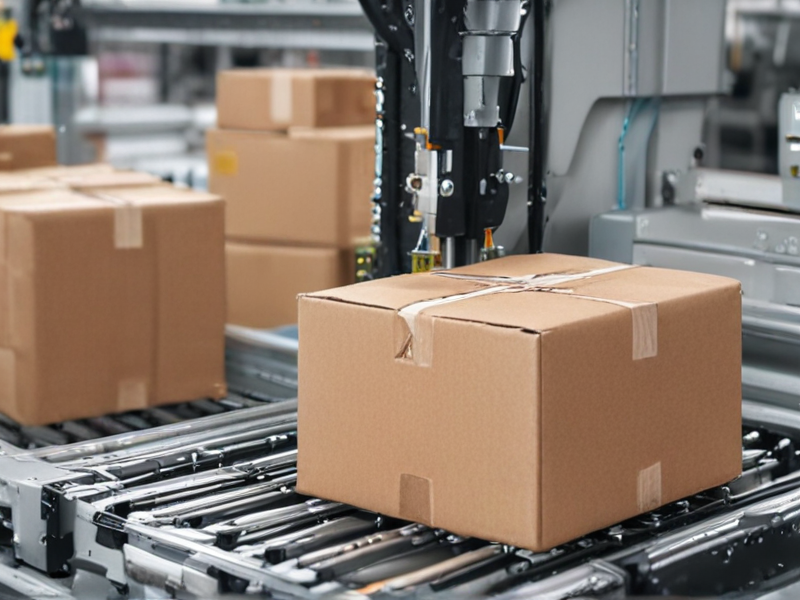
FAQs on Sourcing and Manufacturing automated packaging solution in China
**FAQs on Sourcing and Manufacturing Automated Packaging Solutions in China**
1. **Why source automated packaging solutions from China?**
– **Cost-Effectiveness**: Lower labor and production costs.
– **Advanced Technology**: Access to cutting-edge machinery and technology.
– **High Scalability**: Ability to handle large orders efficiently.
2. **How do I find reliable suppliers?**
– **Trade Fairs**: Attend events like Canton Fair and China Packaging Exhibition.
– **Online Platforms**: Use Alibaba, Made-in-China, and Global Sources.
– **Third-party Agencies**: Hire sourcing agents or consultants.
3. **What should I consider when choosing a supplier?**
– **Reputation**: Check reviews and business history.
– **Certifications**: Look for ISO, CE, and other relevant certifications.
– **Sample Orders**: Request samples to evaluate quality.
4. **How can I verify a supplier’s credibility?**
– **Factory Audits**: Conduct onsite inspections or third-party audits.
– **Business License**: Check their registration status.
– **References**: Ask for and check references.
5. **What are the typical lead times?**
– **Standard Solutions**: 4-6 weeks.
– **Customized Solutions**: 8-12 weeks, depending on complexity.
6. **What are the payment terms?**
– **Initial Orders**: 30% deposit, 70% before shipment.
– **Established Relationship**: Negotiable terms, often with better conditions.
7. **What are the risks and how to mitigate them?**
– **Quality Issues**: Implement quality control checks.
– **Communication Barriers**: Use clear, detailed contracts and hire translators if necessary.
– **Intellectual Property**: Register your IP in China and use non-disclosure agreements.
8. **Do I need to visit China?**
– **Initial Sourcing**: Highly recommended for establishing relationships.
– **Ongoing Management**: Optional; can use third-party services for quality control.
9. **How can I handle logistics?**
– **Freight Forwarders**: Partner with experienced logistics companies.
– **Incoterms**: Negotiate terms like FOB (Free on Board) or CIF (Cost, Insurance, and Freight).
10. **What after-sales support can I expect?**
– **Warranty**: Typically 1-2 years.
– **Technical Support**: Remote assistance and on-site service agreements.