Top 10 primary packaging automation in China introduce,list main products and website if have
Here are ten leading companies in primary packaging automation in China, their main products, and websites:
1. **SaintyCo**
– **Main Products**: Tablet presses, capsule filling machines, blister packaging machines, and softgel production lines.
– **Website**: [saintyco.com](https://www.saintyco.com)
2. **Hangzhou Youngsun Intelligent Equipment**
– **Main Products**: Strapping machines, shrink wrapping machines, and carton sealers.
– **Website**: [youngsunpack.com](http://www.youngsunpack.com)
3. **Tofflon Science and Technology Group**
– **Main Products**: Freeze dryers, sterilizers, and filling lines for pharmaceuticals.
– **Website**: [tofflon.com](http://www.tofflon.com)
4. **Jornen Machinery Co., Ltd.**
– **Main Products**: Blister packing machines, cartoning machines, and liquid filling machines.
– **Website**: [jornen.com](https://www.jornen.com)
5. **Shanghai Pharmaceutical Machinery Co., Ltd. (SPM)**
– **Main Products**: Tablet presses, capsule fillers, and blister packaging machines.
– **Website**: [china-spm.com](http://www.china-spm.com)
6. **Ruian Trustar Pharma & Packing Equipment Co., Ltd.**
– **Main Products**: Blister packing machines, cartoning machines, and liquid filling machines.
– **Website**: [trustarmachinery.com](http://www.trustarmachinery.com)
7. **Foshan Samfull Packaging Machinery Co., Ltd.**
– **Main Products**: Vertical form fill seal (VFFS) machines, and packaging lines for granular and powder products.
– **Website**: [samfullpack.com](http://www.samfullpack.com)
8. **Guangzhou Kisen Packing Machinery Co., Ltd.**
– **Main Products**: Horizontal flow wrappers and vertical packaging machines.
– **Website**: [kspack.com.cn](http://www.kspack.com.cn)
9. **Wenzhou Zhuding Machine Co., Ltd.**
– **Main Products**: Blister packaging machines and end-of-line packaging solutions.
– **Website**: [zhudingmachine.com](http://www.zhudingmachine.com)
10. **Shanghai Kaiquan Machine Valve Co., Ltd.**
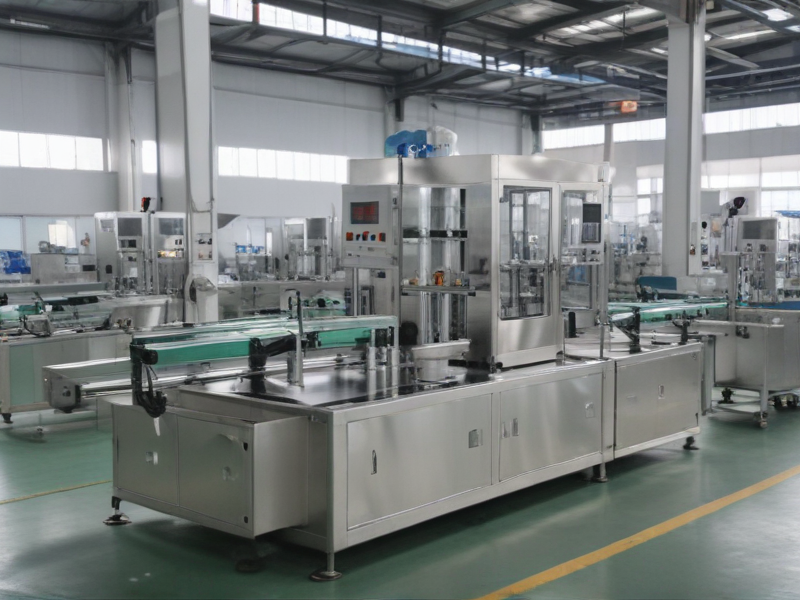
Types of primary packaging automation
Primary packaging automation is essential for enhancing efficiency, consistency, and safety in packaging operations. It involves the use of automated systems to handle and package individual products. Here are the key types of primary packaging automation:
1. **Form, Fill, and Seal (FFS) Machines**:
– **Vertical FFS (VFFS)**: Suitable for products like snacks, grains, and powders. The machine forms a pouch from a flat roll of film, fills it with the product, and seals it.
– **Horizontal FFS (HFFS)**: Ideal for products such as confectionery, pharmaceuticals, and sachets. It forms a pouch or tray, fills it, and seals it horizontally.
2. **Blister Packaging Machines**:
– Used extensively in the pharmaceutical and consumer goods industries, these machines create a cavity or pocket made from a formable web, usually a plastic or aluminum film. Products are placed in these cavities, which are then sealed with a lidding material.
3. **Cartoning Machines**:
– These machines are designed to form cartons, fill them with products such as bottles or packets, and seal them. They are used for items like cosmetics, pharmaceuticals, and food products.
4. **Flow Wrapping Machines**:
– Often used for products like candy bars, baked goods, and hardware. Flow wrappers envelop a product in a continuous, flexible film that wraps around it, forming a tight seal.
5. **Tray Sealers**:
– These machines are used for sealing product-filled trays, commonly used in packaging fresh produce, ready meals, and medical devices. They ensure an airtight seal, often under a modified atmosphere to prolong shelf life.
6. **Bottle Filling and Capping Machines**:
– Widely used in the beverage, pharmaceutical, and cosmetic industries, these machines automate the process of filling bottles with liquids, powders, or granules and then capping them.
Each type of primary packaging automation offers distinct advantages tailored to specific products and industries, thereby optimizing packaging processes and ensuring product integrity and safety.
Pros and Cons of Using primary packaging automation
**Pros of Using Primary Packaging Automation:**
1. **Increased Efficiency**: Automation speeds up the packaging process, significantly reducing the time required compared to manual methods. This leads to higher throughput and faster product-to-market times.
2. **Consistency and Quality**: Automated systems deliver uniform and precise packaging, minimizing the risk of human error. This consistency enhances product quality and customer satisfaction.
3. **Cost Savings**: Over time, automation can reduce labor costs and operational expenses. Although the initial investment is high, the return on investment can be substantial due to lower ongoing costs.
4. **Enhanced Safety**: Automation reduces the need for human interaction, lowering the likelihood of workplace injuries. These systems can handle hazardous or repetitive tasks safely.
5. **Scalability**: Automated systems can be easily scaled up to meet increased demand without a proportional increase in labor costs, making them ideal for growing businesses.
6. **Data Collection and Monitoring**: Automated systems can provide valuable data on production rates, down-time, and other metrics. This data can be analyzed to optimize processes and improve efficiency further.
**Cons of Using Primary Packaging Automation:**
1. **High Initial Cost**: The upfront investment for automated systems can be prohibitive for small businesses. Costs include not just the machinery but also installation, training, and maintenance.
2. **Complexity**: Automated systems require significant technical knowledge to operate, troubleshoot, and repair. This can necessitate ongoing training and hiring of specialized staff.
3. **Maintenance Requirements**: Automated systems require regular maintenance and occasional upgrades, which can lead to additional costs and downtime.
4. **Job Displacement**: Automation can result in the reduction of manual labor positions, which may impact employment rates and worker morale.
5. **Rigidity**: Automated systems may lack the flexibility to handle varied tasks or rapid changes in product lines without significant adjustments or reprogramming.
6. **Integration Issues**: Incorporating new automated systems into existing production lines can be challenging and disruptive, requiring careful planning and execution.
In summary, while primary packaging automation offers numerous advantages like efficiency and cost savings, the drawbacks such as high initial costs and complexity must be carefully considered.
primary packaging automation Reference Specifications (varies for different product)
Primary packaging automation pertains to the technology and machinery used to package products directly in their first layer of packaging. This layer comes into direct contact with the product and is crucial for ensuring its safety, integrity, and freshness. Reference specifications will vary depending on the type of product, but general standards and considerations include:
1. **Product Compatibility**:
– **Food & Beverages**: Must meet FDA or relevant food safety standards, ensuring materials are food-grade and capable of preserving freshness.
– **Pharmaceuticals**: Compliance with Good Manufacturing Practices (GMP) and must often support sterile or contamination-free environments.
– **Cosmetics**: Ensure that materials do not react with product formulations and comply with cosmetic safety standards.
2. **Material Handling**:
– **Durability**: Materials must be resilient enough to protect the product during transportation and storage.
– **Sustainability**: Increasingly important, materials should be recyclable or biodegradable when possible.
3. **Machinery Specifications**:
– **Speed and Efficiency**: Machinery should meet the desired throughput rates without compromising quality.
– **Flexibility**: Capability to handle various product sizes, shapes, and materials without extensive downtime for changeovers.
– **Accuracy**: Precision in measurements and filling to reduce waste and ensure consistent product quality.
4. **Integration**:
– **IoT and Smart Systems**: Modern systems often integrate with IoT for real-time monitoring, diagnostics, and predictive maintenance.
– **Compatibility**: Ease of integration with existing manufacturing systems and processes.
5. **Safety and Compliance**:
– **Worker Safety**: Must include safety features such as emergency stops, guards, and sensors to prevent accidents.
– **Regulatory Compliance**: Adherence to local and international regulations, including health, safety, and environmental standards.
6. **Quality Control**:
– Implement sensors and inspection systems for real-time quality checks to ensure packaging integrity and product adherence to standards.
Adhering to these reference specifications ensures that primary packaging automation systems are efficient, compliant, and capable of maintaining product integrity through the supply chain.
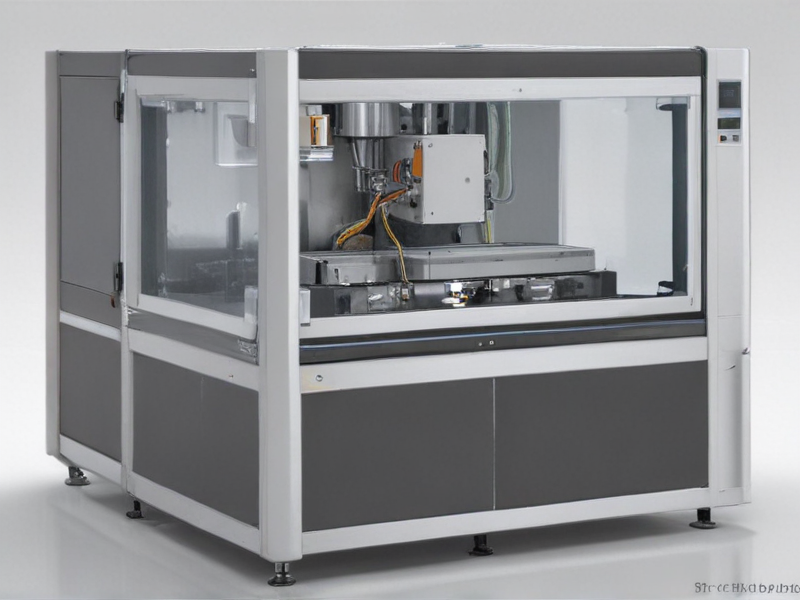
Applications of primary packaging automation
Primary packaging automation, a technology-driven methodology, has earmarked its significance across a multitude of industries by introducing efficiency, accuracy, and cost-effectiveness. Here are notable applications of primary packaging automation:
1. **Pharmaceuticals**: Automated systems in pharmaceuticals ensure precise filling, sealing, and labeling of medicinal products, thereby minimizing contamination risks and maintaining dosage accuracy. This enhances compliance with stringent regulatory standards and improves patient safety.
2. **Food and Beverages**: In this sector, automation streamlines the packaging process for various consumables such as snacks, dairy, and beverages. It ensures uniformity, enhances hygiene by reducing human contact, and speeds up the packaging process to keep up with high demand.
3. **Cosmetics**: Automation facilitates precise filling of creams, lotions, and other cosmetic products into containers, ensuring minimal spillage and maintaining the consistency of each product’s presentation. This contributes to brand integrity and customer satisfaction.
4. **Consumer Goods**: For items like batteries, household supplies, and small electronics, automated packaging systems offer high flexibility and adaptability, managing diverse product sizes and shapes efficiently. This reduces labor costs and production timelines.
5. **Agriculture**: Packaging automation in the agricultural sector involves packing seeds, fertilizers, and agricultural chemicals. It ensures accurate weight measurements and secure sealing to prolong shelf life and maintain product integrity during transportation.
6. **Medical Devices**: Automated systems package items like syringes, surgical instruments, and diagnostic tools in sterile conditions, ensuring they remain uncontaminated which is imperative for patient safety during medical procedures.
7. **Personal Care Products**: Automation aids in the packaging of toiletries and hygiene products, ensuring tamper-evident seals and enhancing shelf appeal through precise labeling and finishing.
Overall, primary packaging automation not only enhances operational efficiency and product safety but also supports scalability, reducing time-to-market for various products across diverse industries. This technology is pivotal in addressing modern consumer demands for higher quality and safety standards.
Material of primary packaging automation
Certainly! Primary packaging automation involves using machinery and technology to streamline the process of enclosing or protecting products for distribution, storage, sale, and use. The choice of material for primary packaging in automated systems is critical for ensuring efficiency, protection, and sustainability.
1. **Plastic:** Widely used due to its versatility, durability, and lightweight nature. Automated systems handle various forms of plastic, including polyethylene (PE), polypropylene (PP), and PET. These materials are ideal for molding, sealing, and providing a moisture barrier. However, concerns about environmental impact are pushing innovations in recyclable and biodegradable plastics.
2. **Glass:** Preferred for its impermeability and ability to preserve the integrity of products, especially in pharmaceuticals and food and beverages. Automated systems require precise handling techniques because of glass’s brittleness. Advancements in robotics and cushioning techniques have mitigated breakage risks.
3. **Metal:** Frequently used for canned goods and beverages. Metals like aluminum and steel are robust, offer excellent protection, and are highly recyclable. Automation ensures precise forming, filling, and sealing, boosting production efficiency.
4. **Paper and Cardboard:** Sustainable and biodegradable, these materials are essential for eco-friendly packaging. Automation helps in cutting, folding, and gluing processes, producing various container shapes quickly and efficiently. Coated papers enhance barrier properties against moisture and grease.
5. **Biodegradable Materials:** Plant-based plastics and other eco-friendly materials are emerging in the automated packaging sector. These materials aim to reduce environmental impact without sacrificing performance. Automation must adapt to handle these materials delicately to maintain their structural integrity.
In conclusion, the selection of material for primary packaging automation balances factors such as product protection, cost-efficiency, sustainability, and the specific demands of the automated process. Ongoing innovations continue to refine this balance, supporting greater efficiency and reduced environmental impact in packaging operations.
Quality Testing Methods for primary packaging automation and how to control the quality
Quality testing methods for primary packaging automation are crucial for ensuring product safety and integrity. Key testing methods include:
1. **Visual Inspection Systems**: Automated cameras and sensors check for defects such as cracks, dents, and improper seals. Advanced systems use artificial intelligence (AI) to identify anomalies.
2. **Leak Detection**: Techniques like vacuum decay, pressure decay, and helium mass spectrometry test for leaks in sealed packaging. These methods ensure that the package maintains its integrity and protects the product.
3. **Dimensional and Weight Checks**: Automated systems measure and weigh packages to ensure they meet specified dimensions and weight criteria, guaranteeing uniformity and compliance.
4. **Seal Integrity Testing**: This involves destructive and non-destructive methods to ensure that seals are secure. Vacuum seal testing and bubble emission are examples used to detect weak points or leaks in the seal.
5. **Label Inspection**: Ensures that labels are correctly placed, legible, and free of defects. This is often done using high-resolution cameras and image recognition software.
To control quality in primary packaging automation:
1. **Integration of Real-time Monitoring**: Implement sensors and IoT devices to collect data continuously, enabling instant detection of deviations from standards.
2. **Feedback Loops**: Automated systems should have feedback mechanisms to adjust processes when deviations are detected, ensuring consistent product quality.
3. **Regular Calibration and Maintenance**: Schedule calibration and maintenance of machines to retain accuracy and functionality. This includes checking and updating software systems regularly.
4. **Statistical Process Control (SPC)**: Use statistical methods to monitor and control quality during packaging. Control charts and capability analysis help in maintaining process consistency and identifying variations.
5. **Employee Training**: Continuous training for staff on using automated quality control systems effectively ensures that human intervention, when necessary, is knowledgeable and efficient.
Implementing these methods and controls ensures high-quality primary packaging, reducing errors, waste, and ensuring compliance with regulatory standards.
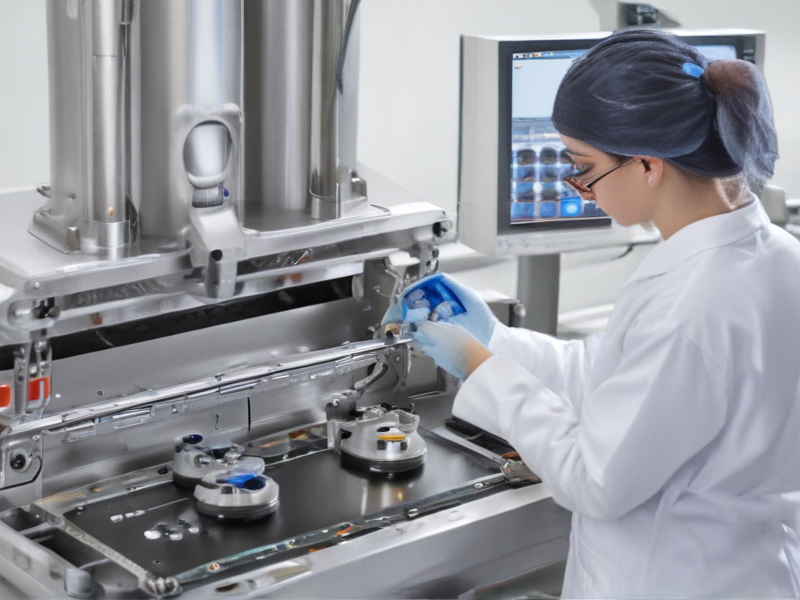
The Work Process and how to use primary packaging automation
Primary packaging automation refers to the use of technology to streamline the process of enclosing products in their first layer of packaging, directly contacting the product. This automation can significantly improve efficiency, accuracy, and consistency in packaging operations. Here’s how to integrate primary packaging automation into your work process:
1. **Assessment and Planning**
– **Evaluate Needs**: Determine the type and volume of products to be packaged.
– **Select Equipment**: Choose suitable automated machinery, such as filling machines, sealing machines, and labeling systems.
2. **Integration**
– **Design Layout**: Plan the placement of machinery to ensure a smooth workflow.
– **Install Equipment**: Set up machinery according to the manufacturer’s specifications and your packaging line requirements.
3. **Initial Testing**
– **Run Trials**: Perform initial test runs to ensure the equipment functions correctly with your products.
– **Adjust Settings**: Fine-tune machine settings like speed, product handling, and precision until optimal performance is achieved.
4. **Training**
– **Staff Training**: Provide comprehensive training for operators on running and maintaining the automated packaging machines.
– **Safety Protocols**: Ensure that employees adhere to safety standards to prevent workplace accidents.
5. **Operation and Monitoring**
– **Continuous Operation**: Start full-scale production with automated systems in place.
– **Monitor Performance**: Use sensors and software to monitor equipment performance and packaging quality in real time.
– **Regular Maintenance**: Schedule routine maintenance to prevent downtime and extend machinery life.
6. **Quality Control**
– **Inspect Packages**: Regularly check packaged products to ensure they meet quality standards.
– **Feedback Loop**: Implement a system for continuous feedback and improvement based on inspection results.
By following these steps, you can efficiently integrate primary packaging automation into your operations, leading to increased productivity, reduced labor costs, and enhanced product consistency.
primary packaging automation Importing questions including Cost,Supplier,Sample,Certification and Market
Sure, here’s a concise overview of importing primary packaging automation solutions:
1. **Cost**: The cost of primary packaging automation varies widely based on complexity, capacity, and technology. Basic systems might start around $10,000, but comprehensive setups can exceed $500,000. Consider not just the purchase price, but also shipping, installation, and ongoing maintenance costs.
2. **Supplier**: Research and select reputable suppliers with experience in your industry. Key suppliers often have a global presence and offer robust customer support. Examples include companies like Bosch Packaging Technology, Tetra Pak, and ProMach. Engage with multiple suppliers to compare offerings and prices.
3. **Sample**: Request samples or trials to evaluate the equipment. This can often be arranged at trade shows, through demo units, or via virtual simulations. Assess the machinery’s compatibility with your products, ease of use, and integration with existing systems.
4. **Certification**: Ensure the equipment meets industry standards and regulatory requirements. Look for certifications like CE (Europe), UL (USA), and ISO 9001 (Quality Management). Compliance with these standards ensures safety, reliability, and quality.
5. **Market**: Understand your market’s specific needs and trends. Packaging automation can enhance efficiency, consistency, and scalability, supporting market demands for faster turnaround and reduced human error. Stay informed about innovations, and competitor strategies to maintain a competitive edge.
By carefully considering these aspects, you can make informed decisions in importing primary packaging automation systems that align with your operational and business goals.
How to find and select check reliable primary packaging automation manufacturers in China
Finding and selecting reliable primary packaging automation manufacturers in China requires careful research and due diligence. Here is a concise, step-by-step guide:
1. **Online Research**:
– Begin with comprehensive online searches using keywords like “primary packaging automation manufacturers in China.”
– Utilize industry websites, trade portals (Alibaba, Global Sources), and business directories.
2. **Review Credentials**:
– Verify certifications (ISO, CE).
– Check for industry association memberships.
3. **Evaluate Reputation**:
– Look for reviews and case studies on platforms such as Alibaba, Made-in-China, and customer forums.
– Contact previous clients for their feedback.
4. **Assess Product Quality and Range**:
– Examine the range of products and technologies offered.
– Request product samples or demos.
5. **Compare Technical Capabilities**:
– Ensure the manufacturer’s technology aligns with your specific packaging requirements.
6. **Factory Visit**:
– If possible, conduct an on-site visit to assess manufacturing facilities and quality control processes.
7. **Check Supply Chain Reliability**:
– Investigate the manufacturer’s raw material sources and supply chain robustness.
8. **Negotiate Terms and Services**:
– Discuss pricing, warranty, after-sales service, and training.
9. **Legal and Financial Due Diligence**:
– Confirm the company’s legal standing and financial stability.
– Verify business licenses and company registration.
10. **Trial Order**:
– Place a small trial order to evaluate performance and reliability before committing to larger purchases.
By systematically following these steps, you can identify and select a reliable primary packaging automation manufacturer in China.
Background Research for primary packaging automation manufacturers Companies in China, use qcc.com archive.org importyeti.com
China hosts a dynamic market for primary packaging automation manufacturers, driven by technological advancements and the need for efficiency. To research these companies, resources like qcc.com, archive.org, and importyeti.com offer valuable insights.
**Qcc.com**
Qcc.com is a comprehensive corporate database in China. It provides detailed information about manufacturers, including financials, patents, and market performance. By searching for primary packaging automation manufacturers, you can identify key players such as Somic Automation Co., Ltd., Guangzhou Tech-Long Packaging Machinery Co., Ltd., and Hangzhou Youngsun Intelligent Equipment Co., Ltd. This platform allows you to examine their operational scale, industry status, and area of expertise.
**Archive.org**
Archive.org is a useful tool for accessing historical snapshots of company websites and other relevant industry reports. By examining past versions of the websites of major companies, you can trace their development, product evolution, and market strategies. This archival data helps in understanding how these companies have adapted to technological trends and market demands over time.
**ImportYeti.com**
ImportYeti.com enables the analysis of import data to track the global trade activities of packaging automation equipment. By inputting the names of Chinese manufacturers, you can discover their export volumes, key markets, and major trading partners. Companies like Newamstar Packaging Machinery Co., Ltd., and GSK (Shanghai) Automation Systems Ltd., often surface as significant exporters. This data highlights their international presence and reliability.
In summary, utilizing qcc.com for corporate insights, archive.org for historical context, and ImportYeti.com for trade analysis, you can gather a robust understanding of primary packaging automation manufacturers in China. Prominent companies like Somic Automation, Guangzhou Tech-Long, and Newamstar stand out as industry leaders with strong domestic and international footprints.
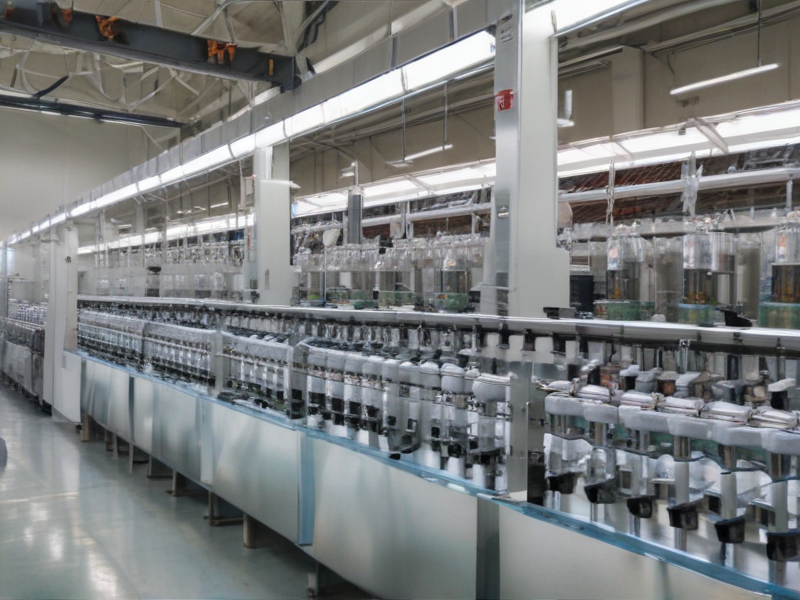
Price Cost Research for primary packaging automation manufacturers Companies in China, use temu.com and 1688.com
Sure, here’s a concise research summary on the pricing of primary packaging automation manufacturers in China, using data from Temu.com and 1688.com:
**Primary Packaging Automation Manufacturers in China**
1. **Temu.com:**
– Temu.com typically lists a range of primary packaging automation equipment including filling machines, sealing machines, and labeling machines.
– The average price for entry-level semi-automatic machines is between $500-$1,500 USD.
– Fully automated packaging machinery starts at approximately $10,000 USD, with prices escalating to $50,000 USD or more depending on complexity and capacity.
2. **1688.com:**
– Known as a major Chinese B2B marketplace, 1688.com features a comprehensive selection of primary packaging machinery.
– Semi-automatic filling machines are priced between Â¥3,000-Â¥10,000 RMB (roughly $450-$1,500 USD).
– Fully automated systems are priced broadly, generally starting from Â¥50,000 RMB (about $7,500 USD) and can exceed Â¥400,000 RMB (around $60,000 USD) based on specifications and brand reputation.
– Notable manufacturers such as Newamstar and Zhongya Packaging offer high-end solutions, often including customization options that can significantly impact the final price.
**Trends and Insights:**
– **Customization and Capacity:** Prices vary widely based on machine capacity, speed, and the degree of customization required.
– **Brand and Quality:** Renowned brands typically command higher prices but offer better after-sales support and reliability.
– **Bulk Purchases & Negotiations:** Bulk buying and direct negotiations can lead to significant discounts, particularly on 1688.com.
In conclusion, while entry-level semi-automatic equipment is relatively affordable, fully automated systems require a substantial investment. When sourcing from Chinese platforms, considering factors like machine capacity, level of automation, and brand can help optimize cost-efficiency and performance.
Shipping Cost for primary packaging automation import from China
Shipping costs for primary packaging automation equipment imported from China can vary greatly depending on several factors:
1. **Type of Shipment**:
– **Air Freight**: Faster but more expensive. Ideal for smaller or urgent shipments.
– **Sea Freight**: Slower but more cost-effective, suitable for larger or non-urgent shipments.
2. **Weight and Volume**: Heavy and bulky items will incur higher shipping costs.
3. **Shipping Distance**: Costs will increase with the distance between the Chinese port and the final destination.
4. **Freight Method**:
– **Full Container Load (FCL)**: More cost-effective for large shipments.
– **Less than Container Load (LCL)**: Suitable for smaller shipments but might include additional handling fees.
5. **Customs and Duties**: Vary by country and often include import duties, taxes, and customs clearance fees.
6. **Insurance**: Optional but recommended to protect against loss or damage during transit.
7. **Incoterms**: Determines who is responsible for different stages of shipping and can affect the overall cost.
### Estimated Costs:
1. **Air Freight**:
– For a lightweight parcel (up to 100 kg), costs could range between $5 to $10 per kilogram.
– Larger, heavier cargo will have a discounted rate per kilogram but can range from $3 to $6 per kilogram.
2. **Sea Freight**:
– FCL might range from $1,500 to $3,000 per 20-foot container or $2,500 to $4,500 per 40-foot container, depending on the port and season.
– LCL typically charges by volume (cubic meters), ranging from $50 to $150 per cubic meter.
### Example:
For a medium-sized, 200 kg packaging machine:
– **Air Freight**: Around $1,000 to $2,000.
– **Sea Freight**:
– FCL: Part of the cost based on volume can be $500 to $800, if shared.
– LCL: Around $200 to $500 for the machine’s part of the container.
**Additional Costs**: Customs duties (varies by country, typically 5%-25% of the item’s value), insurance (~1% of the item’s value), and domestic transport to the final destination.
Consult shipping and logistics experts for precise quotes tailored to your specific circumstances.
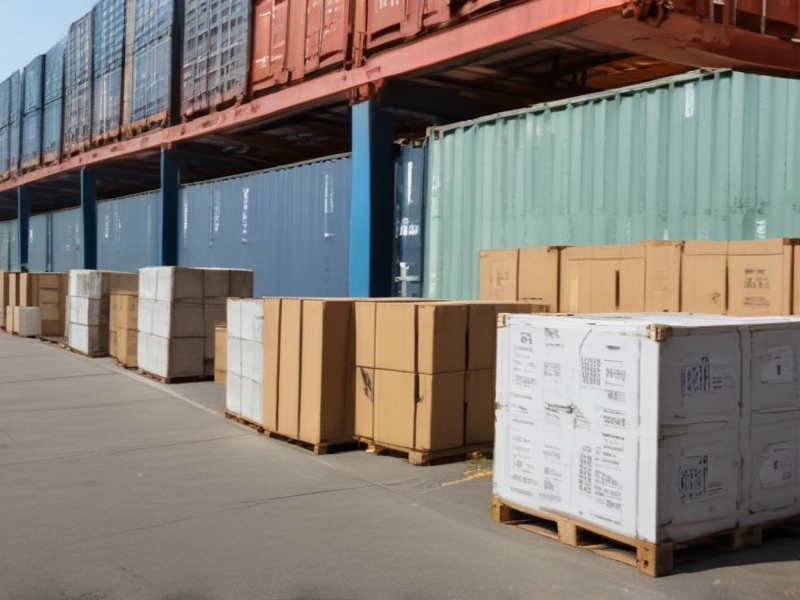
Compare China and Other primary packaging automation Markets: Products Quality and Price,Visible and Hidden Costs
When comparing China and other primary packaging automation markets such as Germany, the United States, and Japan, several factors come into consideration including product quality, price, and both visible and hidden costs.
**Product Quality**:
German, American, and Japanese packaging machinery is often renowned for high precision, durability, and technological advancements. Brands from these regions typically have stringent quality control standards and superior engineering. Chinese machinery, while improving rapidly, may still sometimes lag in these aspects, although top-tier manufacturers are closing the gap.
**Price**:
Chinese packaging machines generally come at a significantly lower price point due to lower labor and material costs. This provides an attractive entry-level point for many small to medium enterprises. In contrast, machinery from Germany, the United States, and Japan is more expensive but often justified by longevity, higher productivity rates, and fewer operational hiccups over time.
**Visible Costs**:
Visible costs include the initial purchase price, installation, and immediate operational costs. Chinese machines usually have lower upfront costs, making them an appealing choice for businesses with tight budgets. American, German, and Japanese machines will have higher purchase and setup costs.
**Hidden Costs**:
Hidden costs can include long-term maintenance, downtime due to breakdowns, availability of spare parts, and after-sales service. German, American, and Japanese manufacturers typically have robust customer support, comprehensive warranties, and readily available spare parts, which can minimize downtime. Chinese machines may incur higher long-term costs due to frequent maintenance needs, potential for quicker wear and tear, and sometimes inconsistent after-sales support.
In sum, while China offers cost-effective initial investments for primary packaging automation, opting for machinery from Germany, the United States, or Japan can be advantageous for businesses looking for high-quality, reliable equipment with better long-term performance and support, albeit at a higher initial cost.
Custom Private Labeling and Branding Opportunities with Chinese primary packaging automation Manufacturers
Custom private labeling and branding opportunities with Chinese primary packaging automation manufacturers present significant advantages for businesses looking to enhance their market presence. These manufacturers offer a wide range of packaging solutions, spanning from automatic fillers and cappers to sophisticated labeling machines and complete turnkey systems. By partnering with these manufacturers, companies can leverage cost-effective production without compromising on quality.
Firstly, China’s advanced manufacturing capabilities ensure high precision and efficiency in packaging automation. The use of state-of-the-art technology and strict quality control processes ensures that the end products meet international standards. This makes it easier for businesses to build trust with their end consumers.
Secondly, private labeling with Chinese manufacturers allows for extensive customization. Companies can collaborate with manufacturers to design packaging that aligns perfectly with their brand aesthetics and functional requirements. This can include custom shapes, sizes, materials, and printing options. The ability to customize packaging is crucial for creating a distinct market identity and enhancing brand value.
Additionally, partnering with Chinese manufacturers can significantly reduce costs. The lower labor and operational costs in China enable manufacturers to offer competitive pricing. This cost-efficiency, when combined with bulk production capabilities, results in significant economies of scale. Consequently, companies can pass on these reduced costs to consumers or reinvest in further brand development.
Moreover, many Chinese packaging automation manufacturers have robust R&D departments. This enables continuous innovation and the incorporation of the latest technology trends into the packaging solutions, thereby keeping the products at the forefront of the market.
In conclusion, custom private labeling and branding with Chinese primary packaging automation manufacturers offer an excellent opportunity to achieve high-quality, cost-effective, and uniquely branded packaging solutions. This strategic partnership can play a pivotal role in enhancing brand image and gaining a competitive edge in the marketplace.
Tips for Procurement and Considerations when Purchasing primary packaging automation
When purchasing primary packaging automation, several critical considerations can optimize decision-making:
1. **Understand Your Needs**: Assess volume, product types, regulatory requirements, and specific constraints before starting the procurement process.
2. **Technology Compatibility**: Ensure the automation equipment is compatible with existing systems. Look for machines that integrate seamlessly with your current production line.
3. **Flexibility and Scalability**: Choose equipment that can adapt to evolving product lines and increased production rates, accommodating future needs without significant overhauls.
4. **Quality and Reliability**: Prioritize machines from reputable manufacturers known for durability and minimal downtime. This reduces long-term maintenance costs and production delays.
5. **Ease of Use**: Opt for user-friendly systems with straightforward interfaces. This minimizes the learning curve, reducing training time and potential for operator error.
6. **Service and Support**: Evaluate the availability of technical support, spare parts, and after-sales service. This ensures quick resolution of any issues that might arise.
7. **Total Cost of Ownership (TCO)**: Consider all costs beyond the initial purchase price, including installation, maintenance, energy consumption, and depreciation.
8. **Compliance**: Ensure the equipment meets industry standards and regulations pertinent to your product, such as FDA regulations for food and pharmaceuticals.
9. **Customization**: Assess if the equipment can be customized to meet unique packaging requirements. Tailored solutions can enhance efficiency and product presentation.
10. **Vendor Reputation**: Research potential suppliers’ reputations. Reliable vendors typically offer better service and products that stand the test of time.
11. **Trial and Testing**: Request a trial period or a demonstration. This helps verify that the equipment meets your operational needs and performs as expected.
12. **Environmental Impact**: Opt for energy-efficient machines with sustainable packaging options, aligning with corporate environmental responsibility goals.
By thoughtfully considering these factors, you can make a well-informed decision that enhances your production capabilities and aligns with your strategic objectives.
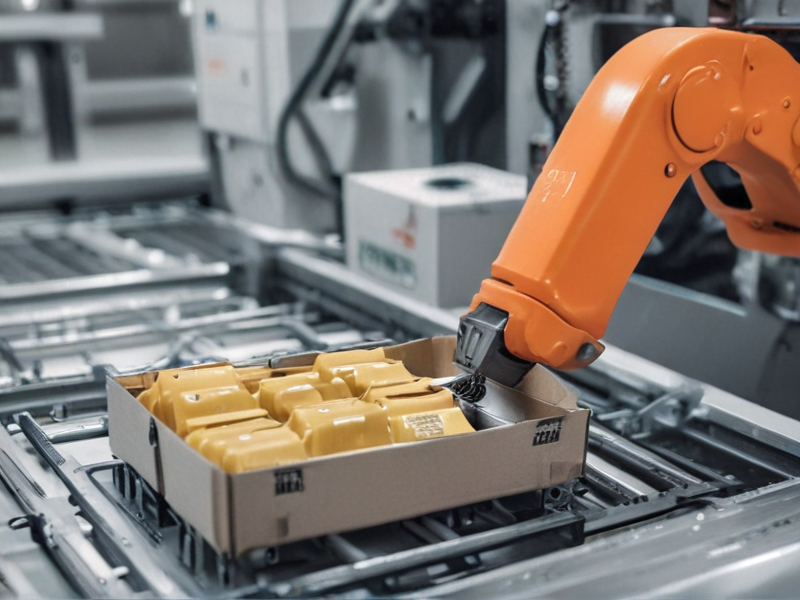
FAQs on Sourcing and Manufacturing primary packaging automation in China
**FAQs on Sourcing and Manufacturing Primary Packaging Automation in China**
1. **Why Source Primary Packaging Automation from China?**
– **Cost Efficiency**: Competitive pricing due to lower labor and production costs.
– **Advanced Manufacturing**: Growing expertise in advanced manufacturing technologies and automation.
– **Scalability**: Ability to scale production swiftly to meet demand fluctuations.
2. **How to Find Reliable Manufacturers?**
– **Trade Shows**: Attend international trade shows like the Canton Fair.
– **Online Platforms**: Use Alibaba, Made-in-China, and Global Sources to identify and vet potential suppliers.
– **Local Agents**: Engage sourcing agents or consult firms specializing in Chinese manufacturing.
3. **What Should I Consider When Choosing a Manufacturer?**
– **Experience**: Look for manufacturers with a proven track record in packaging automation.
– **Certifications**: Ensure compliance with international standards like ISO, CE, and GMP.
– **Reputation**: Check references, client testimonials, and reviews.
4. **What are the Key Challenges?**
– **Quality Control**: Variability in product quality; necessitates stringent QC processes.
– **Communication**: Language barriers and time zone differences can complicate coordination.
– **Logistics**: Potential delays in shipping and customs.
5. **How Can I Ensure Quality and Compliance?**
– **Inspections**: Regular on-site inspections and audits.
– **Prototypes**: Request and evaluate prototypes before full-scale production.
– **Third-Party Verification**: Use third-party quality control services.
6. **What are The Shipping and Regulatory Considerations?**
– **Logistics Partners**: Collaborate with reliable logistics partners for smooth transit.
– **Customs Compliance**: Ensure all documentation and tariffs are meticulously handled.
– **Regulations**: Stay updated on international trade regulations and tariffs affecting imports.
7. **How to Handle After-Sales Support?**
– **Service Agreements**: Establish clear after-sales service and support agreements.
– **Spare Parts**: Ensure availability and quick dispatch of spare parts.
– **Training**: Arrange for training sessions for your team on using and maintaining the automation systems.