Top 10 accurate packaging system in China introduce,list main products and website if have
Certainly! Here are the top 10 accurate packaging systems in China, including their main products and websites:
1. **Mespack**
– Main Products: Horizontal and vertical form-fill-seal machines.
– Website: [mespack.com](http://www.mespack.com)
2. **Jinming Machinery**
– Main Products: Blown film lines, cast film lines, extrusion laminating lines.
– Website: [jmjj.com](http://www.jmjj.com)
3. **Sunswell Machinery**
– Main Products: Bottling, filling, and packaging systems.
– Website: [sunswell.com](http://www.sunswell.com)
4. **Newamstar**
– Main Products: PET bottle blow molding machines, beverage filling and packaging systems.
– Website: [newamstar.com](http://www.newamstar.com)
5. **Ruian Honetop Machinery**
– Main Products: Tea bag packing machines, granule/powder/liquid packing machines.
– Website: [cntopack.com](http://www.cntopack.com)
6. **Jochamp Machinery**
– Main Products: Cartoning machines, blister packing machines, flow wrapping machines.
– Website: [jochampmachinery.com](http://www.jochampmachinery.com)
7. **Focusmachinery**
– Main Products: Labeling machines, filling machines, capping machines.
– Website: [focusmachinery.com.cn](http://www.focusmachinery.com.cn)
8. **Zhangjiagang Mars Packing Machinery**
– Main Products: Water treatment equipment, beverage filling machines, packaging machines.
– Website: [marsmachinery.com](http://www.marsmachinery.com)
9. **Guangzhou Mingna Packing Machinery**
– Main Products: Vacuum packing machines, liquid packing machines, granule packing machines.
– Website: [mingna-packer.com](http://www.mingna-packer.com)
10. **Shanghai Longteng Technology**
– Main Products: Automatic packaging and printing systems.
– Website: [longteng-tech.com](http://www.longteng-tech.com)
These companies are leading providers in the packaging industry, known for their reliable, high-quality equipment and solutions tailored to various industries.
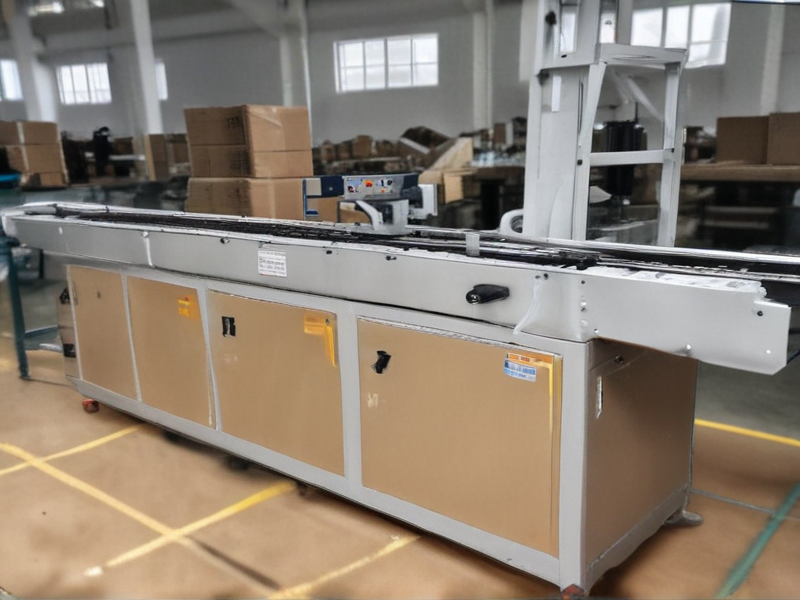
Types of accurate packaging system
Accurate packaging systems are crucial for ensuring product integrity, compliance with regulations, and customer satisfaction. Several types of sophisticated packaging systems are designed to enhance precision and efficiency:
1. **Automated Weighing and Filling Systems**:
These systems use advanced scales and sensors to accurately measure and dispense products into packaging. They are ideal for food items, pharmaceuticals, and chemicals, ensuring that each package meets the specified weight.
2. **Vision Inspection Systems**:
These involve high-resolution cameras and image processing software to inspect packaging for defects, proper labeling, and seal integrity. They are commonly used in industries like cosmetics, electronics, and food to maintain high-quality standards.
3. **Robotic Packaging Systems**:
Incorporating robotic arms and advanced software, these systems enhance precision in tasks such as picking, placing, and packing products. Robotics are widely used in automotive, aerospace, and electronics industries, achieving high efficiency and accuracy.
4. **Blister Packaging Machines**:
Predominantly used in pharmaceutical and consumer goods industries, these machines ensure accurate and tamper-evident packaging. They thermoform blisters and accurately fill them with products, ensuring hermetic seals and compliance with strict regulations.
5. **Flow Wrapping Machines**:
These machines wrap products in clear or printed film, ensuring tight-sealed packages. They are frequently used in food and confectionery sectors to provide accurate and protective wrapping, enhancing shelf life and appeal.
6. **Modified Atmosphere Packaging (MAP) Systems**:
Designed to extend the shelf life of perishable goods, these systems adjust the composition of gases within the packaging. They are commonly used in meat, dairy, and bakery products, ensuring freshness and safety.
**Conclusion**:
Accurate packaging systems are diverse and tailored to specific industry needs. Automated weighing and filling ensure precise quantities, vision inspection maintains quality, robotics enhance efficiency, blister packaging provides security, flow wrapping ensures protection, and MAP systems extend shelf life. Each system contributes significantly to the accurate and efficient packaging process.
Pros and Cons of Using accurate packaging system
Implementing an accurate packaging system offers several advantages and disadvantages. Here’s a concise overview:
### Pros:
1. **Reduced Waste:**
Accurate packaging ensures precise measurement of materials, leading to minimal waste. This can significantly reduce costs, especially in industries dealing with expensive raw materials.
2. **Enhanced Customer Satisfaction:**
Consistently accurate packages meet customer expectations in terms of product quantity and quality, which boosts customer trust and loyalty.
3. **Regulatory Compliance:**
Many industries have strict regulations regarding packaging. An accurate system helps meet these legal standards, avoiding fines and legal issues.
4. **Efficiency:**
Automation and precision in packaging speed up production processes, improving overall operational efficiency.
5. **Resource Optimization:**
Better control over materials can lead to optimal use of resources, lowering material costs and reducing the environmental impact.
### Cons:
1. **High Initial Costs:**
Implementing sophisticated and accurate packaging systems often requires a substantial initial investment in technology and training.
2. **Maintenance:**
Advanced packaging systems require regular maintenance and updates, which can be costly and time-consuming.
3. **Complexity:**
Integrating an accurate packaging system into existing operations can be complex, requiring significant changes in workflows and potentially causing temporary disruptions.
4. **Dependence on Technology:**
Relying heavily on automated accurate systems can make a business vulnerable to technological failures or cyber-attacks, which could halt production.
5. **Skill Requirements:**
Operating and maintaining high-accuracy packaging systems often require skilled personnel, leading to higher labor costs and a need for specialized training.
In conclusion, while accurate packaging systems offer substantial benefits in terms of waste reduction, customer satisfaction, and efficiency, they also come with challenges such as high initial costs, maintenance needs, and complexity. Businesses must weigh these pros and cons to determine if the investment aligns with their operational goals and budget constraints.
accurate packaging system Reference Specifications (varies for different product)
Accurate packaging systems are vital for maintaining product integrity, ensuring safety, and enhancing consumer satisfaction. Here’s an outline of reference specifications, which may vary depending on the product type:
### 1. **Dimensions and Weight**
– **Tolerance:** ±0.5 mm for dimensions and ±0.1 g for weight
– **Specificity:** Adapt packaging size to securely fit the product without excessive space
### 2. **Materials**
– **Quality:** Food-grade, biodegradable, recyclable, or reusable materials
– **Strength:** Appropriate tensile strength (e.g., 20 MPa for plastics), tear resistance, and puncture resistance relative to product type
### 3. **Sealing and Closure**
– **Integrity:** Airtight, moisture-proof, and tamper-evident seals
– **Types:** Heat sealing, adhesive sealing, crimping, or ultrasonic welding
### 4. **Labeling**
– **Clarity:** Legible font (minimum 6 pt), accurate information
– **Durability:** Waterproof, smudge-proof, and resistant to environmental conditions
### 5. **Barcoding and Tracking**
– **Standards:** GS1-compliant barcodes or QR codes for inventory and tracking
– **Application:** Proper placement for easy scanning and minimization of errors
### 6. **Compliance**
– **Regulations:** Adherence to regional and international standards (like FDA, EU, ISO)
– **Certification:** Ensure certifications are up-to-date for materials and processes
### 7. **Environmental Considerations**
– **Sustainability:** Use eco-friendly materials and processes
– **Waste Reduction:** Design for minimal waste and consider reuse or recycling options
### 8. **Performance Testing**
– **Drop Test:** Ensure packaging survives drops from a height of 1 meter
– **Temperature Cycling:** Test for resilience in temperature variations (e.g., -20°C to 50°C)
– **Vibration Test:** Simulate transportation conditions to ensure integrity
### 9. **Customization**
– **Adaptability:** Custom packaging solutions to fit unique product shapes and sizes
– **Innovations:** Incorporate user-friendly features like easy-open tabs, resealable options
Adhering to these specifications helps in achieving consistent quality, efficiency, and reliability in packaging systems, thereby ensuring product safety and customer satisfaction.
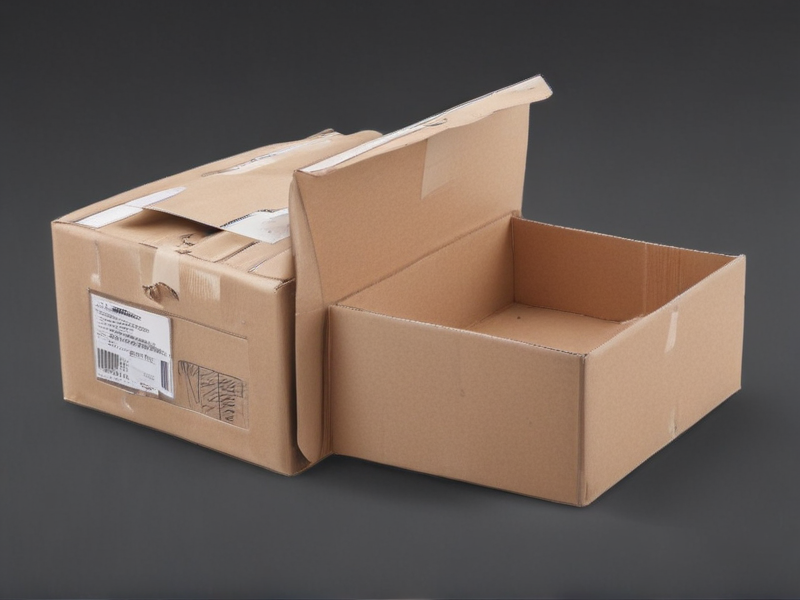
Applications of accurate packaging system
Accurate packaging systems are crucial across various industries, contributing to efficiency, safety, and compliance. Here are key applications:
1. **Food and Beverage Industry**:
Maintaining product safety and extending shelf life are critical. Accurate packaging systems ensure consistent sealing, appropriate portion control, and contamination prevention. This precision minimizes waste and complies with health regulations.
2. **Pharmaceutical Industry**:
Precision in packaging medicines is mandatory for dosage accuracy and patient safety. Automated packaging systems handle various forms including tablets, capsules, and liquids, ensuring tamper-evidence, secure closures, and clear labeling.
3. **Consumer Goods**:
Consistent packaging enhances brand image and customer trust. Accurate systems manage diverse product types and packaging styles efficiently, maintaining uniformity which is crucial for stocking and inventory management.
4. **E-commerce**:
Efficient packaging is essential for safe product delivery and reducing return rates. Automated systems optimize packaging materials and dimensions, balancing protection and cost-effectiveness, resulting in better customer satisfaction and reduced shipping expenses.
5. **Automotive Industry**:
Parts and components need secure and precise packaging to prevent damage during transit. Accurate systems handle varied shapes and sizes, ensuring protection and easy identification, which improves assembly line efficiency.
6. **Medical Devices**:
Sterility and integrity are paramount. Automated packaging systems provide cleanroom-compatible solutions, ensuring devices are contamination-free and properly labeled, which is crucial for regulatory compliance.
7. **Cosmetics**:
Packaging affects preservation and customer appeal. High accuracy ensures aesthetic consistency, proper sealing, and accurate labeling, crucial for branding and consumer safety.
In summary, accurate packaging systems enhance operational efficiency, reduce waste, ensure regulatory compliance, and improve customer satisfaction across multiple sectors. Their role is indispensable in modern industry.
Material of accurate packaging system
Accurate packaging systems are essential for maintaining product quality, ensuring safety, and enhancing consumer satisfaction. The materials used in such systems must exhibit properties that ensure precision, durability, and compatibility with the products they are meant to protect.
1. **Plastics**: Widely used due to their versatility, lightweight nature, and cost-effectiveness. High-density polyethylene (HDPE), polyethylene terephthalate (PET), and polyvinyl chloride (PVC) are common choices. These materials offer excellent barrier properties, protecting products from moisture, oxygen, and contaminants.
2. **Metals**: Tin-coated steel and aluminum are prevalent for packaging foods, beverages, and pharmaceuticals. Metals provide superior protection against environmental factors such as light, air, and pests while also being recyclable.
3. **Glass**: Known for its impermeability and inert nature, glass is ideal for products like beverages, cosmetics, and pharmaceuticals. It’s non-reactive, ensuring that the contents remain intact and unaltered over time.
4. **Paper and Cardboard**: Paper-based materials are excellent for eco-friendly packaging. They are biodegradable, recyclable, and offer good printability for logos and information, making them suitable for secondary packaging and lightweight goods.
5. **Foam**: Often used in cushioning delicate items, polyurethane foam, and expanded polystyrene (EPS) can prevent damage during transit. They are integral to protecting electronics, medical devices, and other fragile products.
6. **Biodegradable Materials**: Polylactic acid (PLA) and other bioplastics are becoming popular as an environmentally conscious alternative. These materials reduce the carbon footprint and address consumer demand for sustainable packaging.
Each material has its particular advantages and limitations. The choice of material largely depends on the product’s nature, the required shelf-life, and specific transportation and storage conditions. Accurate packaging systems meticulously combine these materials to deliver optimal performance and sustainability.
Quality Testing Methods for accurate packaging system and how to control the quality
Ensuring accurate packaging requires several quality testing methods and control mechanisms. Here are key strategies:
1. **Visual Inspection**: Regular visual checks can identify obvious defects such as incorrect labeling, leakage, or damage. Automated vision systems enhance consistency.
2. **Weight Checking**: Automated scales confirm that package contents meet specified weight standards, ensuring no underfilling or overfilling issues.
3. **Seal Integrity Testing**: Methods like vacuum seal testers or dye penetration tests can verify that seals are airtight, crucial for product freshness and contamination prevention.
4. **Drop Testing**: Simulating handling impacts through drop tests assesses whether packaging can withstand transportation and handling stresses.
5. **Temperature and Humidity Control**: Monitoring and controlling the environment can prevent packaging deformities caused by temperature and humidity fluctuations.
6. **Barcode Verification**: Ensuring barcodes are printed clearly and correctly scanned helps maintain inventory accuracy and streamlines distribution.
7. **Material Testing**: Conduct tests on packaging materials for strength, flexibility, and chemical compatibility to ensure they meet required standards.
Controlling quality involves implementing a robust Quality Management System (QMS) with the following practices:
1. **Standard Operating Procedures (SOPs)**: Develop detailed SOPs for every packaging process to ensure consistent practices.
2. **Employee Training**: Regularly train staff on quality standards and proper procedures.
3. **Supplier Quality Audits**: Continuously evaluate suppliers to ensure they meet your quality requirements for packaging materials.
4. **Process Optimization**: Utilize statistical process control (SPC) to monitor production processes and identify variations that could indicate quality issues.
5. **Regular Quality Audits**: Conduct internal audits and inspections to identify and rectify any deviations from quality standards.
6. **Corrective Action Plans**: Implement systems for documenting and addressing quality issues promptly to prevent recurrence.
By integrating these testing methods and control mechanisms, companies can ensure the accuracy and quality of their packaging systems, enhancing product reliability and customer satisfaction.
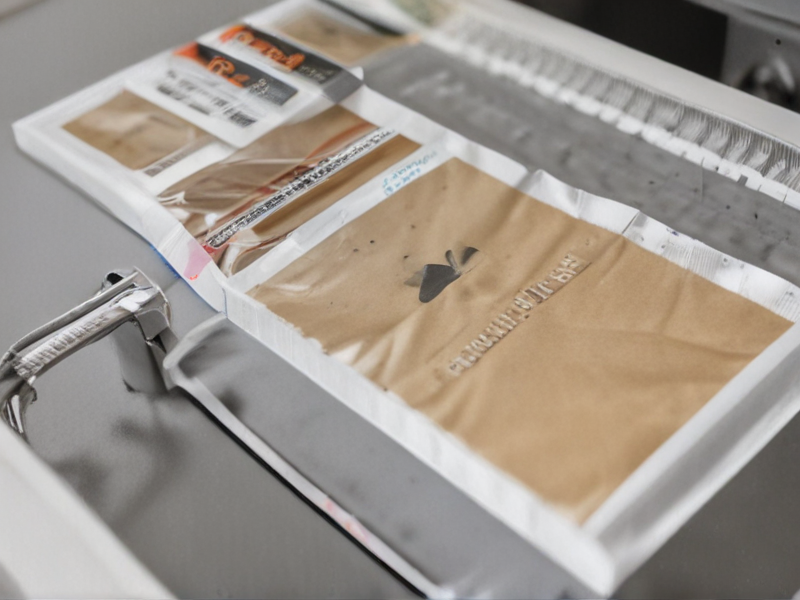
The Work Process and how to use accurate packaging system
An efficient work process in packaging is vital for ensuring product safety, enhancing brand image, and optimizing logistics. Here’s a brief guide:
1. **Assessment and Planning**:
– **Needs Analysis**: Determine product dimensions, weight, fragility, and transportation conditions.
– **Material Selection**: Choose packaging materials that offer adequate protection and alignment with sustainability goals.
2. **Design and Prototyping**:
– **Structural Design**: Create packaging that balances protection with cost-efficiency using CAD software.
– **Prototype Testing**: Develop prototypes and subject them to stress tests to evaluate durability and performance.
3. **Production Setup**:
– **Machinery Configuration**: Set up and calibrate packaging machinery (e.g., automated filling, sealing machines) for consistency.
– **Quality Control (QC)**: Establish QC checkpoints to inspect materials and packaging integrity.
4. **Execution**:
– **Automated Systems**: Utilize automated systems for precision in filling, sealing, and labeling. Automation minimizes human error and speeds up the process.
– **Operator Training**: Ensure operators are trained for efficient machine use and troubleshooting.
5. **Quality Assurance**:
– **Consistent Monitoring**: Regularly monitor the packaging line for defects and compliance with standards.
– **Feedback Loop**: Implement a feedback mechanism for continuous improvement.
6. **Logistics and Inventory Management**:
– **Efficient Stacking**: Use accurate measurements to optimize pallet configurations and storage space.
– **Barcode Systems**: Utilize barcode/RFID systems for real-time tracking and inventory control.
7. **Sustainability Practices**:
– **Material Optimization**: Minimize waste by optimizing material usage and recycling.
– **Eco-friendly Alternatives**: Shift towards biodegradable or recyclable packaging materials.
Using these steps ensures an accurate and efficient packaging process, improving product quality, operational efficiency, and customer satisfaction while supporting sustainability initiatives.
accurate packaging system Importing questions including Cost,Supplier,Sample,Certification and Market
When considering the import of an accurate packaging system, several key factors should be addressed to ensure a smooth and cost-effective process. Below are critical questions to guide your assessment:
### Cost
– **Initial Purchase**: What is the cost of the packaging system unit? Are there bulk purchase discounts available?
– **Shipping and Handling**: What are the shipping costs, and does the supplier cover insurance for transit damages?
– **Additional Charges**: Are there any hidden costs such as taxes, import duties, or handling fees?
### Supplier
– **Reputation**: Is the supplier reputable, and do they have positive reviews or testimonials?
– **Experience**: How long has the supplier been in the industry? Do they have experience exporting to your country?
– **Support Services**: Do they offer after-sales support, maintenance, and technical assistance?
### Sample
– **Availability**: Can the supplier provide a sample unit for evaluation?
– **Cost of Sample**: Is the sample free, or do you need to pay for it, and will the cost be deducted from future orders?
– **Trial Period**: Is there an opportunity for a trial period or demonstration of the packaging system?
### Certification
– **Compliance**: Does the packaging system comply with international standards such as ISO, CE, or specific local regulations?
– **Quality Assurance**: Does the supplier provide certification of quality control procedures and materials used?
– **Warranty**: What are the warranty terms offered by the supplier for the packaging system?
### Market
– **Demand**: Is there a demand for such a packaging system in your local market?
– **Competitors**: Who are your main competitors, and what packaging systems do they use?
– **Return on Investment**: Can you estimate the ROI of purchasing the packaging system based on current market prices and projected demand?
Thoroughly exploring these questions will provide a solid foundation for making an informed decision about importing an accurate packaging system.
How to find and select check reliable accurate packaging system manufacturers in China
Finding and selecting reliable and accurate packaging system manufacturers in China involves a systematic approach:
1. **Research**:
– Use online platforms like Alibaba, Made-in-China, and Global Sources.
– Look for manufacturers with high ratings, good reviews, and verified statuses.
2. **Certifications & Standards**:
– Check for ISO 9001 certification which ensures quality management.
– Look for compliance with international standards like CE, UL, and FDA, depending on your industry.
3. **Experience**:
– Prefer manufacturers with a long history and experience in the industry.
– Evaluate their expertise in the specific type of packaging system you need.
4. **References & Reviews**:
– Request references from past clients.
– Read detailed reviews and case studies.
5. **Factory Audit**:
– Conduct or hire a third-party to perform a factory audit.
– Check their production capabilities, quality control processes, and working conditions.
6. **Sample Testing**:
– Ask for samples to test the reliability and accuracy of their products.
– Conduct thorough testing to ensure they meet your requirements.
7. **Communication**:
– Gauge the responsiveness and clarity of their communication.
– Determine their ability to understand and cater to your specific needs.
8. **After-Sales Service**:
– Inquire about their warranty, maintenance, and support services.
– Ensure they provide technical support and spare parts availability.
By following these steps, you can identify and select a reliable packaging system manufacturer in China, ensuring quality and efficiency in your operations.
Background Research for accurate packaging system manufacturers Companies in China, use qcc.com archive.org importyeti.com
To identify accurate packaging system manufacturers in China, several resources can be utilized for comprehensive research:
1. **Qichacha (qcc.com)**:
– Qichacha is a renowned corporate information platform in China, providing detailed company profiles, financials, and legal records. Using Qichacha, you can search for packaging system manufacturers and vet their legitimacy, operational scale, and market reputation.
Example Companies:
– **Guangdong Zhonghe Machinery Co., Ltd.**: Specializes in automated packaging machines and systems.
– **Shanghai Boevan Packaging Machinery Co., Ltd.**: Known for their high-speed packaging lines and innovation.
2. **Archive.org**:
– By accessing historical records and archived websites, you may track the evolution of specific companies, their product offerings, and customer feedback over time. This can help you understand long-term performance and reliability.
Example Search:
– Historical snapshots of the websites of key manufacturers like **Hangzhou Youngsun Intelligent Equipment Co., Ltd.** can provide insights into their product development history and changes in business strategy.
3. **ImportYeti.com**:
– ImportYeti provides access to U.S. import data, revealing trade patterns and major importers from China. This data can be useful to identify which packaging system manufacturers are actively exporting to significant markets, indicating global trust and compliance with international standards.
Example Data Findings:
– **Wenzhou Zhonghuan Packaging Machinery Co., Ltd.**: Frequently appears in import data for its diverse packaging solutions, indicating a strong presence in the international market.
These platforms together ensure a rounded perspective on manufacturing companies, aiding in making an informed decision:
1. **Guangdong Zhonghe Machinery Co., Ltd.**
2. **Shanghai Boevan Packaging Machinery Co., Ltd.**
3. **Hangzhou Youngsun Intelligent Equipment Co., Ltd.**
4. **Wenzhou Zhonghuan Packaging Machinery Co., Ltd.**
This layered approach ensures that the identified manufacturers are not only operationally sound but also have a proven track record in delivering quality packaging systems globally.
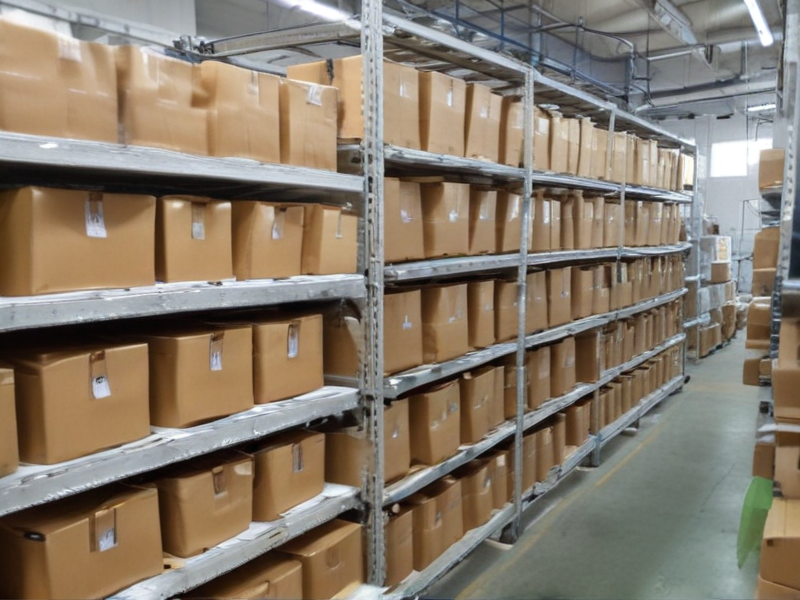
Price Cost Research for accurate packaging system manufacturers Companies in China, use temu.com and 1688.com
Certainly! Here’s a concise overview of the pricing and cost research for accurate packaging system manufacturers in China, using data from temu.com and 1688.com:
### Temu.com
1. **Company A:**
– Product: High-precision automatic packaging machine
– Price Range: $8,000 – $12,000
– Features: Touchscreen interface, high-speed sealing, customizable settings
– MOQ: 1 unit
2. **Company B:**
– Product: Multi-functional packaging system
– Price Range: $5,000 – $10,000
– Features: Versatility in packaging materials, automated weighting system
– MOQ: 1 unit
3. **Company C:**
– Product: Vertical Form Fill Seal (VFFS) machines
– Price Range: $3,500 – $7,500
– Features: Compact design, energy-efficient, rapid operation
– MOQ: 1 unit
### 1688.com
1. **Company D:**
– Product: Automatic Vacuum Packaging Machine
– Price Range: Â¥25,000 – Â¥40,000 (approx. $3,900 – $6,200)
– Features: Stainless steel body, vacuum and gas flushing
– MOQ: 1 unit
2. **Company E:**
– Product: Horizontal Flow Wrapping Machine
– Price Range: Â¥18,000 – Â¥35,000 (approx. $2,800 – $5,500)
– Features: High precision, customizable wrapping styles
– MOQ: 1 unit
3. **Company F:**
– Product: Tray Sealing Machine
– Price Range: Â¥15,000 – Â¥30,000 (approx. $2,300 – $4,600)
– Features: Automatic tray feeding, precise sealing
– MOQ: 1 unit
### Summary
– **temu.com** provides higher-end machinery with a broader price range, allowing for robust features and technologies.
– **1688.com** offers competitive pricing, making it attractive for smaller-scale operations without sacrificing essential functionalities.
### Recommendations
1. **Budget and Scale:** Smaller businesses may benefit from the competitive prices on 1688.com, while larger operations can explore the advanced features on temu.com.
2. **MOQ Consideration:** Both platforms generally have low MOQ requirements, making it easier to start small and scale as needed.
By combining insights from both websites, you can find cost-effective and high-quality packaging solutions tailored to your specific needs.
Shipping Cost for accurate packaging system import from China
When importing an accurate packaging system from China, various factors affect shipping costs. Here are some key considerations to help you estimate the expenses:
1. **Shipping Method**: Options include air freight, sea freight, and express services like DHL, FedEx, or UPS. Air freight is faster but more expensive, whereas sea freight is cost-effective for large, heavy items but slower.
2. **Weight and Dimensions**: The cost depends significantly on the size and weight of the cargo. Larger and heavier packages incur higher shipping fees. Ensure you have precise measurements of your packaging system.
3. **Incoterms**: Determine the Incoterms (International Commercial Terms) that specify who bears the cost and risk during transit. Common terms include FOB (Free on Board) and CIF (Cost, Insurance, and Freight). FOB means you handle shipping costs once the goods are on board, while CIF includes shipping to the destination port.
4. **Destination and Origin**: The geographical locations of the origin (China) and the destination country affect costs. Longer distances and less common routes typically cost more.
5. **Customs and Duties**: Budget for tariffs, duties, and taxes imposed by the destination country. These charges vary by product category and destination.
6. **Insurance**: Protect your investment with shipping insurance. Costs vary, so obtain quotes from different providers.
7. **Freight Forwarder**: Using a freight forwarder can simplify the process. They offer consolidation services, reducing costs for smaller shipments.
8. **Additional Fees**: Be prepared for potential additional costs such as packaging, documentation, handling, and storage fees.
### Example Cost Estimation
– **Packaging System Weight**: 500 kg
– **Dimensions**: 3m x 2m x 2m
– **Shipping Method**: Sea Freight
– **Route**: Shanghai, China to Los Angeles, USA
Estimated Sea Freight Cost:
– **Shipping Fee**: $1,200 – $1,500
– **Customs Duties**: Varies (e.g., 3-5%)
– **Insurance**: Approximately $100
– **Additional Fees**: $200 – $300
### Total Estimated Cost:
Approximately **$1,500 – $2,000** excluding duties and taxes.
Accurate quotes will depend on the specifics of your shipment. Consulting with a shipping expert or freight forwarder is advisable for precise calculations.
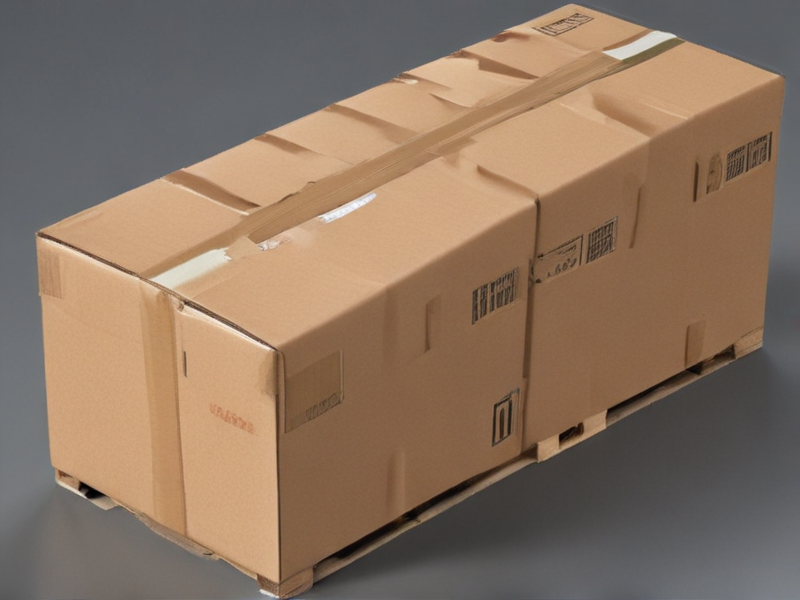
Compare China and Other accurate packaging system Markets: Products Quality and Price,Visible and Hidden Costs
When comparing the packaging system markets of China and other major regions like the U.S. and Europe, several factors come into play: product quality and price, visible and hidden costs.
### Product Quality and Price
**China**: Chinese packaging systems are often cost-effective, primarily due to cheaper labor and lower production costs. While high-quality options are available, there is a wide range, and some manufacturers may cut corners, impacting the consistency of quality.
**U.S. and Europe**: Generally, packaging systems from these regions are perceived as higher quality. Stricter regulations and higher manufacturing standards largely contribute to this. However, this quality comes at a premium, making Western-made systems more expensive than their Chinese counterparts.
### Visible Costs
**China**: Initial purchase costs are typically lower in China. This includes cheaper raw materials and lower labor charges, which can be enticing for companies looking to minimize capital investment.
**U.S. and Europe**: The upfront costs are higher due to more expensive labor, better materials, and stringent safety and quality standards.
### Hidden Costs
**China**: The hidden expenses can include longer lead times and higher shipping costs due to distance. Quality control issues may also lead to increased costs in repairs or replacements. There can be additional expenses in ensuring compliance with local standards when importing.
**U.S. and Europe**: While the initial costs are higher, hidden costs tend to be lower. Products often come with comprehensive warranties and after-sales customer service. Shorter supply chains and quicker response times reduce operational downtime, and adherence to international standards minimizes regulatory compliance issues.
### Conclusion
In summary, Chinese packaging systems are generally cheaper but may come with variability in quality and potentially higher hidden costs. Conversely, Western systems offer higher quality and more predictable hidden costs but demand substantial upfront investment. Your choice depends on your budget, tolerance for risk, and specific quality requirements.
Custom Private Labeling and Branding Opportunities with Chinese accurate packaging system Manufacturers
Engaging with Chinese manufacturers for custom private labeling and branding of packaging systems presents a myriad of opportunities for businesses seeking to enhance their product offerings and market presence. These opportunities are particularly appealing due to the technological advancements, cost-efficiency, and high standards maintained by Chinese manufacturers.
1. **Technological Expertise**: Chinese manufacturers have made significant strides in adopting cutting-edge technologies. They offer advanced and accurate packaging systems, which ensure precision in product packaging. This expertise enhances product integrity and shelf appeal, critical for brand differentiation.
2. **Cost-Effectiveness**: One of the most attractive aspects of partnering with Chinese manufacturers is the cost efficiency. Lower production costs do not compromise quality, enabling businesses to maintain competitive pricing while enjoying substantial profit margins. This affordability extends to custom and private labeling, allowing for sophisticated branding at a fraction of the cost compared to other markets.
3. **Customization and Flexibility**: Chinese manufacturers are highly adaptable to specific client needs. They offer extensive customization options, including unique packaging designs, materials, and sizes tailored to a brand’s identity. This flexibility supports distinctive branding strategies that resonate with target audiences.
4. **Scalability**: Whether you are a startup or an established business, Chinese manufacturers provide scalable solutions. Bulk production capabilities ensure that as your demand grows, the supply chain remains consistent, supporting market expansion and preventing stock shortages.
5. **Quality Assurance**: Despite the competitive pricing, Chinese manufacturers adhere to strict quality control standards. Certifications like ISO, GMP, and others are prevalent, ensuring the packaging systems meet international quality benchmarks.
6. **Innovation and Sustainability**: Many Chinese companies are at the forefront of innovative, environmentally friendly packaging solutions. This aligns with the increasing consumer demand for sustainable packaging, thereby enhancing brand reputation and customer loyalty.
By leveraging these advantages, businesses can significantly optimize their packaging operations, enhance brand appeal, and achieve greater market penetration efficiently and effectively.
Tips for Procurement and Considerations when Purchasing accurate packaging system
When procuring an accurate packaging system, there are several vital considerations to ensure efficiency and long-term value.
1. **Define Requirements**: Clearly outline the product specifications, packaging materials, and process requirements. Ensure the system aligns with your specific needs, such as speed, volume, and product type.
2. **Budgeting**: Determine a realistic budget that factors in initial costs, installation, training, and ongoing maintenance. Opt for a system that offers the best cost-benefit ratio, not just the cheapest option.
3. **Quality and Accuracy**: Accuracy in packaging is critical to avoid waste and maintain product integrity. Evaluate systems known for precision and consistency.
4. **Scalability and Flexibility**: Choose a system that can adapt to future changes, such as increased production volumes or new product lines. Flexibility in handling various packaging sizes and types is a plus.
5. **Technology Integration**: Ensure the system integrates seamlessly with your existing ERP or manufacturing execution systems for streamlined operations and data accuracy.
6. **Supplier Reputation**: Consider suppliers with strong industry reputations and positive customer feedback. Their expertise and reliability can significantly impact your system’s performance.
7. **After-Sales Support**: Robust after-sales support, including training, maintenance, and readily available spare parts, is crucial. A supplier with local service centers can reduce downtime.
8. **Compliance and Safety**: Ensure the packaging system complies with relevant regulatory standards. Safety features should protect operators from potential hazards.
9. **Energy Efficiency**: Opt for energy-efficient systems to reduce operational costs and enhance sustainability.
10. **Total Cost Ownership (TCO)**: Look beyond the purchase price; consider the TCO, including energy use, maintenance, and potential downtime.
By meticulously evaluating these factors, you can select an accurate packaging system that meets your specific needs and offers long-term operational benefits.
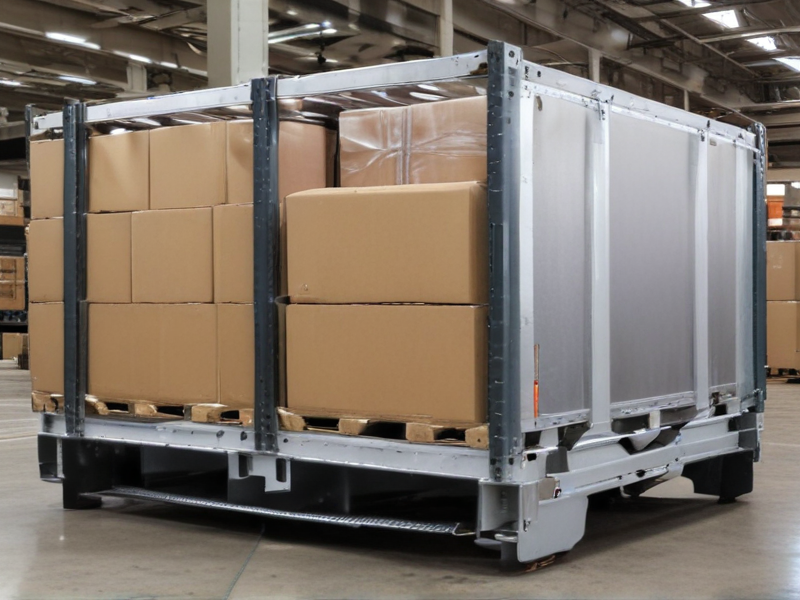
FAQs on Sourcing and Manufacturing accurate packaging system in China
**FAQs on Sourcing and Manufacturing Accurate Packaging Systems in China**
**1. Why Source Packaging Systems from China?**
China offers a competitive edge in terms of cost, advanced manufacturing capabilities, and a wide range of materials. The country’s infrastructure supports large-scale production, making it ideal for high-volume orders.
**2. How to Find Reliable Suppliers?**
Utilize platforms like Alibaba, Global Sources, and Made-in-China. Attend trade shows such as the Canton Fair. Verify suppliers through third-party audit companies and request samples before finalizing contracts.
**3. What are the Key Considerations?**
– **Quality Control**: Ensure the supplier has robust QC processes.
– **Certifications**: ISO, CE, and other relevant certifications.
– **Compliance**: Make sure the packaging meets international standards and regulations.
– **MOQ**: Understand the minimum order quantity requirements.
**4. How to Ensure Quality?**
– Conduct factory audits.
– Employ third-party inspection services.
– Maintain clear communication and detailed product specifications.
**5. What is the Typical Lead Time?**
Lead times can vary but expect 4-12 weeks, depending on the complexity and customization level. Confirm this during negotiations to align with your timelines.
**6. How are Payments Structured?**
Standard practices include a 30% deposit before production and 70% upon shipment. Payment methods often accepted are T/T (Telegraphic Transfer), L/C (Letter of Credit), and sometimes PayPal for smaller orders.
**7. What Shipping Options are Available?**
Options include sea freight for large orders, which is cost-effective, and air freight for smaller, urgent shipments. Work with freight forwarders for better rates and logistics management.
**8. Can I Protect My Intellectual Property (IP)?**
Sign Non-Disclosure Agreements (NDAs) and, where possible, register your IP in China. RFQs and contracts should also include clauses that protect your designs and trademarks.
**9. What are Common Challenges?**
– Language barriers.
– Time zone differences.
– Potential for delays.
Mitigate these by hiring local agents or using sourcing services that understand both cultures.
**10. Are There Any Hidden Costs?**
Be aware of costs related to tariffs, duties, and transportation. A clear agreement on Incoterms can help avoid unexpected expenses.
By addressing these questions, businesses can better navigate the complexities of sourcing and manufacturing packaging systems in China.