Top 10 automatic container filling in China introduce,list main products and website if have
Sure! Here’s an introduction to 10 leading automatic container filling machine manufacturers in China, highlighting their main products and including their websites:
1. **Newamstar Packaging Machinery Co., Ltd.**
– **Products:** Beverage filling machines, liquid filling lines, water treatment systems
– **Website:** [newamstar.com](http://www.newamstar.com)
2. **Hangzhou Zhongya Machinery Co., Ltd.**
– **Products:** Tube filling machines, automatic sealing machines, cosmetic filling equipment
– **Website:** [zypack.cn](http://www.zypack.cn)
3. **Guangzhou Lianmeng Machinery Equipment Co., Ltd.**
– **Products:** Automatic filling machines, capping machines, and labeling lines for food and cosmetic industries
– **Website:** [gzlianmeng.com](http://www.gzlianmeng.com)
4. **Shanghai Joygoal Food Machinery Co., Ltd.**
– **Products:** Liquid filling machines, powder filling machines, and vacuum packing machines
– **Website:** [joygoal.net](http://www.joygoal.net)
5. **Zhangjiagang King Machine Co., Ltd.**
– **Products:** Bottle filling lines, water filling machines, juice and carbonated drink filling equipment
– **Website:** [zjgfillingmachine.com](http://www.zjgfillingmachine.com)
6. **Shandong HG Machinery Co., Ltd.**
– **Products:** Beer filling machines, can filling lines, and beverage production equipment
– **Website:** [brewerybeerequipment.com](http://www.brewerybeerequipment.com)
7. **Guangzhou Rifu Packaging Machinery Co., Ltd.**
– **Products:** Liquid filling machines, paste filling machines, automatic capping equipment
– **Website:** [rifumachine.com](http://www.rifumachine.com)
8. **Hefei Zhongchen Light Industrial Machinery Co., Ltd.**
– **Products:** Aerosol filling machines, liquid filling equipment, automated packaging lines
– **Website:** [zhongchenpack.com](http://www.zhongchenpack.com)
9. **Jiangsu Tom Packaging Machinery Co., Ltd.**
– **Products:** Bag filling machines, pouch packing equipment, and vertical form fill seal machines
– **Website:** [tom-mac.com](http://www.tom-mac.com)
10. **Shanghai NPACK Automation Equipment Co., Ltd.**
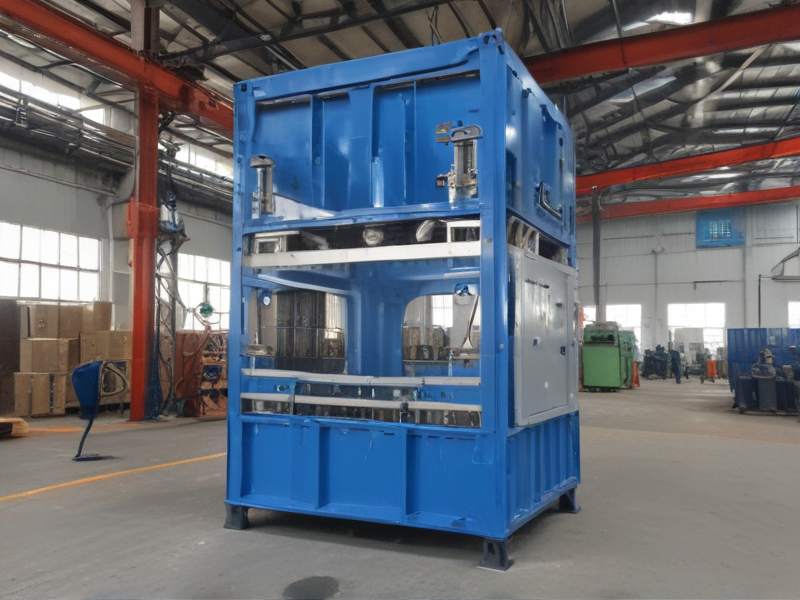
Types of automatic container filling
Automatic container filling machines streamline the process of packaging liquids, powders, and granules into various types of containers. There are several types of automatic filling systems, each designed for specific applications and materials.
1. **Gravity Fillers:**
These utilize gravity to fill containers. Ideal for thin, free-flowing liquids like water and certain chemicals, gravity fillers are simple, cost-effective, and easy to maintain.
2. **Pump Fillers:**
Using different types of pumps (gear, piston, peristaltic), these fillers handle a variety of viscosities. They are versatile, making them suitable for soaps, shampoos, creams, and other thicker substances.
3. **Piston Fillers:**
Leveraging pistons to draw and dispense products, these machines are excellent for thick, viscous materials such as pastes, gels, and some heavy sauces. They ensure precise volume control.
4. **Overflow Filling Machines:**
Overflow fillers provide a consistent fill level regardless of container volume variations. They are typically used for transparent containers where even filling is visually important, such as bottles of beverages or liquid soaps.
5. **Auger Fillers:**
Ideal for powdery products, auger fillers use a rotating screw to dispense precise amounts of product into containers. They are widely used in the food, pharmaceutical, and chemical industries for products like spices, flour, and protein powders.
6. **Vacuum Fillers:**
These machines use a vacuum to draw liquid into the container until it reaches a pre-specified level. Suitable for products like perfumes and volatile liquids, vacuum fillers are highly accurate.
7. **Net Weight Fillers:**
Net weight filling systems measure the weight of the product as it is dispensed into the container, ensuring consistent, precise fills. They are used for bulk products such as granules, seeds, and snacks.
8. **Time-Pressure Fillers:**
These systems dispense product by maintaining a constant pressure and timing the flow, making them suitable for a wide range of liquid viscosities and ensuring consistent volume.
Each type of filler offers distinct advantages depending on the specific requirements of the product and packaging.
Pros and Cons of Using automatic container filling
**Pros of Automatic Container Filling:**
1. **Efficiency and Speed:** Automatic systems can fill containers much faster than manual labor, increasing the overall production rate.
2. **Consistency and Accuracy:** Automation ensures uniform filling levels and reduces the risk of human error, ensuring product quality.
3. **Labor Cost Reduction:** Automation minimizes the need for manual labor, leading to significant cost savings in wages and associated expenses.
4. **Reduced Waste:** Precise filling reduces overfilling and spillage, leading to less waste and lower material costs.
5. **Improved Safety:** Automation reduces the risk of workplace injuries by limiting the need for manual handling of potentially hazardous substances.
6. **Scalability:** Automated systems can easily be scaled up to meet increasing production demands without the need for proportional increases in labor.
7. **Data Collection:** Automated systems often come with integrated data collection capabilities, enabling better monitoring and process optimization.
**Cons of Automatic Container Filling:**
1. **High Initial Investment:** The cost of purchasing and installing automatic filling machinery can be substantial.
2. **Maintenance and Repairs:** Automated machines require regular maintenance and can be costly to repair, adding to ongoing operational expenses.
3. **Technical Issues:** Machines can face malfunctions or technical glitches, leading to downtime and potential production delays.
4. **Employee Training:** Employees need training to operate and maintain automatic systems, which can incur additional expenses and time.
5. **Flexibility Limitations:** Automated systems may lack the flexibility to handle small, customized production runs as efficiently as manual labor.
6. **Energy Consumption:** Automated filling machines often consume significant amounts of energy, which can increase operational costs.
7. **Redundancy for Existing Labor:** Automation can lead to job displacement, creating concerns among the existing workforce about job security and morale.
In summary, while automatic container filling offers significant advantages in terms of efficiency, consistency, and cost savings, it also comes with notable challenges, such as high initial investment and maintenance requirements. Assessing these factors is crucial for determining whether automation is a suitable solution for a given operation.
automatic container filling Reference Specifications (varies for different product)
Automatic container filling systems are crucial in various industries, ensuring precision, efficiency, and speed. Below are typical reference specifications to consider, though they can vary based on the product being filled:
1. **Filling Capacity**:
– **Volume Range**: 10 mL to 10,000 mL per container.
– **Containers per Minute**: 20 to 200, depending on the machine and product specifications.
2. **Types of Products**:
– **Liquids**: Water, oils, juices, detergents.
– **Semi-liquids**: Sauces, creams, gels.
– **Granular & Powdered**: Flour, sugar, pharmaceutical powders.
– **Viscous Products**: Honey, pastes, syrups.
3. **Filling Mechanisms**:
– **Gravity Fillers**: Ideal for free-flowing liquids.
– **Piston Fillers**: Suitable for semi-viscous and viscous products.
– **Pump Fillers**: Versatile for handling various viscosities.
– **Auger Fillers**: Designed for powders and granular products.
4. **Accuracy & Precision**:
– **Standard Volume Deviation**: ± 0.5% to 1% of the target volume.
– **Weight Deviation**: ± 1 gram to ± 5 grams, depending on product and container size.
5. **Material Compatibility**:
– **Contact Materials**: Stainless steel (304/316) for food and pharmaceutical applications.
– **Corrosion Resistance**: For acidic or harsh chemical products.
6. **Automation & Control**:
– **Control System**: PLC (Programmable Logic Controller) with touch screen interface.
– **Sensors**: To detect container presence and alignment.
– **Integration**: Capable of interfacing with upstream and downstream equipment (e.g., conveyors, labeling machines).
7. **Container Types**:
– **Shapes and Sizes**: Bottles, jars, cans, pouches.
– **Materials**: Plastic, glass, metal.
8. **Compliance & Safety**:
– **Regulatory Standards**: FDA, GMP, CE, depending on industry.
– **Safety Features**: Emergency stop functions, guarding, and interlocks.
9. **Maintenance & Cleaning**:
– **CIP (Clean-In-Place)**: For ease of cleaning internal components.
– **Tool-Free Changeover**: For quick adaptation to different container sizes and products.
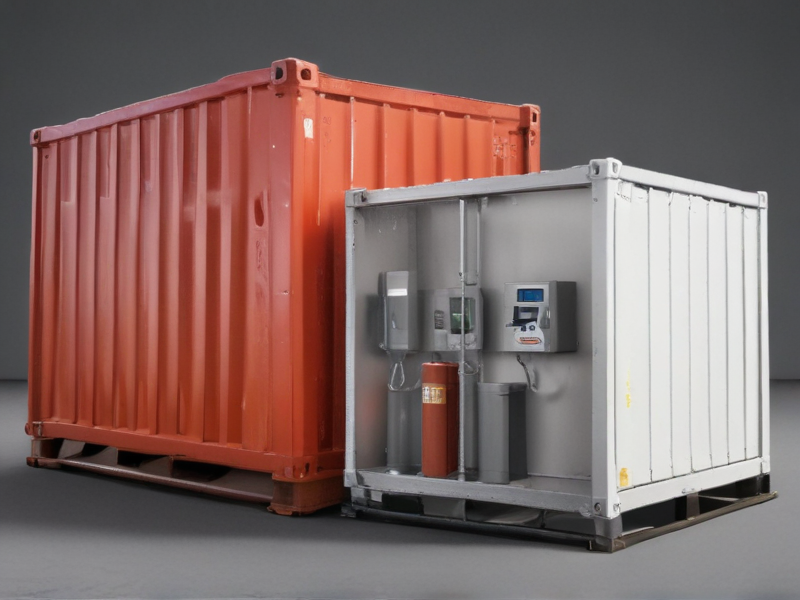
Applications of automatic container filling
Automatic container filling systems have revolutionized various industries by offering precision, efficiency, and consistency. Here are some primary applications:
1. **Food and Beverage Industry**: Automatic filling machines are widely used to fill bottles, cans, and jars with liquids such as water, soda, juice, sauces, and oils. They ensure that each container is filled to the exact specified level, minimizing wastage and ensuring quality control.
2. **Pharmaceutical Industry**: Precision is crucial when dealing with medications. Automatic filling machines are employed to fill capsules and liquid medications into bottles accurately, ensuring dosage accuracy and maintaining sterile conditions.
3. **Cosmetics and Personal Care**: These machines are used to fill a variety of containers with products like shampoos, lotions, perfumes, and creams. They handle different viscosities and container types, ensuring product consistency and packaging integrity.
4. **Chemical Industry**: Whether it’s industrial chemicals, cleaning agents, or pesticides, automatic fillers ensure safe and precise dispensing, minimizing human exposure and improving workplace safety.
5. **Petroleum and Lubricants**: In this sector, automated systems are used to fill oil, lubricants, and other petroleum products into various containers, ensuring accurate measurement and reducing spillage.
6. **Agriculture**: Automatic filling equipment helps package seeds, fertilizers, and animal feed into bags or containers with accuracy, promoting efficiency in the supply chain.
7. **E-Commerce and Retail**: With the rise of e-commerce, automatic filling machines facilitate the mass packaging of goods, ensuring that each package contains the right amount of product, thus streamlining the logistics and delivery process.
By integrating automation into the container filling process, businesses can enjoy enhanced productivity, reduced labor costs, and a significant improvement in product consistency and safety.
Material of automatic container filling
Automatic container filling systems are crucial components in various industries like food and beverages, pharmaceuticals, and chemicals. The material choice for these systems is critical to ensure durability, hygiene, and compatibility with the substances being filled. Common materials include:
1. **Stainless Steel**:
– **Grades**: Typically, 304 or 316 stainless steel.
– **Advantages**: Resistant to corrosion, easy to clean, and maintains integrity under different temperatures and pressures.
– **Applications**: Widely used in food and beverage industries for its hygiene and stringent regulatory compliance.
2. **Plastic**:
– **Types**: High-Density Polyethylene (HDPE), Polypropylene (PP), and Polyvinyl Chloride (PVC).
– **Advantages**: Lightweight, cost-effective, and resistant to various chemicals.
– **Applications**: Suitable for specific non-food applications like chemical distribution where metal could be reactive or overly costly.
3. **Glass**:
– **Advantages**: Non-reactive surface, transparency for easy monitoring, and high chemical resistance.
– **Applications**: Used in pharmaceutical industries for products that require high purity standards and minimal contamination risk.
4. **Aluminum**:
– **Advantages**: Lightweight, corrosion-resistant, and relatively inexpensive.
– **Applications**: Non-food applications where weight reduction is critical.
5. **Ceramics and Coated Materials**:
– **Advantages**: Highly resilient to aggressive chemicals and high temperatures.
– **Applications**: Specialized sectors like certain chemical processes and high-purity applications.
**Conclusion**:
The selection of material for automatic container filling systems is dictated by the specific requirements of the application, such as chemical compatibility, temperature resistance, food safety regulations, and cost considerations. Stainless steel remains the most versatile and widely used material, particularly in high-hygiene industries.
Quality Testing Methods for automatic container filling and how to control the quality
### Quality Testing Methods for Automatic Container Filling
**1. Vision Systems:**
– **Application:** High-speed cameras combined with image processing software to inspect fill levels.
– **Control:** Real-time adjustments to filling machines if deviations are detected.
**2. Weight Measurement:**
– **Application:** Load cells measure the weight of containers before and after filling.
– **Control:** Automatic feedback loop adjusts filling process based on weight data.
**3. Flow Meters:**
– **Application:** Measure the volume or mass flow of filling material during the process.
– **Control:** Ensures consistent fill by real-time monitoring and adjustments.
**4. Ultrasonic Sensors:**
– **Application:** Non-contact measurement of liquid levels within containers.
– **Control:** Immediate feedback for correction of fill levels, ensuring uniformity.
**5. X-Ray Systems:**
– **Application:** Non-invasive inspection technique to check fill levels inside opaque containers.
– **Control:** Provides data for immediate corrective actions.
### Controlling Quality
**1. Statistical Process Control (SPC):**
– **Description:** Collects data from filling processes to monitor performance and detect anomalies.
– **Implementation:** Uses control charts to trigger adjustments when variations exceed control limits.
**2. Automated Feedback Loops:**
– **Description:** Integrated sensors and measurement tools provide continuous data to control systems.
– **Implementation:** Real-time tweaks based on sensor data ensure accuracy and consistency.
**3. Calibration and Maintenance:**
– **Description:** Regular calibration of sensors and maintenance of machinery.
– **Implementation:** Scheduled checks and servicing to maintain high accuracy and reliability.
**4. Quality Audits:**
– **Description:** Periodic audits of the filling process to ensure compliance with standards.
– **Implementation:** Reviews by quality control teams and documentation of findings.
**5. Training and SOPs:**
– **Description:** Comprehensive training for operators and well-defined Standard Operating Procedures (SOPs).
– **Implementation:** Continuous education and adherence to SOPs for maintaining consistent quality.
By integrating these testing methods and quality control measures, the automatic container filling process can achieve high precision, reliability, and compliance with quality standards.
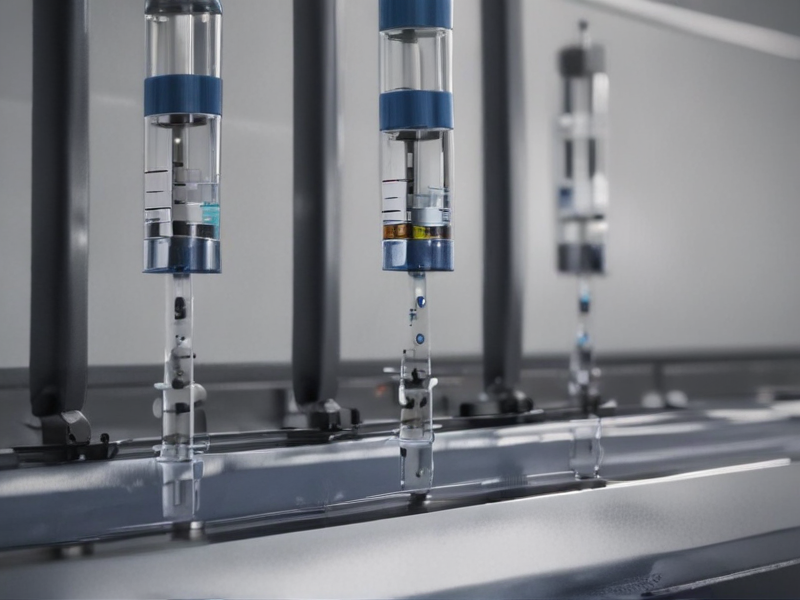
The Work Process and how to use automatic container filling
### Work Process and Automatic Container Filling
**1. Setup and Calibration:**
– **Placement:** Arrange the filling machine on a stable surface near the bulk product source.
– **Connection:** Connect the machine to the power supply and, if necessary, to the compressed air supply.
– **Calibration:** Set the machine to dispense the desired quantity by adjusting the parameters on the control panel. Run a few test fills and measure the output to ensure accuracy.
**2. Loading Containers:**
– **Positioning:** Place empty containers on the conveyor belt or filling station.
– **Alignment:** Ensure containers are correctly aligned under the filling nozzles to avoid spillage and ensure uniform filling.
**3. Automatic Filling Process:**
– **Activation:** Start the machine from the control panel or via automation software.
– **Dispensing:** The machine uses sensors to detect the container’s position and starts dispensing the product. The filling can be done by various methods like gravity, pressure, or pump, depending on the product and machine type.
– **Shutoff:** The machine stops filling once the preset quantity is reached, using weight sensors or volume measurements.
**4. Quality Control:**
– **Monitoring:** Continuously monitor the filling process using visual checks or automated systems.
– **Adjustment:** Make real-time adjustments if discrepancies in fill levels are noticed.
**5. Post-Filling:**
– **Capping:** After filling, containers often move to the capping station where lids are applied.
– **Labeling:** Containers may then proceed to labeling for identification and branding.
– **Packaging:** Finally, filled containers are collected and packed for distribution.
**6. Maintenance and Safety:**
– **Routine Checks:** Regularly clean and inspect the machine to prevent contamination and mechanical issues.
– **Safety Protocols:** Follow safety guidelines to prevent accidents, including proper shutdown procedures during maintenance.
Using an automatic container filling machine enhances efficiency, consistency, and safety in the production process. Proper setup, monitoring, and maintenance are crucial for optimal performance.
automatic container filling Importing questions including Cost,Supplier,Sample,Certification and Market
Importing automatic container filling machines involves several key considerations:
1. **Cost**: The cost of an automatic container filling machine can vary significantly based on its capacity, automation level, brand, and features. Basic models might start around $10,000, while high-end, fully automated systems can exceed $100,000. Be sure to include shipping fees, import duties, taxes, and possible installation costs in your budget.
2. **Supplier**: Research and identify reputable suppliers. Key factors include the supplier’s experience, customer reviews, and after-sales support. Consider suppliers from countries known for manufacturing industrial machinery, such as Germany, China, and the USA. Trade directories, industry trade shows, and online marketplaces like Alibaba can be valuable resources.
3. **Sample**: Request a sample or a demo of the machine. While not always feasible for large machinery, some suppliers may offer virtual demonstrations, detailed videos, or smaller-scale versions of their machines for testing. This helps ensure the equipment meets your operational requirements and quality standards.
4. **Certification**: Ensure the machinery complies with the relevant certifications and safety standards. This may include ISO certifications, CE marking for machines imported to the European Union, or compliance with UL standards for North America. Certifications ensure the machinery meets safety, quality, and regulatory standards.
5. **Market**: Analyze your target market to ensure there is sufficient demand for the products you plan to produce. Consider factors such as market size, competition, and customer preferences. Conduct a SWOT analysis (Strengths, Weaknesses, Opportunities, Threats) to understand your position and potential challenges.
In summary, while importing automatic container filling machines, thoroughly evaluate costs, choose reputable suppliers, ensure compliance with certifications, request samples if feasible, and conduct comprehensive market research. This approach will help you make informed decisions and ensure a successful investment.
How to find and select check reliable automatic container filling manufacturers in China
Finding and selecting reliable automatic container filling machine manufacturers in China involves several steps. Here’s how to do it concisely:
1. **Research Online**: Use platforms like Alibaba, Global Sources, and Made-in-China to find manufacturers. Filter results by product categories and reviews.
2. **Evaluate Credentials**: Check for certifications such as ISO 9001 and CE, which indicate quality standards. Read customer reviews and ratings to assess reliability.
3. **Check Experience**: Prefer manufacturers with several years of experience and a proven track record in producing automatic container filling machines.
4. **Request Samples**: Ask for product samples or case studies from previous clients to evaluate the machine’s performance and build quality.
5. **Factory Visit**: If feasible, visit the manufacturer’s factory to inspect their production capabilities, quality control processes, and workforce expertise.
6. **Compare Quotes**: Gather detailed quotations from multiple manufacturers. Ensure the quotes include machine specifications, shipping costs, warranty, and after-sales support.
7. **Negotiate Terms**: Discuss payment terms, delivery schedules, and warranty policies. Reliable manufacturers will provide clear, transparent terms.
8. **Seek References**: Request contact details of past clients to obtain firsthand feedback on their experiences with the manufacturer.
9. **Use Third-Party Services**: Employ third-party inspection services to verify the manufacturer’s credibility and quality.
10. **Verify Communication**: Evaluate their responsiveness and communication skills. Reliable manufacturers will respond promptly and address queries effectively.
By following these steps, you can identify and select a reliable automatic container filling machine manufacturer in China.
Background Research for automatic container filling manufacturers Companies in China, use qcc.com archive.org importyeti.com
**Background Research on Automatic Container Filling Manufacturers in China**
**1. Overview of Industry in China:**
China is home to a vast manufacturing sector specializing in automation and packaging machinery, including automatic container filling systems. These systems are crucial in various industries like food and beverage, pharmaceutical, and chemicals for efficiently filling containers with liquids, powders, or granules.
**2. Leading Companies:**
Through qcc.com, a database providing comprehensive company information, several leading manufacturers can be identified:
– **Shanghai Develop Machinery Co., Ltd.:** Specializes in automatic filling and packaging solutions. They offer state-of-the-art technology and customize machines to suit different customer needs.
– **Guangzhou V-Pack Machinery Co., Ltd.:** Known for its high-quality automatic filling machines, integrating advanced technology to ensure precision and reliability.
– **Shenzhen J&D Drinking Water Equipment Co., Ltd.:** Offers a wide range of filling machines particularly for the food and beverage industry.
**3. Import Data Insights:**
Using ImportYeti.com, which analyzes import records to understand trading patterns and relationships:
– **Newamstar Packaging Machinery Co., Ltd.:** Top-tier manufacturer with a significant export volume, indicating their strong presence and reliability in the global market.
– **Higee Machinery (Shanghai) Co., Ltd.:** Known for exporting high-performance automatic filling machines, often seen in import records associated with US and European companies.
**4. Historical Web Data:**
Archive.org provides historical snapshots of these companies’ websites, offering insights into their evolution over the years:
– Many companies have progressively advanced their technology and expanded their product lines, showing a trend towards higher automation and integration of Industry 4.0 principles.
**5. Conclusion:**
China’s automatic container filling machine manufacturers such as Shanghai Develop Machinery, Guangzhou V-Pack, and Shenzhen J&D, stand out due to their advanced technology and significant export volumes. Companies like Newamstar and Higee Machinery further highlight China’s competitive edge in this sector, driven by continuous innovation and high-quality standards.
This concise background captures the key players and industry dynamics essential for understanding the automatic container filling manufacturing landscape in China.
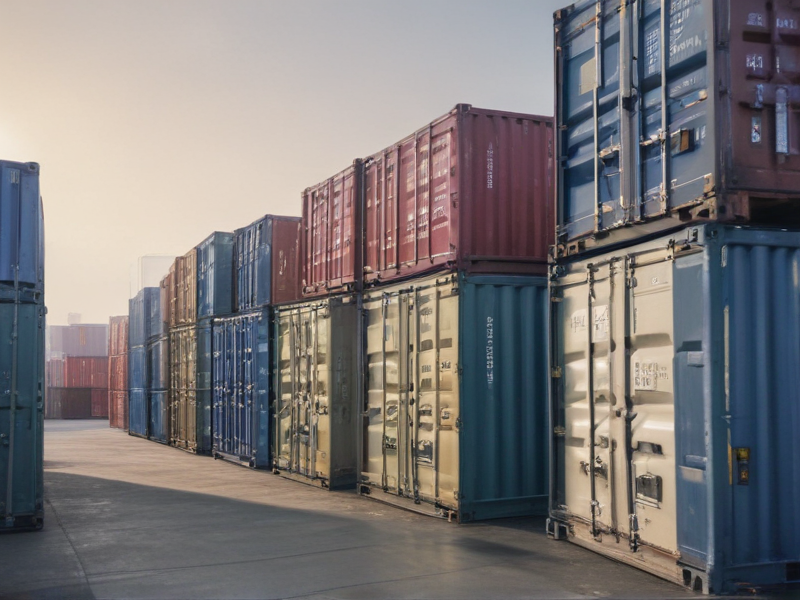
Price Cost Research for automatic container filling manufacturers Companies in China, use temu.com and 1688.com
Sure! Here’s a concise price cost research for automatic container filling manufacturers in China using temu.com and 1688.com:
### 1. **temu.com**
– **Company A**
– **Product**: Automatic Liquid Filling Machine
– **Price**: $3,500 – $5,000 USD per unit
– **Details**: Suitable for liquids such as beverages, chemicals, and pharmaceuticals.
– **Company B**
– **Product**: Automatic Paste Filling Machine
– **Price**: $4,200 – $6,000 USD per unit
– **Details**: Designed for thicker substances, including pastes and gels.
– **Company C**
– **Product**: Multifunctional Filling Machine
– **Price**: $5,800 – $7,500 USD per unit
– **Details**: Can handle both liquid and semi-liquid products with customizable nozzles.
### 2. **1688.com**
– **Company D**
– **产品**: 自动液体灌装机 (Automatic Liquid Filling Machine)
– **价格**: ¥22,000 – ¥35,000 RMB per unit (Approx. $3,200 – $5,000 USD)
– **细节**: 多用于饮料、化工和医药行业。
– **Company E**
– **产品**: 自动膏体灌装机 (Automatic Paste Filling Machine)
– **价格**: ¥28,000 – ¥40,000 RMB per unit (Approx. $4,090 – $5,850 USD)
– **细节**: 适用于粘稠物料,如膏体和凝胶。
– **Company F**
– **产品**: 多功能灌装机 (Multifunctional Filling Machine)
– **价格**: ¥38,000 – ¥50,000 RMB per unit (Approx. $5,550 – $7,300 USD)
– **细节**: 可处理液体和半液体产品,喷嘴可定制。
### Summary
Prices for automatic container filling machines in China range approximately from $3,200 to $7,500 USD per unit. Temu.com and 1688.com offer a variety of options catering to different substances such as liquids, pastes, and gels, with multifunctionality and customization features influencing the price. Currency conversions and additional fees like shipping should be considered for precise budgeting.
Shipping Cost for automatic container filling import from China
Shipping costs for importing an automatic container filling machine from China depend on several factors including the size and weight of the machine, the shipping method, and any additional services required. Here is a detailed breakdown:
### Shipping Methods
1. **Sea Freight**:
– **FCL (Full Container Load)**: Ideal for large shipments.
– **LCL (Less than Container Load)**: Suitable for smaller shipments.
– **Cost Estimate**: $2,000 – $4,000 for a 20-foot container.
2. **Air Freight**:
– Faster but significantly more expensive.
– **Cost Estimate**: $5 – $10 per kilogram.
3. **Rail Freight**:
– Mid-point in terms of cost and speed.
– **Cost Estimate**: Similar to sea freight but varies by destination.
### Additional Costs
1. **Customs Duties and Taxes**:
– Varies by country.
– Example: U.S. import tariffs on machinery can range from 0% to 8%.
2. **Insurance**:
– Protects against damage or loss.
– Typically 1% – 2% of the shipment value.
3. **Port Fees and Handling**:
– Varies depending on the port and services required.
4. **Local Transportation**:
– From port to final destination.
– Depends on distance and local logistics costs.
### Tips for Cost Efficiency
1. **Consolidate Shipments**: To maximize container space.
2. **Negotiate with Suppliers**: For better shipping rates.
3. **Use Freight Forwarders**: For hassle-free logistics at competitive rates.
4. **Plan Ahead**: To avoid rush fees and choose cost-effective shipping methods.
### Example Calculation
For a medium-sized automatic container filling machine:
– **Sea Freight (FCL)**: $3,000
– **Customs Duties**: $500
– **Insurance**: $200
– **Port Fees and Local Transportation**: $700
**Total Estimate**: $4,400
Keep in mind that costs can vary significantly based on the specifics of the shipment and destination. Always obtain multiple quotes and consult a logistics expert.
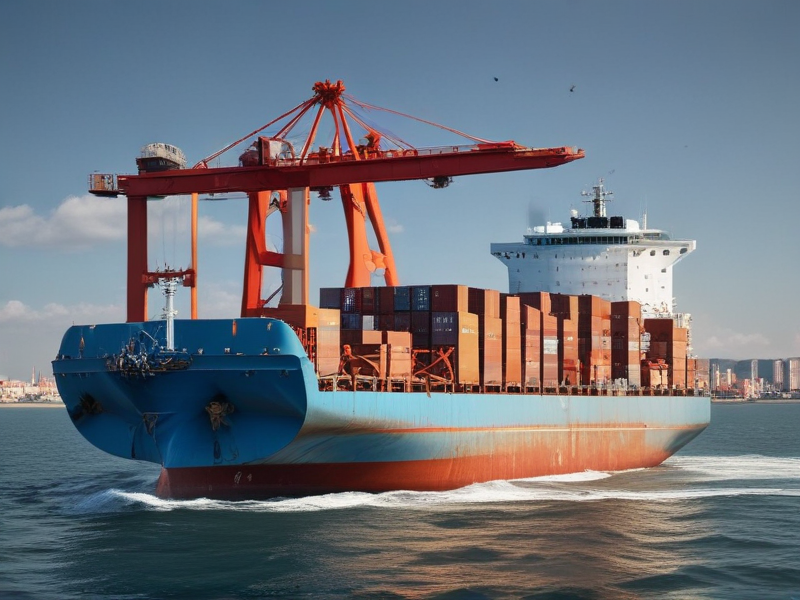
Compare China and Other automatic container filling Markets: Products Quality and Price,Visible and Hidden Costs
When comparing China’s automatic container filling markets to other global markets, several aspects stand out:
**Products Quality and Price**:
– **China**: Generally known for lower manufacturing costs, China offers competitive pricing. However, the quality may vary; while there are high-quality producers, many lower-cost options may compromise on durability and precision.
– **Other Markets (e.g., Germany, the USA)**: These markets typically offer higher-quality products with advanced technology and stricter quality control standards. As a result, prices tend to be higher, but reliability and performance are often superior.
**Visible and Hidden Costs**:
– **Visible Costs**:
– **China**: Lower upfront costs for machinery due to cheaper labor and materials.
– **Other Markets**: Higher initial purchase price reflecting better build quality and advanced features.
– **Hidden Costs**:
– **China**: Potential for higher maintenance and repair costs due to variable product reliability. Longer shipping times and potential tariffs can also add to costs.
– **Other Markets**: Generally lower maintenance and operational costs due to high reliability. However, higher costs may arise from more expensive replacement parts and labor if repairs are needed.
**Conclusion**:
Choosing between China and other automatic container filling markets involves balancing initial costs against long-term reliability and maintenance. Lower upfront costs from China can be tempting, but higher-quality products from markets like Germany or the USA may offer better value over time due to lower hidden costs. Buyers need to consider the total cost of ownership, factoring in both visible and hidden expenses, to make an informed decision.
Custom Private Labeling and Branding Opportunities with Chinese automatic container filling Manufacturers
Partnering with Chinese automatic container filling manufacturers for custom private labeling and branding offers numerous advantages for businesses seeking cost-effective and high-quality production solutions. Here’s a concise overview:
1. **Cost Efficiency**: Chinese manufacturers offer competitive pricing due to lower labor and production costs, which can significantly enhance profit margins.
2. **Advanced Technology**: Many Chinese manufacturers invest in state-of-the-art machinery and adhere to stringent quality standards, ensuring precision and reliability in the filling process.
3. **Customization Options**: These manufacturers provide extensive customization opportunities, allowing businesses to tailor machines to specific needs. Personalization can extend to machine design, filling capacities, and integrated smart features.
4. **Scalability**: Chinese manufacturers can accommodate orders of varying sizes, making them ideal partners whether you’re looking for small batch production or large-scale operations.
5. **Private Labeling and Branding**: Chinese factories can produce goods under your brand name, offering OEM (Original Equipment Manufacturer) and ODM (Original Design Manufacturer) services. This enables you to enter the market with a unique identity without the need for extensive R&D investment.
6. **Quality Assurance**: Many reputable Chinese manufacturers comply with international standards such as ISO and CE certifications, ensuring products meet global quality and safety requirements.
7. **Market Speed**: Due to efficient production processes and robust supply chains, Chinese manufacturers can often reduce lead times, allowing quicker market entry and adaptation to demand changes.
8. **Global Trade Experience**: Chinese manufacturers often have extensive experience in international trade, providing expert assistance with logistics and regulatory compliance.
9. **Partnership Flexibility**: Engaging with these manufacturers offers flexibility in terms of contract agreements, payment terms, and long-term partnerships, providing more control over production and brand direction.
In summary, collaborating with Chinese automatic container filling manufacturers provides a strategic blend of cost-efficiency, advanced capabilities, and customized solutions, enhancing your market competitiveness with custom-branded products.
Tips for Procurement and Considerations when Purchasing automatic container filling
When procuring an automatic container filling machine, several key considerations can ensure you make an informed and strategic investment.
1. **Capacity and Speed**: Evaluate your production needs. Select a machine that matches your required throughput to avoid bottlenecks in your operation.
2. **Customization and Flexibility**: Opt for machines that accommodate various container sizes and types. Flexibility can support product diversification without additional investments.
3. **Accuracy and Precision**: Ensure the machine offers high filling accuracy to minimize wastage and maintain product consistency.
4. **Ease of Operation and Maintenance**: Look for user-friendly interfaces and consider the availability of local support and spare parts. Machines should have straightforward maintenance protocols to minimize downtime.
5. **Scalability**: Choose a system that can scale with your business growth. Consider modular designs that allow for future upgrades.
6. **Compliance and Safety Standards**: Ensure the equipment meets industry-specific regulations such as FDA, CE, or ISO standards if applicable. Safety features are crucial for protecting operators and maintaining compliance.
7. **Cost and ROI**: Balance initial costs with long-term benefits. Consider energy efficiency, potential labor savings, and overall return on investment.
8. **Reputation of Manufacturer**: Select reputable manufacturers known for quality and reliability, and check reviews or request case studies to gauge past performance and customer satisfaction.
9. **Integration**: Ensure the machine can seamlessly integrate into your existing production line and communicate with other equipment.
10. **Training and Support**: Assess the training provided by the manufacturer and the level of post-purchase support, including installation, troubleshooting, and software updates.
Careful consideration of these factors will help in acquiring an efficient, reliable, and cost-effective automatic container filling machine suited to your specific needs.
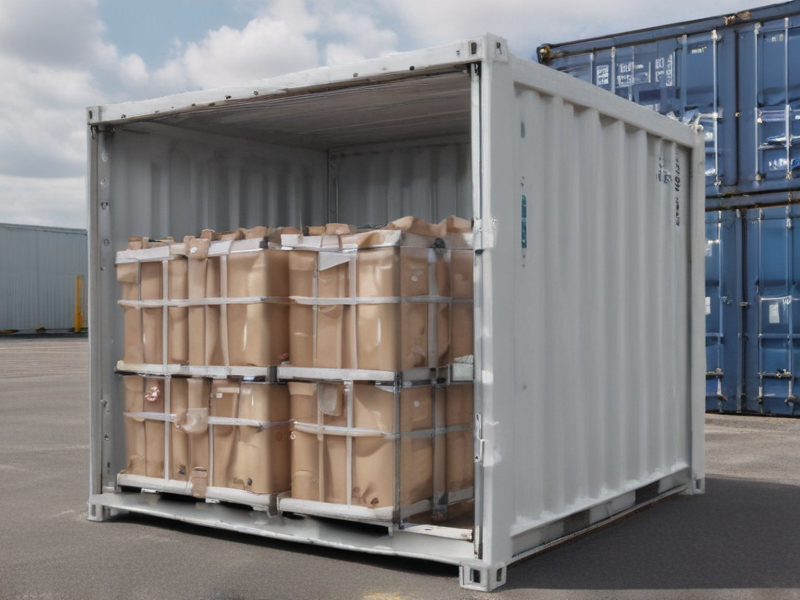
FAQs on Sourcing and Manufacturing automatic container filling in China
**FAQs on Sourcing and Manufacturing Automatic Container Filling Machines in China**
1. **Why source from China?**
– China offers competitive pricing, advanced technology, and a vast supply chain network for automatic container filling machines.
2. **How to find reliable manufacturers?**
– Use platforms like Alibaba, Made-in-China, and Global Sources. Attend trade shows like Canton Fair. Seek recommendations and conduct due diligence including factory visits.
3. **What are the key factors to consider?**
– Look for ISO certifications, production capacity, customizability, lead times, and after-sales service.
4. **How can I ensure product quality?**
– Insist on factory audits, request samples, and employ third-party inspection services.
5. **Are there language barriers?**
– Many manufacturers have English-speaking sales teams. Using a local sourcing agent can also help mitigate language issues.
6. **What’s the usual lead time?**
– Typically, 30-60 days depending on customization and order size.
7. **Can the machines be customized?**
– Yes, most manufacturers offer customization options according to specific requirements.
8. **What about logistics and shipping?**
– Manufacturers can assist with logistics. Options include sea, air, and rail, with Incoterms like FOB, CIF, or EXW.
9. **How do I handle payment?**
– Common methods include T/T (telegraphic transfer), L/C (letter of credit), and payment platforms like PayPal for initial transactions.
10. **What are the warranty and after-sales services?**
– Warranties usually range from 1-2 years. Ensure clear terms on after-sales support and parts availability.
11. **Is Intellectual Property (IP) protection an issue?**
– Concerns exist; use contracts with confidentiality clauses and consider IP registration in China.
12. **Are there regulatory considerations?**
– Ensure compliance with international standards (e.g., CE, FDA) and local regulations depending on your target market.
By thoroughly addressing these common questions, you can streamline the process of sourcing and manufacturing automatic container filling machines in China.