Top 10 automatic palletizing system in China introduce,list main products and website if have
Sure! Here’s a concise list of the top 10 automatic palletizing system providers in China, along with their main products and websites if available:
1. **Siasun Robot & Automation Co., Ltd.**
– **Main Products:** Robotic palletizers, handling robots, automated storage systems
– **Website:** [siasun.com](http://www.siasun.com/)
2. **Shanghai Triowin Automation Machinery Co., Ltd.**
– **Main Products:** Robotic palletizers, automated conveying systems, end-of-line packaging solutions
– **Website:** [triowin.com](http://www.triowin.com/)
3. **Guangzhou Risong Technology Co., Ltd.**
– **Main Products:** Robotic palletizing systems, automatic guided vehicles (AGVs), intelligent logistics systems
– **Website:** [risonggroup.com](http://www.risonggroup.com/)
4. **KUKA Robotics China**
– **Main Products:** Robotic palletizers, robotic arms for material handling, automation solutions
– **Website:** [kuka.com](https://www.kuka.com/)
5. **FANUC Robotics China**
– **Main Products:** Robotic palletizers, handling robots, integrated automation solutions
– **Website:** [fanuc.com.cn](https://www.fanuc.com.cn/)
6. **YASKAWA China**
– **Main Products:** Robotic palletizers, automation systems, robot controllers
– **Website:** [yaskawa.com.cn](http://www.yaskawa.com.cn/)
7. **DIAOTEC Technology Co., Ltd.**
– **Main Products:** Robotic palletizing systems, AGVs, smart factory solutions
– **Website:** [diaotec.com](http://www.diaotec.com/)
8. **Bosch Rexroth China**
– **Main Products:** Robotic palletizers, motion control systems, hydraulic drives
– **Website:** [boschrexroth.com.cn](https://www.boschrexroth.com.cn/)
9. **ABB Robotics China**
– **Main Products:** Robotic palletizers, industrial robots, automation solutions
– **Website:** [abb.com.cn](https://new.abb.com/cn)
10. **EP Equipment**
– **Main Products:** Automated guided vehicles (AGVs), palletizing robots, warehouse automation solutions
– **Website:** [ep-ep.com](https://www.ep-ep.com/)
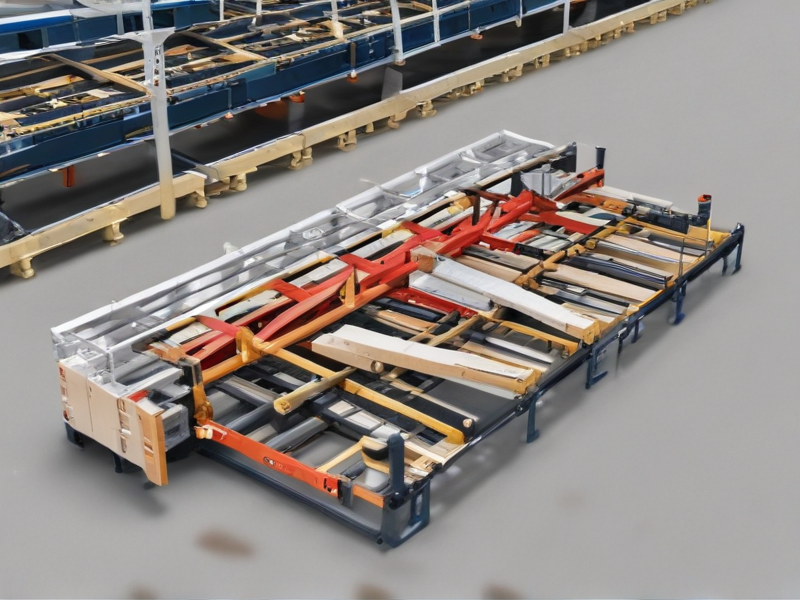
Types of automatic palletizing system
Automatic palletizing systems come in various types to suit different industrial needs for stacking and organizing products on pallets efficiently. Here are the main types:
1. **Cartesian Palletizers**:
These systems use linear actuators (axial robots) to achieve movements along X, Y, and Z axes. They are ideal for precise and consistent pallet placement and are often used in environments where space is constrained.
2. **Articulated Arm Palletizers**:
These systems leverage multi-joint robotic arms that offer high flexibility and dexterity. They can handle complex palletizing patterns and different product sizes. Industries with varied product lines often choose these for their adaptability.
3. **Layer Palletizers**:
Layer palletizers arrange products layer by layer onto the pallet. They often include mechanisms such as a sliding plate or a push arm to position entire layers. These systems are suitable for high-output production lines where speed and uniformity are critical.
4. **Cooperative Robots (Cobots)**:
Cobots work alongside human workers, sharing the workspace safely. They are equipped with advanced sensors and programming to handle tasks that require more delicate handling and can be integrated into existing workflows with minimal disruption.
5. **Mixed-Case Palletizers**:
These systems are designed to handle mixed SKU (stock-keeping unit) loads, sorting and stacking different items on the same pallet according to a predefined pattern. They are often used in distribution centers where diverse product selection is essential.
6. **Robotic Gantry Palletizers**:
Combining the principles of gantry cranes and robotic palletizing, these systems can cover large areas and handle heavy loads. They are suitable for industries that require extensive, high-volume palletizing over large spaces.
Each type of automatic palletizing system brings unique advantages, tailored to specific operational needs, product types, and spatial constraints. Choosing the right system depends on the required speed, flexibility, complexity of pallet patterns, and volume of goods to be palletized.
Pros and Cons of Using automatic palletizing system
**Pros of Using Automatic Palletizing Systems:**
1. **Increased Efficiency**: Automated systems can handle high volumes of products consistently, leading to faster loading and unloading processes compared to manual labor.
2. **Cost Reduction**: Lower labor costs due to reduced dependency on human workers. Over time, this can lead to significant savings despite the initial investment.
3. **Consistency and Precision**: Minimizes human error, ensuring products are stacked uniformly and securely, which reduces damage during transportation.
4. **Enhanced Safety**: Reduces the risk of workplace injuries associated with manual palletizing tasks, such as lifting heavy items or repetitive strain injuries.
5. **Scalability**: Easily adaptable to varying production volumes and can be reprogrammed for different palletizing requirements without the need for extensive retraining or physical changes.
6. **Space Optimization**: Automated systems can maximize space utilization with precise stacking, allowing for better warehouse organization.
**Cons of Using Automatic Palletizing Systems:**
1. **High Initial Investment**: Significant upfront costs for purchasing and installing the system, which may not be feasible for smaller operations.
2. **Maintenance and Repairs**: Requires regular maintenance and can be costly to repair. Downtime during repairs can disrupt operations.
3. **Complexity and Training**: Operators and maintenance staff need training to effectively manage and troubleshoot the system, which involves additional time and resources.
4. **Flexibility Limitations**: Automated systems may struggle with non-standard or irregularly shaped items, requiring manual intervention.
5. **Dependence on Technology**: System failures or malfunctions can halt production lines, making businesses highly dependent on technology reliability.
6. **Obsolescence**: Rapid technological advancements can render the initial system outdated, necessitating further investment in upgrades or new technologies.
In conclusion, while automatic palletizing systems offer substantial benefits in terms of efficiency, cost reduction, and safety, they also come with significant drawbacks like high initial costs, maintenance demands, and potential flexibility issues.
automatic palletizing system Reference Specifications (varies for different product)
An automatic palletizing system is designed to stack products on pallets efficiently, enhancing warehouse management and reducing manual labor. Reference specifications for such a system can vary based on the type of product being handled, as well as the requirements of the operational environment. Below are common specifications to consider:
### System Capacity
– **Throughput:** Typically ranges from 60 to 120 items per minute, depending on product size and weight.
– **Load Capacity:** Capable of handling weights up to 2,500 kg per pallet.
### Product Specifications
– **Product Dimensions:** Accommodates a variety of sizes, with typical dimensions ranging from 200 mm to 1,200 mm in length, width, and height.
– **Product Weight:** Supports individual product weights from 0.5 kg to 50 kg.
### Pallet Specifications
– **Pallet Size:** Commonly supports standard pallet sizes like 800 x 1200 mm and 1000 x 1200 mm.
– **Pallet Type:** Compatible with wooden, plastic, and metal pallets.
### Operational Features
– **Layer Configurations:** Customizable stacking patterns and layers to optimize pallet stability.
– **Sorting:** Advanced vision systems or barcode readers for product identification and sorting.
– **Conveyor Integration:** Seamless integration with existing conveyor systems for infeed and outfeed.
### Control System
– **Automation:** Programmable Logic Controllers (PLC) for precise control and operation.
– **User Interface:** Intuitive Human-Machine Interface (HMI) for easy operation and monitoring.
– **Safety Features:** Equipped with safety sensors, emergency stops, and safety fences to protect operators.
### Environmental Considerations
– **Temperature Range:** Operates effectively in environments ranging from -10°C to 40°C.
– **Humidity Resistance:** Designed to work in humid conditions, up to 95% relative humidity.
### Maintenance and Support
– **Service Intervals:** Recommended maintenance schedule based on operational hours.
– **Technical Support:** Remote diagnostics and troubleshooting capabilities.
### Power and Energy
– **Power Requirements:** Typically operates on 230/380V, 50/60Hz electrical supply.
– **Energy Efficiency:** Incorporates energy-saving modes to reduce power consumption.
These specifications aim to provide a balanced overview for an automatic palletizing system, ensuring it meets diverse operational needs while maintaining efficiency and safety.
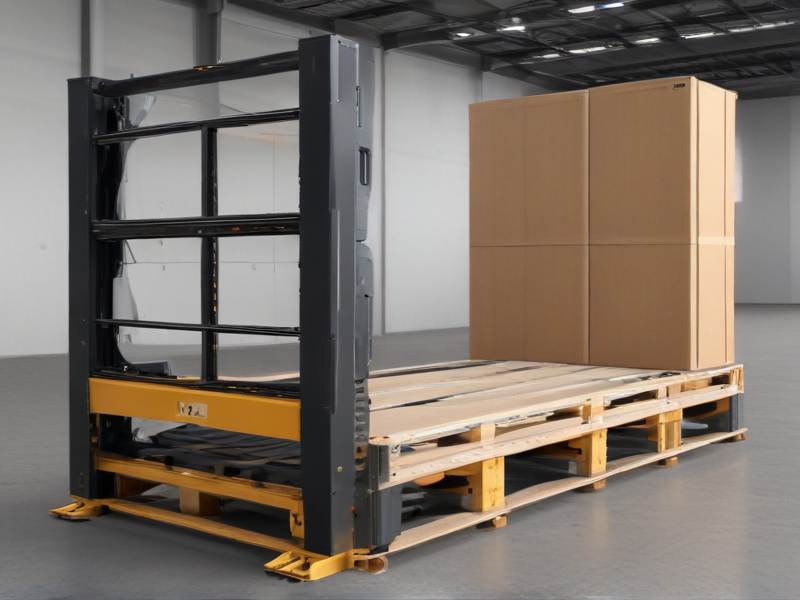
Applications of automatic palletizing system
Automatic palletizing systems are versatile solutions widely applied across various industries to streamline operations and improve efficiency. Here are some key applications:
1. **Manufacturing**: These systems are used to stack products such as automotive parts, electronics, and consumer goods onto pallets. This enhances speed, reduces manual labor, and minimizes errors in arranging products.
2. **Warehouse and Distribution Centers**: They optimize the logistics process by efficiently stacking and organizing products for shipment. This improves space utilization, speeds up loading and unloading, and increases overall throughput.
3. **Food and Beverage**: Automatic palletizers handle delicate and varied packaging such as bottles, cans, and cartons. They ensure hygienic handling and precise stacking to maintain product integrity and compliance with safety standards.
4. **Pharmaceuticals**: In the pharmaceuticals industry, palletizers manage the high-volume, repetitive task of stacking boxes of medicines and other products, ensuring accuracy and reducing the risk of contamination.
5. **Agriculture**: These systems are employed for stacking products like bags of seeds, animal feed, and fertilizers. This application supports heavy-duty operations and weather-proof packaging needs.
6. **Consumer Packaged Goods (CPG)**: From toiletries to cleaning supplies, palletizing systems help in arranging various packaged goods in a consistent manner, ready for transportation and retail distribution.
7. **Construction Materials**: Automatic palletizers are used to manage heavy and irregularly shaped items such as bricks, tiles, and cement bags, ensuring safe stacking and transport.
8. **E-commerce**: In E-commerce fulfillment centers, these systems expedite the sorting and packing process, accommodating a variety of packaging sizes and weights, crucial for meeting rapid shipping requirements.
In conclusion, automatic palletizing systems significantly enhance productivity, safety, and efficiency across various sectors by automating the labor-intensive task of pallet stacking. They are indispensable in modern supply chain and manufacturing environments where precision and speed are critical.
Material of automatic palletizing system
Automatic palletizing systems are engineered for efficiency, durability, and longevity. The material selection for these systems is crucial to ensure they operate effectively in different industrial environments. Key materials commonly used include:
1. **Stainless Steel**: Widely used for its corrosion resistance and strength, stainless steel is ideal for components exposed to harsh environments or requiring stringent hygiene standards, such as in food and beverage industries.
2. **Aluminum**: Known for its lightweight and rust-resistant properties, aluminum components are often used to reduce the system’s overall weight, subsequently lowering operational energy consumption.
3. **Carbon Steel**: Often used in the structural framework due to its high strength and cost-effectiveness. It is typically coated with protective layers to enhance durability and rust resistance.
4. **Plastics and Composites**: Engineering plastics like UHMW (Ultra-High Molecular Weight Polyethylene) and composite materials are used for parts exposed to wear and tear, such as conveyor belts, guides, and rollers, due to their low friction, noise reduction, and lightweight properties.
5. **Rubber**: Used for cushioning elements and grip pads to handle various products without causing damage.
6. **Electronics and Control Systems**: These include microprocessors, sensors, and actuators made from high-grade electronic materials to ensure precision and reliability in automation.
In designing an automatic palletizing system, the combination of these materials depends on the specific needs of the application, such as the type of products being palletized, environmental conditions, and desired longevity. The right material selection enhances operational efficiency, minimizes maintenance, and delivers consistent performance.
Quality Testing Methods for automatic palletizing system and how to control the quality
Quality testing for an automatic palletizing system ensures it operates efficiently, safely, and without errors. Here’s a concise overview of key methods and controls:
1. **Functionality Testing**:
– **Operational Tests**: Verify the system’s basic operations, including picking, orienting, and placing items on pallets.
– **Endurance Tests**: Run the system over extended periods to ensure durability and consistent performance.
2. **Accuracy Checks**:
– **Positioning Accuracy**: Ensure that items are placed precisely where intended on the pallet.
– **Weight and Dimension Verification**: Check that the system correctly handles varying weights and dimensions of items without error.
3. **Safety Testing**:
– **Emergency Stop Functionality**: Test emergency stops and other fail-safes.
– **Obstacle Detection**: Ensure sensors detect obstacles and react appropriately to prevent accidents.
4. **Load Stability Tests**:
– **Impact and Vibration Analysis**: Assess how well the stacked pallets withstand external impacts and vibrations.
5. **Integration Testing**:
– **Compatibility Tests**: Verify that the palletizing system integrates smoothly with upstream and downstream processes and systems.
**Quality Control Measures**:
1. **Real-Time Monitoring**:
– Employ sensors to track the system’s performance in real-time and detect deviations immediately.
2. **Scheduled Maintenance**:
– Regular maintenance checks help prevent unexpected breakdowns and ensure long-term reliability.
3. **Statistical Process Control (SPC)**:
– Use SPC techniques to monitor the variability of key processes within the system, ensuring they stay within defined limits.
4. **Feedback Loop**:
– Implement a feedback mechanism where data from performance metrics guide continuous improvement efforts.
5. **Operator Training**:
– Ensure operators are well-trained to recognize issues and perform basic troubleshooting.
Effective application of these methods and controls ensures the automatic palletizing system performs reliably, safely, and efficiently.
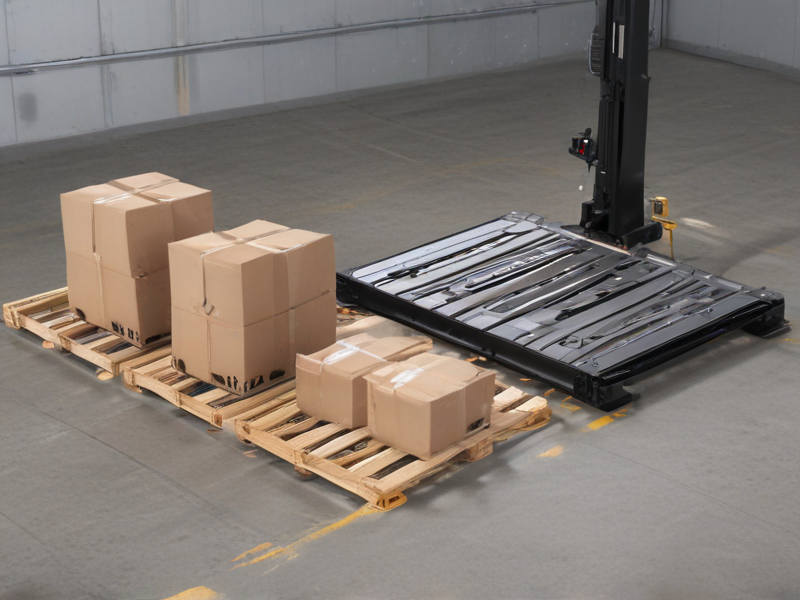
The Work Process and how to use automatic palletizing system
An automatic palletizing system streamlines the stacking of products onto pallets, enhancing efficiency in various industries. Here’s a simplified work process and guide on how to use such a system:
### Work Process:
1. **Product Infeed**: Products arrive on a conveyor belt from the production line.
2. **Orientation and Sorting**: Items are oriented correctly and sorted based on predefined criteria.
3. **Layer Formation**: Items are grouped into layers, optimizing the stacking pattern for stability.
4. **Layer Transfer**: A robotic arm or shuttle transfers each layer to the pallet.
5. **Pallet Loading**: Layers are stacked systematically until the pallet reaches the desired height.
6. **Pallet Discharge**: The fully loaded pallet is transported to a wrapping station or staging area for shipping.
### How to Use:
1. **Set Up**:
– **Power On**: Ensure the system is connected and powered on.
– **Select Mode**: Choose the operational mode (e.g., automatic, semi-automatic).
2. **Input Specifications**:
– **Product Details**: Enter product dimensions and weights.
– **Pallet Configuration**: Define the pallet pattern and stacking height.
3. **Load Products**:
– Place products on the infeed conveyor.
– Adjust sensors and guides as necessary to ensure proper alignment.
4. **Monitor Operation**:
– **Supervise Initial Runs**: Watch the system for any misalignments or errors.
– **Adjust Parameters**: Fine-tune settings based on initial observations.
5. **Regular Maintenance**:
– **Inspect Components**: Regularly check belts, robotic arms, and sensors.
– **Clean System**: Keep the conveyor and robot free of debris.
6. **Safety Protocols**:
– **Emergency Stops**: Familiarize with emergency stop buttons and procedures.
– **Protective Gear**: Wear necessary safety equipment when operating or maintaining the system.
By following these steps, the automatic palletizing system can significantly improve warehouse and production line efficiency, ensuring precise and timely handling of products.
automatic palletizing system Importing questions including Cost,Supplier,Sample,Certification and Market
When considering the import of an automatic palletizing system, it’s essential to address several key questions:
1. **Cost**:
– What is the total cost of the system, including shipping, taxes, and installation?
– Are there any hidden fees, such as customs duties or service charges?
– What are the ongoing operational and maintenance costs?
2. **Supplier**:
– Who are the reputable suppliers or manufacturers of automatic palletizing systems?
– Can the supplier provide a product catalog and client testimonials?
– What is the lead time for delivery?
3. **Sample**:
– Is it possible to get a sample or a trial run of the palletizing system before purchasing?
– Can the supplier provide a virtual demo or an on-site demonstration?
– Are there any pilot programs available to test the system in a real-world setting?
4. **Certification**:
– What certifications does the palletizing system hold (e.g., CE, ISO, UL)?
– Are these certifications recognized and compliant with the regulations in your country?
– Can the supplier provide documentation to verify certification claims?
5. **Market**:
– What is the current market demand for automated palletizing systems?
– Who are your primary competitors, and what systems are they using?
– What are the latest trends in palletizing technology that could impact your business decisions?
By carefully considering these questions, you can make a more informed decision about importing an automated palletizing system that meets your logistical, financial, and operational needs.
How to find and select check reliable automatic palletizing system manufacturers in China
To find and select reliable automatic palletizing system manufacturers in China, follow these steps:
1. **Research and Shortlist**:
– Use online platforms like Alibaba, Made-in-China, and Global Sources to identify potential manufacturers.
– Search for manufacturers with high ratings, positive reviews, and a history of exporting to your country.
2. **Verify Credentials**:
– Check their business licenses and certifications such as ISO 9001, CE, and relevant industry-specific certifications.
– Review their company websites and look for detailed product information, case studies, and client testimonials.
3. **Assess Experience**:
– Prefer manufacturers with a proven track record in producing automatic palletizing systems. Look for those with at least 5-10 years of experience.
– Request case studies or references from similar projects they have completed.
4. **Product Quality and Innovation**:
– Evaluate the technical specifications and innovation level of their products. Ensure they use high-quality materials and advanced technology.
– Ask for samples or conduct a factory visit to inspect the manufacturing process and product quality.
5. **After-Sales Support**:
– Confirm the availability of after-sales support, including installation, training, and maintenance services.
– Ensure they offer a warranty period for their products.
6. **Compare Quotes**:
– Request detailed quotations from multiple manufacturers. Compare not only the pricing but also the quality, features, and included services.
7. **Communication and Responsiveness**:
– Evaluate their communication skills and responsiveness. Reliable manufacturers should be prompt, clear, and professional in their responses.
8. **Third-Party Verification**:
– Consider hiring a third-party inspection company to verify the manufacturer’s claims and inspect the product quality before finalizing the order.
By following these steps, you can select a reliable automatic palletizing system manufacturer in China that meets your specific needs.
Background Research for automatic palletizing system manufacturers Companies in China, use qcc.com archive.org importyeti.com
Certainly! Conducting background research on automatic palletizing system manufacturers in China, leveraging qcc.com, archive.org, and importyeti.com, reveals some key players and insights.
1. **Qcc.com**: This platform offers detailed company information and is useful for understanding Chinese corporate landscapes. Searches for “automatic palletizing system manufacturers” surfaced several notable companies:
– **Siasun Robot & Automation Co., Ltd.**: Recognized as a leading robotics company, Siasun specializes in various automation solutions including palletizing systems. Established in 2000, it has a broad portfolio and a significant R&D focus.
– **Guangdong Foshan Sifang Automation Equipment Co., Ltd.**: Known for robust manufacturing capabilities in palletizing systems. It boasts a strong domestic market presence and a growing international clientele.
– **Kawasaki Robotics (Tianjin) Co., Ltd.**: A division of the Japanese robotics giant, this company offers advanced palletizing solutions tailored for diverse industries in China.
2. **Archive.org**: The Wayback Machine can reveal historical data about corporate web pages:
– **Estun Automation**: Examination of their site archives shows consistent expansion in automation products, including advances in palletizing systems technology.
– **SCARA Robot**: Historical data indicates a progressive enhancement in their product lines with increasing integration of AI for precision palletizing.
3. **Importyeti.com**: This tool tracks import-export data, providing insights into trade activities:
– **Shanghai Triowin Automation Machinery Co., Ltd.**: Records indicate substantial exports of palletizing systems to North America and Europe, underscoring the company’s international market penetration.
– **Jingyuan Automatic Equipment Co., Ltd.**: Showing frequent shipments to Southeast Asia, verifying their extensive export logistics for automated palletizing solutions.
In summary, companies like Siasun, Sifang, Kawasaki Robotics, Estun Automation, SCARA Robot, Triowin, and Jingyuan are prominent players in China’s automatic palletizing systems industry. They demonstrate strong capabilities in innovation, domestic and international market reach, and diverse application of palletizing technologies.
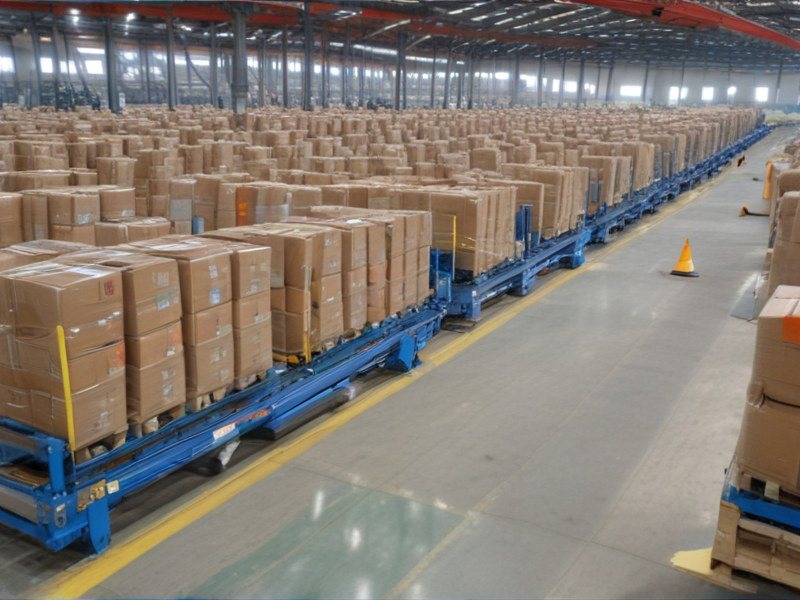
Price Cost Research for automatic palletizing system manufacturers Companies in China, use temu.com and 1688.com
Conducting price cost research for automatic palletizing systems on Chinese platforms like Temu.com and 1688.com can provide insights into costs and manufacturers. Below is a brief overview based on online data:
### Temu.com:
– **Niryo One**: An entry-level robotic arm often used for educational purposes with basic palletizing capabilities. Priced around $1,500-$2,000.
– **ROBone by Elephant Robotics**: Priced around $3,000-$5,000, suitable for light palletizing tasks.
– **DFRobot Palletizing Solutions**: More industrial-grade, starting at approximately $8,000-$12,000.
### 1688.com:
– **Shenzhen Yiernuo Intelligent Technology**: Automatic palletizing robots priced between Â¥50,000-Â¥100,000 ($7,000-$14,000).
– **Jingbei Tech**: Known for heavy-duty industrial robots, with prices around Â¥80,000-Â¥150,000 ($11,000-$21,000).
– **Shandong Lisen Automation**: Offers various models starting from Â¥70,000 ($10,000) to Â¥200,000 ($29,000) for advanced versions.
### Key Manufacturers on Both Platforms:
– **ABB Robotics**: Globally recognized, with prices ranging from $15,000-$50,000 depending on customization and specifications.
– **Fanuc China**: Known for robust industrial robots with prices starting at around $20,000.
– **KUKA Robotics**: Provides highly customizable solutions, generally priced between $25,000 and $60,000.
### General Insights:
– **Entry-Level**: $1,500 – $5,000
– **Mid-Range**: $7,000 – $14,000
– **Industrial-Grade**: $15,000 – $60,000
**Recommendations**:
– Carefully assess requirements such as payload capacity, speed, and integration capabilities.
– Reach out to multiple suppliers to get detailed specifications and customized quotes.
– Consider after-sales support and warranty options when making a decision.
By utilizing Temu.com and 1688.com, you can gain a broad understanding of the market spectrum in China and select a supplier that aligns with your budget and technical requirements.
Shipping Cost for automatic palletizing system import from China
Shipping costs for importing an automatic palletizing system from China can vary greatly depending on several factors. Here are some key considerations:
### 1. **Shipping Method:**
– **Sea Freight:** The most common and economical method for large, heavy equipment.
– **Air Freight:** Faster but significantly more expensive; typically used for urgent or smaller shipments.
### 2. **Size and Weight:**
– Heavier and bulkier items cost more to ship. Packaging size also influences the cost.
### 3. **Destination:**
– The cost differs depending on the final destination’s distance from major ports or airports. For instance, shipping to a major port like Los Angeles is usually cheaper than to an inland city.
### 4. **Freight Charges:**
– **Port Charges:** Fees for loading and unloading at ports.
– **Customs Duties:** Import duties and taxes, which can vary by country.
– **Insurance:** Optional but recommended, particularly for high-value equipment.
### 5. **Additional Services:**
– Crating, packaging, and labeling services might incur extra costs.
### 6. **Freight Forwarder Fees:**
– These include documentation, handling charges, and any other logistical support services provided.
### Estimated Costs:
– **Sea Freight:**
– A 20-foot container could cost anywhere from $2,000 to $4,000.
– A 40-foot container might range from $4,000 to $7,000.
– **Air Freight:**
– Costing approximately $5 to $10 per kilogram, depending on the urgency and airline.
### Example Calculation (Sea Freight):
– **Palletizing System Weight:** 5,000 kg
– **Volume:** 10 cubic meters
– **From Shanghai to Los Angeles:**
– Approximate total cost: $3,500 (including handling and documentation).
### Conclusion:
While it’s challenging to give an exact figure without detailed specifications, understanding these factors will help in estimating and optimizing shipping costs. Always get multiple quotes from freight forwarders to ensure you’re getting the best deal.
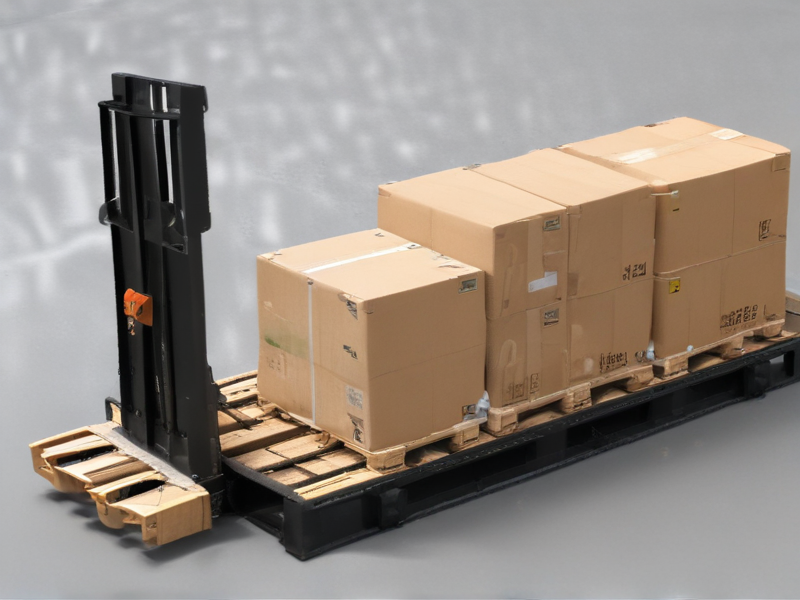
Compare China and Other automatic palletizing system Markets: Products Quality and Price,Visible and Hidden Costs
When comparing automatic palletizing systems from China with other leading markets (e.g., Germany, Japan, and the United States), several critical factors such as product quality, price, and both visible and hidden costs should be considered.
**Product Quality:**
– **China:** Typically, Chinese palletizing systems offer robust basic functionality at a lower cost. The quality has been improving, though long-term reliability and advanced features might sometimes lag behind.
– **Other Markets:** Systems from Germany, Japan, and the USA often boast superior engineering, durability, and advanced technological features, albeit at a higher cost. They are renowned for reliability and precision.
**Price:**
– **China:** Lower initial purchase price is a significant attraction. Chinese manufacturers often offer competitive pricing due to lower labor costs and economies of scale.
– **Other Markets:** Higher upfront costs are common. Premium pricing reflects the advanced technology, better build quality, and stringent manufacturing standards.
**Visible and Hidden Costs:**
– **China:** While upfront costs are lower, hidden costs can emerge from potential issues like shorter product lifespans, increased maintenance needs, and less accessible after-sales service. Costs related to downtime, repairs, and replacement parts can add up over time.
– **Other Markets:** Although the initial investment is higher, visible costs often align with known high quality. Hidden costs are minimized due to longevity, fewer breakdowns, and comprehensive support services. These systems also tend to have better integration and upgrade paths, reducing long-term expenditure.
In summary, while Chinese automatic palletizing systems offer budget-friendly options with essential functionalities, systems from other leading markets deliver higher quality, reliability, and lower long-term hidden costs despite the higher initial investment. Decisions should weigh immediate budget constraints against long-term operational efficiency and total cost of ownership.
Custom Private Labeling and Branding Opportunities with Chinese automatic palletizing system Manufacturers
Custom private labeling and branding opportunities with Chinese automatic palletizing system manufacturers present a compelling proposition for businesses seeking to enhance their product offerings and market presence. By leveraging the advanced manufacturing capabilities and cost-effective production of Chinese suppliers, companies can create uniquely branded solutions tailored to their specific market needs.
Chinese manufacturers are renowned for their flexibility and willingness to accommodate custom requests. This opens up several avenues for private labeling, such as incorporating a company’s logo, brand colors, and unique features into the design of the automatic palletizing systems. Custom packaging and instruction manuals can also be developed to align with the branding strategy, ensuring a cohesive and professional look.
An additional benefit of private labeling with Chinese producers is the opportunity for rapid prototyping and scaling. With their extensive manufacturing infrastructure, these producers can quickly bring customized products from the design phase to full-scale production, enabling businesses to respond swiftly to market demands and trends.
Furthermore, partnering with reputable Chinese manufacturers often provides access to the latest technological innovations in automatic palletizing systems. These partnerships can yield cutting-edge solutions that enhance efficiency, reduce labor costs, and improve overall operational performance. By branding these advanced systems under their own name, companies can position themselves as leaders in the logistics and automation sectors.
However, successful collaboration requires diligent due diligence. It’s crucial to select manufacturers with proven track records, robust quality control measures, and compliance with international standards. Establishing clear communication channels and setting explicit expectations for quality and delivery times are imperative to maintaining a positive working relationship.
In essence, custom private labeling and branding with Chinese automatic palletizing system manufacturers can significantly boost a business’s competitive edge, offering tailored, high-quality solutions that resonate with targeted customer bases while ensuring rapid market responsiveness.
Tips for Procurement and Considerations when Purchasing automatic palletizing system
When procuring an automatic palletizing system, consider the following tips:
1. **Assess Requirements:**
– **Production Rate:** Align the system’s capacity with your production volumes.
– **Product Variety:** Ensure the system can handle different shapes, sizes, and weights.
2. **Technical Specifications:**
– **Compatibility:** Confirm compatibility with your existing conveyor and packaging systems.
– **Flexibility:** Opt for a system that can adapt to future changes in product lines.
– **Accuracy and Precision:** High precision reduces product damage and increases stacking efficiency.
3. **Space and Layout:**
– **Footprint:** Ensure you have adequate space; some systems have a large footprint.
– **Integration:** Plan the layout for smooth integration with current operations.
4. **Cost Considerations:**
– **Budget:** Factor in both initial costs and long-term savings from labor and efficiency improvements.
– **Total Cost of Ownership (TCO):** Include maintenance, spare parts, and energy consumption.
5. **Vendor Evaluation:**
– **Reputation:** Research vendor reliability and experience.
– **Technical Support:** Ensure robust after-sales support and training.
– **Warranty:** Review warranty terms and conditions.
6. **Safety and Compliance:**
– **Regulations:** Ensure the system complies with local safety standards and regulations.
– **Safety Features:** Look for systems with advanced safety features like emergency stops and safety barriers.
7. **Technology and Innovation:**
– **Automation Level:** Decide between semi-automatic and fully-automatic based on your needs.
– **Software Integration:** Check for advanced software capabilities for better control and diagnostics.
8. **Future-Proofing:**
– **Scalability:** Choose a system that can scale with your business growth.
– **Upgradability:** Prefer systems that offer easy upgrades for new technologies.
Conduct thorough research and engage with multiple vendors to make an informed decision that meets both your current and future needs.
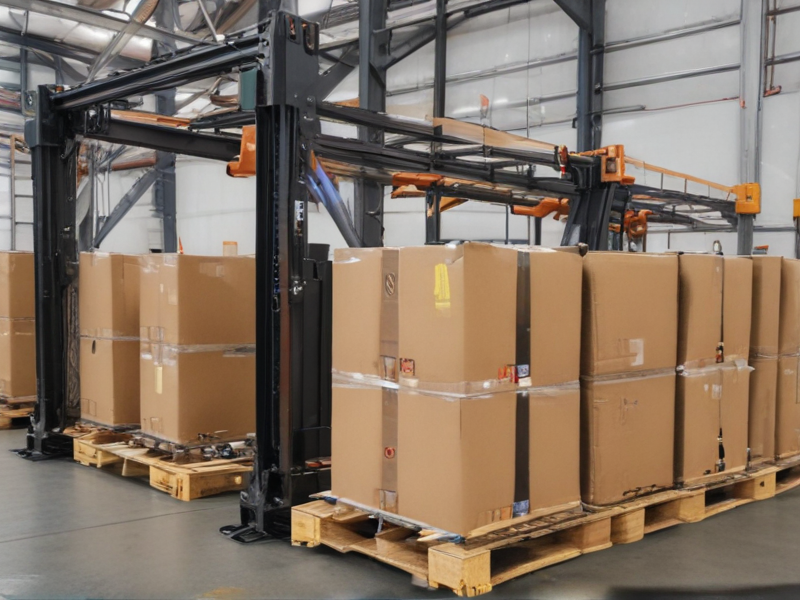
FAQs on Sourcing and Manufacturing automatic palletizing system in China
### FAQs on Sourcing and Manufacturing Automatic Palletizing Systems in China
**1. Why source automatic palletizing systems from China?**
China offers competitive pricing, advanced technology, and a broad range of manufacturers. The country’s robust industrial base helps ensure quick turnaround times and scalable solutions.
**2. How do I find a reliable manufacturer?**
Utilize online platforms like Alibaba or global trade shows like the Canton Fair. Verify certifications (ISO, CE), and request case studies or client references. Factory audits either in-person or via third-party inspection agencies are also recommended.
**3. What are the key features to consider?**
Look for speed, accuracy, payload capacity, flexibility in handling multiple product types, and ease of integration into existing production lines. Safety features and after-sales service are critical as well.
**4. Can manufacturers customize solutions to my needs?**
Yes, many Chinese manufacturers offer customizable solutions. Share detailed requirements and participate in the design process to ensure the final product meets your specifications.
**5. What quality control measures are in place?**
Ensure the manufacturer adopts rigorous quality control processes like RoHS compliance and routine factory inspections. Third-party inspections before shipment are also advisable.
**6. How is intellectual property protected?**
While IP laws in China have improved, ensure to sign NDAs and contracts specifying IP rights. Registering patents and trademarks in China can offer added protection.
**7. What are the payment terms?**
Typically, payment is made through T/T (Telegraphic Transfer) with a 30% deposit and 70% before shipment. L/C (Letter of Credit) is another option for larger orders.
**8. What about logistics and shipping?**
Manufacturers can handle shipping, but working with an experienced freight forwarder ensures smoother customs clearance and better rates. Opt for incoterms like FOB (Free on Board) to control shipping costs.
**9. Are there after-sales services?**
Reputable manufacturers offer comprehensive after-sales services including installation support, training, and maintenance. Ensure these services are clearly outlined in your contract.
**10. How do tariffs and duties affect costs?**
Import tariffs and duties vary by country. Check local regulations and utilize free trade agreements where applicable to minimize costs.