Top 10 automatic robotic palletizer in China introduce,list main products and website if have
Sure, here is a brief introduction to the top 10 automatic robotic palletizer manufacturers in China along with their main products and websites:
1. SIASUN Robot & Automation Co., Ltd.
– Main Products: Robotic palletizers, automated guided vehicles, industrial robots.
– Website: [SIASUN](http://www.siasun.com/)
2. EFORT Intelligent Equipment Co., Ltd.
– Main Products: Palletizing robots, welding robots, assembly line robots.
– Website: [EFORT](http://www.efort.com/)
3. Rise Robotics Co., Ltd.
– Main Products: Robotic palletizers, pick-and-place robots, conveying systems.
– Website: [Rise Robotics](http://www.riserobotics.cn/)
4. GSK CNC Equipment Co., Ltd.
– Main Products: Palletizing and handling robots, CNC machine tools.
– Website: [GSK CNC](http://www.gsk.com.cn/)
5. Estun Automation Co., Ltd.
– Main Products: Robotic palletizers, industrial robots, motion control products.
– Website: [Estun](http://www.estun.com/)
6. Triowin Automation Machinery Co., Ltd.
– Main Products: End-of-line packaging systems, robotic palletizers, fresh produce processing.
– Website: [Triowin](http://www.triowin.com/)
7. Guangzhou Risong Intelligent Technology Holding Co., Ltd.
– Main Products: Robotic palletizers, welding robotics, automation solutions.
– Website: [Risong](http://www.risonginc.com/)
8. Jingyuan Mechatronics Co., Ltd.
– Main Products: Palletizing robots, pick and place systems, CNC machines.
– Website: [Jinguan CNC](http://www.jingyuancnc.com/)
9. AUBO Robotics
– Main Products: Collaborative robots, palletizing robots, robotic arms.
– Website: [AUBO Robotics](http://www.aubo-robotics.cn/)
10. Keenon Robotics Co., Ltd.
– Main Products: Delivery robots, service robots, robotic palletizers.
– Website: [Keenon Robotics](http://www.keenonrobot.com/)
These companies represent the cutting edge of automation technology in China, providing efficient and advanced robotic palletizing solutions for various industries.
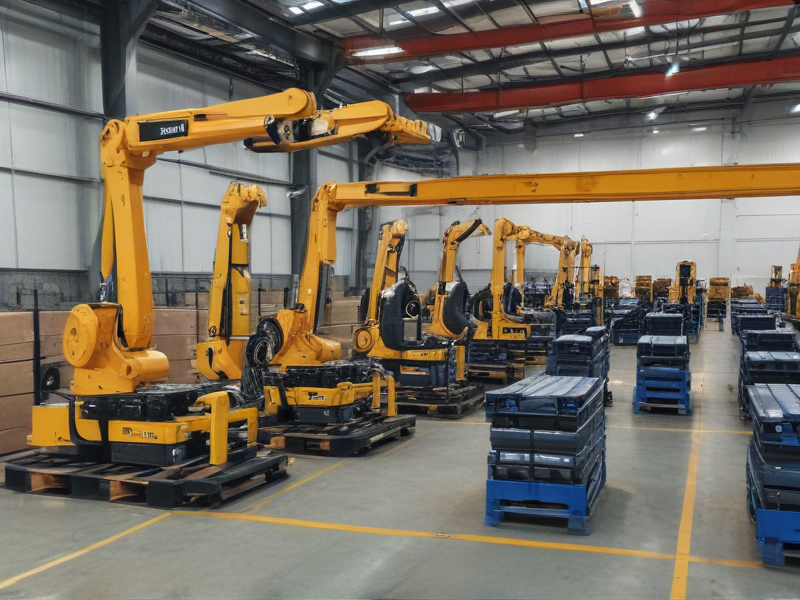
Types of automatic robotic palletizer
Automatic robotic palletizers efficiently arrange products onto pallets, streamlining warehouse operations. Several types are available, each suited to different applications and needs:
1. Cartesian Palletizers: These use linear axes (X, Y, Z) to move products. They are ideal for simple, repetitive palletizing tasks, offering precision and reliability. Cartesian systems are often more affordable but less flexible compared to more advanced robots.
2. Articulated Arm Palletizers: These feature a multi-jointed arm (often with six degrees of freedom) that can mimic human arm movements. They’re highly versatile and can handle a variety of product shapes and sizes. These robots are suitable for dynamic and complex palletizing scenarios.
3. Collaborative Robots (Cobots): Designed to work alongside humans safely, cobots combine flexibility and ease of programming. They are useful in environments where space is limited or where human-robot interaction is necessary.
4. Gantry Palletizers: Similar to Cartesian but generally larger and capable of handling heavier loads, they move along a gantry structure covering larger areas. They are used in applications requiring lifting and positioning of heavy or bulky items.
5. Delta Robots: Known for their high speed and accuracy, delta robots are typically used for high-speed pick-and-place tasks. They are less common for palletizing heavy items but excel in handling lightweight, small products efficiently.
6. Hybrid Palletizers: These combine elements from different robotic types to leverage their benefits. For instance, a hybrid system might use a gantry for heavy lifting while employing an articulated arm for precise placement.
Each type offers distinct advantages tailored to specific palletizing needs, from speed and accuracy to load capacity and flexibility. Selection depends on the application’s complexity, required throughput, and product characteristics.
Pros and Cons of Using automatic robotic palletizer
### Pros and Cons of Using Automatic Robotic Palletizer
#### Pros:
1. Increased Efficiency:
– Speed: Robotic palletizers can operate continuously without breaks, significantly increasing the speed of palletizing operations compared to manual labor.
– Consistency: Robots perform with a high degree of precision and repeatability, ensuring consistent pallet stacks and reducing the risk of errors.
2. Cost Savings:
– Labor Costs: Reduces the need for manual labor, which can result in long-term cost savings on wages and associated benefits.
– Minimal Downtime: Robots require less downtime, leading to higher productivity rates.
3. Safety:
– Reduced Injuries: Minimizes the risks of workplace injuries related to heavy lifting and repetitive tasks, improving overall worker safety.
– Hygiene: Ideal for industries requiring strict hygiene standards, as robots can work in environments unsuitable for humans.
4. Flexibility and Scalability:
– Versatility: Capable of handling various product sizes, shapes, and weights with minimal adjustments.
– Scalability: Easily adaptable to changes in production demands and can be integrated into existing systems.
#### Cons:
1. High Initial Investment:
– Cost: Significant upfront costs for purchasing and installing robotic palletizing systems.
– Maintenance: Ongoing costs for maintenance and potential need for specialized technical support.
2. Complexity:
– Implementation: Requires careful planning and integration with existing processes, which can be time-consuming and complex.
– Training: Workers will need to be trained to operate and troubleshoot the robotic systems, incurring additional training costs.
3. Technical Issues:
– Downtime: Potential for technical failures or malfunctions, which can lead to production downtime if not promptly addressed.
– Dependency: Over-reliance on automation can be risky if alternative manual processes are not in place for emergencies.
4. Job Displacement:
– Employment Impact: Potential reduction in manual labor jobs, which can have economic and social implications for workers.
In conclusion, while automatic robotic palletizers offer significant benefits in terms of efficiency, safety, and cost savings, they also come with challenges like high initial costs, complexity, and potential workforce displacement. Businesses must weigh these factors carefully to determine if automation aligns with their operational goals and capabilities.
automatic robotic palletizer Reference Specifications (varies for different product)
Automatic Robotic Palletizer Reference Specifications
1. Payload Capacity:
– Varies based on model; typically ranges from 50kg to 500kg.
2. Palletizing Speed:
– Up to 30 cycles per minute, depending on product weight and configuration.
3. Reach:
– Effective working envelope ranging from 1.8 meters to 3.15 meters.
4. Precision:
– Repeatability within ±0.1mm to ±0.5mm.
5. Gripper Technology:
– Customizable end-effectors: mechanical, vacuum, or magnetic grippers for different product types.
6. Product Types Supported:
– Boxes, cartons, bags, pails, drums, and custom shapes.
7. Pallet Configuration:
– User-defined patterns, supporting single and multi-pallet systems.
8. Control System:
– Advanced HMI with programmable logic controller (PLC) integration.
– Ethernet/IP, Modbus, and other communication protocols supported.
9. Safety Features:
– Light curtains, emergency stop buttons, and safety fencing.
– Compliance with ISO 10218-1 and ISO 13849-1 standards.
10. Power Requirements:
– Voltage: 380V to 480V, 3-phase.
– Power Consumption: Variable, typically 1.5kW to 5kW.
11. Environmental Conditions:
– Operating Temperature: 0°C to 45°C.
– Humidity: ≤ 85%, non-condensing.
12. Cycle Automation:
– Integration with conveyor systems for automatic feeding and discharge.
– Vision systems for quality inspection.
13. Maintenance:
– Predictive maintenance algorithms.
– Quick-change components and modular design for easy servicing.
14. Footprint:
– Compact design to fit within varied factory layouts, typically requiring 4m² to 10m².
15. Software:
– Intuitive programming interface.
– Remote diagnostics and update capabilities.
These specifications can vary significantly based on the robotic palletizer model and intended application. Always consult the manufacturer for detailed requirements and custom solutions.
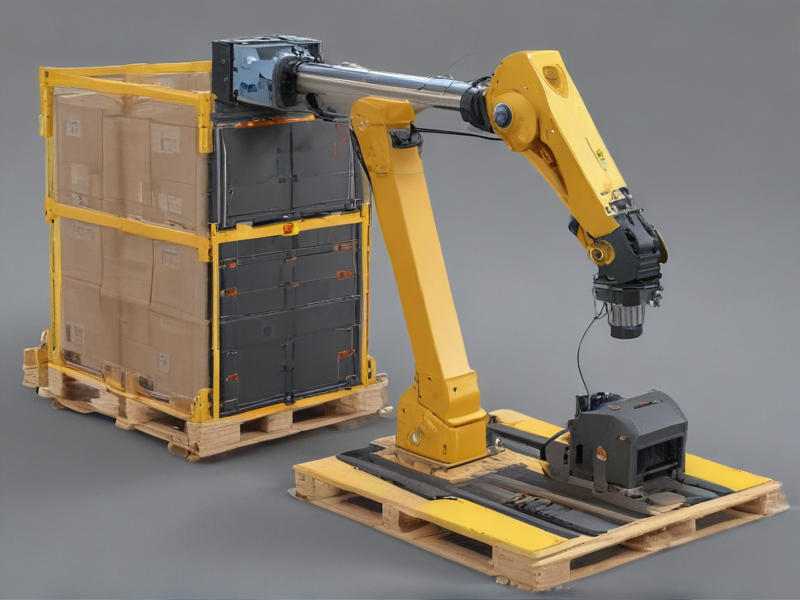
Applications of automatic robotic palletizer
Automatic robotic palletizers offer significant benefits across various industries by optimizing the process of stacking products onto pallets for storage or shipment. Their applications are extensive and diverse:
1. Food and Beverage Industry: Robotic palletizers handle boxes, bottles, and cans with precision, ensuring hygiene and speeding up operations. They handle sensitive items, reducing the risk of damage during stacking.
2. Pharmaceuticals: In this highly regulated sector, robotic palletizers ensure accurate, contamination-free handling of products such as medicines and medical supplies, adhering to stringent standards.
3. Consumer Goods: For manufacturers of products like detergents, cosmetics, and electronics, these palletizers offer flexible stacking patterns and can quickly adapt to different packaging sizes and shapes, enhancing efficiency and throughput.
4. Automotive and Manufacturing: Heavy components such as engine parts, tires, and assembled products require robust palletizing solutions. Robots cater to these demands with precision and strength, improving workplace safety by minimizing manual handling.
5. Retail and E-commerce: With the surge in online shopping, palletizers are essential in distribution centers for organizing diverse items swiftly and correctly, aiding in faster and more accurate order fulfillment.
6. Agricultural Products: They efficiently handle bags of seeds, fertilizers, and other farm products, ensuring organized and secure pallet loads ready for transport, reducing labor intensity, and increasing productivity.
7. Building Materials: Industries producing bricks, tiles, and other heavy construction materials benefit from robotic palletizers due to their ability to manage heavy loads and work continuously without fatigue.
8. Chemical Industry: Handling chemicals requires precision and safety. Robotic palletizers manage drums, containers, and other packages, reducing human exposure to hazardous materials.
Robotic palletizers are integral to modern industrial automation, offering reliability, speed, and safety, thereby transforming the efficiency of supply chains across various sectors.
Material of automatic robotic palletizer
An automatic robotic palletizer is typically composed of several essential materials that contribute to its functionality, durability, and efficiency. Key materials include:
1. Steel: The frame and structural components are usually made of high-grade steel, such as carbon steel or stainless steel. Steel provides the necessary strength and durability to handle heavy loads and endure long-term usage. Stainless steel may be preferred in food and pharmaceutical industries due to its corrosion resistance and ease of cleaning.
2. Aluminum: Certain parts of the robotic arm or gripper might be made from aluminum to reduce weight while retaining adequate strength. Aluminum is also resistant to corrosion, which is beneficial in humid or corrosive environments.
3. Plastics and Composites: High-performance plastics like polycarbonate, ABS (Acrylonitrile Butadiene Styrene), and composites are often used for housings, covers, and non-load-bearing components. These materials are lightweight, impact-resistant, and can be molded into complex shapes.
4. Rubber and Elastomers: These materials are used for gripping pads, seals, and vibration dampening elements within the robotic palletizer. They provide the necessary friction and cushioning to securely handle various types of packages without causing damage.
5. Electronics and Sensors: Robotic palletizers incorporate numerous electronic components such as sensors, controllers, and circuit boards. These are typically made from silicon, copper, gold, and other specialized materials that facilitate precise movement and control.
6. Hydraulics and Pneumatics: Components like pistons, cylinders, and valves made from steel, aluminum, and high-strength plastics are used in the hydraulic and pneumatic systems to drive the robotic arms and gripping mechanisms.
7. Bearings and Actuators: These are crucial for the movement of the robot and are usually composed of high-quality steel for the bearings and a combination of metals and polymers for the actuators.
By carefully selecting and integrating these materials, automatic robotic palletizers can achieve optimal performance, longevity, and adaptability to various industrial settings.
Quality Testing Methods for automatic robotic palletizer and how to control the quality
Quality testing for an automatic robotic palletizer involves several methods to ensure efficiency, accuracy, and safety. Key quality testing methods include:
1. Functional Testing: Ensures the robot performs tasks correctly. This includes testing for accurate palletizing patterns, correct stacking orientation, and the ability to handle different package sizes and weights.
2. Cycle Time Testing: Measures the time taken to complete a palletizing cycle. A target benchmark must be set, and the robot’s performance compared to ensure it meets production requirements.
3. Load Testing: Assesses the robot’s capability to handle maximum and varied loads without failure. This ensures robustness and longevity under different operational scenarios.
4. Vision System Testing: If equipped, the vision system must be tested for accuracy in identifying and positioning packages. This includes verifying object recognition, alignment correction, and detecting irregularities.
5. Safety Testing: Ensures compliance with safety standards. Sensors, emergency stop buttons, and guarding systems must be rigorously tested to prevent accidents.
6. Environmental Testing: Evaluates performance under different environmental conditions such as temperature variations, humidity, and dust levels. This is crucial for ensuring reliable operation in real-world settings.
Quality control techniques include:
1. Statistical Process Control (SPC): Utilizes control charts to monitor the robot’s performance over time. Trends and variances are analyzed to detect deviations from desired performance.
2. Preventive Maintenance Checks: Regularly scheduled inspections and maintenance keep the robot functioning optimally. Logs of these checks provide a history of performance and issues.
3. Calibration: Regular calibration of sensors and actuators ensures precision in operations.
4. Training and Documentation: Operators and maintenance staff should be well-trained. Detailed documentation of procedures and troubleshooting guides helps maintain consistent quality control.
5. Automation Feedback: Implement feedback loops within the software to detect and adjust for errors in real-time, improving accuracy and reliability.
By employing these testing methods and control techniques, the quality of automatic robotic palletizers can be effectively maintained and enhanced.
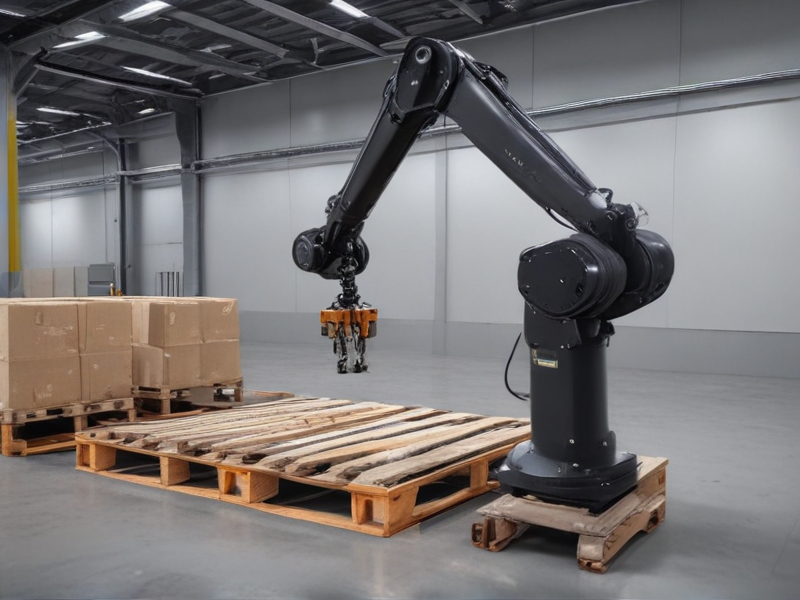
The Work Process and how to use automatic robotic palletizer
A robotic palletizer is an automated system designed to load products onto pallets for storage or transportation. Here’s a concise guide to its work process and usage:
### Work Process
1. Product Infeed:
– Products are conveyed to the palletizer via a conveyor system.
– The system identifies and aligns products.
2. Robotic Arm Operation:
– The robotic arm, equipped with a gripper or suction device, picks up products.
– It places products on the pallet in a pre-programmed pattern.
3. Layer Formation:
– Products are often stacked in layers, which may involve rotation or repositioning.
– Spacers or sheets can be placed between layers to enhance stability.
4. Pallet Handling:
– Once a pallet is fully loaded, it is transferred to an output conveyor or storage.
– An empty pallet is then automatically positioned for loading.
### How to Use
1. Setup:
– Configuration: Input product dimensions, weight, and pallet pattern into the control software.
– Safety Checks: Ensure safety barriers and emergency stop functions are active.
– Calibration: Calibrate the robotic arm and sensors for accuracy.
2. Operation:
– Start System: Initiate the system via the control panel.
– Monitoring: Regularly monitor the process through the Human-Machine Interface (HMI) to ensure smooth operation.
– Troubleshooting: Address any faults or jams promptly using diagnostic tools provided in the system.
3. Maintenance:
– Routine Inspections: Conduct regular checks for wear and tear on mechanical parts.
– Software Updates: Keep the control software updated for optimal performance.
– Cleanliness: Maintain a clean operating environment to prevent sensor and actuator malfunctions.
By following these steps, an automatic robotic palletizer can significantly enhance efficiency, accuracy, and safety in material handling and storage operations.
automatic robotic palletizer Importing questions including Cost,Supplier,Sample,Certification and Market
When looking to import an automatic robotic palletizer, several critical questions need to be addressed to ensure a smooth and successful acquisition:
1. Cost:
– What is the base price of the automatic robotic palletizer?
– Are there additional costs for customization, installation, and training?
– What are the shipping and import duties?
2. Supplier:
– Who are the reputable suppliers and manufacturers of these palletizers?
– Can the supplier provide references or case studies of previous installations?
– What are the terms of sale and return policies?
3. Sample:
– Is it possible to obtain a demo unit or sample for evaluation?
– Can the supplier provide a virtual or physical demonstration of the palletizer in action?
– What is the lead time for receiving a sample unit?
4. Certification:
– Does the palletizer meet international standards and certifications such as CE, ISO, or UL?
– Are there any local certifications required for importing and operating the machine in your country?
– Can the supplier provide all necessary documentation for compliance?
5. Market:
– What is the current market demand for automatic robotic palletizers?
– Who are the key competitors in this market?
– What are the latest technological trends and innovations in palletizing robotics?
– How will this investment impact your company’s operational efficiency and ROI?
Addressing these questions will enable you to make a more informed decision about importing an automatic robotic palletizer, ensuring that you find a solution that meets your operational needs and complies with all regulatory requirements.
How to find and select check reliable automatic robotic palletizer manufacturers in China
To find and select reliable automatic robotic palletizer manufacturers in China, follow these steps:
1. Online Research:
– Use professional platforms like Alibaba, Made-in-China, and Global Sources.
– Filter results by verified suppliers and look for companies with years of experience and positive reviews.
2. Trade Shows:
– Consider visiting trade shows such as the Canton Fair or CIIF (China International Industry Fair) to meet manufacturers in person.
3. Company Reputation:
– Check for certifications like ISO 9001, CE, and other relevant standards.
– Look for awards or recognitions within the industry.
4. Client References and Reviews:
– Ask for client references.
– Read reviews and testimonials on third-party websites.
5. Facility Visit:
– If possible, visit the manufacturer’s facility to see their production capabilities and quality control processes.
6. Technical Support and Service:
– Ensure the company provides robust after-sales support, including installation, training, and maintenance services.
7. Customization and Flexibility:
– Check if they offer customization options to meet specific needs.
– Evaluate their flexibility in handling different project scales.
8. Sample Orders:
– Start with a small order to evaluate product quality and performance.
9. Compare Quotes:
– Request detailed quotes from multiple suppliers.
– Compare not just prices but also the inclusions such as warranty, lead time, and service.
10. Contract and Terms:
– Carefully review the terms of service, warranty, and return policy.
– Ensure all agreements are in writing.
By systematically evaluating these factors, you can identify and select a reliable manufacturer that meets your specific needs.
Background Research for automatic robotic palletizer manufacturers Companies in China, use qcc.com archive.org importyeti.com
Conducting background research on automatic robotic palletizer manufacturers in China can provide essential insights. The following sources and approaches are utilized: qcc.com, importyeti.com, and archive.org.
QCC.com:
QCC.com is a comprehensive database of Chinese companies. With its user-friendly interface, one can explore various manufacturers specializing in robotic palletizers. Important metrics such as company registration details, financial health, certifications, and operational scales are accessible. Leading companies in this sector include:
1. Siasun Robot & Automation Co., Ltd: Known for advanced automation and robotics solutions.
2. Guangzhou Risun Automation Technology Co., Ltd.: Specializes in industrial robotics and automatic palletizing systems.
ImportYeti.com:
ImportYeti offers insights into global trade data, particularly focusing on shipments and trade partners. By examining import records, a clearer picture of the export capabilities and international reach of Chinese palletizer manufacturers can be achieved. Noteworthy insights include:
1. QuickTime Robotics: Shows substantial export data indicating international market acceptance.
2. ABB Robotics (China): Has significant shipment records, reflecting robust demand for their palletizing solutions.
Archive.org:
Archive.org can be used to access historical snapshots of company websites and digital archives. This helps in understanding the evolution and technological advancements of manufacturers over time. For historical data:
1. Estun Automation: Archival data reveals consistent product innovation and expanding global footprint over the years.
2. EFORT Intelligent Equipment Co., Ltd: Archived web records show their growth trajectory and strategic expansions.
By leveraging these sources, a comprehensive view of the automatic robotic palletizer manufacturers in China can be developed, encompassing current capabilities, historical growth, and international trade activities. This consolidated information aids in identifying key players and evaluating their market positions effectively.
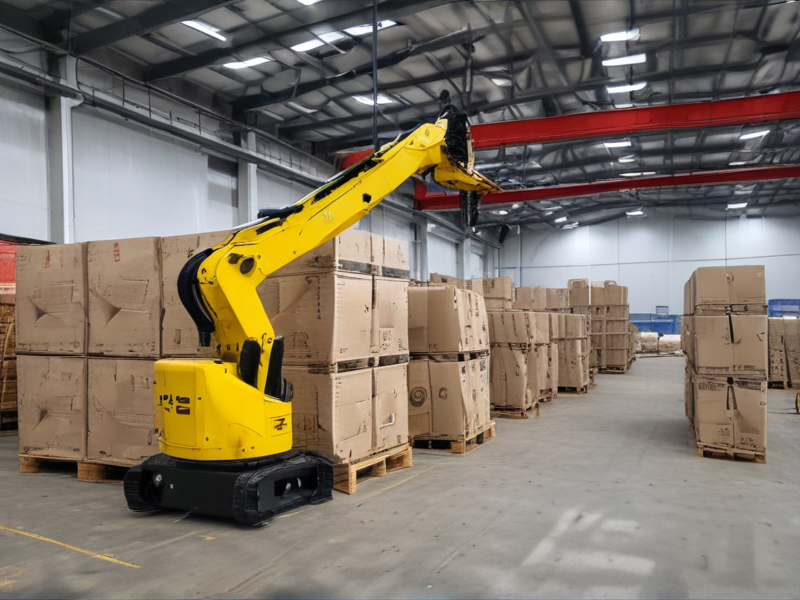
Price Cost Research for automatic robotic palletizer manufacturers Companies in China, use temu.com and 1688.com
Conducting price cost research for automatic robotic palletizer manufacturers in China using platforms like Temu.com and 1688.com can provide insights into the competitive landscape and potential pricing for these advanced machines.
### Temu.com
Temu is primarily a consumer-oriented platform and may have limited industrial automation listings. However, it can be useful for basic comparisons or understanding consumer electronics and smaller scale automation systems. Browsing through Temu, you may find basic models and components in the range of $10,000 to $50,000 depending on complexity and specifications. For detailed and accurate pricing on industrial-grade palletizers, manufacturers often direct inquiries from Temu to their official websites or sales teams for bespoke quotes.
### 1688.com
1688.com, run by Alibaba Group, serves as a significant B2B platform, making it more suitable for industrial equipment like robotic palletizers. By searching for “automatic robotic palletizer” (自动化机器人码垛机) on 1688.com, several listings from various manufacturers can be found.
1. Product Listings and Prices:
– Entry-level models: Prices generally start around ¥80,000-¥150,000 ($11,000-$22,000).
– Intermediate models: These can range between ¥200,000-¥400,000 ($29,000-$58,000), offering better customization and higher throughput.
– Advanced models: High-end systems featuring sophisticated robotics and automation can cost from ¥500,000 (~$73,000) and beyond, depending on specific capabilities and integration needs.
2. Manufacturers:
– Topstar TZ: Offers mid to high-range models with advanced features.
– KUKA Robotics China: Known for high-end palletizing solutions with robust performance.
– Nanjing Estun Automation: Provides a competitive range of mid-tier to premium options.
### Conclusion
Prices for automatic robotic palletizers in China vary widely based on functionality, capacity, and technology. For mid-tier models, expect to spend around $20,000-$60,000, while high-end models may require significantly higher budgets. Utilizing platforms like 1688.com offers a comprehensive view, but direct negotiations with suppliers are recommended for precise costing and customization.
Shipping Cost for automatic robotic palletizer import from China
The shipping cost for importing an automatic robotic palletizer from China can vary significantly based on several key factors:
1. Size and Weight: Palletizers are typically heavy and bulky, impacting both volumetric and actual weight, both of which are crucial for determining shipping costs.
2. Shipping Method:
– Air Freight: Faster but more expensive. Suitable for urgent needs or smaller equipment. Costs range from $5 to $8 per kilogram, potentially more.
– Sea Freight: More economical for heavy machinery, but slower. Costs usually range from $100 to $200 per cubic meter (CBM).
3. Origin and Destination: The distance between the Chinese port (e.g., Shanghai, Shenzhen) and the destination port affects the cost. Proximity to major shipping routes reduces costs.
4. Customs and Duties: Import duties, taxes, and clearance fees vary by destination country. For instance, the US might charge 0% to 5% duty on industrial machinery.
5. Insurance: Optional but recommended, especially for high-value equipment. Costs about 0.3% to 0.5% of the total shipment value.
6. Additional Fees: Loading/unloading, documentation, and handling charges are also part of the total shipping cost.
Example Calculation (Sea Freight):
– Palletizer Weight: 1000 kg
– Volume: 5 CBM
– Sea Freight Rate: $150 per CBM
– Total Freight Cost: 5 CBM * $150 = $750
– Insurance (0.4% of $50,000 value): $200
– Duties/Taxes (estimate 3% of value, $50,000): $1,500
– Additional Fees: $200
Estimated Total Shipping Cost = $750 (freight) + $200 (insurance) + $1,500 (duties) + $200 (fees) = $2,650
Costs vary, so getting multiple quotes from freight forwarders is advisable for accuracy.
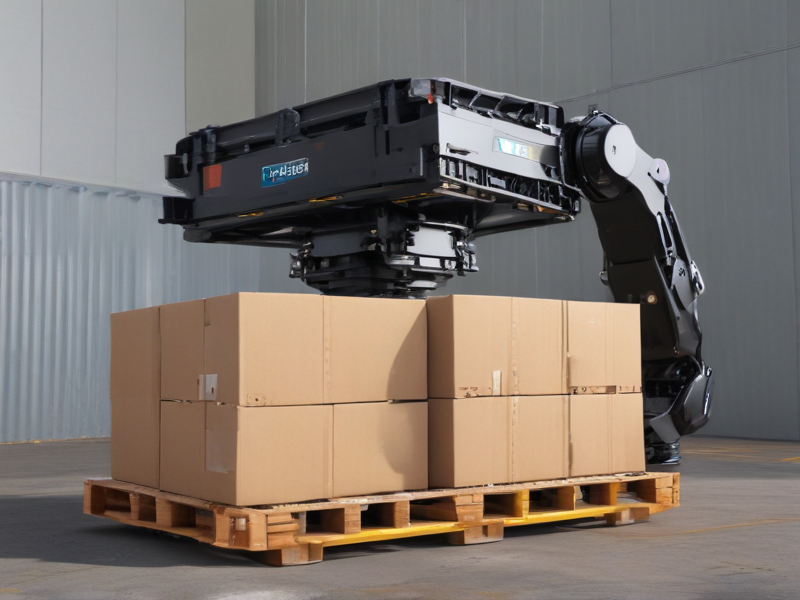
Compare China and Other automatic robotic palletizer Markets: Products Quality and Price,Visible and Hidden Costs
China has emerged as a significant player in the automatic robotic palletizer market, often standing out for its competitive pricing and growing quality. Comparatively, markets like the U.S., Germany, and Japan are known for exceptional product quality but generally command higher prices.
Product Quality and Price:
– China: Chinese palletizers are often more affordable due to lower labor costs and economies of scale in manufacturing. However, the gap in quality is narrowing, and many Chinese manufacturers now produce reliable and durable palletizers.
– U.S., Germany, Japan: These markets prioritize high-quality components and stringent engineering standards. As a result, their palletizers tend to be more efficient, durable, and feature-rich but come with a higher price tag.
Visible and Hidden Costs:
– Visible Costs: Chinese palletizers are typically cheaper upfront, offering cost savings on initial purchase. Western and Japanese options have higher upfront costs but may offer better long-term reliability and efficiency.
– Hidden Costs: Purchasing from China may incur additional costs such as higher shipping fees, longer lead times, and potentially more customs duties. Additionally, after-sales service and spare parts availability might be less efficient, leading to longer downtimes.
In contrast, Western and Japanese manufacturers often provide excellent customer support, faster response times, and readily available spare parts, reducing potential downtime costs. However, these benefits come at a premium.
Conclusion:
Choosing between Chinese and other renowned markets involves balancing initial costs with long-term reliability and service. While China offers cost-effective options with improving quality, Western and Japanese palletizers often justify their higher prices through superior quality, efficiency, and service.
Custom Private Labeling and Branding Opportunities with Chinese automatic robotic palletizer Manufacturers
Partnering with Chinese manufacturers for custom private labeling and branding of automatic robotic palletizers provides many compelling opportunities for businesses. China, known for its advanced manufacturing capabilities and cost-effective production, offers a range of benefits for companies seeking customized automation solutions.
1. Cost Efficiency: Chinese manufacturers often present more competitive pricing compared to Western counterparts while maintaining high quality. This allows businesses to offer advanced technologies at more accessible price points.
2. Customization: Many Chinese manufacturers provide extensive customization options, enabling companies to align products closely with brand specifications. Whether it’s design, features, or functionality, businesses can develop a palletizer that meets their unique requirements.
3. Advanced Technology: Chinese manufacturers invest heavily in R&D and incorporate the latest advancements in robotics and automation. This ensures the products are equipped with cutting-edge technology and efficient performance metrics.
4. OEM/ODM Services: Original Equipment Manufacturer (OEM) and Original Design Manufacturer (ODM) services are readily available, allowing companies to easily brand and package the palletizers under their own labels. This flexibility supports brand differentiation and market competitiveness.
5. Speed to Market: The robust supply chain infrastructure in China enables faster production cycles and delivery times. Businesses can quickly adapt to market demands and timely update their offerings.
6. Strategic Partnerships: Building strategic partnerships with Chinese manufacturers can lead to long-term collaborations, fostering innovation and continual improvement in product offerings.
7. Regulatory Compliance: Reputable Chinese manufacturers stay abreast of international standards and regulations, ensuring their products comply with necessary certifications and industry norms.
By leveraging these opportunities, businesses can enhance their product portfolios, achieve superior brand positioning, and drive increased market share through strategically sourced, customized automatic robotic palletizers.
Tips for Procurement and Considerations when Purchasing automatic robotic palletizer
When purchasing an automatic robotic palletizer, several key considerations can help ensure long-term efficiency and cost-effectiveness. Here are some essential tips to guide your procurement process:
1. Assess Your Needs: Evaluate the specific requirements of your operation, such as palletizing speed, load capacity, and the types of products you need to handle. Understanding these parameters helps in selecting the right model.
2. Space Requirements: Ensure you have adequate space for installation and operation. Measure the available area and compare it with the spatial specifications of the palletizer.
3. Flexibility and Scalability: Opt for a palletizer that can adapt to different sizes and shapes of products. Scalability is important if you anticipate changes in production volume.
4. Integrations and Compatibility: Check compatibility with existing systems, such as conveyors and warehouse management systems. Seamless integration can significantly boost operational efficiency.
5. Ease of Use: Look for user-friendly interfaces and straightforward programming options. This minimizes training time and reduces the likelihood of operational errors.
6. Safety Features: Safety should be a priority. Ensure the palletizer has safety features like emergency stop buttons, safety fences, and sensors to prevent accidents.
7. Maintenance and Support: Consider the ease of maintenance and availability of spare parts. Select a vendor who offers robust after-sales support and maintenance services.
8. Energy Efficiency: Energy-efficient models can lead to significant cost savings over the machine’s lifespan. Check the energy consumption ratings and explore potential for energy recovery options.
9. Vendor Reputation: Research the reputation of the vendor. Customer reviews, case studies, and references can provide insights into their reliability and customer service quality.
10. Cost-Benefit Analysis: Perform a thorough cost-benefit analysis, considering not just the initial investment but also long-term operational costs, potential downtime, and return on investment (ROI).
By paying attention to these factors, you can make a well-informed decision that aligns with your operational goals and budget constraints.
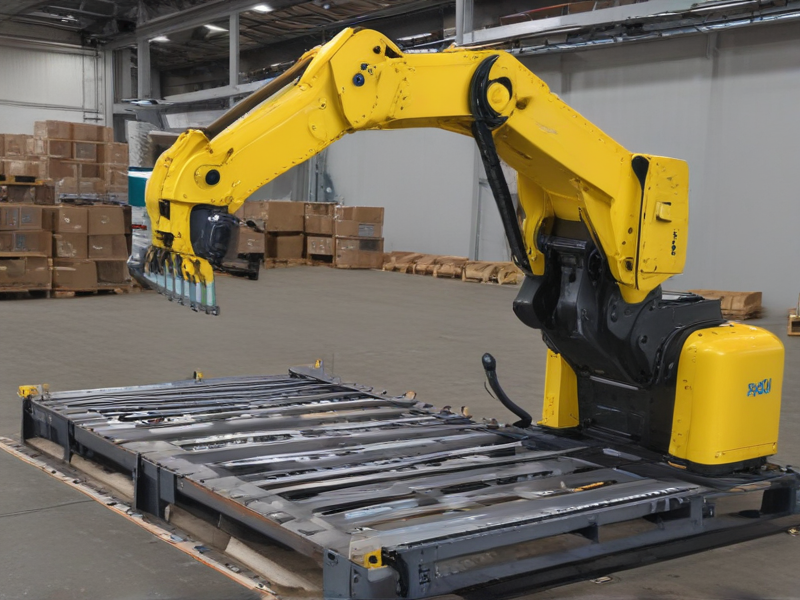
FAQs on Sourcing and Manufacturing automatic robotic palletizer in China
Sourcing and manufacturing an automatic robotic palletizer in China can offer significant cost savings and high-quality products. Below are some frequently asked questions (FAQs) to help guide you through the process:
### 1. Why source a robotic palletizer from China?
China is a leading manufacturer of industrial automation equipment, including robotic palletizers. They offer competitive pricing, advanced technology, and a skilled workforce, making it an attractive option for businesses worldwide.
### 2. What are the key factors to consider when choosing a supplier?
– Reputation: Look for suppliers with a strong industry reputation and positive reviews.
– Certifications: Ensure they have necessary certifications like ISO9001.
– Experience: Suppliers with experience in manufacturing robotic palletizers.
– Customization: Ability to customize based on your specific requirements.
– After-sales Support: Availability of comprehensive after-sales services.
### 3. How do I vet potential manufacturers?
– Factory Visits: When possible, visit the factory to inspect facilities and processes.
– Sample Products: Request samples to evaluate quality.
– Third-party Inspections: Hire third-party inspectors for independent assessments.
– References: Ask for references from previous clients.
### 4. What are the common challenges in this process?
– Communication Barriers: Language differences can lead to misunderstandings.
– Quality Control: Ensuring consistent product quality can be challenging.
– Logistics: Navigating international shipping and customs.
### 5. What are the typical lead times?
Lead times can vary but typically range from 8-12 weeks, depending on the complexity of the customization and current production schedules.
### 6. How do I ensure quality control?
– Inspections: Regular factory inspections and third-party quality checks.
– Clear Specifications: Provide detailed technical specifications and quality standards.
– Initial Orders: Place smaller initial orders to evaluate quality and reliability.
### 7. How does the payment process work?
Common payment terms include a down payment (30-50%) with the balance paid upon completion or before shipping. Payment methods often include T/T (Telegraphic Transfer) and L/C (Letter of Credit).
By carefully selecting your supplier and maintaining rigorous quality control, you can successfully source a reliable and cost-effective robotic palletizer from China.