Top 10 bag filling system in China introduce,list main products and website if have
Sure, here are the top 10 bag filling systems in China:
1. **Wuxi Sici Auto Co., Ltd.**
– **Main Products:** Automatic bagging machines, packaging equipment, automatic stacking machines.
– **Website:** [siciauto.com](http://www.siciauto.com/)
2. **Guangdong Kenwei Intellectualized Machinery Co., Ltd.**
– **Main Products:** Multihead weighers, automatic packaging machines, checkweighers.
– **Website:** [kenweigh.com](http://www.kenweigh.com/)
3. **Newamstar Packaging Machinery Co., Ltd.**
– **Main Products:** Filling machines, packaging lines, liquid packaging machinery.
– **Website:** [newamstar.com](http://www.newamstar.com/)
4. **Shanghai Shouda Packaging Machinery Co., Ltd.**
– **Main Products:** Liquid filling machines, capping machines, labeling machines.
– **Website:** [shoudapack.com](http://www.shoudapack.com/)
5. **Jiangsu Zhongtai Packing Machinery Co., Ltd.**
– **Main Products:** Bag filling machines, powder packing machines, granule packing machines.
– **Website:** [ztoem.com](http://www.ztoem.com/)
6. **Foshan Land Packaging Machinery Co., Ltd.**
– **Main Products:** Vertical form fill seal machines, weighing packaging systems.
– **Website:** [landpacking.net](http://www.landpacking.net/)
7. **Guangdong Chaoqiang Electronic Technology Co., Ltd.**
– **Main Products:** Weight sorting machines, bag filling machines.
– **Website:** [chaokezdh.com](http://www.chaokezdh.com/)
8. **Anhui Zengran Packaging Technology Co., Ltd.**
– **Main Products:** Bag packing machines, automatic packing systems, vacuum packaging.
– **Website:** [zengranpack.com](http://www.zengranpack.com/)
9. **Wuhan Huale Machinery Co., Ltd.**
– **Main Products:** Bagging machines, powder packing machines, liquid packaging systems.
– **Website:** [hualemachine.com](http://www.hualemachine.com/)
10. **Shanghai Acepack Intelligent Technology Co., Ltd.**
– **Main Products:** Pre-made pouch packing machines, VFFS machines, stick pack machines.
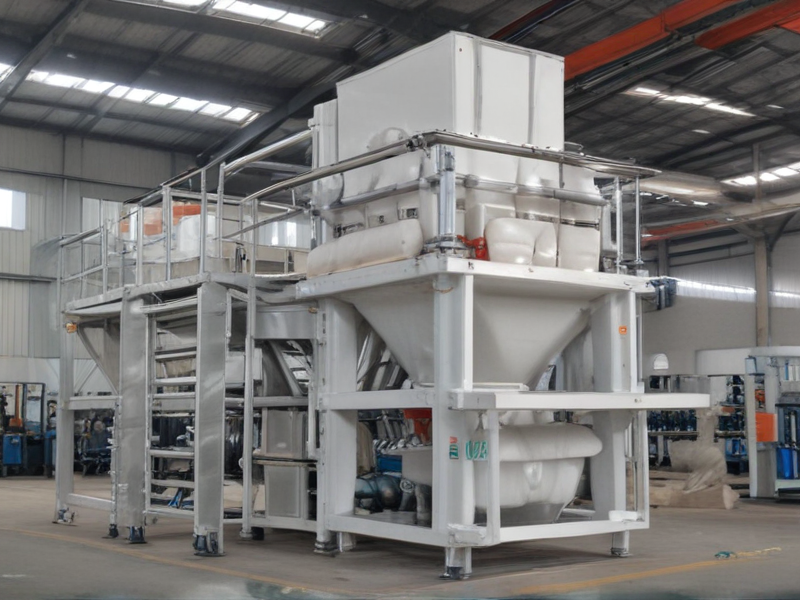
Types of bag filling system
Bag filling systems are essential for efficiently packaging a wide range of products across various industries, including food, pharmaceuticals, agriculture, and chemicals. Here are some common types:
1. **Manual Bag Filling Systems**:
– **Description**: Operators manually place the bags to be filled under the spout.
– **Pros**: Cost-effective, suitable for low-volume production.
– **Cons**: Labor-intensive and slower compared to automated systems.
2. **Semi-Automatic Bag Filling Systems**:
– **Description**: Combines manual bag placement with automated filling processes. Operators usually place and remove the bags, while the machine measures and fills them.
– **Pros**: Enhanced accuracy and efficiency over fully manual systems.
– **Cons**: Requires some labor; not fully automated.
3. **Automatic Bag Filling Systems**:
– **Description**: Fully automated from bag placement to sealing. The system handles product measurement, bag orientation, filling, sealing, and even packaging.
– **Pros**: High speed, consistency, reduced labor costs.
– **Cons**: Higher initial investment and maintenance costs.
4. **Gravity-Fed Bag Filling Systems**:
– **Description**: Uses gravity to fill bags. Ideal for free-flowing materials like grains or pellets.
– **Pros**: Simple and cost-effective.
– **Cons**: Limited to specific types of materials.
5. **Vacuum Bag Filling Systems**:
– **Description**: Removes air from the product before sealing to reduce product bulk.
– **Pros**: Great for perishable food items, improves product shelf-life.
– **Cons**: More complex and expensive.
6. **Net-Weigh Bag Filling Systems**:
– **Description**: Pre-weighs the product in a separate chamber before filling the bag.
– **Pros**: High precision, suitable for high-value or regulated products.
– **Cons**: More complex, higher cost.
7. **Valve Bag Filling Systems**:
– **Description**: Uses a valve bag that has a small opening through which the product is filled.
– **Pros**: Used for fine powders needing dust-free packing.
– **Cons**: More specialized and can be limited in application.
Each type caters to different requirements based on the product type, production volume, and desired level of automation.
Pros and Cons of Using bag filling system
**Pros of Using Bag Filling Systems:**
1. **Increased Efficiency**: Automating the bag filling process significantly speeds up production, reducing manual labor and increasing throughput.
2. **Accuracy**: Modern bag filling systems provide precise weight measurements, minimizing product wastage and ensuring consistency.
3. **Labor Savings**: Automation reduces the need for manual handling, allowing companies to reallocate human resources to other tasks and lowering labor costs.
4. **Safety**: Using a filling system reduces the risk of repetitive strain injuries and accidents associated with manual bagging.
5. **Versatility**: Bag filling systems can handle a variety of products and bag types, making them suitable for different industries such as food, chemicals, and construction materials.
6. **Hygiene**: Automated systems minimize human contact, crucial in maintaining high hygiene standards particularly in the food and pharmaceutical industries.
7. **Scalability**: Easy to scale up or modify to meet increasing production demands without significant downtime.
**Cons of Using Bag Filling Systems:**
1. **High Initial Cost**: Investing in a bag filling system can be expensive, posing a significant upfront cost for small and medium-sized enterprises.
2. **Maintenance Requirements**: Regular maintenance is essential to ensure optimal functioning, which can be time-consuming and costly.
3. **Complexity**: Technical expertise is needed to operate and troubleshoot automated systems, potentially necessitating additional training or hiring specialized staff.
4. **Downtime**: If the system malfunctions, it can halt production, leading to potential delays and loss of revenue.
5. **Space Requirement**: These systems often require considerable floor space, which might not be feasible for smaller facilities.
6. **Dependency**: Over-relying on automation can make businesses vulnerable to technological failures or cyber threats.
7. **Flexibility**: Although versatile, some automated systems might struggle with non-standard bag types or require significant reconfiguration, impacting productivity.
In conclusion, while bag filling systems enhance productivity, safety, and accuracy, they require substantial investment and maintenance. Balancing these pros and cons is crucial depending on the specific needs and capacities of a business.
bag filling system Reference Specifications (varies for different product)
A bag filling system is tailored to meet the specific needs of different products, ensuring precise and efficient packaging. Key aspects to consider in the specification of these systems encompass:
1. **Product Type**: Compatibility with various materials such as powders, granules, or liquids. For example, a sugar filling system might focus on reducing dust, while a liquid filling system ensures spill-free operation.
2. **Bag Size and Weight**: Systems can be adjusted to fill different bag sizes and weights, typically ranging from small sachets to bulk bags (up to 2000 kg). High accuracy load cells ensure precise weight measurement, essential for costly or regulated products.
3. **Filling Speed**: Depending on the production requirement, systems can range from semi-automatic (50-100 bags/hour) to high-speed automatic machines (up to 2000 bags/hour). Operational speed should match the production line speed without compromising accuracy.
4. **Sealing Mechanism**: Adaptable sealing mechanisms such as heat sealing, stitching, or gluing ensure the integrity of bags post-filling, which is critical for product shelf-life and transportation safety.
5. **Material Handling**: A robust material feeding system – such as screw feeders for powders or gravity feeder valves for granular products – minimizes spillage and ensures consistent flow.
6. **Dust Control**: Integrated dust collection systems for powdery products help maintain a clean working environment and prevent product loss.
7. **User Interface**: Intuitive controls featuring touchscreen HMIs (Human-Machine Interfaces) facilitate easy operation and adjustments. Advanced systems might include IoT features for remote monitoring and diagnostics.
8. **Compliance and Safety**: Designed to meet industry standards including USDA, FDA, CE, or ATEX for explosive environments, ensuring compliance and worker safety.
9. **Maintenance and Durability**: Components crafted from durable materials like stainless steel for food products, and easy access for maintenance reduce downtime and enhance longevity.
10. **Customization**: Systems can be tailored with additional features such as batch coding, check weighing, or metal detection to meet specific production requirements.
In summary, the reference specifications for a bag filling system hinge on product type, accuracy, speed, safety, and ease of use, ensuring optimal performance tailored to varied packaging needs.
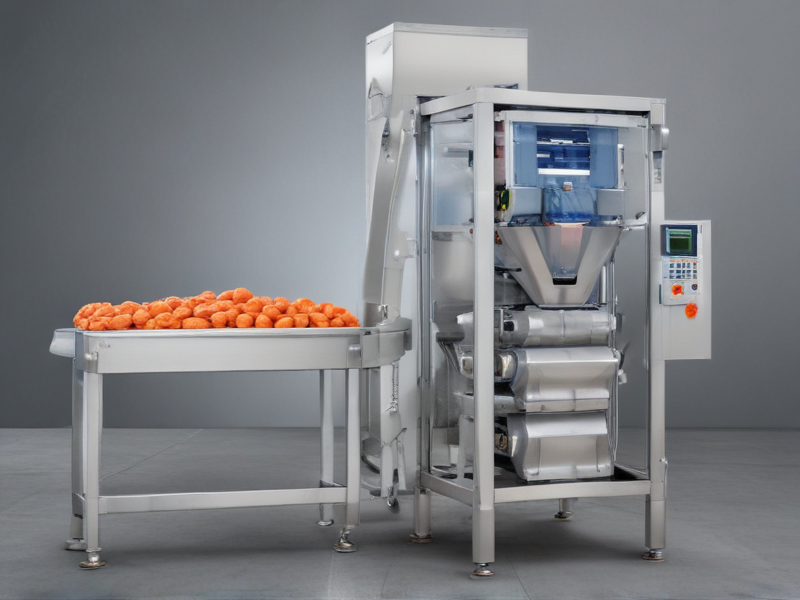
Applications of bag filling system
A bag filling system is a versatile automation tool used in various industries to efficiently fill bags with different products. Here are some key applications:
### 1. **Food Industry:**
– **Grains and Cereals:** Facilitates high-speed filling of rice, wheat, oats, and other grains.
– **Sugar and Salt:** Ensures precise measurement and filling to avoid wastage.
– **Snacks and Confectionery:** Helps in packaging chips, candies, and other snacks in a hygienic manner.
### 2. **Agriculture:**
– **Seeds:** Ensures accurate filling to maintain seed quality and prevent damage.
– **Fertilizers and Pesticides:** Allows for safe packaging of potentially hazardous materials.
### 3. **Chemical Industry:**
– **Powders and Granules:** Used for chemicals like detergents, cleaning agents, and raw material granules.
– **Industrial Chemicals:** Ensures precise and safe filling of materials requiring careful handling.
### 4. **Construction:**
– **Cement and Sand:** Facilitates the bulk packaging needed for large construction projects.
– **Mortar and Plaster:** Ensures consistent and moisture-protected filling.
### 5. **Pharmaceuticals:**
– **Medicinal Powders:** Ensures contamination-free and precise filling for medications.
– **Supplements:** Automates the packaging of dietary supplements to maintain dosage accuracy.
### 6. **Mining:**
– **Coal and Minerals:** Automates the filling process, improving speed and efficiency in mining operations.
– **Precious Metals:** Secures and measures precious material fill rates accurately.
### 7. **Pet Food:**
– **Dry Food:** Streamlines the filling of kibbles and dry pet food.
– **Feed Bags:** Enhances the packaging of large quantities of animal feed.
### 8. **Retail and Wholesale:**
– **Clothing and Textiles:** Assists in bulk packaging of clothes and textiles for retail distribution.
– **Consumer Goods:** Automates packaging of goods ranging from dry fruits to hardware items.
### 9. **Environment and Recycling:**
– **Recycled Materials:** Facilitates the packaging of recycled paper, plastics, and metals for further processing or resale.
### 10. **Other Applications:**
– **Mail Order Fulfillment:** Automates the packaging process for e-commerce companies.
– **Toys and Gifts:** Streamlines the packaging of seasonal and promotional items.
Material of bag filling system
A bag filling system is a crucial component in various industries, ensuring efficient, accurate, and hygienic packaging of products. The choice of materials for constructing a bag filling system depends on several factors, including the type of product being filled, regulatory requirements, and operational environment. Here are key material considerations:
1. **Stainless Steel:** Most bag filling systems are made from stainless steel, particularly grades like 304 and 316. Stainless steel is chosen for its corrosion resistance, durability, and ease of cleaning, making it ideal for handling food, pharmaceuticals, and other sensitive products.
2. **Aluminum:** For applications where weight is a concern, aluminum can be used for some parts of the system. It is lighter than stainless steel but doesn’t provide the same level of corrosion resistance.
3. **Polyethylene or Polypropylene:** These are used for contact parts and surfaces that handle non-food items. They are resistant to chemicals and wear while being less expensive than metals.
4. **Rubber and Elastomers:** Seals, gaskets, and flexible connections within the system often use food-grade rubber or elastomer materials. These materials need to be compliant with industry standards like FDA or EU regulations for food safety.
5. **Acetal or UHMW:** For moving parts that need to reduce friction and wear, plastics such as acetal (POM) or Ultra-High-Molecular-Weight Polyethylene (UHMW) are employed. They ensure smooth operation and reduce maintenance needs.
In summary, the optimal material selection for a bag filling system balances performance requirements, regulatory compliance, and cost-effectiveness, ensuring the system operates efficiently and safely within its designated environment.
Quality Testing Methods for bag filling system and how to control the quality
Quality testing for a bag filling system involves several methods to ensure accuracy, consistency, and safety. Here are key techniques and controls:
1. **Weight Verification**:
– **Static Weighing**: Periodic checks of filled bags on calibrated scales.
– **Dynamic Weighing**: Inline checkweighers that verify weight without stopping the production line.
2. **Filling Consistency**:
– **Volume Testing**: Ensure the system dispenses the correct volume using level sensors or flow meters.
– **Visual Inspection**: Use cameras or manual inspection to check for underfilling or overfilling.
3. **Leak Detection**:
– **Pressure Testing**: Apply pressure to check for leaks.
– **Soap Solution Test**: Apply soapy water and look for bubbles indicating a leak.
4. **Seal Integrity**:
– **Tensile Testing**: Ensure seals meet strength requirements.
– **Visual Inspection**: Regular checks for proper sealing.
5. **Material Compatibility**:
– **Sampling**: Test materials to ensure compatibility with the product.
6. **Environmental Controls**:
– **Temperature and Humidity Monitoring**: Maintain product integrity, especially for moisture-sensitive materials.
**Quality Control Measures:**
1. **Standard Operating Procedures (SOPs)**:
– Documented procedures for consistent operation and testing.
2. **Calibration**:
– Regular calibration of weighing scales, sensors, and other measurement devices.
3. **Automated Systems**:
– Use of PLCs and SCADA systems to monitor and control filling parameters.
4. **Statistical Process Control (SPC)**:
– Use SPC techniques to monitor process variability and implement corrective actions.
5. **Training**:
– Continuous training programs for operators to ensure adherence to quality standards.
6. **Audit and Inspection**:
– Internal and external audits to ensure compliance with regulatory standards.
By employing these testing methods and controls, a bag filling system can maintain high-quality standards, reduce waste, and ensure product consistency.
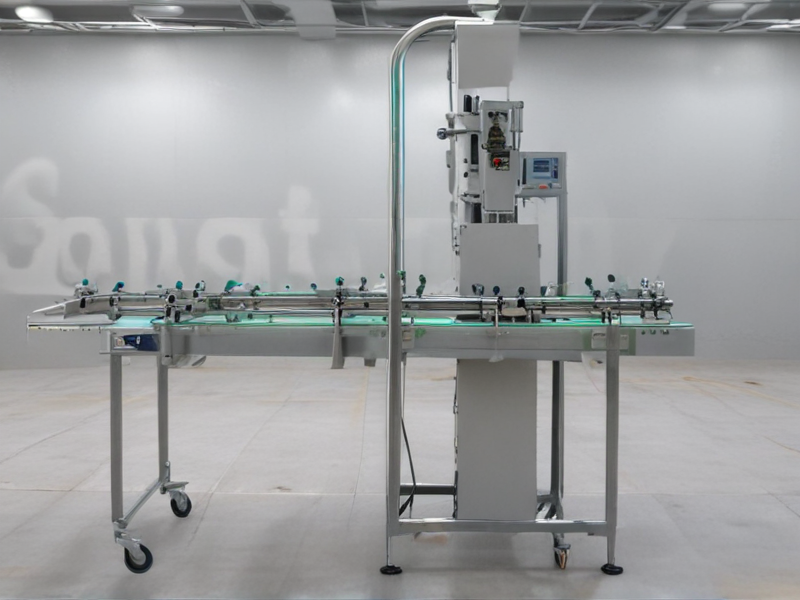
The Work Process and how to use bag filling system
A bag filling system is an automated or semi-automated machinery used to fill bags with bulk materials like grains, powders, or granules. Here’s a concise guide to its work process and usage:
### Work Process:
1. **Material Feeding**:
– The bulk material is transported from storage (e.g., a silo or hopper) to the filling system via conveyors or feeders.
2. **Bag Placement**:
– An empty bag is positioned at the filling spout. This can be done manually by an operator or automatically by a bag placer.
3. **Filling**:
– The system dispenses the precise amount of material into the bag using weigh-fill technology or volumetric filling methods.
4. **Vibration and Settling**:
– Some systems include a vibrating platform to settle the material, ensuring efficient packing and eliminating air pockets.
5. **Sealing**:
– The bag is sealed using heat sealing, stitching, or another appropriate sealing method immediately after filling to maintain product integrity.
6. **Quality Check**:
– Weight and seal quality are often checked to ensure compliance with specifications.
7. **Transport**:
– Filled and sealed bags are transported away from the filling zone by a conveyor for further handling, such as palletizing or storage.
### How to Use:
1. **Preparation**:
– Ensure materials, bags, and machine are ready. Set the desired weight or volume on the control panel.
2. **Start-Up**:
– Turn on the system and perform an initial test run with a few bags to adjust settings if needed.
3. **Loading Bags**:
– Manually or automatically load empty bags onto the spout.
4. **Monitor Operation**:
– Regularly check the filling and sealing process. Adjust settings for consistency and troubleshoot errors promptly.
5. **Post-Operation**:
– After the filling process, clean the machinery as per maintenance protocols to prevent contamination or mechanical issues.
### Safety Tips:
– Always follow manufacturer guidelines.
– Use personal protective equipment (PPE).
– Keep emergency stop controls accessible.
This streamlined process maximizes efficiency and ensures accurate, consistent bag filling.
bag filling system Importing questions including Cost,Supplier,Sample,Certification and Market
When considering importing a bag filling system, it is crucial to address several key questions to ensure a smooth and economically viable process. Here are the primary areas of focus:
### Cost
1. **Initial Costs:** What is the unit cost of the bag filling system including shipping and import duties?
2. **Ongoing Costs:** Are there any maintenance, training, or operational costs associated with the system?
3. **Payment Terms:** What are the payment terms? Is there an option for installment payments or financing?
### Supplier
1. **Reputation:** How reputable is the supplier? What do customer reviews and industry ratings say about them?
2. **Experience:** How long has the supplier been in business and how much experience do they have with international exports?
3. **Support:** Does the supplier offer technical support, and what are the terms for after-sales service and warranties?
### Sample
1. **Availability:** Can the supplier provide a sample unit or demo of the bag filling system?
2. **Cost of Sample:** Is the sample free, discounted, or charged at full price? Who covers the shipping cost?
3. **Evaluation:** How long can you evaluate the sample before committing to a bulk purchase?
### Certification
1. **Compliance:** Does the system meet local compliance and safety standards (e.g., CE, ISO, FDA)?
2. **Documentation:** Can the supplier provide necessary certifications and documentation for import?
3. **Inspection:** Is third-party inspection or certification available or required?
### Market
1. **Demand:** What is the market demand for this type of bag filling system in your region?
2. **Competition:** Who are your main competitors, and what systems do they use?
3. **Adaptability:** How adaptable is the system to the types of bags and materials predominant in your market?
Addressing these questions carefully can help you make an informed decision regarding the import of a bag filling system, balancing cost efficiency with quality and compliance.
How to find and select check reliable bag filling system manufacturers in China
To find and select reliable bag filling system manufacturers in China, follow these steps:
1. **Research Online Marketplaces**: Start with platforms like Alibaba, Made-in-China, and Global Sources. Use keywords like “bag filling system” to search for manufacturers, paying attention to user ratings and reviews.
2. **Verify Manufacturer Credentials**: Check for certifications such as ISO9001, which indicates quality management standards. Look for CE marking if you need compliance with European health, safety, and environmental requirements.
3. **Evaluate Experience and Expertise**: Prioritize manufacturers with extensive experience in producing bag filling systems. Look for information about their years in business, main products, and notable clients.
4. **Request Technical Specifications**: Contact shortlisted manufacturers to request detailed product specifications, including materials, capacity, accuracy, and any customization options. This ensures the system meets your specific needs.
5. **Ask for References**: Request references or case studies from the manufacturers to understand their track record and reliability better. Contact these references to get direct feedback.
6. **Assess Quality Control Measures**: Inquire about the manufacturer’s quality control processes. Understanding their methods for ensuring product quality can give you confidence in their reliability.
7. **Compare Quotes and Payment Terms**: Obtain detailed quotes and payment terms from multiple manufacturers. Be cautious of prices that seem too good to be true, as they may indicate compromised quality.
8. **Review After-Sales Support**: Ensure the manufacturer offers comprehensive after-sales support, including warranties, spare parts availability, and technical assistance.
9. **On-Site Visits and Inspections**: If feasible, visit the manufacturer’s facility to get a firsthand understanding of their operations and manufacturing standards. Alternatively, hire a third-party inspection service.
By thoroughly researching and vetting potential suppliers, you can effectively find a reliable bag filling system manufacturer in China.
Background Research for bag filling system manufacturers Companies in China, use qcc.com archive.org importyeti.com
When searching for manufacturers of bag filling systems in China, three valuable resources are qcc.com, archive.org, and importyeti.com. These platforms provide comprehensive insights into companies, historical data, and import/export activities respectively.
**1. Qcc.com:**
Qcc.com is an extensive database for Chinese companies, detailing their registration, financial status, and operational scope. A search for “bag filling system manufacturers” yields numerous results. Key companies include:
– **Shanghai Joygoal Food Machinery Co., Ltd.:**
Noteworthy for its extensive product line including automatic bag filling and sealing machines used for food, pharmaceutical, and chemical industries.
– **Zhejiang Dingye Machinery Co., Ltd.:**
This company focuses on a variety of packing machinery, including bag filling systems, with a strong market presence both domestically and internationally.
**2. Archive.org:**
Archive.org serves as a digital time machine, offering snapshots of websites over time. Researching historical versions of relevant websites can track the evolution of company offerings and market approaches. For example:
– **Wenzhou Accurate Machinery Manufacturing Co., Ltd.:**
By viewing previous versions of their site, one can observe advancements in their technology and expansion of their product range, indicating a sustainable growth trajectory in bag filling systems.
– **Guangzhou Rifu Packaging Machinery Co., Ltd.:**
Historical data point to a consistent development focus, improving their bag filling systems to incorporate higher efficiency and precision over the years.
**3. Importyeti.com:**
This platform analyzes shipment records to understand supply chain dynamics. Notable insights for bag filling systems point to significant exporters in China:
– **Wenzhou Chunlai Packing Machinery Co., Ltd.:**
Imports records indicate a strong international demand for their bag filling systems, highlighting the company’s reliability and global reach.
– **Ruian City Honetop Machinery Co., Ltd.:**
With substantial export activities, this company emerges as a key player capable of meeting diverse packaging needs worldwide.
In summary, leveraging qcc.com, archive.org, and importyeti.com unveils key players in the Chinese bag filling system manufacturing sector, such as Shanghai Joygoal, Zhejiang Dingye, Wenzhou Accurate, Guangzhou Rifu, Wenzhou Chunlai, and Ruian Honetop. These companies showcase robust capabilities, technological advancements, and strong international presence.
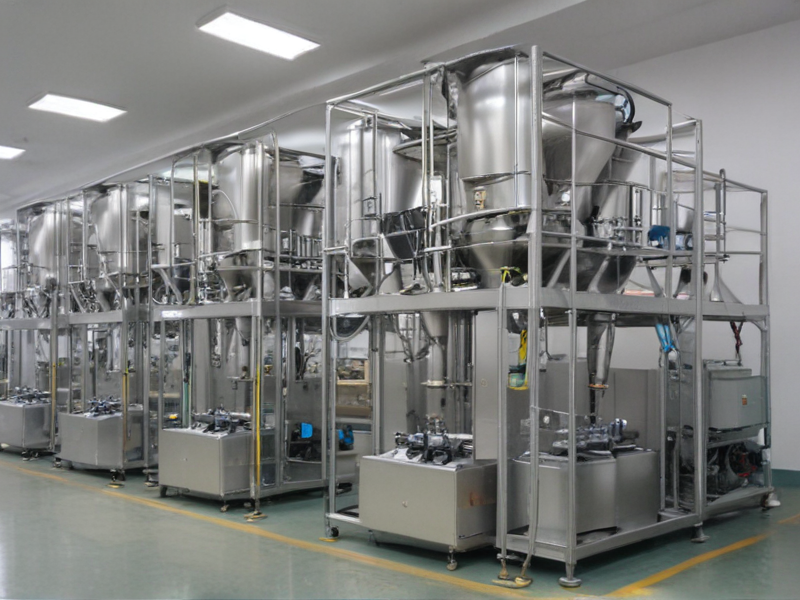
Price Cost Research for bag filling system manufacturers Companies in China, use temu.com and 1688.com
I conducted price cost research for bag filling system manufacturers using two popular Chinese e-commerce platforms: Temu.com and 1688.com. Below are the findings for prices and manufacturers.
### Temu.com
Temu.com primarily focuses on consumer goods, making industrial equipment options limited. However, a few listings for bag filling machines were found:
1. **Small-Scale Bag Filling Machine**:
– **Price**: Approximately $500 – $800
– **Features**: Suitable for small-scale operations, often used for powders and granules.
– **Manufacturers**: Various smaller manufacturers and distributors, lesser-known brands.
2. **Automatic Bag Filling Machine**:
– **Price**: $1,200 – $2,500
– **Features**: Automated systems with higher capacity, often including weighing sensors.
– **Manufacturers**: Few mid-sized manufacturers, often with basic automation.
### 1688.com
1688.com is a wholesale platform under Alibaba, catering to more industrial needs. Here are some price estimates and manufacturers for bag filling systems:
1. **Semi-Automatic Bag Filling Machine**:
– **Price**: Â¥3,000 – Â¥5,000 RMB (Approximately $450 – $750)
– **Features**: Basic semi-automation, manual supervision required, ideal for small businesses.
– **Manufacturers**: Numerous smaller manufacturers, such as Guangzhou Luen Cheong and Wenzhou Accurate Machinery.
2. **Fully Automatic Bag Filling System**:
– **Price**: Â¥8,000 – Â¥20,000 RMB (Approximately $1,200 – $3,000)
– **Features**: Complete automation, higher production capacity, integrated weighing and sealing systems.
– **Manufacturers**: Established manufacturers like Yantai Pri-Safety Equipment and Zhengzhou Vtops Machinery Co., Ltd.
3. **Industrial Grade Automatic Bag Filling Machine**:
– **Price**: Â¥30,000 – Â¥60,000 RMB (Approximately $4,500 – $9,000)
– **Features**: High-end features, larger throughput, advanced automation suited for large-scale operations.
– **Manufacturers**: Key industry players such as Anhui Zengran Packaging Technology and Tinsley Equipment Company.
### Summary
Shipping Cost for bag filling system import from China
Sure, calculating the shipping cost for importing a bag filling system from China involves several factors, including the weight and volume of the system, shipping method, and destination. Here’s a concise guide:
1. **Weight and Volume**: Determine the weight and dimensions (length, width, height) of the bag filling system. Most freight companies charge by volume weight for large but light items.
2. **Shipping Method**:
– **Air Freight**: Faster but more expensive. Suitable for lighter or urgent shipments.
– **Sea Freight**: More economical for heavy or bulky equipment, but slower.
3. **Freight Charges**:
– **Air Freight**: Costs typically range from $4 to $8 per kg. For instance, a 500 kg system might cost $2000 to $4000.
– **Sea Freight**: Typically calculated in cubic meters (CBM). Prices vary widely, but a common range might be $100 to $200 per CBM. An industrial machine might take up 1-2 CBM, so you may be looking at $100 to $400 in base shipping costs.
4. **Additional Costs**:
– **Customs Duties**: Vary by country and product category. Check your local customs office for precise rates.
– **Insurance**: Optional but recommended. Usually around 0.3% to 0.5% of the shipment value.
– **Handling Fees**: Includes packaging, loading, unloading, and possibly warehousing fees.
5. **Destination Charges**: Port handling, delivery to your site, and any local transportation.
**Example Calculation** (Sea Freight):
– System Volume: 2 CBM
– Sea Freight Cost: $150 per CBM
– Total: 2 CBM * $150 = $300
– Add Customs Duty (~5% of $10,000 value): ~$500
– Insurance (0.5% of $10,000): $50
– Miscellaneous Fees: ~$200
– Total Estimated Cost: $300 (freight) + $500 (duties) + $50 (insurance) + $200 (fees) = ~$1050
**Note**: Costs can fluctuate due to fuel surcharges, seasonal variations, and specific routes. Always get quotes from multiple freight forwarders for precise pricing.
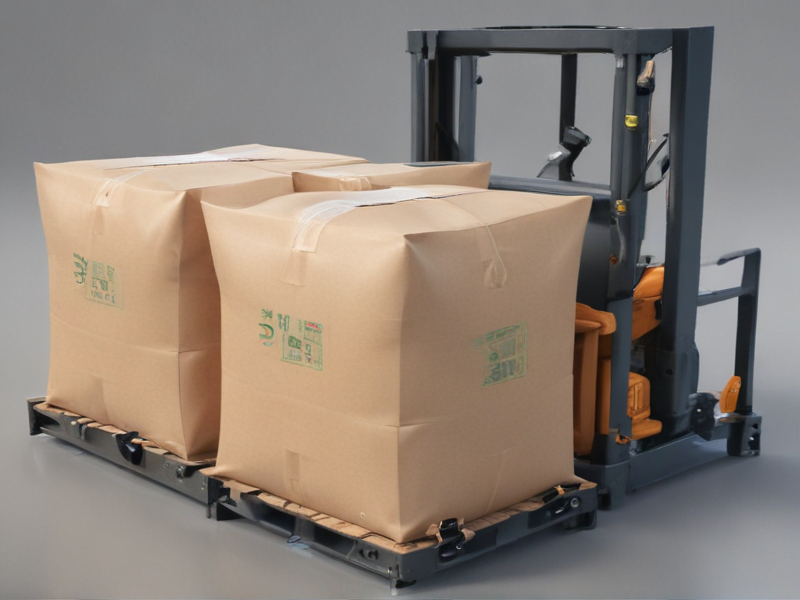
Compare China and Other bag filling system Markets: Products Quality and Price,Visible and Hidden Costs
When comparing China’s bag filling systems to those from other markets, several important factors should be considered: product quality, price, and both visible and hidden costs.
**Product Quality:**
China’s manufacturing sector has seen tremendous improvements in quality due to advanced technologies and stringent quality control processes. While previously criticized for lower quality, many Chinese manufacturers now approach the standards of Western and Japanese producers. European and American markets are generally credited with higher reliability and durability, often incorporating advanced features and excellent customer support.
**Price:**
China’s bag filling systems are often more affordable due to lower labor and production costs, appealing to budget-conscious buyers. Competitive pricing stems from economies of scale and a well-established manufacturing ecosystem. Other markets, particularly in Western countries and Japan, tend to offer systems at higher prices, justified by superior materials, more sophisticated technologies, and better after-sales service.
**Visible Costs:**
Visible costs include the initial purchase price, shipping fees, and basic installation charges. Chinese products, while cheaper upfront, might incur higher shipping and installation costs due to geographical distance. Western and Japanese systems, although more costly to purchase, often bundle additional services like free installation and training, mitigating some of these expenses.
**Hidden Costs:**
Hidden costs can be a significant factor. Chinese products may lead to higher long-term maintenance costs due to potentially lower durability and the need for frequent part replacements. Additionally, warranty services could be less comprehensive, leading to out-of-pocket repair expenses. In contrast, Western and Japanese products generally have more extensive warranties and lower maintenance needs. Furthermore, downtime associated with repairs can be costly, and Western products often ensure reduced downtime due to quicker service turnaround and availability of parts.
In conclusion, Chinese bag filling systems are attractively priced and have improved significantly in quality. However, careful consideration must be given to the potential for higher hidden costs. Western and Japanese systems, though more expensive, may offer better long-term reliability and lower hidden expenditures.
Custom Private Labeling and Branding Opportunities with Chinese bag filling system Manufacturers
Engaging with Chinese manufacturers for custom private labeling and branding presents a unique opportunity to differentiate your product in the competitive market of bag filling systems. China’s advanced manufacturing infrastructure, coupled with cost-effective production, makes it an appealing destination for sourcing high-quality equipment tailored to your brand’s specific needs.
1. **Customization Flexibility**: Chinese manufacturers often provide extensive customization options. Whether you need specific design alterations, color variations, or unique branding elements, these manufacturers can accommodate your specifications. This flexibility ensures that the bag filling systems align perfectly with your brand image and business requirements.
2. **Cost Efficiency**: One of the primary advantages of partnering with Chinese manufacturers is the cost benefits. Competitive pricing for both manufacturing and labor can significantly reduce overall expenditure. This allows businesses to invest more in other critical areas such as marketing, distribution, and customer service.
3. **Technological Advancements**: Chinese manufacturers are at the forefront of integrating advanced technologies in their bag filling systems. They offer state-of-the-art features such as automated controls, precision filling, and enhanced safety mechanisms. These technological enhancements can provide a significant edge in terms of efficiency and reliability.
4. **Scalability**: As your business grows, the ability to scale up production effortlessly becomes crucial. Chinese manufacturers are equipped to handle both small and large production volumes, ensuring that you can meet increasing demand without compromising on quality.
5. **Quality Standards**: Reputable Chinese manufacturers adhere to stringent quality control measures and international standards. By choosing the right partner, you can assure your customers of the high quality and durability of your products.
For successful collaboration, conduct thorough due diligence, seek references, and possibly visit factories to ensure they meet your quality and ethical standards. Establishing clear communication channels and setting detailed agreements on product specifications and delivery timelines will further facilitate a smooth partnership.
In summary, leveraging the capabilities of Chinese manufacturers for custom private labeling and branding in bag filling systems can lead to substantial cost savings, enhanced product customization, and improved market positioning.
Tips for Procurement and Considerations when Purchasing bag filling system
**Tips for Procurement and Considerations when Purchasing a Bag Filling System**
1. **Assess Your Needs**: Understand your production requirements, such as bag size, filling speed, and the nature of the materials to be packed. This helps identify the type of bag filling system that best suits your operation.
2. **Type of System**: Choose between various systems like gravity-fed, volumetric, and auger fillers based on the material consistency and required accuracy. For example, gravity-fed systems work well for free-flowing materials, while auger fillers suit powders.
3. **Automation Level**: Determine the level of automation you need. Semi-automatic systems offer greater flexibility and lower costs, whereas fully automated systems provide higher efficiency and consistency but come with a higher upfront investment.
4. **Materials and Durability**: Ensure the system is constructed from durable, high-quality materials like stainless steel, especially if dealing with corrosive or abrasive substances. This ensures longevity and reduced maintenance costs.
5. **Accuracy and Precision**: Evaluate the system’s accuracy in terms of weight or volume to minimize waste and ensure consistency in product output.
6. **Flexibility and Scalability**: Opt for systems that can easily adapt to changes in production demands and can be scaled up as your business grows.
7. **Ease of Use and Maintenance**: Select a system with straightforward controls and easy access for maintenance. This minimizes downtime and simplifies training requirements.
8. **Supplier Reputation**: Research the supplier’s credibility, looking for reviews, case studies, and references. A reliable supplier offers better service, support, and often a more dependable product.
9. **Compliance and Certifications**: Ensure the bag filling system complies with industry standards and certifications for quality, safety, and sanitation, especially for food, pharmaceuticals, or hazardous materials.
10. **Cost Considerations**: While the initial cost is important, also factor in long-term costs such as parts, maintenance, and operational efficiency. A higher upfront cost might be justified by lower operational expenses over time.
By thoroughly evaluating these factors, you can make an informed decision that aligns with your operational needs and budget constraints.
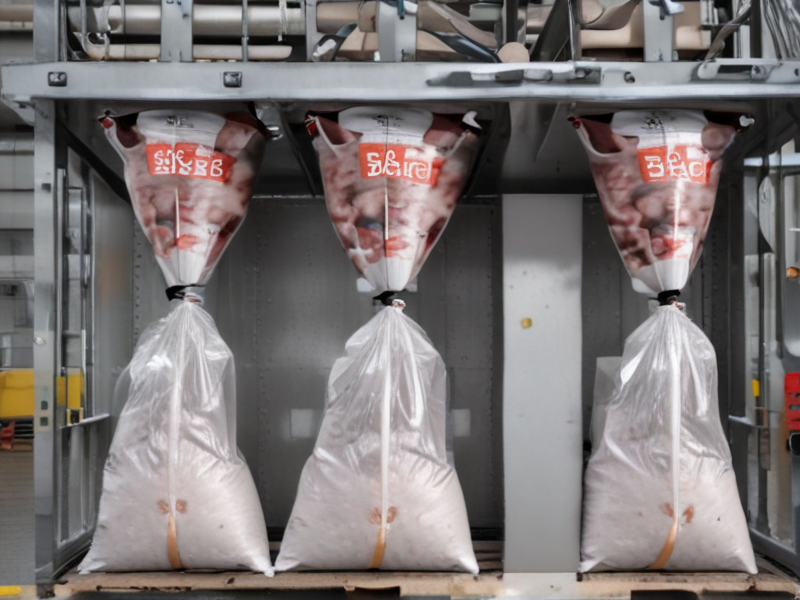
FAQs on Sourcing and Manufacturing bag filling system in China
### FAQs on Sourcing and Manufacturing Bag Filling Systems in China
**1. Why should I consider sourcing bag filling systems in China?**
China offers competitive pricing, robust manufacturing capabilities, and a plethora of suppliers with extensive experience in the bag filling systems industry. The country’s strong supply chain infrastructure can also help in reducing lead times.
**2. How do I find reputable manufacturers in China?**
Start with online directories like Alibaba, Made-in-China, and Global Sources. Additionally, attending trade shows like the Canton Fair can provide direct access to numerous manufacturers. Utilizing third-party verification services can also ensure the credibility of suppliers.
**3. What factors should I consider when choosing a manufacturer?**
Evaluate the manufacturer’s experience, production capacity, quality control processes, certification (like ISO), customer reviews, and after-sales service. Factory visits or audits can also provide firsthand insight into the manufacturer’s operations.
**4. How do I ensure quality control?**
Implement a comprehensive quality control strategy that includes defining clear specifications, setting up pre-production samples, regular inspections (pre-production, in-line, and final inspections), and third-party quality audits.
**5. What are the common payment terms for manufacturing contracts in China?**
Often, manufacturers require a deposit (usually 30% of the total cost) before production begins, with the remaining balance paid upon completion or shipment. Letters of Credit and escrow services are also options for large orders to ensure payment security.
**6. What are the lead times for production?**
Lead times typically range from 30 to 60 days, depending on the complexity of the system and order volume. Initial sampling and prototyping may require additional time.
**7. How do I handle shipping and logistics?**
Collaborate with reliable freight forwarders to manage shipping and customs clearance. Ensure all shipping terms (Incoterms) are clearly defined in the contract to avoid misunderstandings.
**8. Are there any legal considerations when manufacturing in China?**
Yes, intellectual property protection is crucial. Register your patents and trademarks in China. Make sure contracts are clear, comprehensive, and preferably bilingual (Chinese and your native language).
**9. Can I get after-sales support?**
Most reputable manufacturers offer after-sales support, including technical assistance, spare parts supply, and maintenance services. Ensure this is included in your contract.
By considering these FAQs, you can navigate the complexities of sourcing and manufacturing bag filling systems in China more effectively.