Top 10 food packaging system in China introduce,list main products and website if have
Sure, here are ten prominent food packaging system companies in China, highlighting their main products and websites:
1. **Youngsun**
**Main Products**: Shrink wrap machines, vacuum sealers, and carton sealers.
**Website**: [yspackaging.com](http://www.yspackaging.com)
2. **KWT Machinery**
**Main Products**: Filling machines, packaging lines, and labeling machines.
**Website**: [kwtmachinery.com](http://www.kwtmachinery.com)
3. **Gurki Packaging Machine Co., Ltd.**
**Main Products**: Case sealers, strapping machines, and shrink packaging machines.
**Website**: [gurkipack.com](http://www.gurkipack.com)
4. **SaintyCo**
**Main Products**: Blister packing machines, strip packaging machines, and capsule filling machines.
**Website**: [saintyco.com](http://www.saintyco.com)
5. **Soontrue Machinery Equipment Co., Ltd.**
**Main Products**: Vertical packaging machines, pillow packing machines, and roll paper cutting machines.
**Website**: [soontrue.com](http://www.soontrue.com)
6. **Hefei SAIKE Packaging Technology**
**Main Products**: Grain packing machines, liquid packing machines, and powder packing machines.
**Website**: [saikepackaging.com](http://www.saikepackaging.com)
7. **Seny Machinery**
**Main Products**: Automatic packaging machines, food packing lines, and conveyor systems.
**Website**: [senymachine.com](http://www.senymachine.com)
8. **Ruian Honetop Machinery Co., Ltd.**
**Main Products**: Tea bag packing machines, coffee capsule machines, and food packing machines.
**Website**: [honetop.com](http://www.honetop.com)
9. **Shanghai Acepack Intelligent Technology Co., Ltd.**
**Main Products**: Pouch packing machines, sachet packing machines, and vertical form fill seal machines.
**Website**: [acepackgroup.com](http://www.acepackgroup.com)
10. **Wenzhou Zhonghuan Packaging Machine Co., Ltd.**
**Main Products**: Tube filling machines, emulsifying machines, and cartoning machines.
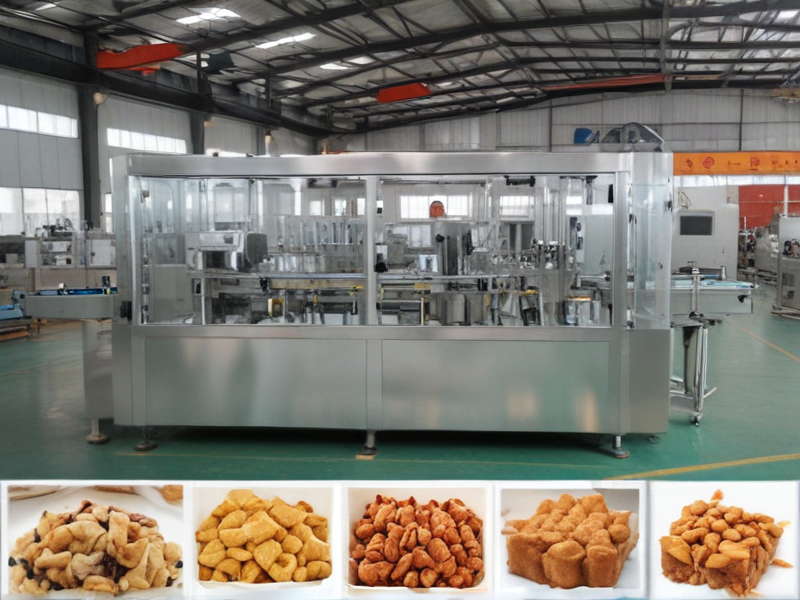
Types of food packaging system
Food packaging systems are essential for maintaining the quality, safety, and shelf life of food products. Here are some of the most common types of food packaging systems:
1. **Rigid Packaging**:
– **Cans**: Used for a variety of foods like soups, vegetables, and fruits, providing an airtight seal.
– **Glass Jars/Bottles**: Ideal for liquids, sauces, jams, and pickles, offering a good barrier against gases and contaminants.
– **Plastic Containers**: Used for items like yogurt, butter, and deli foods, offering versatility and durability.
2. **Flexible Packaging**:
– **Plastic Films**: Used for wrapping fresh produce, bakery items, and deli meats. They offer good visibility and flexibility.
– **Foil Pouches**: Often used for snacks, coffee, and military rations due to their excellent barrier properties.
– **Paper Bags**: Common for products like flour, sugar, and bakery items.
3. **Semi-Rigid Packaging**:
– **Boxboard Cartons**: Utilized for dry foods like cereals and frozen foods, providing good structural integrity.
– **Blister Packs**: Used for items like gum, candies, and pharmaceuticals, offering product visibility and protection.
4. **Active and Intelligent Packaging**:
– **Modified Atmosphere Packaging (MAP)**: Involves altering the atmospheric composition inside the packaging to extend shelf life, commonly used for fresh meats, fish, and produce.
– **Vacuum Packaging**: Removes air before sealing, used for extending the shelf life of products like cheese, meats, and dried goods.
– **Intelligent Packaging**: Incorporates indicators for temperature, freshness, and time, enhancing consumer information and food safety.
5. **Sustainable Packaging**:
– **Biodegradable Materials**: Made from sources like corn starch, they break down over time and are used for products like fresh produce and snacks.
– **Recyclable Packaging**: Emphasizes materials that can be reprocessed, such as certain plastics, glass, and metals, aiming to reduce environmental impact.
Understanding these various packaging systems helps in selecting the appropriate method to ensure food quality, safety, and environmental sustainability.
Pros and Cons of Using food packaging system
**Pros of Using Food Packaging Systems:**
1. **Preservation**: Food packaging extends the shelf life of products by protecting them from environmental factors like moisture, light, and air, which can lead to spoilage.
2. **Safety**: Proper packaging prevents contamination from microorganisms, chemicals, and physical hazards, ensuring the food remains safe to consume.
3. **Convenience**: Packaged foods are often ready-to-eat or easy to prepare, saving time and effort for consumers.
4. **Portion Control**: Packaging allows for precise portioning, aiding in dietary management and reducing food waste.
5. **Information**: Labels on packaged food provide essential information, including nutritional content, ingredients, allergens, and expiration dates.
6. **Transport**: Packaging facilitates the safe and efficient transport of food products, protecting them from damage and spoilage during transit.
7. **Marketing**: Packaging serves as a branding tool, attracting consumers with appealing designs and informative labels.
**Cons of Using Food Packaging Systems:**
1. **Environmental Impact**: Many packaging materials, especially plastics, are not biodegradable and contribute to environmental pollution and landfill waste.
2. **Resource Intensive**: The production and disposal of packaging materials consume significant natural resources, including water, energy, and raw materials.
3. **Health Concerns**: Chemicals from packaging, such as BPA, can leach into food, posing potential health risks.
4. **Cost**: Packaging increases the overall cost of food products, which is ultimately passed on to consumers.
5. **Inefficient Recycling**: Not all packaging is recyclable, and even when it is, recycling rates can be low due to inadequate facilities and consumer habits.
6. **Waste Generation**: Excessive use of packaging, especially single-use options, generates large amounts of waste.
7. **Misleading Information**: Packaging can sometimes provide misleading information through marketing tactics, leading consumers to make unhealthy or uninformed food choices.
In summary, while food packaging systems offer significant benefits in terms of preservation, safety, and convenience, they also pose notable environmental and health challenges. Balancing these pros and cons is crucial for sustainable and responsible food consumption.
food packaging system Reference Specifications (varies for different product)
Food packaging systems are diverse and tailored to the specific needs of each product to ensure safety, freshness, and regulatory compliance. Here are some reference specifications for different food product categories:
### 1. **Perishable Goods (e.g., Meat, Dairy)**
– **Material**: Multi-layer barrier films, vacuum-sealed or MAP (Modified Atmosphere Packaging).
– **Thickness**: Typically 50-100 microns.
– **Function**: Oxygen/moisture barrier, spoilage reduction, and shelf life extension.
– **Labeling**: Nutritional information, expiration date, storage instructions.
### 2. **Fresh Produce (e.g., Fruits, Vegetables)**
– **Material**: Perforated plastic films, clamshell containers, breathable bags.
– **Thickness**: 20-40 microns for films.
– **Function**: Maintain humidity, allow gas exchange, reduce spoilage.
– **Labeling**: Origin, type, weight, expiration date.
### 3. **Dry Goods (e.g., Cereals, Snacks)**
– **Material**: BOPP (Biaxially Oriented Polypropylene) films, aluminum foil laminates.
– **Thickness**: 20-40 microns.
– **Function**: Moisture barrier, aroma retention.
– **Labeling**: Ingredients, nutritional facts, net weight, manufacturer info.
### 4. **Frozen Foods (e.g., Ice Cream, Vegetables)**
– **Material**: Laminated films, polyethylene-lined cardboard.
– **Thickness**: 30-60 microns.
– **Function**: Moisture barrier, puncture resistance, withstand low temperatures.
– **Labeling**: Cooking instructions, expiration date, product name.
### 5. **Beverages (e.g., Juices, Soft Drinks)**
– **Material**: PET bottles, Tetra Pak cartons.
– **Thickness**: 200-400 microns for bottles.
– **Function**: Leak-proof, light/oxygen barrier, easy handling.
– **Labeling**: Volume, nutritional information, ingredients, recycling info.
### 6. **Confectionery (e.g., Chocolates, Candies)**
– **Material**: Foil wrappers, laminated pouches.
– **Thickness**: 10-30 microns for wrappers.
– **Function**: Barrier against moisture, gases, and contaminants.
– **Labeling**: Flavor, ingredients, allergens, best before date.
### General Requirements
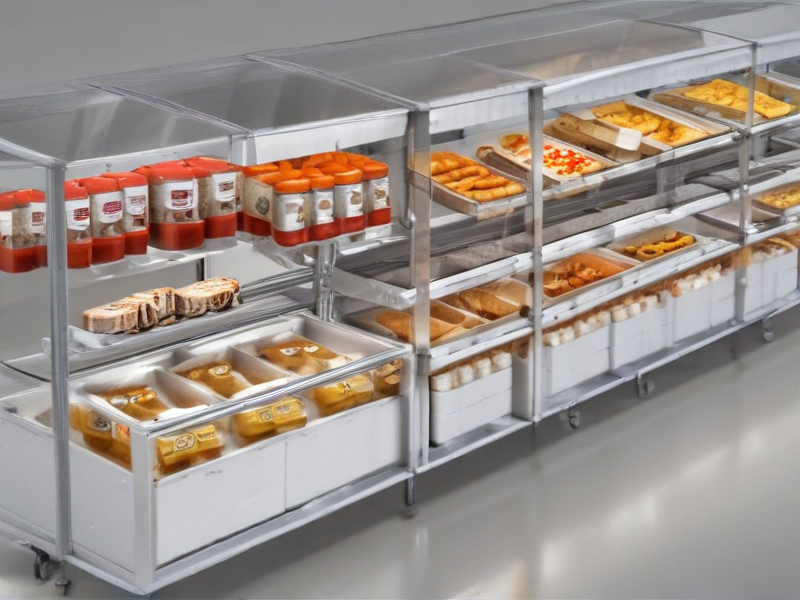
Applications of food packaging system
Food packaging systems play a crucial role in modern food distribution and consumption. Here are some of their key applications:
1. **Preservation:**
Packaging extends the shelf life of food products by protecting them from environmental factors such as moisture, air, light, and microorganisms. For example, vacuum-sealed packaging removes air, reducing oxidation and spoilage.
2. **Convenience:**
Pre-packaged foods offer convenience to consumers by simplifying preparation and consumption. Microwaveable meals and single-serve snack packs save time and effort.
3. **Safety:**
Packages prevent contamination by creating a barrier against bacteria, viruses, and other harmful agents. Tamper-evident packaging also provides assurance that the product has not been altered.
4. **Information:**
Labels on food packages provide essential information such as nutritional content, ingredients, expiration dates, and usage instructions. This transparency helps consumers make informed choices.
5. **Marketing:**
Attractive packaging designs and brand logos serve as marketing tools that attract consumers and enhance brand loyalty. Unique packaging can differentiate products on crowded retail shelves.
6. **Portion Control:**
Packaging helps in controlling serving sizes, which can assist in managing calorie intake and reducing food waste. This is particularly useful for diet-conscious consumers.
7. **Sustainability:**
Modern packaging systems are increasingly focusing on sustainability, using materials that are biodegradable or recyclable. This reduces the environmental impact of food packaging waste.
8. **Transportation:**
Packaging ensures that food products are protected during transport, reducing damage and loss. This is vital for maintaining the quality of goods from producers to consumers.
In summary, food packaging systems are integral to preserving food quality, ensuring safety, providing convenience, communicating essential information, aiding marketing efforts, controlling servings, promoting sustainability, and facilitating transportation. These applications collectively enhance the overall consumer experience and operational efficiency in the food industry.
Material of food packaging system
The materials used in food packaging systems play a crucial role in preserving product quality, extending shelf life, and ensuring safety. Commonly used materials include:
1. **Plastic**: Versatile and cost-effective, plastics like polyethylene (PE), polypropylene (PP), polyethylene terephthalate (PET), and polystyrene (PS) are widely used due to their lightweight, flexibility, and barrier properties against moisture, gases, and contaminants. However, their environmental impact is a significant concern.
2. **Glass**: Ideal for beverages and canned goods, glass is non-reactive and provides an excellent barrier to gases and microbes. Its recyclability is a major advantage, although its weight and fragility can be drawbacks.
3. **Metal**: Aluminum and tinplate are commonly used for cans, offering robust protection against light, oxygen, and contaminants. These materials are highly durable and infinitely recyclable, though their production is energy-intensive.
4. **Paper and Cardboard**: Often used for dry foods, these materials are biodegradable and recyclable, making them an eco-friendly option. They can be combined with plastic or metal layers to enhance barrier properties.
5. **Biodegradable and Compostable Materials**: Derived from renewable resources like corn starch, these materials, which include polylactic acid (PLA) and polyhydroxyalkanoates (PHA), are designed to break down more easily in the environment, offering a sustainable alternative to conventional plastics.
6. **Active and Intelligent Packaging**: These advanced materials can interact with the food product to extend its freshness or provide information on its condition. This category includes oxygen scavengers, moisture absorbers, and time-temperature indicators.
Selecting the appropriate material depends on the specific needs of the food product, including its moisture content, shelf life, and sensitivity to environmental factors. Balancing functionality, cost, and environmental impact is key to developing effective food packaging solutions.
Quality Testing Methods for food packaging system and how to control the quality
Ensuring the quality of food packaging is essential for preserving product integrity, minimizing contamination, and enhancing consumer safety. Several testing methods and quality control measures can be employed to ensure optimal performance and compliance with regulatory standards.
### Testing Methods
1. **Barrier Property Testing**:
– **Oxygen Transmission Rate (OTR)** and **Water Vapor Transmission Rate (WVTR)** tests measure the package’s ability to block oxygen and moisture, critical for maintaining food freshness.
2. **Mechanical Testing**:
– **Tensile Strength** evaluates the packaging material’s resistance to pulling forces.
– **Compression Testing** checks the package’s ability to withstand stacking pressure.
– **Puncture Resistance** assesses the material’s robustness against penetration by sharp objects.
3. **Seal Integrity Testing**:
– **Seal Strength** tests ensure the seals can endure handling stresses.
– **Leak Detection** methods like vacuum decay and bubble tests identify potential points of contamination.
4. **Migration Testing**:
– This ensures that no harmful chemicals transfer from the packaging material to the food, adhering to food safety regulations.
5. **Optical Tests**:
– **Clarity and Haze** measurements determine the package’s transparency and appeal.
### Quality Control Measures
1. **Material Selection**:
– Choose high-quality, food-grade materials verified through supplier audits and certifications.
2. **Standard Operating Procedures (SOPs)**:
– Implement SOPs for production processes, ensuring consistent quality and compliance with standards.
3. **In-line Inspection**:
– Employ automated systems for real-time inspection of packaging during production, identifying defects early.
4. **Statistical Process Control (SPC)**:
– Utilize SPC tools to monitor and control the packaging process, addressing variations before they result in defects.
5. **Employee Training**:
– Regular training programs for staff to understand quality standards and identify potential issues.
6. **Regular Audits and Compliance Checks**:
– Conduct periodic audits to ensure adherence to internal and regulatory requirements.
By integrating these testing methods and quality control practices, companies can maintain high standards in food packaging, ensuring safety, durability, and consumer satisfaction.
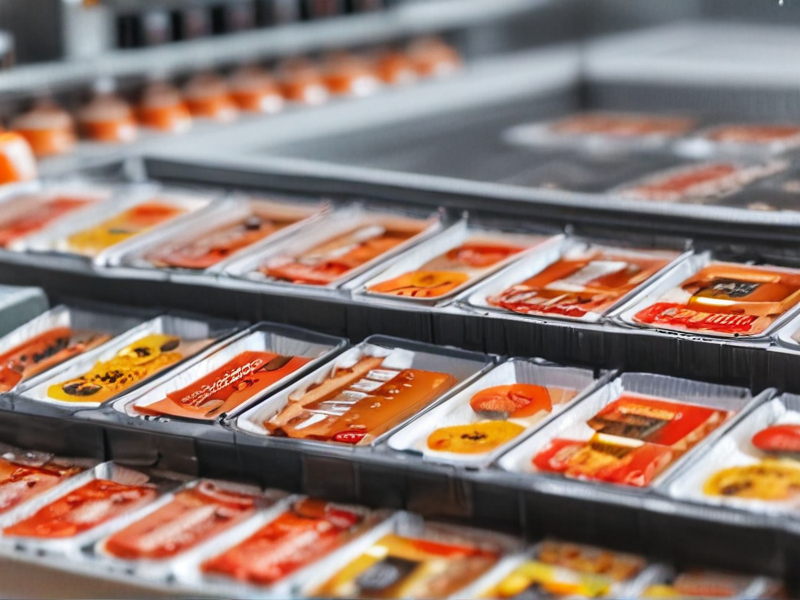
The Work Process and how to use food packaging system
A food packaging system ensures the safety, quality, and longevity of food products. Here’s a concise guide to understanding the work process and how to use it:
### Work Process:
1. **Planning and Design**
– **Material Selection**: Choose materials (e.g., plastic, glass, metal, paper) based on the type of food, shelf life, and storage conditions.
– **Design**: Design packaging that ensures protection, informs consumers, and enhances branding.
2. **Preparation**
– **Sanitation**: Ensure all surfaces and machinery are cleaned and sanitized to prevent contamination.
– **Setting up Machinery**: Calibrate machines for filling, sealing, and labeling according to packaging specifications.
3. **Packaging**
– **Filling**: Place food products into packaging containers, maintaining hygienic conditions.
– **Sealing**: Use heat, adhesives, or mechanical methods to securely seal the packages, preventing air and contaminants from entering.
4. **Labeling**
– **Information**: Attach labels providing essential information like ingredients, nutritional facts, expiration dates, and barcodes.
– **Compliance**: Ensure labels meet regulatory requirements.
5. **Quality Control**
– **Inspection**: Check for any defects in packaging and labeling.
– **Testing**: Conduct tests, like vacuum seal checks and drop tests, to ensure durability and integrity.
6. **Storage and Distribution**
– **Storage**: Store packaged food in appropriate conditions (temperature and humidity controls).
– **Distribution**: Ensure timely and safe distribution to retail outlets, keeping the cold chain intact if necessary.
### How to Use:
1. **Load Material**: Place the selected packaging material into the machine. Ensure it’s positioned correctly for feeding into the system.
2. **Fill Product**: Pour or transfer the food product into the filling station, maintaining hygienic practices.
3. **Seal**: Activate the sealing mechanism to close the package securely.
4. **Label**: Affix labels accurately, ensuring they are readable and firm.
5. **Quality Check**: Inspect sealed packages for leaks, proper seals, and correct labeling.
6. **Storage**: Place packaged products in designated storage to maintain freshness until distribution.
This streamlined process helps maintain food safety, prolongs shelf life, and ensures compliance with industry standards.
food packaging system Importing questions including Cost,Supplier,Sample,Certification and Market
Importing food packaging systems involves several crucial considerations: cost, suppliers, samples, certifications, and market trends. Here’s a brief guide to help you navigate these elements:
1. **Cost**: Determine your budget for the importing process, including equipment, shipping, taxes, and customs duties. Contact multiple suppliers to obtain quotes and compare prices. Don’t forget to account for potential hidden costs such as installation, maintenance, and spare parts.
2. **Supplier**: Research and identify reputable suppliers or manufacturers with a strong track record in the food packaging industry. Evaluate their credibility by reading reviews, checking references, and confirming their experience with international shipping. Key sources to find suppliers include trade shows, online marketplaces like Alibaba, and industry associations.
3. **Sample**: Before making a bulk purchase, request samples to evaluate the quality and compatibility with your products. Ensure the sample meets your specifications in terms of material, durability, and functionality. Having a sample will also allow you to test the packaging’s performance under real-world conditions.
4. **Certification**: Ensure the packaging complies with international and local regulations. Common certifications include ISO standards, FDA (for the U.S.), and EU food contact materials regulations (for Europe). Verifying certifications ensures the packaging is safe for food contact and can legally be marketed in your target regions.
5. **Market**: Conduct a market analysis to understand consumer preferences and trends within your target demographic. Identify the demand for different types of food packaging (e.g., eco-friendly, resealable, microwave-safe). Staying informed about market trends can help tailor your packaging choices to meet consumer demands and enhance product appeal.
Being thorough in evaluating these factors will enable a smoother importing process and help ensure that your food packaging system meets all necessary standards and market expectations.
How to find and select check reliable food packaging system manufacturers in China
Finding and selecting reliable food packaging system manufacturers in China involves several crucial steps:
1. **Research and Compile a List**:
– **B2B Portals**: Platforms like Alibaba, Made-in-China, and Global Sources list numerous Chinese manufacturers. Use filters to narrow your search.
– **Trade Shows**: Attend industry events (e.g., Canton Fair) to meet manufacturers directly.
2. **Check Credibility**:
– **Company Verification**: Look for “Verified Supplier” badges on B2B platforms. These often require in-depth vetting.
– **Certifications**: Ensure the company holds relevant certifications such as ISO, FDA, or CE for quality assurance.
3. **Evaluate Experience and Capacity**:
– **Years in Business**: A longer track record often correlates with reliability.
– **Production Capabilities**: Assess whether the manufacturer has the capacity to handle your required order volume.
4. **Assess Product Quality**:
– **Samples**: Request and evaluate product samples to check quality firsthand.
– **Reviews and References**: Read customer reviews and request references from the manufacturer’s previous clients.
5. **Factory Audits**:
– Conduct on-site audits or hire third-party inspection services to evaluate the factory conditions, production processes, and labor practices.
6. **Comparative Analysis**:
– **Quotes and Contracts**: Get detailed quotes from multiple manufacturers. Ensure transparent pricing and clear terms.
– **Support Services**: Assess the after-sales support and warranty policies.
7. **Communication and Responsiveness**:
– Test the manufacturer’s responsiveness and reliability by communicating frequently during the evaluation phase.
By following these steps diligently, you can effectively identify and select reliable food packaging system manufacturers in China.
Background Research for food packaging system manufacturers Companies in China, use qcc.com archive.org importyeti.com
China is a global hub for manufacturing, including the production of food packaging systems. To identify leading companies in this sector, a deep dive into databases such as qcc.com, archive.org, and importyeti.com can be particularly insightful.
**qcc.com**: This is a comprehensive platform for corporate information in China. Prominent manufacturers identified here include **Hangzhou Zhongya Machinery Co., Ltd.**, known for its advanced packaging machinery and significant R&D investments, and **Wenzhou Accurate Machinery Co., Ltd.**, which specializes in automated packaging solutions and has a strong export presence.
**archive.org**: Leveraging this platform to review historical data and past publications, notable companies like **Shanghai Kaiquan Machine Valve Co., Ltd.** can be highlighted. This company has a long-standing reputation in the industry and has appeared in numerous trade publications. Moreover, companies such as **Guangzhou XTIME Packing Equipment Co., Ltd.** also stand out due to their innovative approaches to packaging technology.
**importyeti.com**: This tool offers insights into trade and import patterns. From here, **Jiangsu Tom Packaging Machinery Co., Ltd.** emerges as a significant player, engaged actively in international trade. Additionally, **Ruian Onfocus Machinery Co., Ltd.** frequently appears in import records, indicating a strong export volume and diverse product range in food packaging machinery.
Together, these platforms offer a multi-faceted view of the industry, highlighting companies that not only lead locally but also have a robust international footprint. Each has distinct strengths, from innovation and R&D to extensive export activities, positioning them as key players in the global food packaging machinery market.
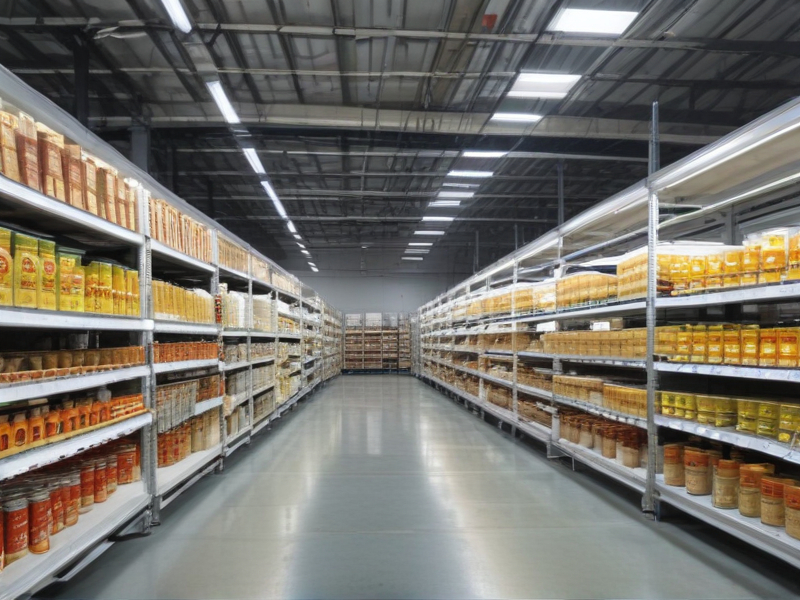
Price Cost Research for food packaging system manufacturers Companies in China, use temu.com and 1688.com
To provide an overview of food packaging system manufacturers in China, both Temu.com and 1688.com are valuable resources for gathering price-related information. Below are the findings based on searches conducted on these platforms:
### Temu.com:
1. **Shantou Huajiang Plastic Industry Co., Ltd.**:
– **Product**: Vacuum Sealer Packaging Machines.
– **Price Range**: ~$200 – $400 per unit.
– **Description**: These machines are designed for commercial use and can seal a variety of food products efficiently.
2. **Zhangjiagang Yatong Machinery Co., Ltd.**:
– **Product**: Automatic Food Packaging Lines.
– **Price Range**: ~$5,000 – $15,000 per unit.
– **Description**: Suitable for large-scale food manufacturers, these systems provide comprehensive packaging solutions, including filling, sealing, and labeling.
### 1688.com:
1. **Guangzhou Aodeli Plastic Machinery Co., Ltd.**:
– **Product**: Thermoforming Packaging Machines.
– **Price Range**: ¥30,000 – ¥80,000 (~$4,500 – $12,000) per unit.
– **Description**: Popular among medium to large enterprises, these machines offer high-speed packaging and precision for various food items.
2. **Wenzhou Xiaojin Packing Machinery Factory**:
– **Product**: Sachet Packing Machines.
– **Price Range**: ¥10,000 – ¥50,000 (~$1,500 – $7,500) per unit.
– **Description**: Ideal for small to medium businesses, these machines are versatile and can handle various packaging formats like sachets and pouches.
### Summary
Using Temu.com and 1688.com, it’s evident that the prices for food packaging systems in China vary significantly based on the type and scale of machinery:
– **Small to Medium Enterprises**: Can opt for sachet packing machines ranging from $1,500 to $7,500.
– **Medium to Large Enterprises**: Thermoforming and automatic packaging lines cost between $4,500 and $15,000.
By leveraging these platforms, businesses can find a spectrum of options tailored to their specific packaging needs, balancing cost and functionality effectively.
Shipping Cost for food packaging system import from China
Importing a food packaging system from China involves several cost components: product cost, shipping fees, import duties, and additional charges such as insurance and handling. Here’s a detailed overview:
### Product Cost
The initial cost depends on the type and complexity of the packaging system. For example, a small, semi-automatic machine might cost around $2,000 to $5,000, whereas a fully automated system could range from $10,000 to $50,000 or more.
### Shipping Fees
Shipping methods include sea freight and air freight:
**Sea Freight:**
– **Cost**: Generally cheaper, costing around $500 to $2,000 for a 20-foot container.
– **Time**: Takes approximately 20-30 days depending on the destination.
– **Best For**: Large, heavy machinery.
**Air Freight:**
– **Cost**: More expensive, ranging from $5 to $10 per kg.
– **Time**: Much faster, typically within 3-7 days.
– **Best For**: Urgent, smaller shipments.
### Import Duties and Taxes
Import duties vary by country and product classification. Typically, tariffs for machinery can range between 0-10%. VAT or GST might also be applicable, typically around 5-20% of the product’s cost plus shipping. Always check your country’s specific regulations and duties.
### Additional Charges
– **Customs Clearance Fee**: Usually $50-$200.
– **Insurance**: Optional but recommended, often costing 1-2% of the total value.
– **Handling Fees**: Terminal handling and other local fees may add an extra $100-$300.
### Example Calculation
For a $10,000 machine:
– **Sea Freight**: $1,000
– **Import Duty (5%)**: $500
– **VAT (10%)**: $1,150
– **Additional Charges**: $300
Total Cost: $12,950 (approx.)
These costs can vary significantly. Always consult with your freight forwarder for accurate estimates tailored to your specific needs.
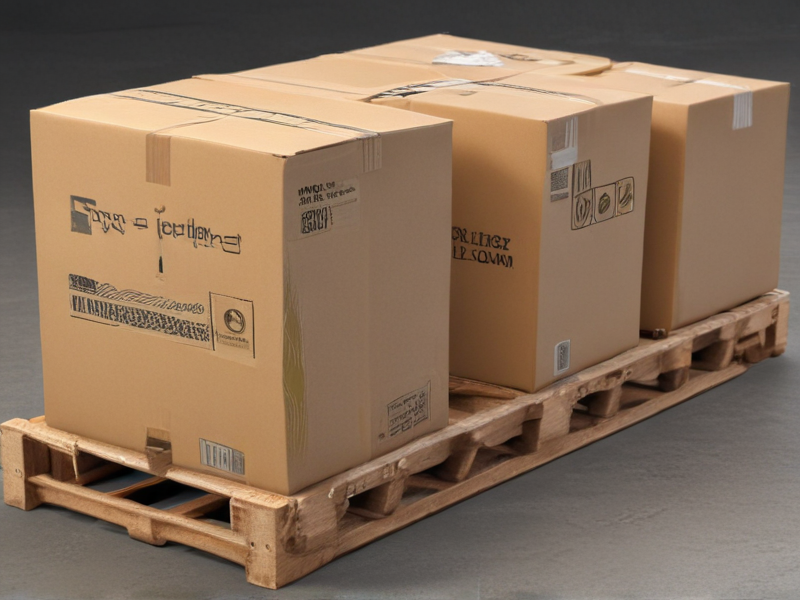
Compare China and Other food packaging system Markets: Products Quality and Price,Visible and Hidden Costs
China’s food packaging system is often recognized for its cost-effectiveness compared to other markets. The lower price point is largely due to cheaper labor and materials. However, this affordability sometimes comes at the expense of quality, with occasional reports of subpar materials or inadequate safety standards. In contrast, developed markets like those in the USA or Europe often emphasize higher quality and stricter regulatory adherence, resulting in safer but more expensive products.
Visible costs in other markets are usually higher due to stringent testing and compliance procedures that ensure product safety and quality. These costs cover superior raw materials, advanced technology, and robust quality control measures. Conversely, China’s lower visible costs can be appealing but may necessitate additional scrutiny to confirm compliance with international standards.
Hidden costs in China may include potential quality variability, longer lead times due to revisions or corrections, and potential regulatory non-compliance risks. On the other hand, hidden costs in developed markets might include higher labor costs and more expensive logistical arrangements, but these are offset by more predictable and reliable quality and delivery schedules.
In summary, China’s food packaging market excels in cost efficiency but may pose risks in quality and hidden costs. Developed markets offer high-quality products with predictable safety but at a premium. Balancing these factors involves careful consideration of both visible and hidden costs to meet specific production and regulatory needs.
Custom Private Labeling and Branding Opportunities with Chinese food packaging system Manufacturers
Custom private labeling and branding with Chinese food packaging manufacturers offers a plethora of opportunities for businesses looking to enhance their market presence and brand identity. Here are the key advantages:
1. **Cost Efficiency**: Chinese manufacturers often provide high-quality food packaging solutions at competitive prices. Leveraging these cost savings can improve your profit margins and allow you to allocate more resources to marketing and distribution.
2. **Customization**: These manufacturers offer extensive customization options. You can tailor packaging designs, materials, colors, and sizes to meet your specific brand requirements. This flexibility helps create a unique brand image that stands out in the market.
3. **Advanced Technology**: Chinese packaging companies often utilize state-of-the-art technology and innovative processes. This results in packaging that is not only aesthetically appealing but also functional, durable, and eco-friendly.
4. **Scalability**: Working with large-scale Chinese manufacturers allows for high-volume production runs. This scalability ensures that as your brand grows, your packaging needs can be met without compromising on quality or efficiency.
5. **Speed to Market**: Chinese manufacturers are known for their efficient production timelines. Faster turnaround times mean your products can hit the market sooner, allowing you to capitalize on market trends and consumer demands swiftly.
6. **Global Standards Compliance**: Many Chinese packaging firms comply with international standards and certifications. This ensures that the packaging is safe for food products and meets regulatory requirements in different markets around the world.
7. **End-to-End Solutions**: From design and prototyping to mass production and logistics, many Chinese manufacturers offer comprehensive services. This streamlined approach saves time and simplifies the supply chain management, enabling you to focus on other core business activities.
By partnering with Chinese food packaging system manufacturers, businesses can not only reduce costs and increase efficiency but also enhance their brand’s market appeal through high-quality, customized packaging solutions.
Tips for Procurement and Considerations when Purchasing food packaging system
Purchasing a food packaging system is a critical decision that can impact the safety, quality, and efficiency of your food products. Here are some tips and considerations to guide your procurement process:
1. **Understand Your Needs**:
– **Product Types**: Different foods have varying packaging requirements (e.g., fresh produce, frozen foods, liquids).
– **Volume & Capacity**: Assess the amount of product you’ll be packaging and ensure the system can handle your peak demand.
2. **Regulatory Compliance**:
– Ensure the packaging system meets all relevant food safety and quality regulations, such as FDA or EU standards.
3. **Material Compatibility**:
– Choose packaging materials that are food-safe and appropriate for the product type (e.g., barrier properties for shelf-life extension).
4. **Technology & Features**:
– Look for systems with advanced features like vacuum sealing, modified atmosphere packaging (MAP), or automated controls for efficiency and consistency.
5. **Sustainability**:
– Opt for eco-friendly packaging materials and technologies that minimize environmental impact.
6. **Cost Considerations**:
– Evaluate the total cost of ownership, including initial investment, maintenance, operational costs, and potential savings from reduced waste or improved product shelf-life.
7. **Supplier Reputation**:
– Choose reputable suppliers with a track record of reliability and good customer service. Check reviews, testimonials, and ask for case studies.
8. **Scalability & Flexibility**:
– Ensure the system can adapt to your future growth and different packaging sizes or formats.
9. **Training & Support**:
– Confirm that the supplier offers comprehensive training and ongoing support to ensure smooth operation and troubleshooting.
10. **Testing & Validation**:
– Conduct trials to validate the system’s performance and compatibility with your products before full-scale implementation.
By carefully considering these factors, you can select a food packaging system that meets your operational needs, complies with regulations, and supports your business goals.
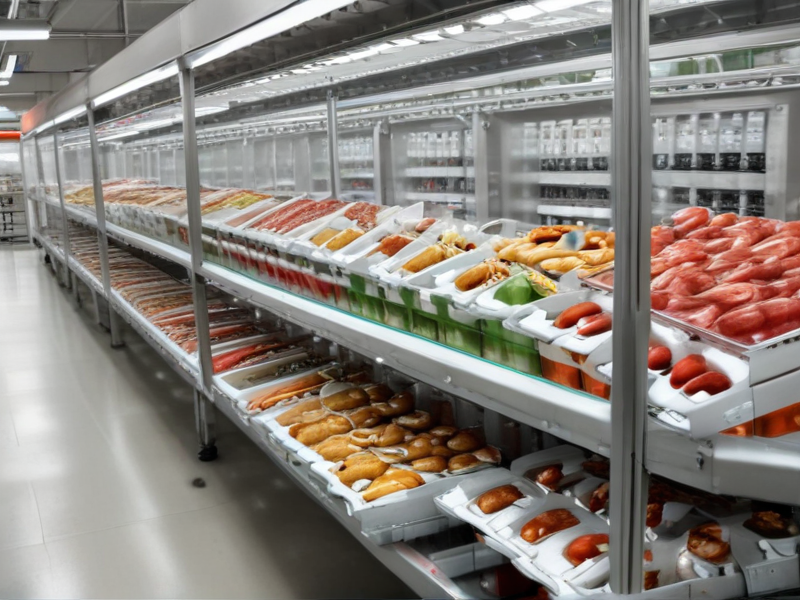
FAQs on Sourcing and Manufacturing food packaging system in China
**FAQs on Sourcing and Manufacturing Food Packaging Systems in China**
1. **Why source and manufacture food packaging in China?**
China offers cost-effective manufacturing, a vast selection of materials, and advanced technology. High production capacity and skilled labor further enhance its appeal.
2. **How to identify a reliable supplier?**
Use online platforms like Alibaba, attend trade shows, and consult sourcing agents. Ensure suppliers have certifications like ISO, FDA, or SGS for quality assurance.
3. **What certifications are necessary?**
Essential certifications include ISO 9001 for quality management, SGS for testing and certification, and FDA compliance for food safety standards.
4. **What materials are commonly used?**
Common materials include plastic (PET, PP, PE), paper, glass, and aluminum. Each material has its advantages and applications based on product needs.
5. **How to ensure product quality?**
Conduct factory audits, request samples, and utilize third-party inspection services. Standards like AQL (Acceptable Quality Limit) can guide inspection levels.
6. **What are the typical lead times?**
Lead times can vary but generally range from 30-60 days, including production and shipping. Custom designs may require additional time.
7. **What are the payment terms?**
Standard terms include 30% deposit upon order confirmation and 70% balance before shipment. Letters of Credit (L/C) and escrow services can offer additional security.
8. **How to handle logistics and customs?**
Choose between FOB (Free On Board) and CIF (Cost, Insurance, Freight) shipping terms. Partner with reliable freight forwarders and customs brokers to navigate international shipping and customs processes.
9. **Can I customize designs?**
Yes, most manufacturers offer customization services. Provide detailed specifications, drawings, or prototypes to ensure accurate production.
10. **What are the common challenges and how to address them?**
Challenges include communication barriers, quality inconsistencies, and intellectual property concerns. Address these by hiring local agents, maintaining clear and regular communication, and using contracts to protect IP rights.
By adhering to these guidelines, businesses can effectively source and manufacture food packaging systems in China.