Top 10 integrated packaging systems in China introduce,list main products and website if have
China is a global leader in integrated packaging systems, offering a wide array of solutions tailored to various industries. Here are the top 10 integrated packaging systems in China:
1. Sainty International Group (SaintyCo)
– Main Products: Pharmaceutical packaging machines, capsule filling machines, tablet presses, blister packing machines.
– Website: [SaintyCo](https://www.saintyco.com/)
2. Hangzhou Youngsun Intelligent Equipment Co., Ltd.
– Main Products: Automatic strapping machines, carton sealers, pallet wrappers, shrink machines.
– Website: [Youngsun](http://www.youngsunpack.com/)
3. Guangdong Soontrue Machinery Equipment Co., Ltd.
– Main Products: Vertical packaging machines, horizontal packaging machines, multi-lane packaging machines.
– Website: [Soontrue](http://www.soontrue.com/)
4. Shanghai Boevan Packaging Machinery Co., Ltd.
– Main Products: Horizontal flow wrap machines, vertical form-fill-seal machines, cartoning machines.
– Website: [Boevan](http://www.boevan.com/)
5. Ruian Honetop Machinery Co., Ltd.
– Main Products: Multi-lane sachet packing machines, tea bag packing machines, powder packing machines.
– Website: [Honetop](https://www.hontecmachinery.com/)
6. Jiangsu Tom Packaging Machinery Co., Ltd.
– Main Products: Pouch packaging machines, bottle filling machines, labeling machines.
– Website: [Tom Packaging](http://www.jstom.com/)
7. Chengdu Kehongda Technology Co., Ltd.
– Main Products: Rotary packing machines, liquid and paste filling machines.
– Website: [Kehongda](https://www.kehongda.en.alibaba.com/)
8. Wenzhou Changs Machinery Co., Ltd.
– Main Products: Vacuum packing machines, skin packing machines, automatic flow packing machines.
– Website: [Changs Machinery](https://www.changsmachinery.com/)
9. Shanghai Acepack Intelligent Technology Co., Ltd.
– Main Products: Premade pouch packing machines, liquid packing machines, granule packing machines.
– Website: [Acepack](http://www.acepackgroup.com/)
10. Hunan Grand Packing Machinery Co., Ltd.
– Main Products: Blister packing machines, strip packing machines, cartoning machines.
– Website: [Grand Packing](https://www.grand-packing.com/)
These companies provide comprehensive packaging solutions catering to various sectors such as pharmaceutical, food, and consumer goods, supported by their respective websites offering detailed information and contact options.
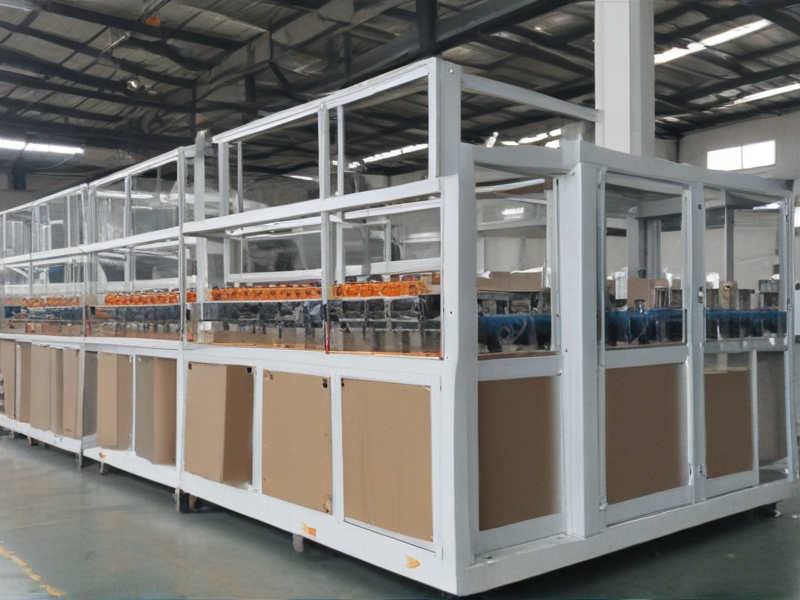
Types of integrated packaging systems
Integrated packaging systems consolidate various packaging processes into a seamless, automated workflow for efficiency, consistency, and cost-effectiveness. Here are key types:
1. Form-Fill-Seal Systems (FFS):
– Horizontal FFS (HFFS): Primarily for solid and semi-solid goods, these systems perform the entire packaging process horizontally. Examples include snack bars and frozen foods.
– Vertical FFS (VFFS): Ideal for granules, powders, and liquids, this system packages products in a vertical format, typically in bag or pouch forms.
2. Cartoning Systems:
– Horizontal Cartoning: Machines form, fill, and seal cartons horizontally. Common applications include pharmaceuticals, cosmetics, and food products.
– Vertical Cartoning: Suitable for heavy or bulky items, these systems feed the product from the top into pre-erected cartons.
3. Palletizing Systems:
– Robotic Palletizers: Utilize robotic arms for flexible, precise stacking of products on pallets, ideal for varied product lines.
– Conventional Palletizers: Use mechanical systems for high-speed, high-volume applications, often seen in beverage and bulk goods industries.
4. Blister Packaging Systems:
– Used extensively in pharmaceuticals and consumer goods, these systems form plastic blisters, fill them with products, and seal with a backing material, typically cardboard or aluminum foil.
5. Thermoforming Systems:
– Common in the food industry, these systems heat and mold plastic sheets into packaging trays, fill them with product, and seal with a film.
6. Shrink-Wrapping Systems:
– Utilize a heat process to shrink plastic film tightly around products. These systems are versatile, used in various sectors from multi-packs of bottled beverages to protective covers for consumer electronics.
7. Flexible Packaging Systems:
– These systems handle pouches, sachets, and other flexible materials, integrating filling, sealing, and printing processes. They are popular for single-serve food items and liquid packaging.
Each integrated packaging system focuses on different product attributes and industry needs, enhancing operational efficiency and product protection.
Pros and Cons of Using integrated packaging systems
Pros of Using Integrated Packaging Systems:
1. Efficiency and Speed: Integrated systems streamline packaging processes, reducing manual interventions and significantly speeding up production. This leads to higher throughput and more consistent output.
2. Cost Savings: Automation and integration can lower labor costs, reduce material wastage, and minimize the need for manual quality checks, translating to substantial cost savings over time.
3. Quality Control: Consistent, automated processes ensure uniformity in packaging, enhancing product quality and reducing the likelihood of defects.
4. Scalability: Integrated systems can be easily scaled up to meet increased demand without a proportional increase in costs or labor, facilitating business growth.
5. Data Collection and Analysis: Advanced integrated systems often come with data analytics capabilities, allowing for real-time monitoring, proactive maintenance, and data-driven decision making.
6. Space Utilization: By consolidating multiple packaging functions into a single system, integrated solutions can make more efficient use of floor space.
Cons of Using Integrated Packaging Systems:
1. High Initial Investment: The upfront costs for purchasing and installing integrated systems can be prohibitive, especially for small and medium-sized businesses.
2. Complexity: Integration of multiple packaging stages can add complexity to operations, requiring skilled personnel to manage and troubleshoot the system.
3. Downtime Risks: A breakdown in one part of an integrated system can halt the entire packaging line, potentially leading to significant downtime and production losses.
4. Maintenance Costs: Specialized, integrated systems may require frequent and sometimes costly maintenance to remain operational and efficient.
5. Rigidity: Integrated systems may lack the flexibility needed to adapt quickly to new packaging formats or varying product sizes, limiting their application in highly dynamic markets.
6. Technology Dependence: Heavy reliance on technology can be a drawback in regions with unstable power supplies or in the event of system malfunctions, making manual fallback plans necessary.
In summary, while integrated packaging systems offer notable advantages in efficiency and cost savings, they also come with significant challenges related to initial investment, complexity, and flexibility. Balancing these factors is crucial for businesses considering their adoption.
integrated packaging systems Reference Specifications (varies for different product)
Integrated packaging systems combine various packaging processes into a cohesive system to handle product packaging efficiently. These systems are customizable and can vary significantly based on the product specifications. Here are some reference specifications commonly considered for different products within an integrated packaging system:
### 1. Product Type and Dimensions:
– Size and Shape: The system must accommodate various product dimensions, whether they are small, large, irregularly shaped, or uniform.
– Weight: The machinery must handle the product weight without compromising speed or causing damage.
### 2. Packaging Material:
– Type: Compatible with materials like cardboard, plastic, glass, metal, etc.
– Thickness: The system must process materials of varying thickness, from thin films to thick boxes.
– Eco-friendliness: Ability to use sustainable and recyclable materials.
### 3. Production Speed:
– Throughput Rate: Customized to meet specific production rates, ensuring high-volume efficiency or precision for smaller batches.
– Cycle Time: The time taken to complete an entire packaging cycle, aimed for optimization.
### 4. Automation Level:
– Manual, Semi-Automatic, Fully Automated: Depending on complexity, labor costs, and desired efficiency.
– Robust Control Systems: Use of PLCs, SCADA, or other control systems for integrated operations.
### 5. Quality Control:
– Inspection: Systems for weight checking, seal integrity, and visual inspections.
– Reject Mechanisms: Removal of defective or non-compliant products from the line.
### 6. Flexibility and Scalability:
– Adaptability: Capable of quick changeovers and adjustments for different packaging formats.
– Modular Design: Scalable to expand capacity or add new functionalities as needed.
### 7. Regulations and Standards:
– Compliance: Must meet industry standards like ISO, FDA, and others relevant such as food grade, pharmaceutical, or hazardous materials packaging.
– Traceability: RFID, barcoding, or serialization for product tracking and compliance.
### 8. Safety Features:
– Operator Safety: Incorporation of machine guards, emergency stops, and compliance with safety regulations.
– Product Safety: Ensuring the hygiene and integrity of the product throughout the packaging process.
Integrated packaging systems should be tailored to the specific needs of the product, ensuring efficiency, compliance, and reliability within various industries from food and beverage to pharmaceuticals and consumer goods.
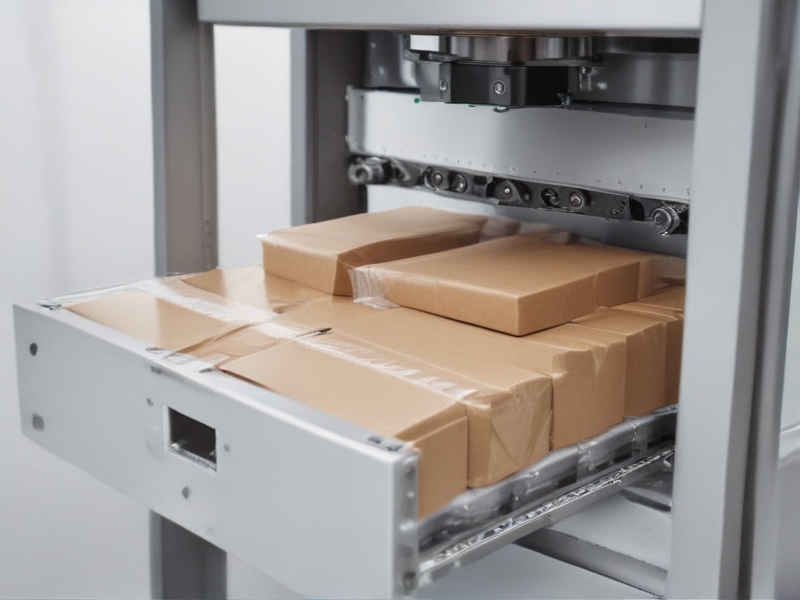
Applications of integrated packaging systems
Integrated packaging systems synergize various packaging processes into a cohesive operation, enhancing efficiency, reducing waste, and ensuring product safety. Here are some key applications:
1. Food and Beverage Industry: Integrated packaging systems optimize the bottling, labeling, and sealing processes, ensuring products are safely packaged while maintaining quality. Automated systems can accommodate varied product lines, from liquids to solids, maximizing throughput.
2. Pharmaceuticals: These systems ensure compliance with stringent regulatory standards by integrating serialization, tamper-evidence, and traceability features. Precise filling, labeling, and packaging processes safeguard against contamination and ensure dosage accuracy.
3. Consumer Electronics: For delicate items like smartphones and tablets, integrated systems automate the packaging process to prevent damage. Automated solutions handle anti-static packaging, cushioning, and precise insertion into protective cases, enhancing product protection during transit.
4. E-commerce and Retail: Streamlined packaging systems speed up the fulfillment process—automating tasks like order picking, packing, and labeling. This efficiency is crucial for meeting the quick turnarounds demanded by e-commerce customers, enhancing overall customer satisfaction.
5. Automotive: Parts and components are often irregularly shaped and require robust packaging solutions. Integrated systems can automate the kitting and packaging of parts, ensuring they are protected against physical damage and corrosion during storage and transport.
6. Cosmetics and Personal Care: These industries benefit from automated systems that handle delicate containers and dispense precise quantities into jars, bottles, or tubes. Integrated labeling and packaging processes ensure product consistency and aesthetic appeal.
Overall, integrated packaging systems offer versatility across diverse industries, providing improved productivity, reduced costs, and enhanced product integrity.
Material of integrated packaging systems
Integrated packaging systems are engineered to enhance the functionality and sustainability of packaging through the use of various materials. The most common materials include:
1. Paper and Cardboard: Highly versatile and widely recyclable, these materials are used for boxes, cartons, and cushioning. Advancements in coating and lamination have enhanced their barrier properties, making them suitable for protecting against moisture, grease, and oxygen.
2. Plastics: Polyethylene (PE), polyethylene terephthalate (PET), and polypropylene (PP) are prevalent due to their durability, flexibility, and lightweight properties. Innovations like bio-based plastics and recycled content aim to mitigate environmental impact.
3. Glass: Often used for its impermeability and inertness, glass provides excellent barrier properties for items that require long-term storage, though it is heavier and more fragile than other materials.
4. Metals: Aluminum and tinplate are primarily used for cans, foils, and closures due to their robust barrier properties against light, oxygen, and moisture. Aluminum is particularly valued for its recyclability.
5. Biodegradable Materials: Polylactic acid (PLA), starch blends, and cellulose-based materials are gaining traction. These materials decompose more readily in the environment, addressing the growing demand for eco-friendly packaging solutions.
6. Multi-layer Combinations: To leverage the strengths of different materials, multi-layered packaging (e.g., laminates of plastic films with aluminum foils or paper) provides enhanced barrier properties, though their recyclability can be complex.
Each material brings unique properties to the integrated packaging systems, balancing factors such as protection, sustainability, cost, and user convenience. The trend is moving towards reducing the environmental footprint through recyclable, biodegradable, and renewable alternatives while maintaining the integrity and efficiency of packaging solutions.
Quality Testing Methods for integrated packaging systems and how to control the quality
Ensuring the quality of integrated packaging systems involves several methodologies and controls to guarantee reliability and performance. Below are key strategies and methods:
1. Pre-production Testing:
– Material Verification: Ensure all materials meet specified standards through tests such as tensile strength, chemical composition, and thermal resistance.
– Prototype Evaluation: Create prototypes to assess design efficacy, ease of assembly, and durability.
2. In-line Inspection:
– Automated Optical Inspection (AOI): Use cameras and software to detect defects during assembly, such as misalignment or incorrect components.
– X-ray and Ultrasonic Testing: For non-destructive testing to uncover hidden flaws like voids in welds or bond integrity.
3. Functional Testing:
– Mechanical Stress Testing: Subject the packaging to forces it will encounter in real-world usage to identify weak points.
– Environmental Testing: Expose packaging to extreme temperatures, humidity, and vibration to ensure it can withstand harsh conditions.
4. Final Product Inspection:
– Leak Testing: Ensure seals are intact and containers are airtight using pressure decay or helium mass spectrometry.
– Drop and Impact Testing: Simulate handling and transportation impacts to ensure the integrity of the packaging.
5. Statistical Process Control (SPC):
– Control Charts: Monitor manufacturing processes using control charts to detect and correct variability before defects occur.
– Capability Analysis: Assess the ability of processes to produce within specified limits consistently.
6. Quality Management Systems (QMS):
– ISO 9001 Certification: Implement and maintain standards like ISO 9001 to ensure continuous quality improvement and standardized practices.
– Documentation and Record Keeping: Maintain detailed records of tests, inspections, and corrective actions for traceability and accountability.
7. Supplier Quality Management:
– Supplier Audits: Regularly audit suppliers to ensure they meet quality standards.
– Incoming Material Inspection: Test raw materials and components upon receipt to avoid integrating faulty parts.
By combining these methods, manufacturers can robustly control and assure the quality of integrated packaging systems, meeting industry standards and customer expectations.
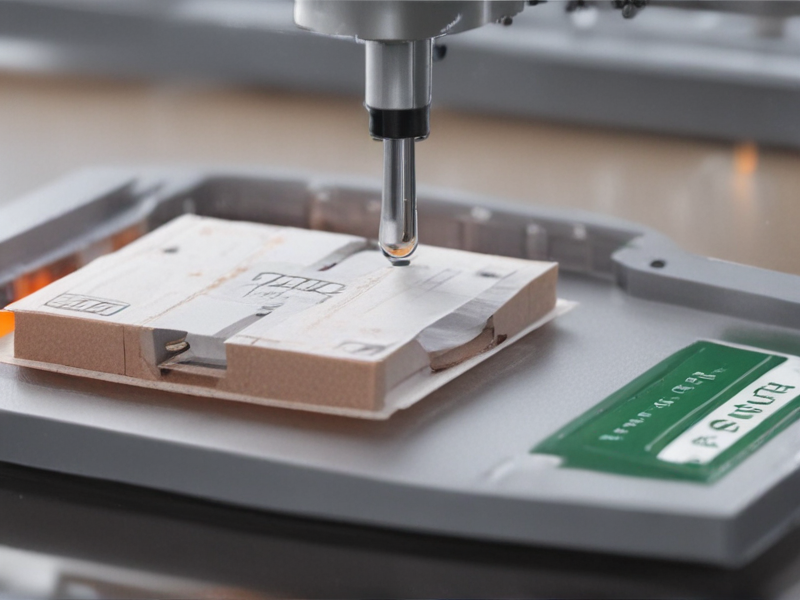
The Work Process and how to use integrated packaging systems
Integrated packaging systems streamline and automate the packaging workflow, enhancing efficiency and consistency. Here’s a concise guide to understanding and using these systems effectively:
### Work Process
1. Assessment and Planning:
– Evaluate packaging needs considering product type, volume, and specific requirements.
– Determine objectives like cost reduction, speed enhancement, or improved packaging quality.
2. System Selection:
– Choose an integrated packaging system that aligns with your objectives.
– Consider factors such as compatibility with existing operations, scalability, and technological advancements.
3. Installation and Setup:
– Install machinery such as automated packing lines, conveyor belts, and robotic arms.
– Configure software for operations management, ensuring seamless integration with enterprise systems.
4. Training and Onboarding:
– Train staff on the new system’s functionalities, safety protocols, and troubleshooting methods.
– Provide continuous learning opportunities to keep up with system updates.
5. Operational Workflow:
– Product Feeding: The system starts with feeding products into the packaging line, often through automated feeders.
– Packaging Formation: Machines form packaging materials into structures like boxes or pouches.
– Filling and Sealing: Products get filled into these structures, followed by sealing to ensure protection.
– Labeling and Coding: Apply necessary labels, barcodes, or QR codes using automated printers and applicators.
– Inspection: Integrated sensors and vision systems check for quality and accuracy.
– Cartoning and Palletizing: Finished packages are placed into cartons, which are then palletized for storage or shipping.
6. Monitoring and Maintenance:
– Utilize built-in analytics and monitoring tools to track performance metrics and identify bottlenecks.
– Schedule regular maintenance to prevent downtime and extend the system’s lifespan.
### Benefits
– Efficiency: Reduces manual intervention, speeding up the packaging process.
– Consistency: Ensures uniform packaging quality and minimizes errors.
– Cost-Effectiveness: Decreases labor costs and material waste.
Embracing integrated packaging systems can significantly optimize your packaging operations, making them faster, more reliable, and scalable.
integrated packaging systems Importing questions including Cost,Supplier,Sample,Certification and Market
Importing integrated packaging systems involves several critical aspects including cost, supplier selection, sample evaluation, certification requirements, and market considerations.
Cost:
When calculating the cost, consider both the initial purchase price and additional expenses such as shipping, customs duties, taxes, and handling fees. Currency exchange rates and international transaction fees can also impact the overall cost. It’s vital to prepare a comprehensive budget that accounts for these factors.
Supplier:
Choosing a reliable supplier is essential. Evaluate potential suppliers based on their reputation, product quality, lead times, and customer support. Request references and reviews from previous clients. Site visits, if feasible, can provide deeper insights into their capabilities and production practices.
Sample:
Before making a large purchase, request samples to test the system’s performance, compatibility, and quality. Samples can help identify any potential issues before committing to a full order. Ensure the sample is representative of the entire production batch.
Certification:
Certifications ensure that the packaging systems meet industry standards and regulatory requirements. Depending on your market, check for certifications like ISO, CE, UL, and RoHS. Proper certification can not only ensure compliance but also add credibility and trust to your product offerings.
Market:
Thoroughly analyze your target market’s needs and preferences. Determine demand, competition, and regulatory environment in the destination market. Adapt your strategies based on market trends and consumer behavior. Tailored marketing approaches, such as highlighting unique features or eco-friendliness, can differentiate your product.
Summary:
Successfully importing integrated packaging systems requires meticulous planning. Focus on optimizing costs, selecting trusted suppliers, evaluating samples rigorously, ensuring necessary certifications, and understanding market dynamics to achieve business success.
How to find and select check reliable integrated packaging systems manufacturers in China
Finding and selecting reliable integrated packaging systems manufacturers in China involves several steps:
1. Research and Shortlist: Start with online directories (e.g., Alibaba, Made-in-China) to identify potential manufacturers. Shortlist based on positive reviews, comprehensive product listings, and years of experience.
2. Verify Credentials: Check their business licenses, ISO certifications, and any industry-specific certificates. Reliable manufacturers will readily provide these documents.
3. Assess Experience and Capabilities: Look for manufacturers with extensive experience in producing integrated packaging systems. Evaluate their production capacity, range of technology, and design capabilities. Browse their portfolio and case studies to understand their expertise.
4. Quality Control Procedures: Inquire about their quality control processes. Reliable manufacturers will have stringent quality checks and adhere to international standards.
5. Request Samples: Before making a decision, request product samples to assess the quality firsthand. This step is crucial in verifying the manufacturer’s ability to meet your standards.
6. Communicate Directly: Engage in direct communication through emails, video calls, or visits. Effective communication can provide insights into their professionalism, responsiveness, and willingness to collaborate.
7. Check References and Reviews: Speak to existing clients or read detailed online reviews. Satisfied customers often indicate reliable manufacturers.
8. Evaluate Logistics and Support: Consider their ability to deliver on time and provide post-sales support. Reliable manufacturers offer excellent customer service and after-sales support.
9. Compare Pricing and Terms: While cost is crucial, it should not compromise quality. Compare pricing, payment terms, and warranty conditions from multiple manufacturers to ensure you get the best value.
By following these steps, you can select a reputable and reliable integrated packaging systems manufacturer in China.
Background Research for integrated packaging systems manufacturers Companies in China, use qcc.com archive.org importyeti.com
Conducting background research on integrated packaging systems manufacturers in China can be streamlined using resources like qcc.com, archive.org, and importyeti.com. These platforms offer pivotal insights into company profiles, historical data, and import/export activities, respectively.
qcc.com:
qcc.com is a comprehensive business directory and credit information system in China. It allows users to search for companies by industry category and obtain detailed business information, including registration details, financial status, and operational history. Key integrated packaging systems manufacturers in China that can be found on qcc.com include Shanghai Custom Packaging Co., Ltd., Hangzhou Bojun Precision Machine Co., Ltd., and Qingdao Ausense Packing Equipment Co., Ltd. These companies exhibit robust profiles with extensive product lines ranging from automated packing machines to customized packaging solutions.
archive.org:
archive.org, also known as the Wayback Machine, offers historical snapshots of websites. This can be particularly useful for examining the development and evolution of company websites and their product offerings. For instance, by searching for archived versions of the websites of leading packaging systems manufacturers like Guangzhou Ming Na Packaging Equipment Co., Ltd., one can track changes in product focus, technological advancements, and market expansion over the years.
importyeti.com:
importyeti.com provides detailed supply chain data based on import records. This can help in identifying the global reach and partnerships of Chinese integrated packaging systems manufacturers. For instance, a search on importyeti.com for the likes of Foshan Land Packaging Machinery Co., Ltd. reveals their export patterns, key clients, and the types of packaging machinery that are frequently shipped to international markets. This data is crucial for understanding the market dynamics and the international competitiveness of these firms.
In summary, using these three platforms, one can gather comprehensive insights into leading integrated packaging systems manufacturers in China, highlighting their business operations, historical developments, and global trade activities. This approach ensures a well-rounded understanding of the industry within a succinct format.
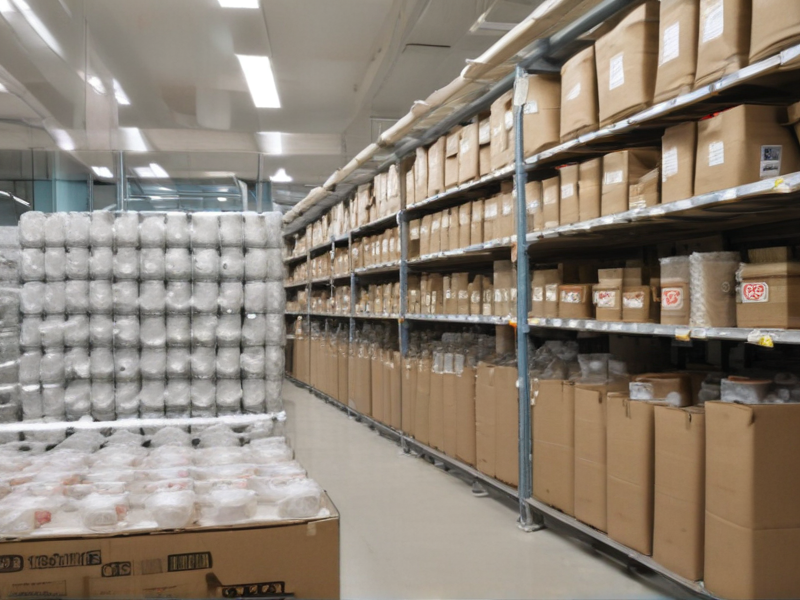
Price Cost Research for integrated packaging systems manufacturers Companies in China, use temu.com and 1688.com
When conducting price cost research for integrated packaging systems manufacturers in China using platforms such as Temu.com and 1688.com, it’s essential to focus on the following key factors: equipment type, pricing, features, and manufacturer reputation.
1. Platform Overview:
– Temu.com: This platform offers a broad range of products, including machinery from various manufacturers. It’s an international marketplace with competitive pricing and a range of options.
– 1688.com: A subsidiary of Alibaba Group, it’s tailored primarily for domestic B2B transactions in China. It often provides detailed product specifications and bulk purchase options.
2. Product Types and Prices:
– Integrated Packaging Systems: These include machinery for processes like filling, sealing, labeling, and palletizing.
Temu.com Findings:
– Automatic Filling and Sealing Machines: Prices range from $5,000 to $20,000 depending on capacity and features.
– Labeling Machines: Priced between $2,000 to $8,000, influenced by speed and precision.
– Palletizers: Range from $10,000 to $30,000, varying by automation level.
1688.com Findings:
– Automatic Filling and Sealing Machines: Generally priced between Â¥30,000 to Â¥120,000 (approximately $4,500 to $18,000).
– Labeling Machines: Often cost between Â¥10,000 to Â¥50,000 ($1,500 to $7,500).
– Palletizers: Found between Â¥70,000 to Â¥200,000 ($10,500 to $30,000).
3. Key Features:
– High-Speed Operations
– Multi-Functionality (e.g., combined filling and sealing)
– Advanced control systems (e.g., PLC touch screen)
– Durability and reliability
4. Manufacturer Reputation:
– Temu.com: Features include user reviews and ratings which can help gauge the reliability of manufacturers.
– 1688.com: Provides detailed supplier profiles, including verification status and transaction history.
Conclusion:
Both platforms offer competitive pricing but differ in their interface and target markets. Temu.com is better for international buyers due to its accessible interface, while 1688.com offers deeper insights into domestic Chinese manufacturers. For large-scale purchases, 1688.com may offer more robust options and better bulk rates. Always ensure to verify supplier credibility through reviews and transaction histories.
Shipping Cost for integrated packaging systems import from China
Shipping costs for importing integrated packaging systems from China can vary widely based on several factors. These include the shipping method, weight, dimensions, and value of the goods, as well as the shipping destination and any additional services required. Here’s an overview to help you estimate costs:
1. Shipping Methods:
– Sea Freight: Generally the most cost-effective for large or heavy shipments. Costs are influenced by container size (e.g., 20-foot or 40-foot containers) and can range from $1,000 to $5,000 per container depending on the shipping route and season.
– Air Freight: Faster but more expensive, suitable for smaller, high-value shipments. Costs can range from $5 to $10 per kilogram.
2. Additional Costs:
– Customs Duties and Taxes: Vary by country; you may need to consult your local customs office to estimate these costs.
– Insurance: Typically around 0.1% to 0.5% of the shipment’s value.
– Handling Fees: Costs can include warehousing, loading, unloading, and delivery to the final destination.
3. Example Cost Breakdown:
– Sea Freight: For a 20-foot container, you might expect costs around $1,500 to $2,500.
– Customs Duties: If the customs duty rate is 5% on a $50,000 shipment, you’ll owe $2,500 in duties.
– Insurance: Around $250 for a $50,000 shipment.
– Handling Fees: Can add an additional $500 to $1,000.
4. Incoterms:
– FOB (Free On Board): Buyer pays for sea freight and insurance.
– CIF (Cost, Insurance, and Freight): Supplier covers sea freight and insurance.
To get specific quotes, contact international freight forwarders or shipping companies, providing detailed information about your shipment. Always consider obtaining multiple quotes to ensure competitive pricing.
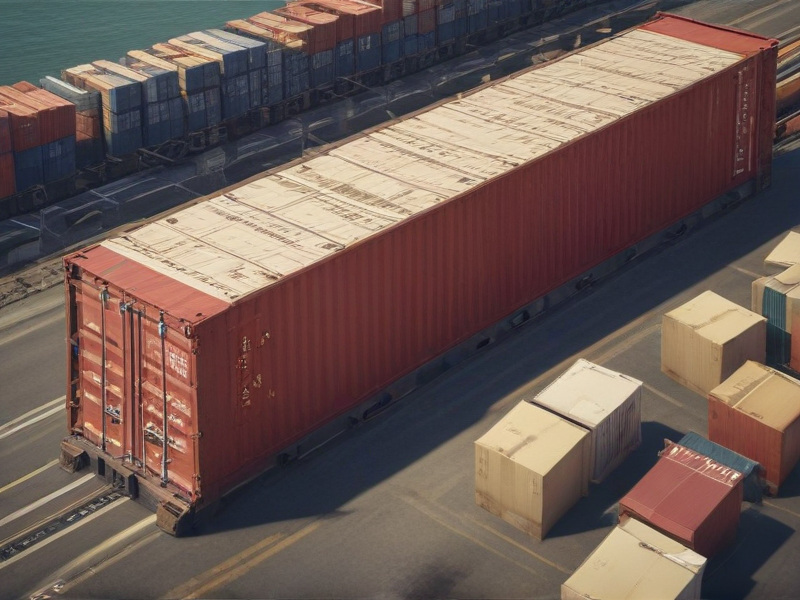
Compare China and Other integrated packaging systems Markets: Products Quality and Price,Visible and Hidden Costs
### China vs. Other Integrated Packaging Systems Markets:
Product Quality and Price:
– China: Known for its cost-effective production capabilities, China offers lower-priced packaging systems. However, the quality can vary widely, with high-end manufacturers offering competitive quality but often at increased prices.
– Other Markets: Countries like Germany, Japan, and the USA are renowned for high-quality, reliable packaging systems. Their products generally command higher prices compared to Chinese counterparts due to advanced technology, durability, and brand reputation.
Visible Costs:
– China: Lower initial purchase prices make Chinese packaging systems attractive. Shipping costs can also be competitive due to subsidized export strategies.
– Other Markets: Higher upfront costs reflect the advanced engineering, R&D, and stricter quality control measures. Shipping from these countries can be more expensive, especially for complex machinery.
Hidden Costs:
– China: Potential for higher hidden costs including maintenance, frequent repairs, and shorter lifespan of machinery. Spare parts may also be less durable, leading to increased downtime.
– Other Markets: Generally have lower hidden costs due to robust design and higher reliability. After-sales service and warranties tend to be more comprehensive, reducing long-term expenses.
Overall Comparison:
China is suitable for businesses prioritizing lower upfront costs and quick scalability, provided they are prepared for possible quality trade-offs and higher maintenance. Conversely, other markets are ideal for companies that value long-term reliability, superior technology, and are willing to invest more initially to minimize hidden costs.
The choice largely depends on a company’s budget, quality standards, and long-term strategy.
Custom Private Labeling and Branding Opportunities with Chinese integrated packaging systems Manufacturers
Partnering with Chinese integrated packaging systems manufacturers offers a wealth of custom private labeling and branding opportunities for businesses looking to enhance their market presence. These manufacturers bring a unique combination of cost-efficiency, advanced technology, and robust production capacity, enabling bespoke packaging solutions tailored to specific brand needs.
### Key Advantages
1. Cost-Effectiveness: Leveraging China’s competitive production costs allows brands to access high-quality packaging solutions at a fraction of the price compared to Western manufacturers. This cost savings can be reinvested into other areas of the business, such as marketing and product development.
2. Customization: Chinese manufacturers are known for their flexibility in accommodating custom designs and specific requirements. This includes various packaging styles, materials, and printing techniques, ensuring that products align seamlessly with brand identity. Whether it’s luxury packaging or eco-friendly options, these manufacturers can provide the perfect fit.
3. Technological Edge: Many Chinese packaging companies utilize state-of-the-art machinery and technology, ensuring precision and innovative packaging solutions. This technological advantage translates to superior quality control and the ability to produce intricate designs and functionalities that enhance the consumer experience.
4. Production Capacity: With their substantial production capacity, Chinese manufacturers can handle large orders within tight deadlines, ensuring that businesses meet market demands without compromising on quality or delivery times.
5. Sustainability Options: Increasingly, Chinese manufacturers are adopting eco-friendly practices and materials, offering sustainable packaging solutions. Brands looking to minimize their environmental footprint can find reliable partners who share these values.
### Operational Considerations
1. Quality Assurance: It’s crucial to establish stringent quality control measures to maintain high standards. Regular site visits and third-party inspections can help ensure consistency.
2. Communication: Clear, ongoing communication is key to overcoming language barriers and ensuring that specifications are met accurately.
3. Legal Compliance: Ensure that intellectual property rights are safeguarded and that all legal and regulatory requirements are adhered to.
By tapping into the capabilities of Chinese integrated packaging systems manufacturers, brands can significantly enhance their product presentation while maintaining cost-efficiency and operational scalability.
Tips for Procurement and Considerations when Purchasing integrated packaging systems
When procuring integrated packaging systems, a strategic approach ensures cost-effectiveness and operational efficiency. Here are some key tips and considerations:
1. Needs Assessment: Clearly define packaging requirements, including capacity, speed, and product types. Understand the specific needs of your production line to choose appropriate systems.
2. Scalability: Select systems that can scale with your business growth. Flexibility to handle varying product sizes and volumes is crucial.
3. Quality and Compliance: Ensure the system complies with industry standards and regulations. Check for certifications and quality assurance metrics.
4. Technology Integration: Opt for systems that can seamlessly integrate with existing equipment and software (e.g., ERP systems). Compatibility reduces downtime and enhances productivity.
5. Total Cost of Ownership (TCO): Consider not just the initial purchase price but also the long-term costs, including maintenance, energy consumption, and potential upgrades.
6. Vendor Reputation: Research and choose reputable vendors with proven track records in reliability, service, and support. Seek references and read reviews.
7. Training and Support: Verify that the vendor provides comprehensive training for your staff and robust after-sales support, including technical assistance and spare parts availability.
8. Customization: Assess the possibility of customized solutions to fit unique packaging requirements. Customization can offer competitive advantages.
9. Energy Efficiency: Focus on energy-efficient systems to reduce operational costs and environmental impact.
10. Future-Proofing: Keep an eye on technological advancements. Invest in systems that incorporate the latest technologies and can adapt to future needs.
By paying attention to these factors, you can make informed decisions that will enhance productivity, reduce costs, and ensure seamless packaging operations.
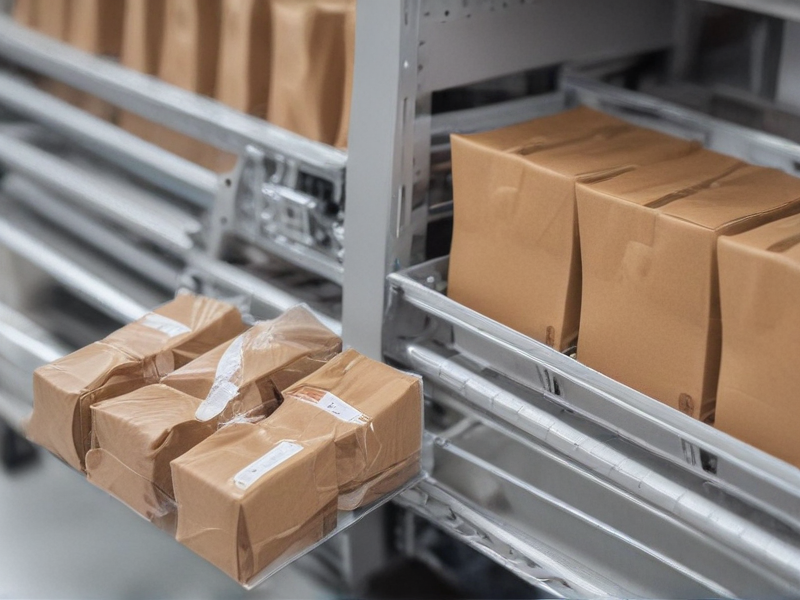
FAQs on Sourcing and Manufacturing integrated packaging systems in China
FAQs on Sourcing and Manufacturing Integrated Packaging Systems in China
1. Why choose China for sourcing integrated packaging systems?
China offers cost-effective manufacturing, a vast selection of suppliers, advanced technology, and a well-established production ecosystem, making it ideal for sourcing packaging systems.
2. How do I find reliable suppliers?
Use sourcing platforms such as Alibaba, Global Sources, and Made-in-China. Attend trade shows like Canton Fair, and consider visiting industrial hubs like Shenzhen or Ningbo.
3. What should I look for in a supplier?
Check the supplier’s certifications (e.g., ISO standards), their experience in the industry, the quality of their products, customer reviews, and their ability to meet your customization needs.
4. How can I verify the quality of products?
Request samples, conduct third-party inspections, or hire local quality control agencies. Visiting the factory for an audit is also advisable.
5. What is the typical lead time for manufacturing?
Lead times can range from 30 to 90 days depending on the complexity and quantity of the packaging systems ordered.
6. How do I handle shipping and logistics?
Hire a reliable freight forwarder. They can manage customs documentation, shipping schedules, and warehousing. Sea freight is cost-effective for bulk orders, while air freight is faster but expensive.
7. What are the payment terms?
Common terms include 30% deposit upon order confirmation and 70% balance before shipment. Using escrow services offers additional security.
8. How do I handle language barriers and cultural differences?
Employ bilingual intermediaries or sourcing agents who understand local business etiquette and practices.
9. What about intellectual property (IP) protection?
Draft clear contracts that include IP protection clauses. Register your trademarks and patents in China to legally safeguard your IP.
10. Are there any import restrictions?
Check your country’s import regulations for specific restrictions and duties on packaging machinery and ensure compliance to avoid legal issues.
By addressing these FAQs, you can streamline sourcing and manufacturing integrated packaging systems in China confidently and effectively.