Top 10 visual inspection system in China introduce,list main products and website if have
Certainly! Here are the top 10 visual inspection systems in China, along with their main products and websites:
1. Hikvision
– Main Products: Machine vision cameras, smart sensors, and deep-learning software.
– Website: [hikvision.com](https://www.hikvision.com)
2. Daheng Imaging
– Main Products: Industrial cameras, frame grabbers, and software libraries.
– Website: [daheng-imaging.com](http://www.daheng-imaging.com)
3. SunVision
– Main Products: Automated optical inspection (AOI) systems, machine vision software, and industrial cameras.
– Website: [sunvision-tech.com](http://www.sunvision-tech.com)
4. CCS Inc. China
– Main Products: LED lighting solutions, machine vision systems, and inspection software.
– Website: [ccs-grp.com](https://www.ccs-grp.com.cn)
5. Daheng Optics
– Main Products: AOI systems, visual positioning systems, and special inspection equipment.
– Website: [computar.com.cn](http://www.computar.com.cn)
6. Euresys Shanghai
– Main Products: Frame grabbers, image acquisition boards, and vision software.
– Website: [euresys.com](https://www.euresys.com)
7. Omron China
– Main Products: AOI systems, 3D vision sensors, and machine vision software.
– Website: [omron.com.cn](https://www.omron.com.cn)
8. Cognex China
– Main Products: Vision systems, barcode readers, and deep learning solutions.
– Website: [cognex.cn](https://www.cognex.cn)
9. Basler China
– Main Products: Industrial cameras, lighting solutions, and image processing software.
– Website: [baslerweb.com](https://www.baslerweb.com/en/sales-and-support/our-locations/china/)
10. Keyence China
– Main Products: Laser sensors, 3D measurement sensors, and microscope systems.
– Website: [keyence.com.cn](https://www.keyence.com.cn)
These companies are renowned for their advanced visual inspection systems and solutions. Their products span a variety of industries including manufacturing, automotive, electronics, and pharmaceuticals.
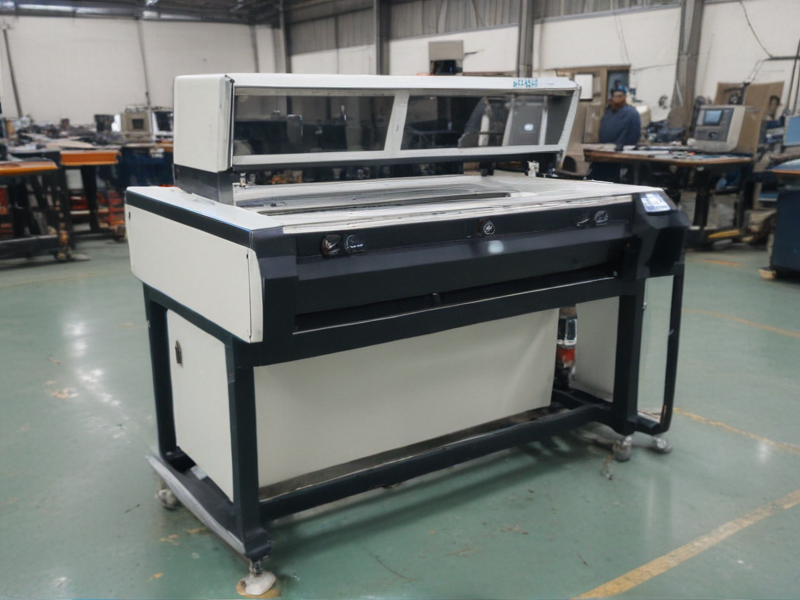
Types of visual inspection system
Visual inspection systems are crucial in numerous industries to ensure product quality and integrity. They can be broadly categorized into several types:
1. Manual Visual Inspection (MVI):
– Description: Involves human inspectors visually checking products for defects or irregularities.
– Pros: Flexible and able to detect subtle defects.
– Cons: Prone to human error, fatigue, and can be inconsistent.
2. Automated Visual Inspection (AVI):
– Description: Utilizes cameras and image processing software to detect defects automatically.
– Pros: Highly accurate, consistent, and efficient.
– Cons: High initial cost, complexity in setup.
3. Destructive Visual Inspection:
– Description: Involves examining the internal structure of a product after it has been intentionally damaged or disassembled.
– Pros: Provides detailed internal defect information.
– Cons: The product is destroyed and cannot be sold or used.
4. Non-Destructive Visual Inspection (NDVI):
– Description: Inspection without causing any damage to the product, often using advanced imaging techniques such as X-ray or ultrasound.
– Pros: Preserves product integrity and can detect internal defects.
– Cons: Generally more costly and requires specialized equipment.
5. Inline Visual Inspection:
– Description: Integrated into the production line to inspect products in real-time.
– Pros: Immediate feedback, assists in maintaining continuous quality control.
– Cons: Can slow down production if not optimized correctly.
6. Offline Visual Inspection:
– Description: Conducted separately from the production process.
– Pros: Does not interfere with production speed.
– Cons: Time-consuming and may delay defect detection.
Each type of system is tailored to specific needs, balancing factors like cost, speed, accuracy, and the nature of the defects being inspected.
Pros and Cons of Using visual inspection system
Pros and Cons of Using a Visual Inspection System
Pros:
1. Speed and Efficiency: Automated visual inspection systems can process large volumes of items quickly, increasing throughput and reducing cycle times compared to manual inspection.
2. Consistency and Accuracy: These systems minimize human errors and inconsistencies, providing reliable and repeatable results.
3. Cost Savings: Over time, the initial investment in a visual inspection system can lead to cost savings by reducing the need for manual labor and minimizing errors that could result in defective products reaching customers.
4. 24/7 Operation: Automated systems can work continuously without fatigue, maximizing productivity and operational uptime.
5. Enhanced Data Collection: These systems can capture and analyze large amounts of data, helping in quality control, trend analysis, and predictive maintenance.
6. Safety: Reduces the need for human inspectors to interact with potentially hazardous environments or materials.
Cons:
1. High Initial Cost: The upfront investment for purchasing and setting up visual inspection systems can be significant, especially for small and medium-sized enterprises.
2. Complexity: Implementing these systems can be complex and may require specialist knowledge to install, calibrate, and maintain.
3. Limitations in Flexibility: Automated systems may struggle with items that have high variability in appearance or require subjective judgment, areas where human inspectors excel.
4. Maintenance: Requires ongoing maintenance and periodic updates to ensure optimal performance, adding to the operational costs.
5. Dependency on Technology: Over-reliance on automated systems may lead to significant downtime if the system fails, making contingency planning essential.
6. Initial Learning Curve: Workers may need training to operate and troubleshoot the system, which could temporarily slow down operations and add to training costs.
In summary, while visual inspection systems offer significant advantages in terms of speed, efficiency, and accuracy, they also come with challenges such as high initial costs and complexity. The decision to implement such a system should consider both the immediate requirements and long-term benefits.
visual inspection system Reference Specifications (varies for different product)
Visual Inspection System: Reference Specifications
1. Objective & Scope:
– To ensure product quality by detecting defects, inconsistencies, and deviations from specified standards using automated visual inspection.
2. System Components:
– Cameras: High-resolution CCD or CMOS cameras.
– Lighting: LED, fiber optics, or laser illumination for consistent lighting conditions.
– Processing Unit: High-performance CPUs or GPUs for real-time image processing.
– Software: Advanced image processing algorithms, AI, and machine learning capabilities.
– Sensors: To detect object presence and position.
– Conveyors/Fixtures: To transport and position products within the inspection area.
3. Inspection Capabilities:
– Defect Detection: Scratches, dents, cracks, discoloration.
– Dimensional Verification: Measurements within micron accuracy.
– Pattern Recognition: Identifying labels, logos, and text.
– Surface Inspection: Analysis for texture, color consistency, and contamination.
4. Operational Requirements:
– Speed: Capable of inspecting up to 1000 units per minute (vary with product type).
– Accuracy: Detection accuracy up to 99.9%.
– Resolution: Camera resolution ranging from 2 MP to 20 MP, depending on product size and detail requirements.
– Lighting: Adjustable lighting intensity and angle for optimal inspection conditions.
5. Integration & Compatibility:
– Connectivity: Ethernet, USB, and wireless options for integration with existing systems.
– Software: Compatible with major industry-standard inspection software.
– Data Management: Real-time data analytics, storage, and reporting features.
– User Interface: Intuitive GUI for system setup, control, and monitoring.
6. Environmental Conditions:
– Temperature Range: 10°C to 45°C.
– Humidity: 20% to 80% non-condensing.
– Vibration: Resistant to industrial vibrations and shocks.
7. Compliance & Standards:
– Safety: Compliance with CE, ISO, and other relevant industry standards.
– Maintenance: Easy access for regular maintenance and cleaning.
8. Applications:
– Suitable for industries like automotive, pharmaceuticals, electronics, and packaging.
Note: Specifications can vary based on specific product and industry requirements. Custom configurations are available.
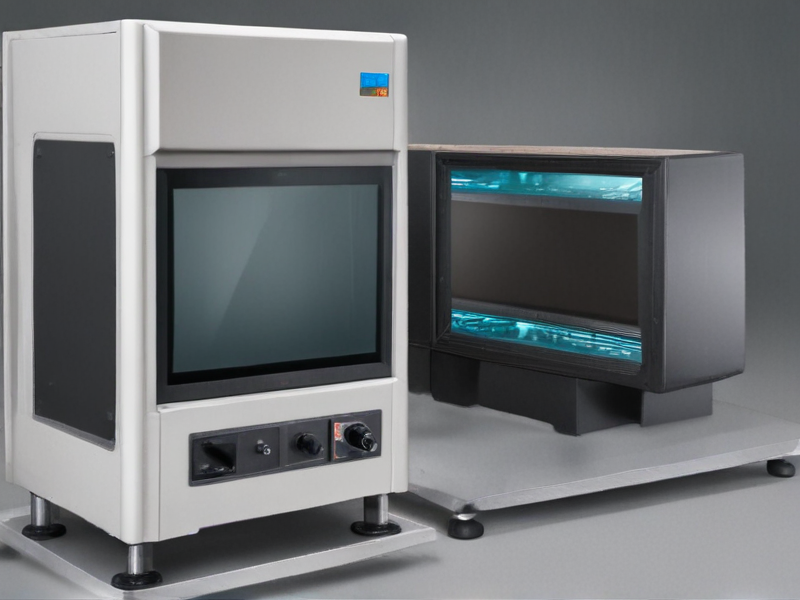
Applications of visual inspection system
A visual inspection system leverages cameras, image processing, and machine learning to inspect, monitor, and analyze products or environments. This technology has diverse applications across multiple industries:
1. Manufacturing: Visual inspection systems ensure quality control by detecting surface defects, misalignments, and dimensional inaccuracies in products. They are extensively used in the automotive, electronics, and pharmaceutical sectors to maintain high-quality standards and compliance.
2. Food and Beverage: In food production, these systems inspect products for contaminants, proper labeling, and packaging integrity. They help ensure safety, quality, and consistency, reducing the risk of recalls and ensuring regulatory compliance.
3. Medical Devices: Inspection systems check for defects in medical devices and components, ensuring they meet stringent industry standards. They play a crucial role in verifying the precision and reliability of devices used in healthcare.
4. Aerospace: In the aerospace industry, visual inspection systems are used for detecting material flaws, surface defects, and structural integrity issues in aircraft components, ensuring safety and reliability.
5. Construction: These systems monitor ongoing projects for compliance with design specifications, identify structural defects, and ensure safety standards are met on construction sites.
6. Packaging: Visual inspection is used to verify proper sealing, labeling, and marking on packaging, ensuring accuracy and preventing mix-ups in product distribution.
7. Textile Industry: They check for flaws in fabrics, such as dye inconsistencies, weave defects, and missing threads, improving product quality and reducing waste.
8. Semiconductor Industry: Inspection systems detect defects on silicon wafers, and ensure the integrity and functionality of microchips, which is critical for the reliability of electronic devices.
By automating the inspection process, these systems enhance efficiency, reduce human error, and lower costs, contributing significantly to the precision and quality control across various sectors.
Material of visual inspection system
A visual inspection system is crucial for quality control in manufacturing and automation. The system typically comprises several materials and components to ensure accurate and reliable inspection.
1. Cameras: High-resolution industrial cameras are essential. They may come with CCD or CMOS sensors, depending on the required image quality and speed. The camera housing is usually made of robust materials like aluminum or stainless steel to withstand industrial environments.
2. Lenses: High-quality optical lenses are used to capture detailed images. These lenses are often made of precision-ground optical glass with anti-reflective coatings to enhance image clarity.
3. Lighting: Proper illumination is vital for capturing clear images. Common materials include LEDs for their longevity and consistent light output. LED housings are usually made from aluminum or plastic.
4. Frame/Enclosure: The system’s frame is generally constructed from aluminum or steel to provide stability and protection. This enclosure protects sensitive components from dust, moisture, and mechanical damage.
5. Processing Unit: The system requires a powerful processing unit, often composed of a ruggedized computer with specialized image processing software. These units are generally housed in metal or high-impact plastic cases to safeguard against industrial wear and tear.
6. Cables and Connectors: High-quality cables and connectors are crucial for data transmission and power supply. They are typically made from materials like copper, with insulation of PVC or rubber to ensure durability and flexibility.
7. Mounting Equipment: Adjustable mounting brackets and stands, usually made from metal alloys, allow for precise positioning of the camera and lighting components.
These materials collectively ensure that a visual inspection system is robust, reliable, and capable of performing in demanding industrial environments, thereby maintaining high standards of product quality.
Quality Testing Methods for visual inspection system and how to control the quality
Quality testing for visual inspection systems is crucial to ensure they accurately detect defects and issues. Below are key methods and control measures:
1. Basic Methods for Visual Inspection:
– Manual Inspection: Operators visually scrutinize products to spot defects. Suitable for simple, low-volume inspections but prone to human error and fatigue.
– Automated Visual Inspection (AVI): Uses cameras and software to detect flaws. Ideal for high-volume production due to consistency and speed.
– Comparative Analysis: Compares images of products against a reference image to identify anomalies. Effective for detecting visible defects.
2. Quality Control Measures:
– Training Data: For AVI systems, using a comprehensive dataset of both defect-free and defective products improves the accuracy of machine learning algorithms.
– Calibration: Regularly calibrate cameras and sensors to maintain precise detection.
– Environment Control: Ensure consistent lighting and minimal vibrations to avoid false readings in automated systems.
– Performance Metrics: Track key metrics such as false positives, false negatives, detection rate, and processing time to continually assess system performance.
– Redundancy: Employ a combination of manual and automated inspections to compensate for potential gaps in either method.
3. Validation and Continuous Improvement:
– Prototyping: Test the system in a controlled environment with sample defects before full-scale deployment.
– Regular Audits: Conduct periodic audits of the systems’ performance and recalibrate as needed.
– Feedback Loop: Implement a feedback mechanism where defect data is used to retrain models, enhancing their accuracy over time.
– Employee Training: Ensure that operators are well-trained in both manual and automated inspection systems for better synergistic outcomes.
Implementing these methods and controls helps in maintaining high inspection accuracy, reducing defects, and improving overall product quality.
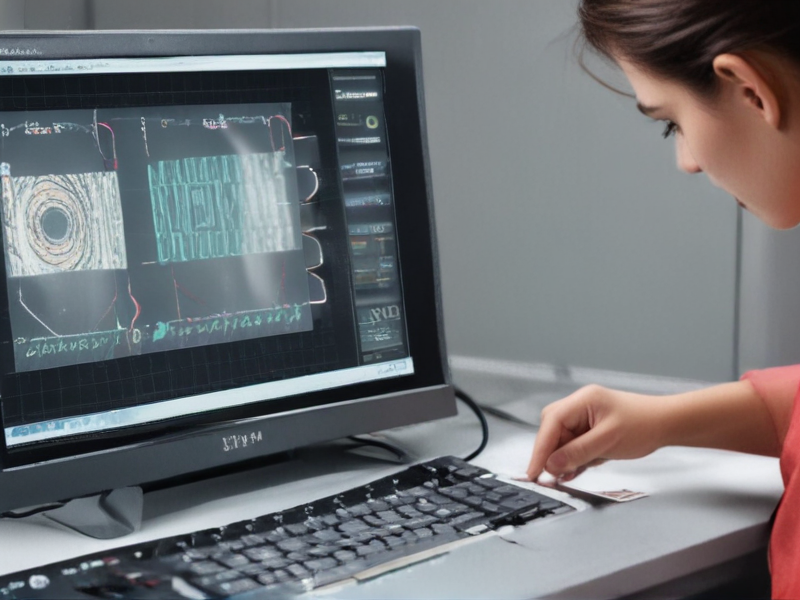
The Work Process and how to use visual inspection system
A visual inspection system is integral in quality control, leveraging imaging technology to scrutinize products efficiently and accurately. Here’s a concise guide on how to use such a system:
1. Setup and Calibration:
– Install Equipment: Position the cameras, lighting, and sensors appropriately for the product area.
– Calibration: Calibrate the system to ensure accurate measurements and assessments. This may require using reference standards or adjusting parameters to match the inspection criteria.
2. Defining Inspection Criteria:
– Image Acquisition Settings: Set the resolution, focus, exposure, and other camera settings.
– Specify Defects: Input specifications for acceptable quality and define the defects that need identification (e.g., scratches, misalignments, deformations).
3. Training the System:
– Sample Runs: Run a series of sample inspections to “teach” the system. Use a set of known good and defective products to train machine learning algorithms, if applicable.
– Fine-Tuning: Adjust parameters based on initial run results to improve accuracy.
4. Real-Time Inspection:
– Continuous Monitoring: The system should consistently capture images of the products passing on the production line.
– Automated Analysis: Algorithms process images in real-time to detect defects. The system compares captured images against the predefined criteria.
5. Data Handling and Reporting:
– Alert Mechanisms: Set up the system to flag defects, log instances, or trigger rejection mechanisms (like ejecting faulty items from the line).
– Report Generation: Compile inspection data into reports for quality control analysis and historical tracking.
6. Maintenance and Updates:
– Regular Checks: Periodically recalibrate and maintain the equipment to ensure persistent accuracy.
– Software Updates: Implement software updates for improved functionality and to keep up with evolving detection algorithms.
By integrating a visual inspection system, manufacturers can enhance quality control processes, reduce manual inspection errors, and maintain consistent product standards efficiently.
visual inspection system Importing questions including Cost,Supplier,Sample,Certification and Market
When importing a visual inspection system, several factors need to be considered to ensure a smooth process. Here are important questions related to cost, supplier, sample, certification, and market:
### Cost:
1. What is the initial purchase price of the visual inspection system?
2. Are there any additional costs such as import duties, shipping fees, or taxes?
3. What are the maintenance and operational costs?
4. Are there bulk purchase discounts or financing options available?
5. What is the return on investment (ROI) period compared to existing inspection methods?
### Supplier:
1. Who are the leading suppliers or manufacturers of visual inspection systems?
2. What is the supplier’s reputation in terms of reliability and customer service?
3. Are there any exclusive distributors or agents in my region?
4. Does the supplier offer installation and training services?
5. Can the supplier provide client references or case studies?
### Sample:
1. Can I obtain a live demonstration or trial period before purchasing?
2. Are demo units available for testing the system with my specific products?
3. What are the sample requirements for different inspection scenarios?
4. Will the demo unit be representative of the production units in terms of performance?
5. Are there any costs associated with obtaining or returning the sample/demo unit?
### Certification:
1. What certifications and standards does the visual inspection system comply with?
2. Is the system certified by relevant industry standards like ISO, CE, or UL?
3. Are there specific certifications required for my industry or region?
4. Does the system include software that meets compliance for data integrity (e.g., CFR 21 Part 11 for pharmaceuticals)?
5. Is there an audit trail or document proof of certification that can be shared?
### Market:
1. What is the market demand for the visual inspection system in my industry?
2. Who are the key competitors using similar systems?
3. What are the latest technological trends in visual inspection systems?
4. How does this system improve product quality and market competitiveness?
5. Are there partnerships or industry networks that could leverage the use of this system?
Considering these questions will help ensure that you make an informed decision when importing a visual inspection system.
How to find and select check reliable visual inspection system manufacturers in China
Finding and selecting reliable visual inspection system manufacturers in China requires a structured approach. Here’s a concise guide:
1. Research Online:
– Use platforms like Alibaba, Made-in-China, and Global Sources.
– Check industry-specific forums and LinkedIn for recommendations.
2. Verify Company Credentials:
– Look for certifications like ISO 9001.
– Check the company’s establishment year and scale of operation.
– Request client references and case studies.
3. Assess Product Quality:
– Request product specifications and datasheets.
– Inquire about technology used, accuracy, and inspection speed.
4. Communication and Support:
– Ensure clear and prompt communication.
– Evaluate the quality of customer support.
– Check if they offer after-sales services and technical support.
5. Factory Visit and Audit:
– If possible, visit the manufacturer’s facility.
– Observe manufacturing processes and quality control measures.
– Assess their R&D capabilities.
6. Samples and Prototyping:
– Request samples to test performance.
– Review quality, consistency, and reliability of the samples.
7. Check Reviews and Ratings:
– Look for online reviews from previous customers.
– Check ratings on B2B platforms and third-party review sites.
8. Compare Multiple Suppliers:
– Obtain quotes from multiple manufacturers.
– Compare costs, warranties, and additional benefits.
9. Legal Safeguards:
– Ensure contracts are detailed and legally binding.
– Include terms for quality assurance and delivery timelines.
10. Start Small:
– Begin with a small order to evaluate performance before scaling up.
This approach will help you identify competent and trustworthy visual inspection system manufacturers in China.
Background Research for visual inspection system manufacturers Companies in China, use qcc.com archive.org importyeti.com
Conducting background research on visual inspection system manufacturers in China can be streamlined using several resources like qcc.com, archive.org, and importyeti.com. Here is a concise summary of the findings:
### Qcc.com
Qcc.com is a comprehensive platform for accessing Chinese company profiles, including financial health, industrial classification, and market reputation. Prominent companies in the visual inspection system market in China include:
– Omron (China) Co., Ltd.: Known for its advanced automation technologies, it offers robust visual inspection systems suitable for various industries.
– Cognex China: A leader in machine vision systems, Cognex provides state-of-the-art visual inspection solutions widely adopted in manufacturing.
– Siasun Robot & Automation Co., Ltd.: This company focuses on innovative robotics and automation technologies, including sophisticated visual inspection systems.
### Archive.org
Archive.org offers historical records and snapshots of websites, which are useful for tracking the evolution, milestones, and updates from these manufacturers. For instance, searching for old snapshots of Omron’s and Cognex’s Chinese websites can reveal product updates, historical product performance, and significant partnerships.
### Importyeti.com
Importyeti.com is beneficial for understanding trade flows and partners by examining US import data. Key insights include:
– Purchase records: Data shows frequent imports of visual inspection systems and components by various Chinese manufacturers into the US market. For instance, shipments from Cognex and Omron indicate a consistent demand.
– Trade partners: Information on key US companies importing from these Chinese manufacturers helps in assessing product popularity and trust.
In summary, Omron (China), Cognex China, and Siasun Robot & Automation are notable manufacturers of visual inspection systems in China. Utilizing qcc.com, archive.org, and importyeti.com provides a comprehensive understanding of their market presence, historical records, and trade activities.
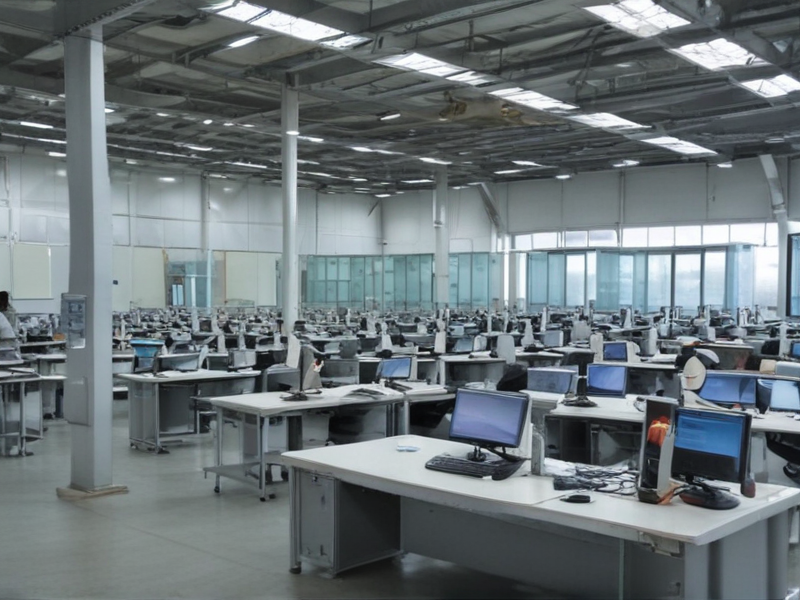
Price Cost Research for visual inspection system manufacturers Companies in China, use temu.com and 1688.com
Conducting price cost research for visual inspection systems in China can be efficiently done using platforms like Temu.com and 1688.com. Here’s a brief summary of findings from these platforms:
### Temu.com:
Temu.com is a B2B platform where various manufacturers list their products and prices. Searching for visual inspection systems here reveals a diverse range, typically within the following price brackets:
1. Basic Visual Inspection Systems: These systems, suitable for simple applications, range from $1,000 to $5,000.
2. Mid-Range Systems: More advanced systems with better accuracy and additional features are priced between $5,000 to $20,000.
3. High-End Systems: For high-precision and industrial-grade applications, prices can go from $20,000 up to $50,000 or more, depending on customization and specifications.
### 1688.com:
1688.com, often considered the Chinese equivalent of Alibaba, provides a wide selection of visual inspection systems from various manufacturers. The prices here can offer competitive insights:
1. Entry-Level Systems: Basic models for smaller businesses or less complex tasks are available from as low as 3,000 RMB to 10,000 RMB (~$420 to $1,400).
2. Intermediate Systems: Systems offering better performance and broader functionality generally cost between 10,000 RMB to 50,000 RMB (~$1,400 to $7,000).
3. Premium Systems: High-end solutions for demanding industrial environments can range from 50,000 RMB to 300,000 RMB (~$7,000 to $42,000), depending on advanced features and the level of customization.
### Conclusion:
The cost of visual inspection systems in China varies significantly based on the complexity and features of the system. For a precise budget and comparison, it’s advisable to directly contact manufacturers for quotes and negotiate bulk purchase deals, taking into account factors such as after-sales support and warranties.
Both Temu.com and 1688.com are valuable resources for initial research, offering a wide overview of market prices and manufacturers’ capabilities.
Shipping Cost for visual inspection system import from China
Shipping costs for importing a visual inspection system from China can vary based on several factors including the dimensions and weight of the system, shipping method, destination, and additional services required such as insurance and handling. Below are key considerations that can influence the shipping cost:
1. Shipping Method:
– Air Freight: Faster but more expensive. Suitable for urgent or high-value shipments.
– Sea Freight: Economical for large or heavy equipment; however, it takes longer to arrive.
2. Dimensions and Weight:
– Larger or heavier systems will incur higher shipping costs. Accurate measurements are essential for an honest quotation.
3. Destination:
– Shipping costs to remote or less accessible areas are typically higher compared to major cities and ports.
4. Insurance:
– Protects against loss or damage during transit, often charged as a percentage of the item’s value.
5. Customs Duties and Taxes:
– Must be calculated based on your country’s regulations. These additional costs can significantly impact the total import cost.
6. Packaging:
– Sturdy, secure packaging is crucial to prevent damage. Special packaging can add to the cost but is necessary for fragile systems.
To provide rough estimates:
– Air Freight: For a small to medium visual inspection system, expect to pay around $5 to $10 per kilogram.
– Sea Freight: Rates vary widely but can be cost-efficient for heavy equipment; typically between $100 to $300 per cubic meter.
Example:
For a visual inspection system weighing 100kg and fitting into 1 cubic meter:
– Air Freight: ~$500 – $1000
– Sea Freight: ~$100 – $300
Bear in mind, contacting logistics companies for quotes based on precise details will yield the most accurate costs.
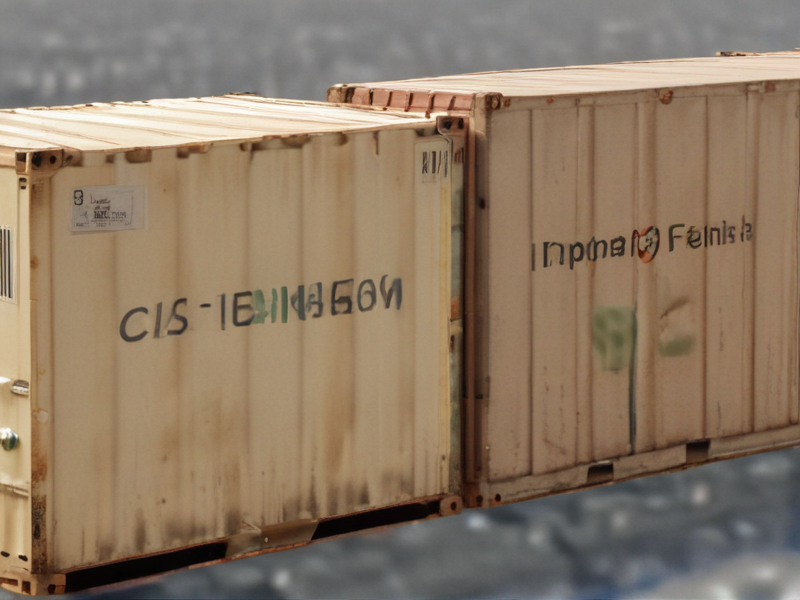
Compare China and Other visual inspection system Markets: Products Quality and Price,Visible and Hidden Costs
China’s visual inspection systems are generally more cost-effective compared to Western markets like the US, Germany, or Japan. These systems can offer competitive quality at a lower price due to lower labor and manufacturing costs. However, it’s crucial to note the visible and hidden costs associated with such systems.
### Products Quality and Price:
– China: Typically offers affordable visual inspection systems that perform adequately for standard industrial applications. However, the high-end capabilities and reliability might not always match those from premium markets.
– Western Markets: Provide higher-quality, more sophisticated visual inspection systems with advanced features and greater reliability. The price is significantly higher, reflecting better technology and stringent quality control.
### Visible and Hidden Costs:
– Visible Costs:
– China: Lower purchase prices but may incur higher shipping costs. Warranty and after-sales service can vary in quality.
– Western Markets: Higher upfront costs but generally include robust warranty, reliable customer service, and easier access to spare parts.
– Hidden Costs:
– China:
– Maintenance & Downtime: Potential for higher maintenance costs and more frequent downtimes due to less robust systems.
– Training & Integration: Staff may require more training to operate systems and integrate with existing infrastructure, possibly leading to delays.
– Western Markets:
– Operational Efficiency: Better system reliability and ease of integration often lower long-term operational costs.
– Technical Support: Stronger and more consistent technical support reduces problem resolution times and potential production halts.
### Conclusion:
China offers affordable visual inspection systems suitable for many applications, but potential hidden costs such as maintenance and integration should be considered. Western systems, while more expensive, generally provide superior quality and long-term support, reducing overall hidden costs and ensuring operational efficiency.
Custom Private Labeling and Branding Opportunities with Chinese visual inspection system Manufacturers
Custom private labeling and branding with Chinese visual inspection system manufacturers offer substantial opportunities for businesses looking to enhance their product line and market presence. China’s advanced manufacturing capabilities and cost-effective production make it an attractive hub for sourcing high-quality visual inspection systems tailored to specific brand needs.
Key Benefits:
1. Cost Efficiency: Leveraging China’s manufacturing proficiency can reduce production costs, enhancing profitability without compromising quality.
2. Customization: Chinese manufacturers are adept at customizing products to align with unique brand specifications, including software features, hardware design, and user interface modifications.
3. Speed to Market: Chinese suppliers often offer shorter lead times due to their established production facilities and streamlined supply chains. This allows quicker market entry and rapid response to demand changes.
4. Innovative Technology: Many Chinese manufacturers are at the forefront of technology, offering cutting-edge visual inspection systems with AI and machine learning capabilities that ensure precision and efficiency.
Steps to Engage:
1. Research and Vetting: Identify reputable manufacturers through industry networks, online directories, and trade shows. Vet potential partners by checking certifications, client reviews, and conducting factory visits when possible.
2. Define Specifications: Clearly outline your branding requirements, including logos, color schemes, packaging, software customizations, and any specific functional features.
3. Prototyping: Request prototypes to assess the quality and functionality of the customized visual inspection systems. This phase is crucial for ensuring that the product meets your standards before mass production.
4. Negotiation & Agreements: Negotiate favorable terms, including pricing, lead times, and minimum order quantities. Ensure contracts clearly define the scope of customization, intellectual property rights, and quality assurance measures.
5. Quality Control: Implement rigorous quality control protocols, including third-party inspections, to ensure products meet your brand’s standards and regulations.
Partnering with Chinese manufacturers for custom private labeling can greatly enhance your product offering, ensure competitive pricing, and streamline your path to market success.
Tips for Procurement and Considerations when Purchasing visual inspection system
When procuring a visual inspection system, ensure you address these key tips and considerations:
1. Define Requirements:
– Inspection Objectives: Clearly outline what you need to inspect (e.g., surface defects, measurements).
– Accuracy and Resolution: Determine the required precision to ensure the system meets quality standards.
– Speed: Consider the inspection speed to match production rates.
2. Compatibility with Existing Infrastructure:
– Integration: Ensure the system can be integrated with your current production line and software.
– Scalability: Choose a system that can grow with your production needs in the future.
3. Technology Selection:
– 2D vs. 3D Inspection: 2D systems are suitable for surface inspections, while 3D systems are better for volume and shape analysis.
– Lighting: Proper lighting is critical for accurate inspections. Choose systems with adjustable lighting options.
4. Ease of Use:
– User Interface: Select a system with an intuitive interface to minimize training and reduce errors.
– Training and Support: Ensure the vendor provides comprehensive training and ongoing technical support.
5. Reliability and Maintenance:
– Durability: Consider the build quality and environmental resistance (e.g., dust, moisture).
– Maintenance: Assess the ease of maintenance and availability of spare parts.
6. Cost Considerations:
– Initial and Operational Costs: Evaluate the total cost of ownership, including initial purchase, operation, and maintenance costs.
– Return on Investment: Analyze how quickly the system can pay for itself through enhanced quality and reduced waste.
7. Vendor Reputation:
– Experience and Expertise: Choose vendors with a proven track record in the industry.
– Customer Feedback: Look for reviews and case studies to gauge customer satisfaction and system performance.
By focusing on these areas, you can select a visual inspection system that enhances your production quality and efficiency while staying within budget and operational requirements.
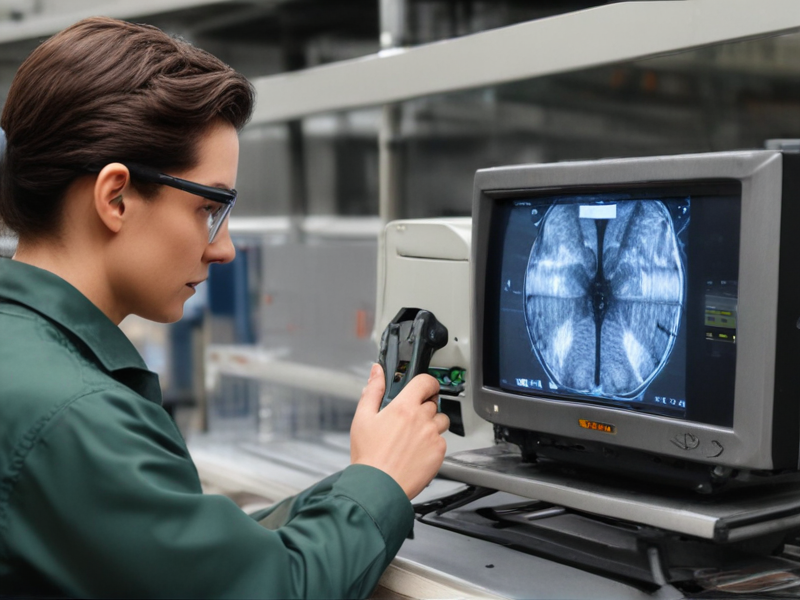
FAQs on Sourcing and Manufacturing visual inspection system in China
### FAQs on Sourcing and Manufacturing Visual Inspection Systems in China
1. Why source visual inspection systems from China?
China is renowned for its advanced manufacturing capabilities and cost-effective production. Many companies here offer high-quality visual inspection systems equipped with the latest technology at competitive prices.
2. What should I consider when selecting a supplier?
Key factors include the supplier’s experience in the industry, product quality, certifications (e.g., ISO, CE), logistical capabilities, customer reviews, and after-sales support.
3. How can I verify the quality of a supplier’s products?
Request product samples, visit the factory if possible, check third-party inspection reports, and ask for references from existing clients.
4. What are the common technologies used in visual inspection systems?
Common technologies include machine vision systems, artificial intelligence (AI), high-resolution cameras, lighting systems, and sophisticated image processing algorithms.
5. Can suppliers customize visual inspection systems based on specific needs?
Yes, many suppliers offer customization options to cater to specific industry requirements such as unique product dimensions, inspection criteria, and integration with existing systems.
6. How do I ensure compliance with international standards?
Ensure that the supplier’s products comply with international standards such as ISO, CE, and other relevant certifications. Discuss compliance requirements early in the negotiation process.
7. What about intellectual property (IP) protection?
Work with suppliers under clear and legally binding contracts, and consider involving local legal expertise to ensure IP protection. Non-disclosure agreements (NDAs) are essential.
8. What are the typical lead times for production and delivery?
Lead times vary depending on customization and order size but typically range from 4 to 12 weeks. Plan for additional time for shipping and customs clearance.
9. How is post-purchase support typically handled?
Reputable suppliers offer comprehensive after-sales support including installation, training, maintenance, and remote troubleshooting. Verify these services beforehand.
10. Are there risks involved with sourcing from China?
Risks include potential communication barriers, quality inconsistencies, and logistical challenges. Mitigate these risks through thorough vetting, clear contracts, and reliable logistics partners.
By addressing these FAQs, you can approach sourcing and manufacturing visual inspection systems from China with greater confidence and better preparedness.