Top 10 weigh filling system in China introduce,list main products and website if have
Here are ten notable weigh-filling system manufacturers in China, along with a brief introduction of their main products and websites:
1. **Yamato Scale**
– **Main Products**: Multihead weighers, checkweighers, and industrial scales.
– **Website**: [Yamato Scale China](http://en.yamato.com.cn/)
2. **Ishida China**
– **Main Products**: Multihead weighers, packaging machinery, and inspection equipment.
– **Website**: [Ishida China](https://www.ishida.com/global/cn/)
3. **ANRITSU Industrial Solutions**
– **Main Products**: Checkweighers, X-ray inspection systems, and metal detectors.
– **Website**: [ANRITSU Industrial China](https://www.anritsu-usa.com/)
4. **HanWei**
– **Main Products**: Automatic weighing, packaging machines, and conveyor systems.
– **Website**: [HanWei](http://www.hanweigh.com/)
5. **Guangdong Kenwei Intellectualized Machinery Co., Ltd.**
– **Main Products**: Multihead weighers, linear weighers, and checkweighers.
– **Website**: [Kenwei](http://www.kenweigh.com/)
6. **Shanghai Shigan Industrial Co., Ltd.**
– **Main Products**: Weighing inspection machines, multihead weighers, and metal detectors.
– **Website**: [Shigan Industrial](http://www.sgmcrown.com/)
7. **Zhongshan Easyweigh Equipment Co., Ltd.**
– **Main Products**: Multihead weighers, loss-in-weight feeders, and batching machines.
– **Website**: [Easyweigh](http://www.easyweigh.com.cn/)
8. **JISIWEI Intelligent Technology**
– **Main Products**: Automatic weighing systems, packaging lines, and inspection equipment.
– **Website**: [JISIWEI](http://www.jisiwei.com/)
9. **Guangzhou Mingke Packaging Machinery Co., Ltd.**
– **Main Products**: Weighing machines, conveyor systems, and packing machines.
– **Website**: [Mingke](http://www.mingkemachine.com/)
10. **Zhongshan Multiweigh Packaging Machinery Co., Ltd.**
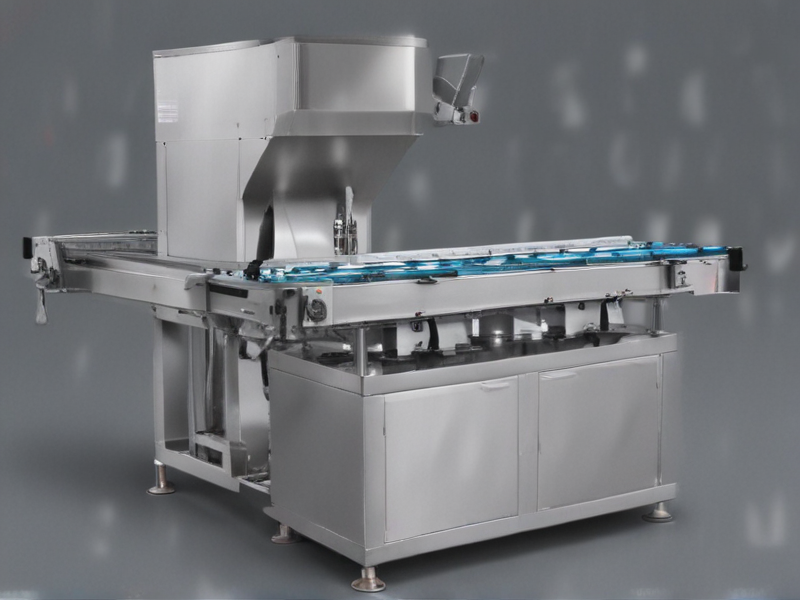
Types of weigh filling system
Weigh filling systems are essential in various industries for accurately filling products by weight rather than volume. Here are the common types:
1. **Gravimetric Filling**:
– **Net Weigh Filling**: The product is pre-weighed in a separate container before being dispensed into the final packaging. This method ensures high accuracy and is ideal for products where consistency is crucial.
– **Gross Weigh Filling**: The product is weighed directly in its final packaging. This system is simpler but can be slightly less accurate due to packaging weight variations.
2. **Volumetric Filling**:
– **Auger Fillers**: Used for powdery and granular products, an auger screw measures out a set volume before dispensing. It’s less accurate than true weigh systems but faster.
– **Cup Fillers**: Utilizes pre-measured cups or containers to dispense products. Best for free-flowing granules and small particulates.
3. **Combination Weighing**:
– **Multi-Head (Combination) Weighers**: Multiple weighing heads measure small amounts of product, which are then combined to achieve the target weight. This method offers high speed and precision, ideal for snacks, candies, and mixed products.
4. **Vibratory Feeders**:
– Uses vibration to feed products into a weigh hopper. It’s suitable for fragile or irregularly shaped items, providing gentle handling while maintaining accuracy.
5. **Belt Weighers**:
– Conveyor belts are integrated with weighing sensors. Continuous weighing and dispensing are possible, making this system ideal for bulk materials in a production line.
6. **Liquid Filling Systems**:
– Typically used for weighing and filling liquids. Mass flow meters or load cells ensure precise quantity dispensation.
Each system has its specific applications based on the product type, required filling accuracy, and desired speed. Proper selection ensures efficient, accurate, and cost-effective packaging.
Pros and Cons of Using weigh filling system
### Pros of Using a Weigh Filling System
1. **Accuracy**: Weigh filling systems provide precise measurement of product weight, ensuring consistency and reducing overfill or underfill occurrences.
2. **Efficiency**: Automated weigh filling can significantly speed up the packaging process, enhancing productivity and throughput.
3. **Cost Reduction**: Accurate filling minimizes product giveaway, leading to potential cost savings in raw materials.
4. **Versatility**: These systems can handle a wide range of product types, including solids, granules, powders, and liquids.
5. **Quality Control**: Consistent product weights ensure that each package meets specified criteria, improving overall product quality and customer satisfaction.
6. **Data Tracking**: Modern weigh filling systems often come with integrated software for tracking and documenting filling performance, aiding in regulatory compliance and process optimization.
### Cons of Using a Weigh Filling System
1. **Initial Investment**: The cost of acquiring and installing a weigh filling system can be high, which may be a barrier for small businesses.
2. **Maintenance**: These systems require regular maintenance and calibration to ensure continued accuracy and reliability, which can incur ongoing costs.
3. **Complexity**: Advanced weigh filling systems can be complex to operate and may require specialized training for staff.
4. **Space Requirements**: These systems can occupy significant floor space, which might be a limitation in smaller facilities.
5. **Initial Setup Time**: Setting up a weigh filling system for different product types can take time, affecting initial production schedules.
6. **Downsizing**: If a factory has to frequently change product lines or volumes, the system may require adjustments, leading to potential downtimes.
In summary, while weigh filling systems offer significant advantages in terms of accuracy, efficiency, and quality control, they also come with high initial costs, maintenance requirements, and potential operational complexities. Balancing these factors is crucial for determining their suitability for a specific application.
weigh filling system Reference Specifications (varies for different product)
A weigh filling system is an automated equipment used in packaging processes to accurately fill products into containers based on weight specifications. The system is versatile and can handle a variety of products, including granular, powdery, and liquid materials. Precise weight measurement is vital for ensuring product consistency, meeting regulatory compliance, minimizing waste, and improving overall operational efficiency. Below are typical reference specifications for a weigh filling system, which may vary depending on the specific product being processed.
### Key Specifications:
1. **Accuracy and Precision**:
– **Weighing Accuracy**: ± 0.1% to ± 0.5% of target weight
– **Precision**: Achieved through advanced load cells and calibration mechanisms
2. **Capacity and Throughput**:
– **Weighing Range**: 0.5 grams to 50 kilograms, depending on specific product requirements
– **Filling Speed**: 10 to 60 fills per minute, influenced by product type and container size
3. **Material Compatibility**:
– **Product Types**: Powders, granules, liquids, pastes, and solids
– **Contact Materials**: Stainless steel, food-grade plastics for hygiene and durability
4. **Container Versatility**:
– **Container Types**: Bags, bottles, jars, cans, pails, and more
– **Size Range**: From small sachets to large industrial totes
5. **Control and Integration**:
– **User Interface**: Touchscreen control panels with programmable settings
– **Automation**: Integration with conveyors, sealing machines, and labeling equipment
– **Data Management**: Connectivity for data logging, batch tracking, and quality control
6. **Compliance and Standards**:
– **Regulatory Compliance**: Meets industry standards like FDA, GMP, and others
– **Safety Features**: Emergency stop, overload protection, and safety guards
7. **Environmental Factors**:
– **Operating Conditions**: Suitable for varied environments from clean rooms to industrial setups
– **Dust and Spill Management**: Systems to manage and mitigate product spillage and dust generation
8. **Maintenance and Support**:
– **Ease of Cleaning**: Designed for easy disassembly and cleaning
– **Technical Support**: Availability of service contracts and remote troubleshooting
These specifications ensure that the weigh filling system meets the diverse needs of different products and industries, providing reliable and efficient filling solutions.
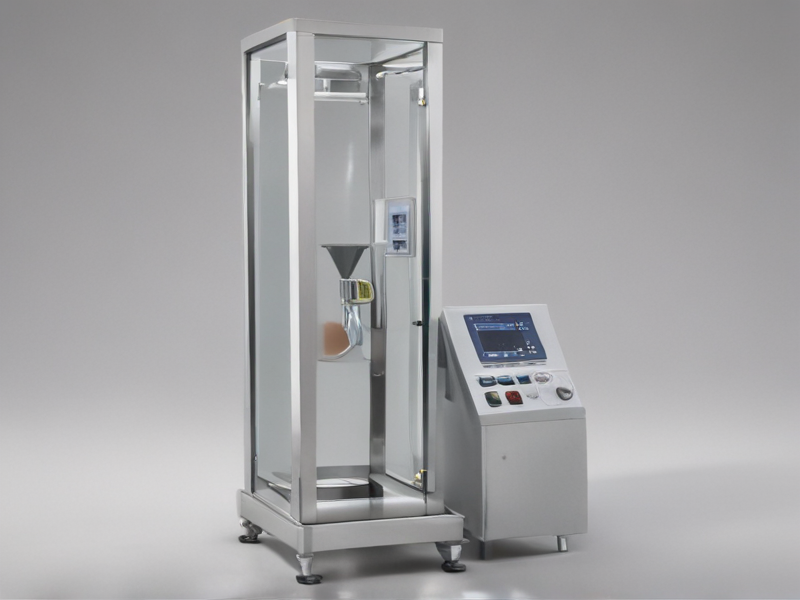
Applications of weigh filling system
Weigh filling systems are pivotal in various industries for precise and efficient product packaging. Below are some key applications:
1. **Food and Beverage Industry**:
– **Snacks and Confectionery**: Ensures uniform product weight in packages, improving quality control.
– **Bulk Ingredients**: Helps in packaging items like flour, sugar, and grains with consistent weight, minimizing waste.
2. **Pharmaceutical Industry**:
– **Medicinal Powders and Tablets**: Accurate weight filling is crucial for dosage integrity and regulatory compliance.
– **Nutraceuticals**: Ensures correct portioning of powders and capsules, maintaining product efficacy and safety.
3. **Chemical Industry**:
– **Powders and Granules**: For chemicals like detergents and fertilizers, precise weigh filling prevents spillage and ensures proper product usage.
– **Industrial Chemicals**: Accurate weight control is essential for safety and effectiveness in product applications.
4. **Cosmetics and Personal Care**:
– **Powders and Creams**: Guarantees consistent product weight in jars and bottles, enhancing customer satisfaction and brand reliability.
– **Bath Salts and Scrubs**: Ensures even distribution and packaging of products, maintaining batch consistency.
5. **Agriculture**:
– **Seeds and Animal Feed**: Accurate weighing ensures fair trade and compliance with agricultural standards, optimizing packaging and distribution.
6. **Pet Food Industry**:
– **Dry Kibble and Treats**: Ensures each package meets advertised weight, enhancing customer trust and reducing returns.
7. **Automotive and Electronics**:
– **Small Components**: Weigh filling of nuts, bolts, and electronic parts requires precision to ensure correct assembly and operation.
8. **Retail and E-Commerce**:
– **Bulk Goods**: Efficient packaging for bulk items like nuts, coffee, and spices, improving shelf appeal and reducing logistical costs.
In summary, weigh filling systems enhance precision, efficiency, and regulatory compliance across diverse sectors, contributing significantly to product quality and operational effectiveness.
Material of weigh filling system
A weigh filling system, used predominantly in packaging and manufacturing industries, is designed to accurately dispense a specified weight of product into containers. The choice of materials for these systems is critical for ensuring durability, hygiene, and compatibility with the types of products being handled. Here’s a concise breakdown of the key materials often used:
1. **Stainless Steel:**
– **Grades:** Commonly 304 or 316.
– **Properties:** Corrosion-resistant, durable, easy to clean, and non-reactive.
– **Applications:** Ideal for food, beverage, pharmaceutical, and chemical industries where hygiene and resistance to corrosive substances are paramount.
2. **Aluminum:**
– **Properties:** Lightweight, corrosion-resistant, and cost-effective.
– **Applications:** Used in parts where high structural strength isn’t as crucial, such as framework components or secondary parts.
3. **Plastics (Food-Grade):**
– **Types:** Polyethylene (PE), Polypropylene (PP), Polyvinyl Chloride (PVC).
– **Properties:** Lightweight, non-toxic, and resistant to many chemicals.
– **Applications:** Often used in components like hoppers, chutes, or parts in direct contact with food products.
4. **Rubber and Elastomers:**
– **Types:** Silicone, EPDM (Ethylene Propylene Diene Monomer), and Teflon.
– **Properties:** Flexible, non-reactive, and provides a good seal.
– **Applications:** Seals, gaskets, and other parts requiring flexibility and a tight fit to prevent leaks and contamination.
5. **Glass and Ceramics:**
– **Properties:** Non-reactive, heat resistant, and easy to sterilize.
– **Applications:** Generally used for very specific applications like certain pharmaceutical operations.
Each of these materials is selected based on the specific requirements of the weigh filling system, considering factors such as product compatibility, regulatory compliance, environmental conditions, and cost. Proper material selection ensures long-term functionality, safety, and efficiency of the weigh filling system.
Quality Testing Methods for weigh filling system and how to control the quality
Quality testing for a weigh filling system is critical to ensure accuracy, consistency, and efficiency. Here are key methods and control strategies:
### Methods for Quality Testing:
1. **Calibration Testing:**
– Regularly calibrate weigh scales with certified weights.
– Perform zero and span adjustments to ensure the system reads accurately.
2. **Repeatability Tests:**
– Perform multiple fill tests to verify consistent performance.
– Calculate standard deviation and variance to assess precision.
3. **Accuracy Verification:**
– Compare measured weight against a known standard.
– Conduct accuracy tests under varying load conditions and environmental factors.
4. **Endurance Testing:**
– Run the system continuously for an extended period.
– Monitor fatigue and potential drift in accuracy over time.
5. **Environmental Testing:**
– Assess the system’s performance under different temperature and humidity conditions.
– Use environmental chambers to simulate extreme conditions.
6. **Material Flow Testing:**
– Evaluate how different materials interact with the system.
– Assess the flow characteristics to adjust fill speed and reduce spillage.
### Quality Control Strategies:
1. **Standard Operating Procedures (SOPs):**
– Develop detailed instructions for calibration, maintenance, and operation.
– Train operators to follow SOPs precisely.
2. **Automated Monitoring:**
– Implement sensors and software for real-time monitoring of weight accuracy.
– Use alarms for deviations beyond predefined tolerances.
3. **Periodic Audits:**
– Conduct regular audits of calibration records and system performance reports.
– Perform random checks to verify adherence to quality standards.
4. **Feedback Loops:**
– Continuously collect data on fill errors and downtime.
– Use statistical process control (SPC) to identify trends and implement corrective actions.
5. **Maintenance Programs:**
– Schedule regular preventive maintenance to minimize wear and tear.
– Keep spare parts inventory to reduce downtime during repairs.
By combining rigorous testing methods with proactive quality control strategies, the reliability and accuracy of weigh filling systems can be maintained, ensuring high-quality output and operational efficiency.
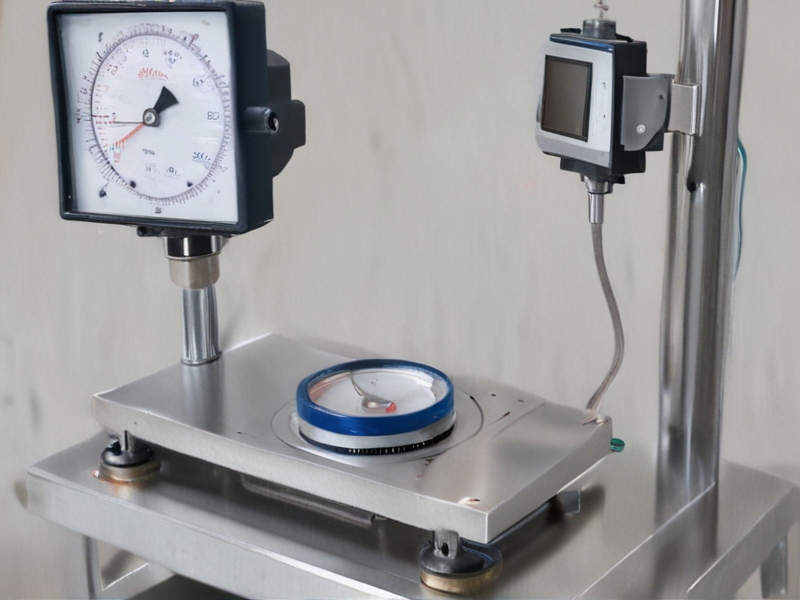
The Work Process and how to use weigh filling system
A weigh filling system is an automated method used to accurately measure and fill products by weight. This system is commonly employed in industries such as food, pharmaceuticals, and manufacturing. Here is a concise overview of how it works and how to use it:
### Work Process:
1. **Setup:**
– **Install the Machine:** Place the weigh filling system on a stable surface and connect it to a power source.
– **Calibration:** Calibrate the scales to ensure accurate measurement. This involves setting zero weight and verifying with known standard weights.
2. **Product Preparation:**
– **Select Product:** Choose the product to be filled and prepare it as per the requirement (e.g., granules, powders, liquids).
– **Filling Parameters:** Set target weights, tolerances, and speeds on the control panel.
3. **Loading:**
– **Hopper Filling:** Load the product into the hopper of the machine. Ensure the hopper has an even flow to avoid clogging.
4. **Weighing and Filling:**
– **Automated Weighing:** When the start button is pressed, the system begins to dispense the product, stopping once the target weight is achieved.
– **Filling Container:** The product is then deposited into containers positioned on the scale.
5. **Quality Control:**
– **Check Weight:** Perform random weight checks to ensure consistency and accuracy.
– **Adjustments:** Make necessary adjustments to the system settings as required based on the quality control checks.
### How to Use:
1. **Power On:** Switch on the machine and allow it to perform initial self-checks.
2. **Calibrate:** Follow the machine’s manual to calibrate the scale.
3. **Configure Settings:** Input desired weight, fill speed, and tolerance on the control panel.
4. **Load Product:** Fill the hopper with the product to be weighed and filled.
5. **Start Filling:** Place containers on the scale. Press the start button to begin automated filling.
6. **Monitor Operation:** Observe the process for any jams or errors. Make adjustments if necessary.
7. **Regular Checks:** Periodically check the filled containers to ensure they meet the specified weight.
8. **Shut Down:** After use, turn off the machine and clean according to manufacturer guidelines to maintain hygiene and equipment longevity.
By following these steps, the weigh filling system can efficiently and accurately manage the filling process, ensuring consistency and quality.
weigh filling system Importing questions including Cost,Supplier,Sample,Certification and Market
When considering the import of a weigh filling system, several key aspects must be addressed to ensure the process is efficient, compliant, and cost-effective:
1. **Cost**: Analyze the total cost, including the purchase price, shipping fees, import duties, and taxes. Factor in long-term costs such as maintenance, spare parts, and operational expenses. Compare multiple suppliers to find the best value for money.
2. **Supplier**: Identify reputable suppliers with a solid track record. Verify their experience and reliability through customer reviews and testimonials. Assess the supplier’s ability to provide after-sales service and support. Consider suppliers who offer warranties and have quick delivery times.
3. **Sample**: Request a sample unit or a demonstration to verify the equipment’s performance and compatibility with your production needs. Testing a sample can help you identify potential issues and ensure that the system meets your quality standards before committing to a larger purchase.
4. **Certification**: Ensure the weigh filling system complies with relevant industry standards and certifications. This may include ISO certification, CE marking for European markets, or specific food safety standards if applicable. Proper certification ensures that the equipment meets regulatory requirements and maintains production quality.
5. **Market**: Assess the demand for the products you’ll produce with the weigh filling system to ensure there is a sufficient market. Conduct a competitive analysis to understand market trends, consumer needs, and price points. This helps in making informed decisions about inventory levels and production scaling.
By thoroughly evaluating these factors, you can make strategic decisions that optimize your investment in a weigh filling system and align with your business objectives.
How to find and select check reliable weigh filling system manufacturers in China
To find and select reliable weigh-filling system manufacturers in China, follow these concise steps:
1. **Research Online Directories**: Utilize online platforms like Alibaba, Made-in-China, and Global Sources. These platforms list verified suppliers and provide ratings and reviews.
2. **Evaluate Supplier Profiles**: Look for manufacturers with extensive experience, preferably over 5 years, in producing weigh-filling systems. Check their product range, certification (e.g., ISO 9001), and quality standards compliance.
3. **Customer Reviews and Ratings**: Pay close attention to customer feedback and ratings on the platforms. Consistent positive reviews are indicators of reliability.
4. **Request Samples**: Contact potential manufacturers and request product samples or videos demonstrating their weigh-filling systems. Assess the quality, precision, and functionality of the samples.
5. **Check Industry Certifications**: Ensure that the manufacturers have relevant industry certifications. This confirms adherence to international standards.
6. **Factory Visit (if possible)**: If feasible, organize a visit to the manufacturer’s factory. This allows you to inspect their production process, quality control systems, and overall operational capacity.
7. **Leverage Trade Shows**: Attend industry-specific trade shows in China such as the Canton Fair. This offers direct interaction with multiple manufacturers and firsthand assessment of their products.
8. **Compare Quotes and Services**: Obtain detailed quotations from shortlisted manufacturers. Compare prices, warranty terms, after-sales service, and lead times.
9. **Request References**: Ask for references from past clients, particularly those in your industry or with similar requirements.
10. **Secure and Verify Contracts**: Ensure all agreed terms are documented in a detailed contract, including specifications, delivery schedules, payment terms, and warranties. Verify the legality and authenticity of the contract.
By following these steps, you can systematically identify and select a reliable weigh-filling system manufacturer in China.
Background Research for weigh filling system manufacturers Companies in China, use qcc.com archive.org importyeti.com
China is home to numerous companies specializing in the manufacture of weigh filling systems, capitalizing on the nation’s extensive industrial base and advanced manufacturing capabilities. Several sources provide detailed insights into these companies, including qcc.com, archive.org, and importyeti.com.
**qcc.com** is a comprehensive business directory and corporate information platform in China. It lists numerous companies involved in the manufacture of weigh filling systems, offering data on their financial health, legal standing, and operational scope. Key players often spotlighted include Anhui Zengran Packaging Technology Co., Ltd., specializing in high-speed, automated weigh filling systems, and modifiable machinery tailored for the food and beverage industry. Companies like Guangzhou Tech-Long Packaging Machinery Co., Ltd. are also prominent, known for their innovative and reliable filling solutions.
Archival resources from **archive.org** provide historical data and older web contents that can reveal the long-term performance and reputation of these manufacturers. Analysis of web crawls and archived financial reports can show the development trajectory and technological advancements of notable companies like Shanghai Zhonghe Packing Machinery Co., Ltd., which has a longstanding presence and proven track record in the automation sector.
**importyeti.com** is another essential tool, offering insights into the import-export activities of various weigh filling system manufacturers. It highlights the international reach of Chinese companies and their frequency of exports, showcasing global trust in their products. Detailed trade data reveals that companies like Foshan Kinghanlong Machinery Manufacturing Co., Ltd. and Xiamen Sengong Packing Equipment Co., Ltd. are highly active in international markets, exporting advanced filling machinery to multiple countries and reinforcing their credibility as reliable suppliers.
In summary, leveraging data from qcc.com, archive.org, and importyeti.com demonstrates that China hosts a robust selection of innovative and internationally trusted weigh filling system manufacturers, exemplified by companies like Anhui Zengran, Tech-Long, Shanghai Zhonghe, Kinghanlong, and Sengong.
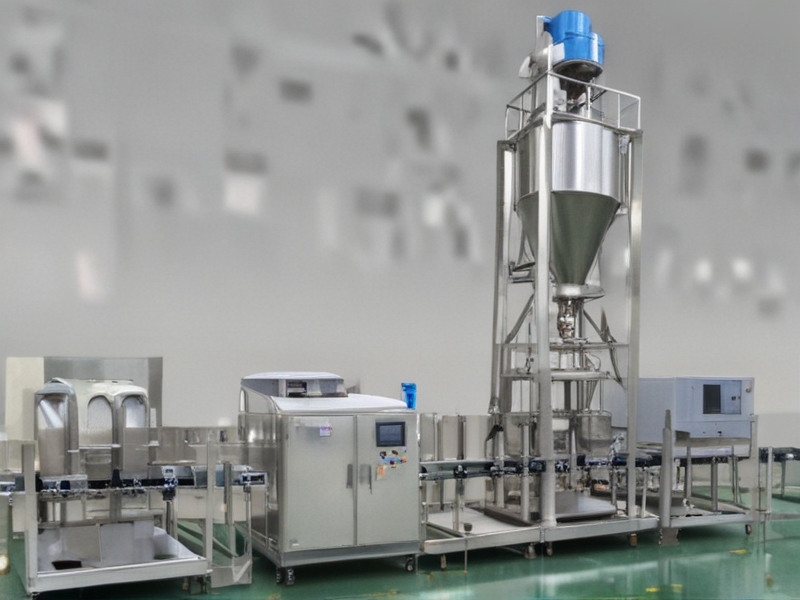
Price Cost Research for weigh filling system manufacturers Companies in China, use temu.com and 1688.com
Conducting price cost research for weigh filling system manufacturers in China using Temu.com and 1688.com requires a strategic approach to gather accurate and comprehensive information. Here’s a step-by-step guide to help you navigate these platforms effectively:
### Temu.com
1. **Search Keywords**: Start with keywords like “weigh filling system” or “weigh filler machine.”
2. **Filter Options**: Use filters for “Manufacturer,” “Supplier,” and “Region (China)” to narrow down results.
3. **Price Comparison**: Take note of the price ranges listed. Temu may show products from different suppliers, so compile an average range.
4. **Supplier Details**: Look for supplier ratings, number of transactions, and customer feedback to assess reliability.
### 1688.com
1. **Language Translation**: Enable browser translation as 1688.com is primarily in Chinese.
2. **Search and Filters**: Use similar search terms like “称重灌装系统” (weigh filling system) and apply filters for dealers and specific provinces.
3. **Product Listings**: Analyze the price per unit and bulk purchase options available in listings. Prices can vary based on specifications and order size.
4. **Contact Suppliers**: For more specific pricing, contact suppliers directly via the platform’s messaging system. Ask for detailed quotations that include shipping and any additional fees.
### Price Range Findings
– **Temu.com**: Generally, weigh filling systems on Temu range between $2,000 to $10,000, depending on the complexity and brand.
– **1688.com**: Prices on 1688.com can be slightly lower, ranging from ¥10,000 to ¥50,000 ($1,500 to $7,500), as the site caters more towards direct factory prices.
### Conclusion
Prices for weigh filling systems in China vary based on the platform, specifications, and order quantities. On Temu.com, prices range from $2,000 to $10,000, while on 1688.com, it ranges from ¥10,000 to ¥50,000 ($1,500 to $7,500). Always validate supplier credibility through reviews and ratings, and consider contacting multiple suppliers for detailed quotes to ensure the best deal.
Shipping Cost for weigh filling system import from China
When importing a weigh filling system from China, the shipping cost can vary significantly based on several key factors:
1. **Shipping Method**:
– **Air Freight**: Faster but more expensive; suitable for urgent or high-value items.
– **Sea Freight**: More economical for bulky or heavy equipment, though transit times are longer.
2. **Weight and Dimensions**:
– Heavier and larger equipment increases shipping costs due to space occupation in the cargo.
3. **Shipping Distance and Route**:
– Costs can vary depending on the distance between the origin port in China and the destination port. Common shipping routes may offer more competitive pricing.
4. **Incoterms**:
– The agreed terms like FOB (Free On Board) or CIF (Cost, Insurance, and Freight) can affect the final landed cost.
5. **Customs and Duties**:
– Additional charges for customs clearance, import duties, and taxes in the destination country.
**Estimations**:
– **For Air Freight**: Typically ranges from $5 to $10 per kilogram.
– **For Sea Freight**: Costs can be between $500 and $3000 for a 20-foot container, depending on the factors mentioned above.
**Example Calculation**:
– Suppose your weigh filling system occupies half a 20-foot container and weighs 500 kg.
– **Sea Freight**:
– Container rate approximately $1000
– Equipment share: $500
– Customs duties and other fees: Varies by country
**Total Cost Estimate**:
$500 (sea freight) + customs and other fees.
To get an accurate quote, contact freight forwarders with the system’s exact specifications and intended delivery destination.
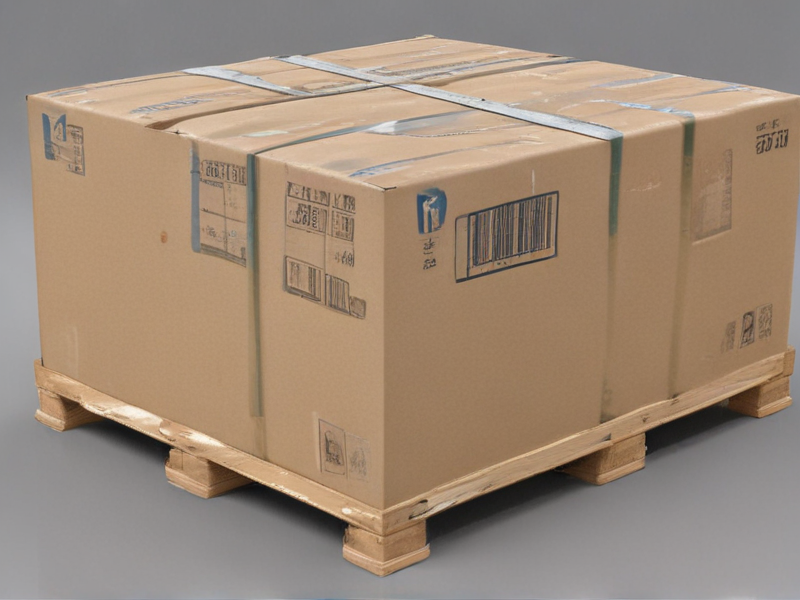
Compare China and Other weigh filling system Markets: Products Quality and Price,Visible and Hidden Costs
When comparing China’s weigh filling systems market to others, several key factors emerge: product quality, price, and associated costs.
**Product Quality**:
Chinese weigh filling systems often emphasize cost-effective production, which can result in mixed quality. Some manufacturers offer high-quality, technologically advanced systems comparable to Western standards, but inconsistencies exist. In contrast, markets in the U.S. and Europe are renowned for their stringent quality controls, leading to more consistent and reliable products. Japanese systems also typically boast superior precision and durability due to meticulous engineering.
**Price**:
Price is where Chinese weigh filling systems significantly stand out. They are generally more affordable due to lower labor and material costs. Western and Japanese systems, while high in quality, come with a premium price tag, reflecting higher production costs and technological advancements.
**Visible and Hidden Costs**:
– **Visible Costs**: The initial purchase price for Chinese systems is often lower. However, Western and Japanese systems might offer better long-term value despite higher upfront costs, due to reliability and fewer operational issues.
– **Hidden Costs**: Hidden costs include maintenance, repair, and potential downtime. Chinese systems might incur higher hidden costs due to variable quality and less stringent quality control, leading to more frequent repairs and replacements. Additionally, after-sales service and support can be less reliable and more costly in the long run. Western and Japanese markets usually offer robust support and lower maintenance costs, enhancing overall value.
In summary, while Chinese weigh filling systems are attractive for their lower prices, potential hidden costs and quality variances make it crucial to consider long-term value. Western and Japanese markets typically provide higher quality and reliability, justifying their higher initial costs through reduced maintenance and better longevity.
Custom Private Labeling and Branding Opportunities with Chinese weigh filling system Manufacturers
Engaging with Chinese manufacturers for custom private labeling and branding of weigh filling systems presents considerable opportunities for businesses aiming to enhance their market presence. China, being a global manufacturing hub, offers advanced technological capabilities, cost-effective production, and flexible business models tailored to diverse needs.
One of the primary advantages is the availability of state-of-the-art weigh filling technology at a lower cost compared to domestic suppliers. Chinese manufacturers provide a range of systems, from semi-automatic to fully automatic, catering to various industries such as food, pharmaceuticals, and chemicals. These manufacturers are adept at customizing machines to meet specific operational requirements, thereby aligning the product with your brand’s unique selling proposition.
Private labeling involves the manufacturer producing weigh filling systems under your brand name. This arrangement permits you to leverage high-quality equipment without the substantial investment into infrastructure and R&D. Moreover, Chinese manufacturers are well-versed in international standards and certifications—ensuring that the products meet stringent quality and safety regulations.
Branding opportunities extend beyond mere labeling. Chinese suppliers often offer comprehensive services including logo engraving, customized color schemes, and branded user interfaces. This holistic approach ensures that the equipment not only performs optimally but also reflects your brand’s identity, thereby enhancing brand loyalty and recognition.
To maximize the benefits, it is advisable to conduct thorough due diligence when selecting a manufacturer. Evaluate their experience, production capabilities, quality control mechanisms, and client testimonials. Establishing clear communication channels and visiting manufacturing sites can further mitigate potential risks.
In conclusion, Chinese weigh filling system manufacturers provide extensive private labeling and branding opportunities. By partnering with the right manufacturer, businesses can elevate their product offerings, reduce costs, and cultivate a strong market presence with customized, high-quality machinery.
Tips for Procurement and Considerations when Purchasing weigh filling system
When purchasing a weigh filling system, several considerations ensure you make a well-informed decision:
**1. Accuracy and Precision:**
– Ensure the system meets the required accuracy and precision levels for your specific application to minimize product giveaway or underfill.
**2. Throughput Capacity:**
– Understand the desired speed and volume. A system that matches or exceeds your production rates avoids bottlenecks.
**3. Product Compatibility:**
– Verify if the system can handle your product’s properties (e.g., granularity, stickiness, fluidity).
**4. Durability and Build Quality:**
– Choose robust materials resistant to wear and environmental factors affecting reliability and lifespan.
**5. Ease of Integration:**
– Ensure compatibility with existing production lines and software for seamless integration and minimal downtime.
**6. Scalability:**
– Consider future growth. A system with modular components can expand capacity as needs grow.
**7. Maintenance and Support:**
– Look for low maintenance systems with easily accessible parts, and ensure manufacturer support and availability of spare parts.
**8. Cost Considerations:**
– Balance upfront costs with long-term operational expenses, including maintenance, energy consumption, and training.
**9. Compliance:**
– Ensure the system meets industry standards and regulatory requirements, such as USDA or FDA regulations for food products.
**10. Technical Features:**
– Evaluate advanced features like touchscreen interfaces, data logging capabilities, and real-time monitoring for enhanced control and traceability.
**11. Reliability and Reputation:**
– Research manufacturer reputation, read reviews, and check references. Reliable brands tend to provide consistent quality and support.
By focusing on these factors, you ensure your weigh filling system purchase aligns with operational needs, budget constraints, and future scalability, optimizing productivity and reducing long-term costs.
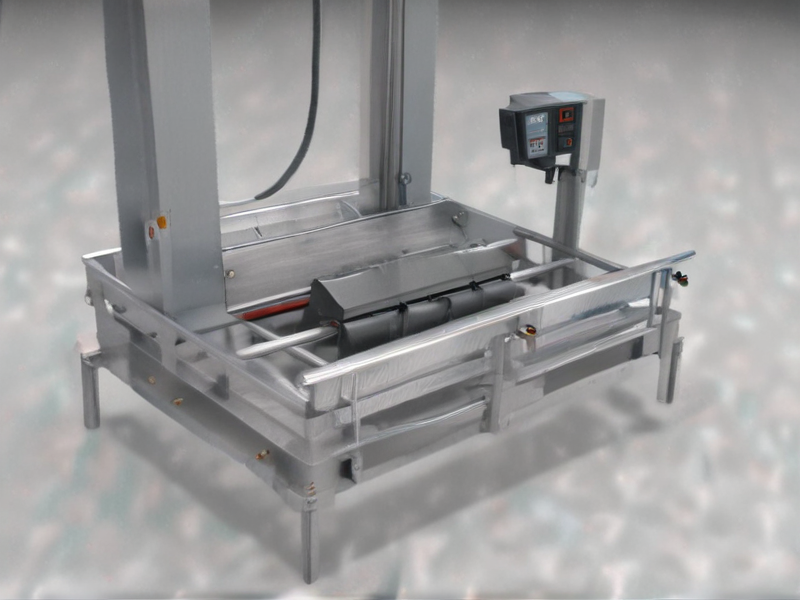
FAQs on Sourcing and Manufacturing weigh filling system in China
**FAQs on Sourcing and Manufacturing Weigh Filling System in China**
1. **What are the advantages of sourcing weigh filling systems from China?**
– **Cost-Effective:** Lower production and labor costs.
– **Advanced Technology:** Access to the latest industry advancements.
– **Large Supplier Base:** Diverse selection of manufacturers.
– **Customization:** High flexibility in meeting custom requirements.
2. **How do I find reliable manufacturers?**
– **Online Platforms:** Use Alibaba, Made-in-China, Global Sources.
– **Trade Shows:** Attend Canton Fair, China International Machine Tool Show (CIMT).
– **Referrals:** Ask for recommendations from industry contacts.
– **Third-Party Services:** Employ sourcing agents or consultancies.
3. **What should I consider when evaluating suppliers?**
– **Reputation:** Check reviews and ratings.
– **Certifications:** Look for ISO, CE, RoHS certifications.
– **Experience:** Prefer manufacturers with a solid track record.
– **Factory Visits:** Conduct on-site inspections if possible.
– **Samples:** Request product samples for quality assessment.
4. **What are the typical lead times?**
– **Standard Products:** 30-60 days.
– **Customized Solutions:** 60-90 days, depending on complexity.
5. **How can I ensure quality control?**
– **Pre-Shipping Inspections:** Hire third-party inspectors.
– **In-House Audits:** Conduct periodic inspections.
– **Testing Protocols:** Agree on comprehensive QA/QC standards.
6. **What is the usual payment term?**
– **Common Practice:** 30% deposit and 70% before shipment.
– **Payment Methods:** T/T, L/C, with options for Escrow services for additional security.
7. **Are there any risks associated with IP theft?**
– **Contracts:** Use Non-Disclosure Agreements (NDAs) and contracts.
– **Legal Support:** Engage a Chinese legal consultant for patent protections.
8. **How do I handle logistics and shipping?**
– **Freight Forwarders:** Use reputable companies.
– **Incoterms:** Clarify terms like FOB, CIF.
– **Customs:** Ensure all documents are correctly handled to avoid delays.
9. **Is after-sales support available?**
– **Service Agreements:** Negotiate terms before purchasing.
– **Local Representatives:** Prefer vendors with local support offices or partners.